
Concrete construction technology in tunnel construction: from primary support to secondary lining
In tunnel construction, concrete construction technology is the key to ensure the stability and safety of tunnel structure. Concrete construction of tunnels usually adopts the method of excavation and lining at the same time. This process involves multiple steps, from initial support to secondary lining, and each step is crucial. This article will introduce this construction process in detail to help readers understand the whole process of tunnel concrete construction more deeply.
Initial support: shotcrete and steel mesh fixing
After tunnel excavation, the first task is to carry out initial support to prevent the collapse of the tunnel wall. This process usually uses shotcrete as a temporary support. Shotcrete can harden quickly and provide immediate support for the tunnel wall. Subsequently, the construction workers will set up the steel mesh and use anchor rods to fix it to the tunnel wall to further enhance the stability of the initial support.
Secondary lining: Collaborative operation of steel bar trolley and casting trolley
After the initial support is stable, the tunnel enters the secondary lining stage. The secondary lining is part of the permanent structure of the tunnel and is crucial to the long-term stability and safety of the tunnel. This stage of construction requires the use of special trolleys, including trolleys for setting up and welding steel bars and casting trolleys.
1. Setting up and welding the steel bar trolley: First, use the steel bar trolley to set up the steel bar frame inside the tunnel. The steel bar frame must be built accurately to ensure the structural strength and durability of the concrete lining.
2. Casting trolley: After the steel bar frame is built, the casting trolley enters the operation for pouring concrete. In the concrete formwork, a casting port of about 50 mm by 50 mm will be reserved to ensure that the concrete can be evenly distributed, avoid the generation of bubbles and voids, and thus improve the density and strength of the concrete.
Tunnel concrete construction is a complex and precise process. From initial support to secondary lining, each step must be strictly controlled to ensure the safety and durability of the tunnel structure. By using shotcrete, steel mesh fixing, and the coordinated operation of the steel bar trolley and the casting trolley, tunnel builders can effectively respond to the challenges of geological conditions and build high-quality tunnel projects.

Lanhi Intelligent Rock Drilling Trolley: Intelligent Equipment for Efficient Mining Excavation
Lanhi Intelligent Rock Drilling Trolley is an advanced equipment designed for mining drilling and blasting, and is widely used in tunnel and tunnel excavation projects in mining, hydropower, highway, railway and other fields. With its excellent performance and intelligent design, this equipment provides a strong guarantee for the efficient, safe and precise operation of the project.
In the fields of mining, tunnel excavation, etc., Lanhi Intelligent Rock Drilling Trolley is leading the industry towards a more efficient and safe future with its excellent performance and intelligent technology. This equipment designed for mining drilling and blasting provides a new solution for the excavation of tunnels and tunnels with its high-power rock drill, long telescopic travel drill arm, and automatic control system.
High-performance rock drill and large-area operation coverage
Lanhi Intelligent Rock Drilling Trolley is equipped with a high-power rock drill, has a strong drilling capability, and is suitable for various complex geological conditions. Its drill arm has a unique design and a long telescopic stroke, which greatly increases the working coverage area, greatly improves the efficiency of drilling operations, and can efficiently complete the drilling tasks of blasting holes and anchor holes. Whether in the narrow space of mine tunnels or in the excavation construction of long-distance tunnels, this equipment can do the job and play an excellent role.
Intelligent positioning and automated drilling
The intelligent operation of Lanhi intelligent rock drilling trolley is a highlight. The vehicle has an automatic positioning function, combined with the automatic adjustment of the boom posture, it can accurately reach the predetermined drilling position to ensure the accuracy and efficiency of the operation. What is even more commendable is that users can directly import the pre-designed drilling layout into the control system of the rock drilling trolley, thereby realizing automated drilling, greatly reducing manual intervention and improving the safety and accuracy of the operation. This automated drilling process not only improves construction efficiency, but also reduces the errors and risks caused by human operation.
Convenient aerial work platform
In order to ensure the safety and comfort of operators, Lanhi intelligent rock drilling trolley is equipped with a work service platform to provide workers with a safe aerial working environment. This design not only facilitates the workers' operation and reduces the risk of high-altitude operations, but also improves the efficiency and comfort of the operation, reflecting the humanized design concept of the equipment. It enables operators to quickly and safely complete various high-altitude operation tasks, further improving the overall efficiency of the construction.
Lanhi intelligent rock drilling trolley, as a special equipment for mining drilling and blasting, provides excellent solutions for operations in mining, tunneling and other fields through its high-power rock drill, automatic control system and humanized design, and helps the smooth progress of engineering projects. It not only improves the operating efficiency, but also significantly improves the safety and accuracy of the operation. It is an indispensable intelligent partner for modern mining and tunnel construction.
