Why choose us
Products
Cases
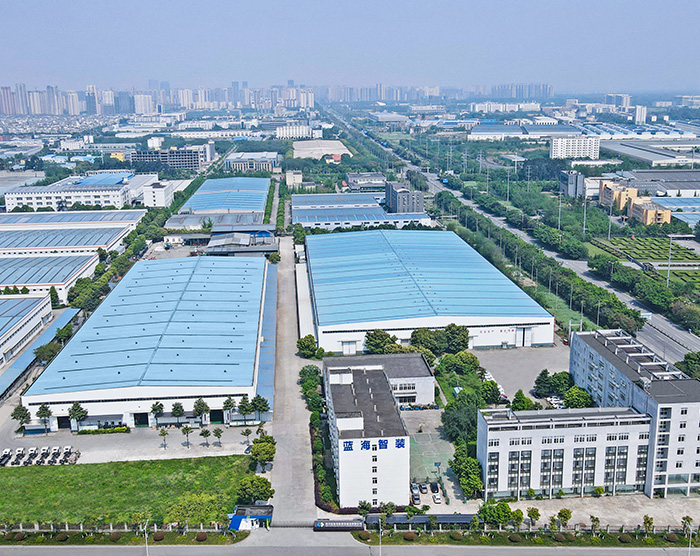
About Us
Since its establishment in 2011, Sichuan Lanhai Intelligent Equipment Manufacturing Co., Ltd. has dedicated itself to the exploration creation, manufacturing, and sales of total solutions for underground engineering machinery and intelligent mining equipment. The company has achieved a number of prestigious honors, including being recognized as a High and new technology enterprises, "Little Giants" , National Intellectual Property Advantage Enterprises a Sichuan Enterprise Technology Center, and a Chengdu Academician (Expert) Innovation Workstation. The company maintains a quality-oriented approach and has successfully obtained certifications for ISO9001 quality management, ISO14001 environmental management, and ISO45001 occupational health and safety management. The company's headquarter is located in the National Cross Strait Science and Technology Industrial Development Park, Wenjiang District, Chengdu City, Sichuan Province, renowned as the “Land of Abundance.” It ...
1568 + Employees