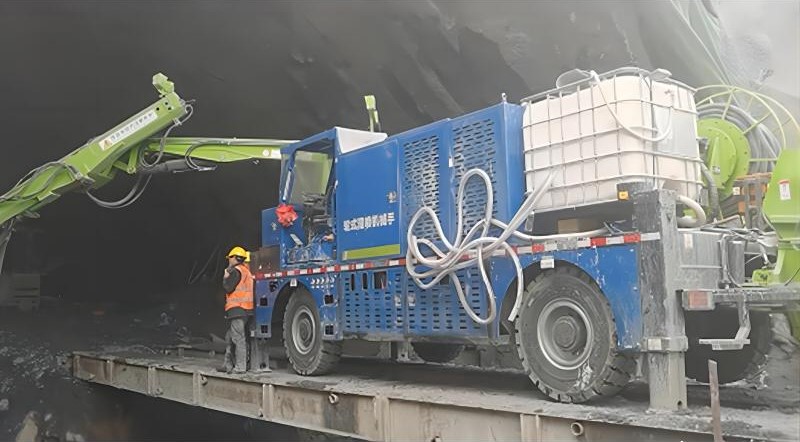
Advantages, characteristics, and application fields of tunnel wet spraying robotic arm
Tunnel wet spraying manipulator is an indispensable and important equipment in modern tunnel engineering, widely used in shotcrete support construction in railway and highway tunnels, water conservancy and hydropower culverts, underground mines and other fields. Compared with traditional dry spraying equipment, wet spraying robots have significant advantages in construction quality, efficiency, and safety.
Improve construction quality and efficiency
The wet spraying robot uses wet spraying concrete, which can cover the tunnel wall more evenly than dry spraying equipment, greatly improving the construction quality. The wet spraying method of concrete has better adhesion and flowability during the spraying process, which can ensure the compactness and uniformity of the concrete layer, effectively reducing the occurrence of voids and cracks. In addition, the wet spraying robot has a high degree of automation and simple operation, which can significantly improve construction efficiency and shorten the project cycle.
Reduce rebound rate
During the spraying process of dry spraying equipment, concrete is prone to rebound, resulting in material waste. The rebound rate of wet spraying robotic arms is relatively low, allowing concrete to better adhere to the construction surface, significantly reducing material waste and lowering construction costs. This not only saves resources, but also enhances the environmental friendliness of construction.
reduce labor intensity
The use of wet spraying robotic arms greatly reduces the labor intensity of workers. Traditional dry spraying construction requires workers to operate in close proximity for a long time, which not only consumes a lot of physical energy but also faces high risks. The automation operation of the wet spraying robotic arm reduces the direct involvement of workers, who only need to monitor and adjust within a safe distance, greatly reducing physical labor and construction difficulty.
Improving the health status of workers
The construction environment of tunnels usually has a lot of dust, and dry spraying equipment can generate a large amount of dust, which poses a serious threat to the health of workers. The wet spraying robotic arm effectively reduces the generation of dust, lowers the risk of workers inhaling harmful dust, and significantly improves the air quality at the construction site. This not only ensures the health of workers, but also meets the requirements of modern environmental protection construction.
Tunnel wet spraying robotic arm plays an important role in tunnel construction due to its superior performance. By improving construction quality and efficiency, reducing rebound rate, reducing labor intensity, and improving the health status of workers, wet spraying robots not only enhance the safety and economy of construction, but also promote the development of tunnel engineering towards a more environmentally friendly and efficient direction. As the core equipment for tunnel construction, wet spraying robotic arm is undoubtedly an important innovation in modern engineering construction.
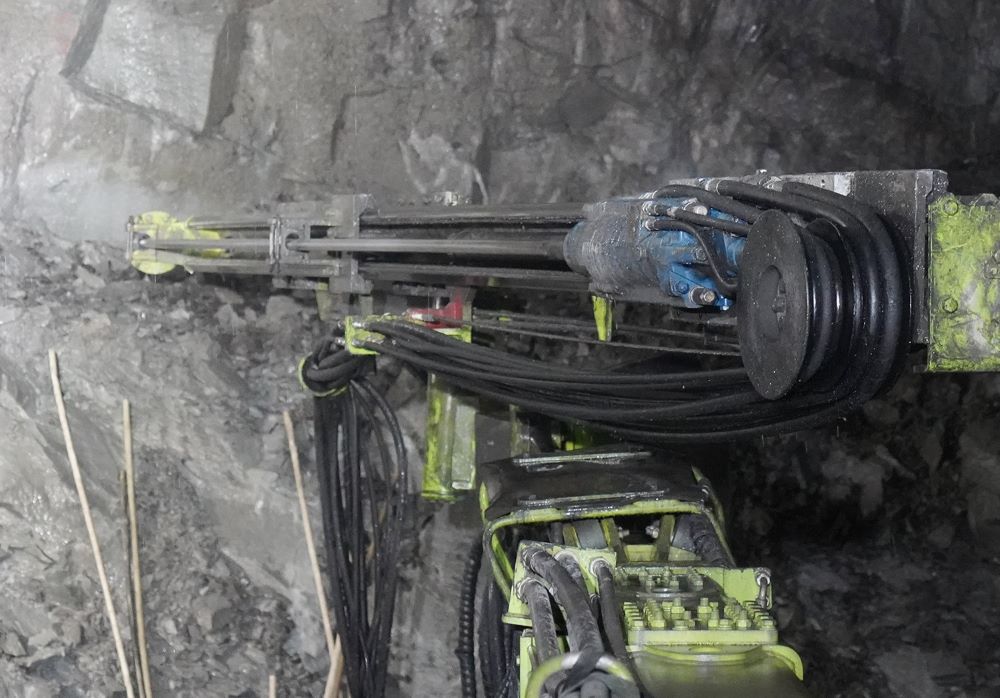
Tunnel anchor drill, an underground engineering equipment used for installing anchor rods in tunnels to provide support
Tunnel anchor drilling rig is a kind of equipment specially used in tunnel and underground engineering, which is used to install anchors to provide support. Here are some main contents about tunnel anchor drilling rig:
1. Purpose
Tunnel anchor drilling rig is mainly used for initial support and reinforcement of tunnel. By drilling holes in the tunnel wall and installing anchors, the stability of the tunnel structure can be improved, and landslides and rock displacement can be prevented.
2. Working principle
Tunnel anchor drilling rig drives the drill tool through a hydraulic or electric system to drill holes in the tunnel surrounding rock. After the drilling is completed, the anchor is inserted into the hole and fixed in the rock layer by grouting or mechanical locking, thereby playing a supporting role.
3. Classification
Tunnel anchor drilling rigs can be divided into the following categories according to the power source and usage scenario:
- Hydraulic anchor drilling rig: driven by a hydraulic system, suitable for most tunnels and underground projects.
- Electric anchor drilling rig: driven by electricity, suitable for engineering scenarios with sufficient power supply.
- Handheld anchor drill: suitable for working in narrow spaces, easy to operate, but relatively small in power.
4. Features
- Efficient construction: can quickly and accurately drill holes on the tunnel wall and install anchors, improving construction efficiency.
- Adapt to different geology: can work in rocks and soils of various hardnesses, adapting to different tunnel geological conditions.
- Precision drilling: ensure the accuracy and verticality of the drilling, and ensure the installation quality of the anchor.
- Flexible operation: many tunnel anchor drills have flexible operating arms that can cope with different angles and position requirements.
5. Application scenarios
- Initial tunnel support: reinforce the tunnel wall by installing anchors to improve the stability of the tunnel.
- Tunnel reinforcement and repair: when problems occur in existing tunnels, anchor reinforcement operations are carried out.
Tunnel anchor drills are widely used in the construction of railway and highway tunnels, especially in rock tunnels, playing a key support role. It is also used in the reinforcement construction of underground spaces such as mine tunnels, underground parking lots and subway projects.
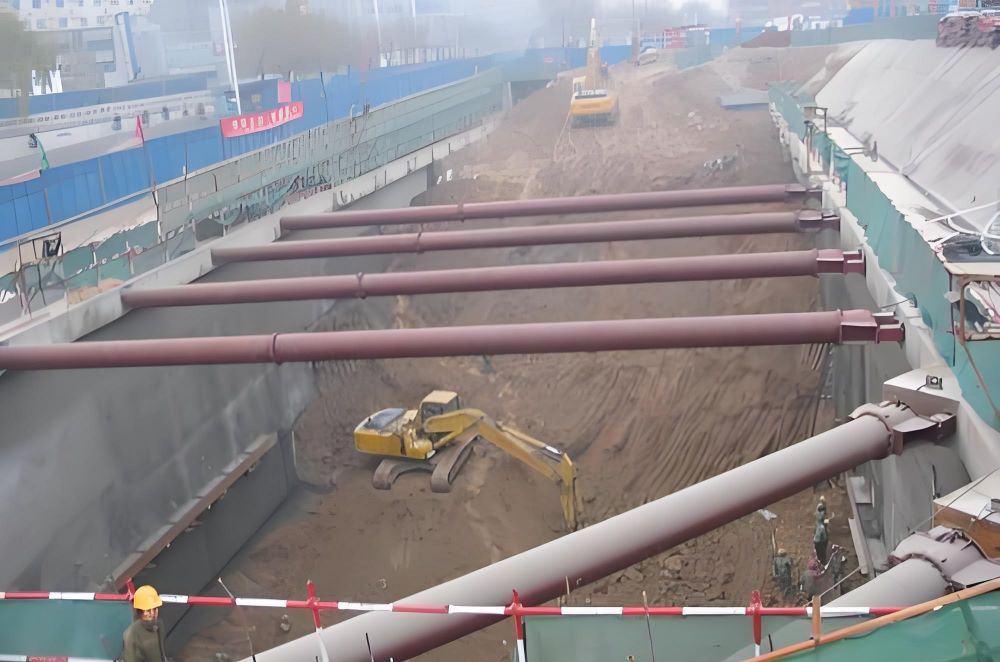
Advantages and disadvantages of open excavation method and construction steps
Open Cut Method is a common method for tunnel or underground structure construction, mainly used for the construction of shallow buried tunnels and underground buildings. This method excavates the ground first, completes the construction of the tunnel or underground structure, and then backfills and restores the surface. The following are some key steps and characteristics of the open cut method:
I、Advantages and Disadvantages of Open Cut Method
1. Advantages:
1> Simple construction: The open cut method is relatively simple to operate and is suitable for shallow buried tunnels and underground structures.
2> Low cost: Compared with other tunnel construction methods (such as shield method or mining method), the construction cost of the open cut method is usually lower.
3> Fast construction progress: Since the surface is completely exposed, the transportation and installation of construction equipment and materials are more convenient, and the construction speed is faster.
2. Disadvantages:
1> Large impact on the environment: Surface excavation will have a greater impact on the surrounding environment, especially in densely populated urban areas, which may cause traffic disruptions, noise and dust pollution.
2> Limited scope of application: The open-cut method is only applicable to shallow buried projects, not deep buried tunnels and underground structures.
3> Risk of surface subsidence: If the construction process is not properly controlled, it may cause surface subsidence and affect the safety of surrounding buildings.
II、Construction steps of the open-cut method
1. Surface excavation: First, fence the construction area and dig up the surface soil until the design elevation is reached. Slope stability needs to be considered during excavation, and support structures (such as retaining walls or soil nail walls) may be used to prevent collapse.
2. Support structure construction: After excavating to the designed depth, temporary or permanent support structures are installed according to geological conditions and construction requirements to ensure the stability of the excavated space.
3. Structural construction: Construction of tunnels or underground buildings in the excavated space, usually including the casting or installation of the bottom plate, side walls and top plate.
4. Waterproofing and drainage: In order to prevent groundwater from infiltrating, waterproofing measures will be taken during the construction process, such as laying a waterproof layer or drainage system to ensure the dryness and stability of the structure.
5. Backfilling and surface restoration: After the structure is completed, backfilling operations are carried out, the earthwork is compacted layer by layer, and finally the surface is restored to its original or designed state, such as restoring roads, green spaces or other surface facilities.
Open-cut method is widely used in shallow buried projects such as subway stations, underground passages, and underground pipe galleries. With the advancement of urbanization, open-cut method plays an important role in the development of urban underground space.
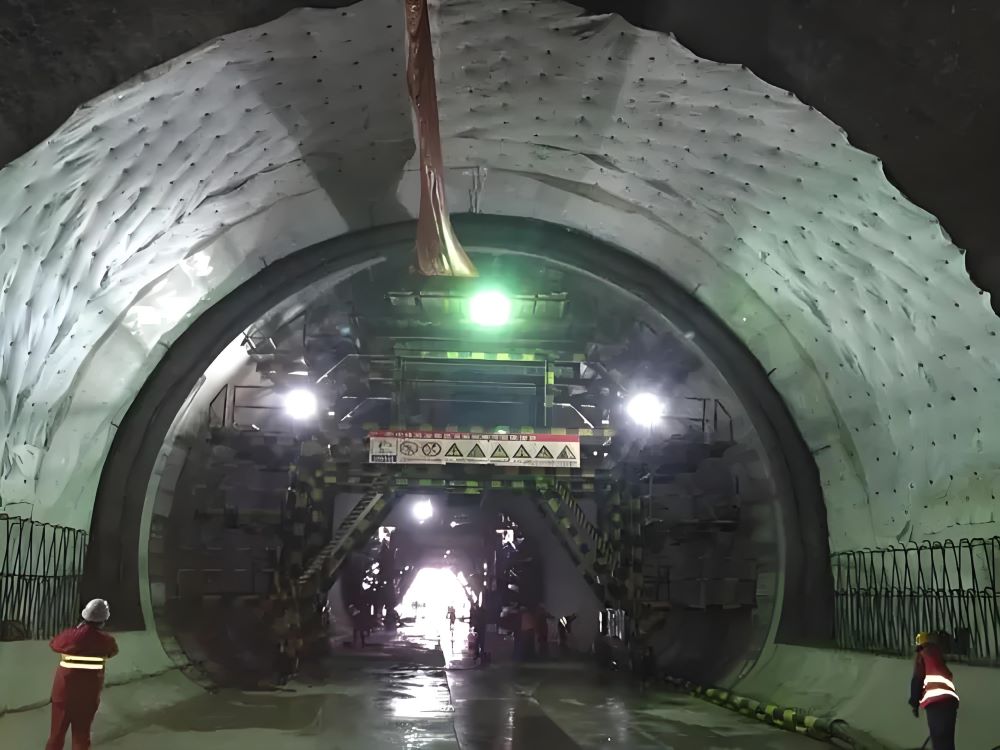
What are the construction methods for integral lining? Types and precautions of construction methods for integral lining
What are the construction methods for integral lining? The construction methods of integral lining are mainly divided into the following categories, each with its applicable scenarios and characteristics, as well as the construction precautions for integral lining.
I、Construction method of integral lining
1. Sliding mode construction method
The sliding formwork construction method is a relatively advanced method in the construction of integral lining. It uses a continuously rising sliding formwork to pour and form in one go, and has the advantages of fast construction speed, good integrity, and smooth surface. Suitable for long-distance and large section tunnel lining construction.
2. Trolley construction method
The trolley construction method uses movable trolleys as templates and is suitable for medium length tunnel construction. During construction, the trolley is in place, the formwork is fixed, and then concrete pouring is carried out. After the concrete reaches a certain strength, move the trolley to the next position and repeat the construction process. This method is flexible in construction and has strong adaptability.
3. Segmented construction method
For projects with complex geological conditions and significant changes in tunnel cross-sections, the segmented construction method can be adopted. According to the different geological conditions and tunnel sections, the lining is designed and constructed in sections, and the construction of the next section is carried out after each section is completed. This method has high flexibility, but relatively low construction efficiency.
4. Assembled integral lining
Prefabricated integral lining is a type of prefabricated component assembly, which involves prefabricating concrete lining sections in the factory and then assembling them inside the tunnel. This method has a fast construction speed, but requires high precision for prefabricated components and requires significant transportation and lifting space.
5. Spray concrete lining
Although shotcrete lining itself is not a typical construction method for integral lining, in some special conditions such as rapid construction or unstable geological conditions, shotcrete can be used as initial support first, and integral lining can be constructed when conditions permit.
II、 Construction precautions
1. When selecting construction methods, factors such as geological conditions, cross-sectional size, construction conditions, and schedule requirements of the tunnel should be fully considered.
2. Adequate preparation should be made before construction, including geological survey, design optimization, construction organization design, etc., to ensure construction quality and safety.
3. During the construction process, the quality of concrete should be strictly controlled to ensure the strength and durability of the lining.
4. Pay attention to construction safety, especially when working in environments with complex geological conditions and abundant groundwater, effective safety measures should be taken.
The construction method selection of integral lining should comprehensively consider multiple factors to achieve the best engineering effect and economic benefits.
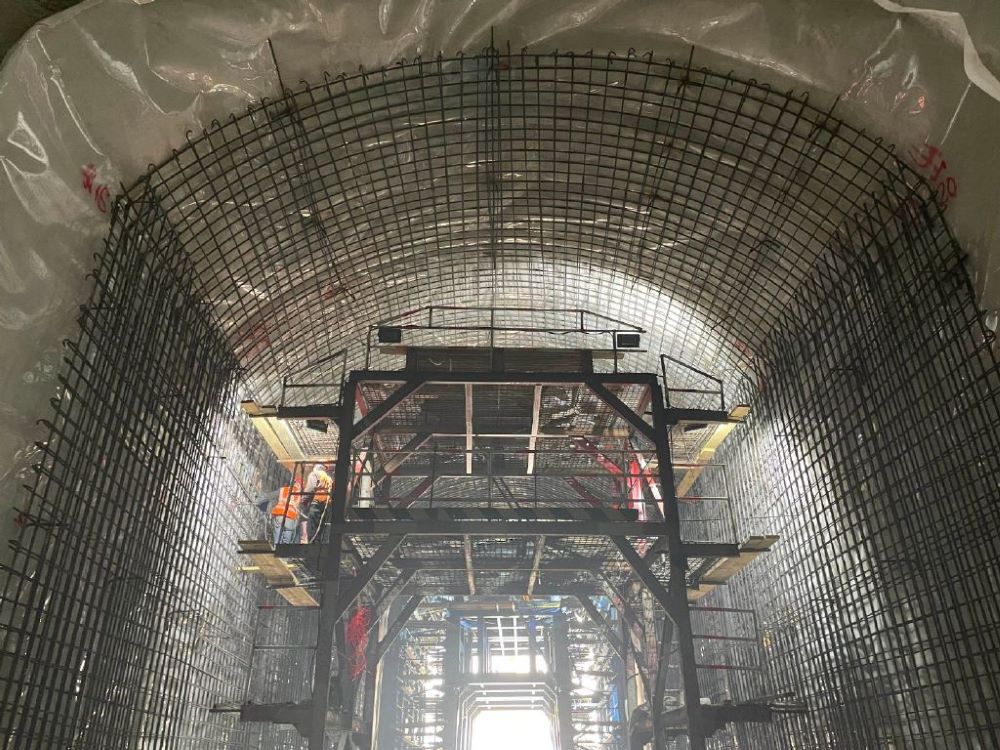
The structural characteristics, construction technology, and application scenarios of integral lining
Integrated lining is an important form of support in tunnel construction. Its main function is to provide a sturdy and stable inner wall for the tunnel to resist external soil pressure, groundwater pressure, and possible seismic forces. At the same time, it can also improve the environmental conditions inside the tunnel, such as reducing water seepage and improving ventilation efficiency.
Structure and Characteristics
Integral lining is usually made of reinforced concrete or prestressed concrete, which has good integrity and durability. Its structural characteristics are as follows:
1. Integrity: The integral lining is continuously poured or assembled to form a seamless whole, which can effectively disperse loads and improve the safety and stability of the structure.
2. High stiffness: Compared to other forms of lining, integral lining has higher stiffness, which can better resist external loads and reduce deformation.
3. Good waterproof performance: By setting a waterproof layer inside the lining, the integral lining can effectively prevent groundwater infiltration and protect the internal structure of the tunnel from erosion.
4. Strong durability: Using high-quality concrete materials and construction techniques, the integral lining has a longer service life and reduces the frequency of maintenance and repair.
Construction technology
The construction of integral lining usually includes the following steps:
1. Excavation and initial support: Firstly, the tunnel outline is formed through excavation, and then initial support is carried out to ensure construction safety.
2. Waterproof layer construction: Before lining, lay a waterproof layer to prevent groundwater infiltration.
3. Template installation: Install templates according to design requirements to ensure the shape and size of the lining.
4. Concrete pouring: Use a concrete pump or pouring equipment to evenly pour concrete into the formwork to form a lining.
5. Maintenance and formwork removal: After the concrete is poured, maintenance is carried out, and the formwork is removed after reaching a certain strength.
Application scenarios
Integrated lining is widely used in subway tunnels, highway tunnels, water conservancy tunnels, mining tunnels and other engineering projects, especially in situations with complex geological conditions, abundant groundwater or high requirements for tunnel stability. The advantages of integrated lining are more obvious.
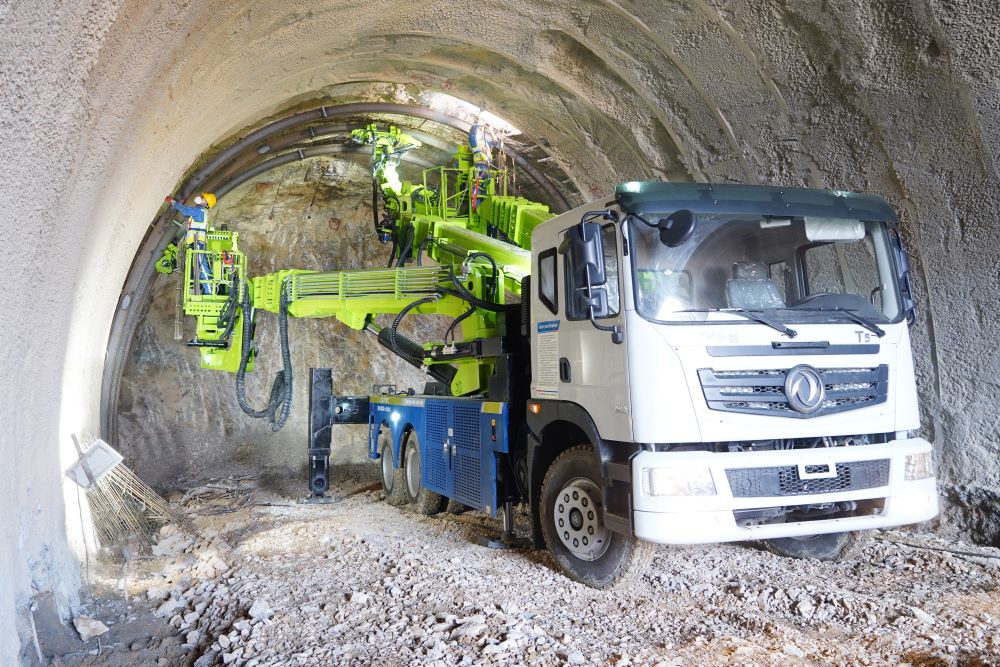
What is prefabricated arch installation? Steps and precautions for installing prefabricated arches
What is prefabricated arch installation? Prefabricated arch installation is a commonly used construction technique in modern bridge, tunnel, and large building construction. It combines the high efficiency of prefabricated components with the flexibility of on-site installation, which can significantly improve construction speed and quality, while reducing construction costs and environmental impact. The following are the basic steps and precautions for installing prefabricated arches:
Basic steps
1. Design and prefabrication: In factories or prefabrication sites, high-precision mechanical equipment and molds are used to prefabricate arch components according to engineering design drawings. During the prefabrication process, it is necessary to strictly control the size and material quality to ensure the accuracy and stability of on-site installation.
2. Transportation and preparation: Prefabricated arch components are transported to the construction site by specialized transportation vehicles. Before installation, the site needs to be leveled and reinforced to ensure that the ground is stable and able to withstand the weight of the arch and construction loads.
3. Positioning and installation: Use a crane or other lifting equipment to lift the arch components to the predetermined position, and ensure that the levelness and verticality of the arch meet the design requirements through precise measurement and adjustment. During the installation process, temporary support structures may be required to ensure the stability of the arch frame before it is fully secured.
4. Connection and fixation: The connection between the arch components and between the arch and the ground is usually achieved through welding, bolt connection, or prestressed reinforcement. Quality inspection is required at the connection to ensure connection strength and sealing.
5. Acceptance and maintenance: After installation, strict quality inspection and acceptance are required to ensure the stability and safety of the arch structure. During use, regular maintenance checks should be conducted to promptly identify and address any potential damage or looseness, thereby extending the service life of the arch frame.
Precautions
·Safety first: During the construction process, it is necessary to strictly follow safety operating procedures, use qualified protective equipment, and ensure the safety of construction personnel.
·Environmental impact: The installation of prefabricated arches should minimize the impact on the surrounding environment, including noise control, waste disposal, and ecological protection.
·Quality control: Strict quality control is required at every stage from design to installation to ensure the structural safety and durability of prefabricated arches.
The continuous development and innovation of prefabricated arch installation technology provide more efficient, environmentally friendly, and safe construction solutions for the modern construction industry, and are an important force in promoting the industrialization of construction and the development of green buildings.
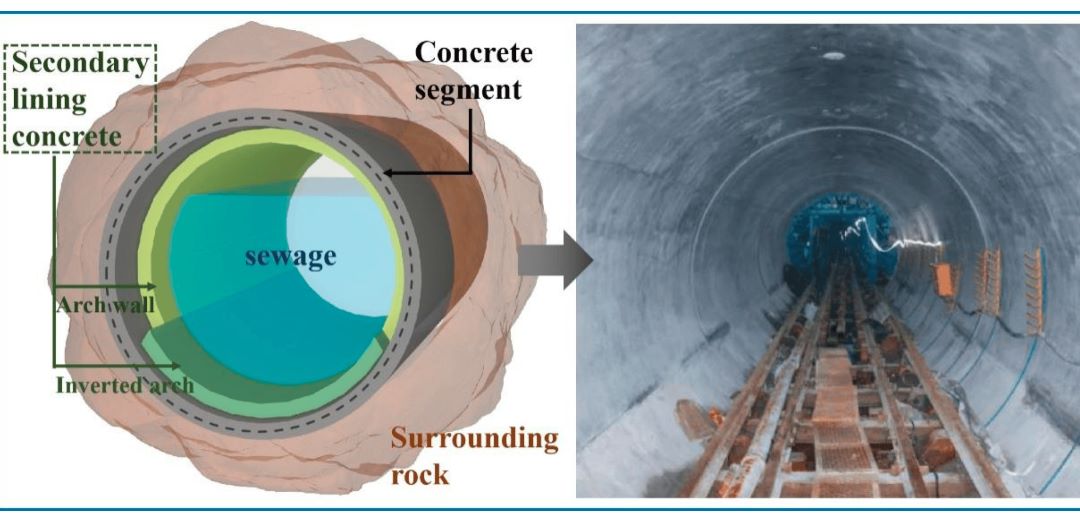
What is the role of secondary lining in composite lining?
Secondary lining plays a crucial role in composite lining systems and is an important component of tunnel structures. It is mainly used to enhance the overall stability of tunnels and provide long-term support and protection. Composite lining usually includes initial support (such as shotcrete, anchor rods, and steel arches) and secondary lining, and the combination of the two can more effectively cope with various geological conditions and stress changes encountered during tunnel excavation and later operation.
Secondary lining plays the following important roles in composite lining:
I、 Bearing function
1. Provide long-term stable support
-The initial support mainly bears the immediate pressure of the surrounding rock after excavation during the construction process, but over time, the deformation of the surrounding rock may continue to develop. As a structure constructed in the later stage, the secondary lining can provide long-term stable support for the tunnel and jointly bear the surrounding rock pressure with the initial support.
-For example, in soft rock tunnels, the creep characteristics of the surrounding rock are obvious, and secondary lining can effectively control the long-term deformation of the surrounding rock, ensuring the safety and stability of the tunnel structure.
2. Take on some of the water pressure
-When there is groundwater in the tunnel, the secondary lining can bear some of the water pressure, especially in the case of local defects in the waterproof layer. The secondary lining can play a certain role in waterproofing and anti-seepage, preventing groundwater from damaging the tunnel structure.
-In areas like Shenzhen with abundant groundwater, the anti water pressure effect of secondary lining is particularly important.
II、 The role of safety reserve
1. Improve the safety factor of the tunnel
-As a safety reserve, secondary lining can play a timely role in preventing serious accidents such as tunnel structure collapse when local damage or insufficient bearing capacity occurs in the initial support.
-For example, when a tunnel encounters unexpected disasters such as earthquakes or explosions, secondary lining can provide additional protection for personnel and equipment inside the tunnel.
2. Ensure construction safety
-During tunnel construction, the application of secondary lining can provide a relatively safe working environment for construction personnel. Especially in areas with complex geological conditions and poor rock stability, timely construction of secondary lining can reduce construction risks and ensure smooth progress of construction.
3、 Waterproof function
III. Form a waterproof barrier
-The secondary lining is usually poured with concrete with good impermeability performance, and a waterproof layer is set between it and the initial support to jointly form the waterproof system of the tunnel. The secondary lining can effectively prevent groundwater from seeping into the interior of the tunnel, ensuring the normal functioning of the tunnel.
-Taking tunnels in the Shenzhen area as an example, due to their proximity to the ocean and high groundwater levels, the waterproof effect of the secondary lining is crucial for the durability of the tunnel.
2. Prevent leakage from damaging the structure
-The leakage of groundwater not only affects the functionality of tunnels, but also causes corrosion and damage to tunnel structures. The good waterproof performance of the secondary lining can avoid the erosion of groundwater on the initial support and internal facilities of the tunnel, and extend the service life of the tunnel.
IV、 Aesthetic and decorative effects
1. Improve the internal environment of the tunnel
-The surface of the secondary lining can be leveled and decorated to make the interior of the tunnel more beautiful and tidy, improving the comfort and safety of driving.
-For example, fireproof and anti-corrosion coatings can be applied to the surface of the secondary lining, and lighting facilities and signage can be installed to provide good visual effects and directional information for tunnel users.
2. Enhance the overall image of the tunnel
-For some important traffic tunnels or urban underground passages, the appearance quality of the secondary lining directly affects the overall image of the tunnel. Through careful design and construction, the secondary lining can become a beautiful scenery line in the city.
The role of secondary lining in composite lining systems is multifaceted. It not only enhances the safety and stability of tunnel structures, but also provides various functions such as waterproofing, fireproofing, and anti-corrosion. It is an important component to ensure the long-term safe operation of tunnels.
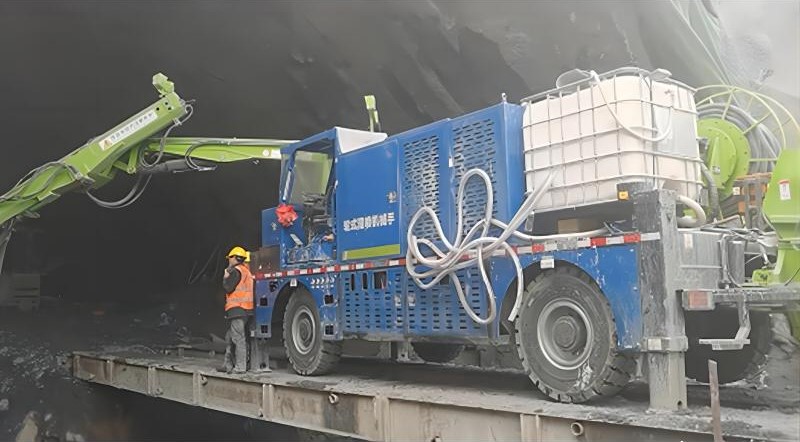
Advantages of hydraulic wet spraying trolleys in underground engineering and modern tunnel construction
In the field of modern tunnel construction and underground engineering, hydraulic wet spraying trolleys, as an innovative technology, are gradually replacing traditional dry spraying processes, bringing significant benefits and environmental advantages to the industry. Its core advantage is to significantly reduce the dust concentration in the working environment, reduce the rebound rate, and improve the quality of sprayed concrete, thereby providing strong protection for the health of construction workers and engineering efficiency.
1. Dust control, protect the health of workers
In the traditional dry spraying process, high concentrations of dust not only seriously deteriorate the working environment, but also pose a potential threat to the respiratory system of construction workers. In contrast, the hydraulic wet spraying trolley greatly reduces the dust generation during the spraying process by pre-mixing concrete with water, effectively improving the working environment and ensuring the health and safety of workers.
2. Reduce rebound rate and improve material utilization
In the dry spraying process, the high rebound of concrete often leads to serious material waste. The hydraulic wet spraying trolley can significantly reduce the rebound rate of concrete by accurately controlling the water-cement ratio. According to measured data, the rebound rate can be reduced from 15%-50% to below 10%, which greatly improves the utilization rate of materials and reduces costs.
3. Improve concrete quality and ensure project quality
The advantages of wet spraying technology are also reflected in the improvement of concrete quality. By accurately controlling the water-cement ratio, the hydraulic wet spraying trolley ensures the uniformity and stability of concrete, avoids the poor hardening phenomenon caused by uneven moisture, thereby greatly improving the quality of sprayed concrete and providing a solid guarantee for the durability and safety of the project.
The wide application of hydraulic wet spraying trolleys marks a technological innovation in the field of tunnel construction and underground engineering. It not only effectively improves the working environment and ensures the health of construction workers, but also makes important contributions to the economic benefits and sustainable development of engineering projects by improving material utilization and concrete quality.