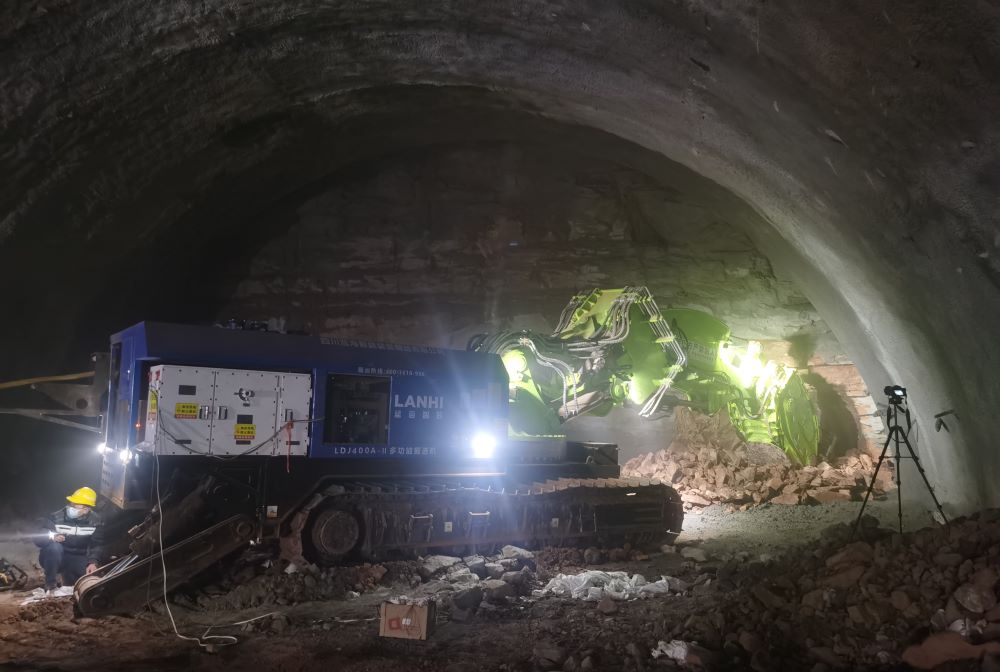
What scientific and technological advances can help reduce geological hazards during tunnel excavation and construction?
During tunneling and construction, many geological disasters such as water gushing, landslides and rock bursts may be encountered, which have a significant impact on tunneling construction. Therefore, reducing and preventing geological disasters in tunneling and construction has become a very important task. So, what scientific and technological methods can help reduce geological disasters in tunneling and construction?
With the development of science and technology, many new technologies have been applied to tunnel construction to help reduce the occurrence and impact of geological disasters. Here are some key new technologies:
1. 3D geological modeling: Using high-precision geological exploration data and advanced software, a 3D geological model of the tunnel route can be created. This helps engineers more accurately predict the geological problems that may be encountered in tunnel construction, so as to plan and design corresponding countermeasures in advance.
2. Remote sensing technology: Through remote sensing technologies such as satellite images and drone aerial photography, a large-scale geological environment along the tunnel can be quickly assessed to identify potential geological risk areas.
3. Geological radar and seismic exploration: These non-destructive detection technologies can be used to detect geological structures in front of and around the tunnel, including faults, cavities, aquifers, etc., to provide real-time information for construction.
4. Automated and intelligent construction equipment: such as automated tunnel boring machines (TBMs) and unmanned transport vehicles, which can improve construction efficiency and safety and reduce disasters caused by human operating errors.
5. Real-time monitoring system: including laser scanning, inclinometers, stress gauges, vibration sensors and other monitoring equipment, which can monitor the deformation, stress state and hydrological conditions of the tunnel surrounding rock in real time, and timely detect potential signs of geological disasters.
6. Numerical simulation and emulation: using numerical simulation techniques such as finite element analysis (FEA) and discrete element method (DEM), the geological response during tunnel construction can be simulated on the computer, and the effects of various construction schemes can be predicted and evaluated.
7. Application of new materials: new high-performance concrete, fiber-reinforced composite materials, etc. can improve the durability and disaster resistance of tunnel support structures.
By comprehensively applying these new technologies, the safety of tunnel construction can be significantly improved, the occurrence of geological disasters can be reduced, and it can also help improve construction efficiency and reduce costs.
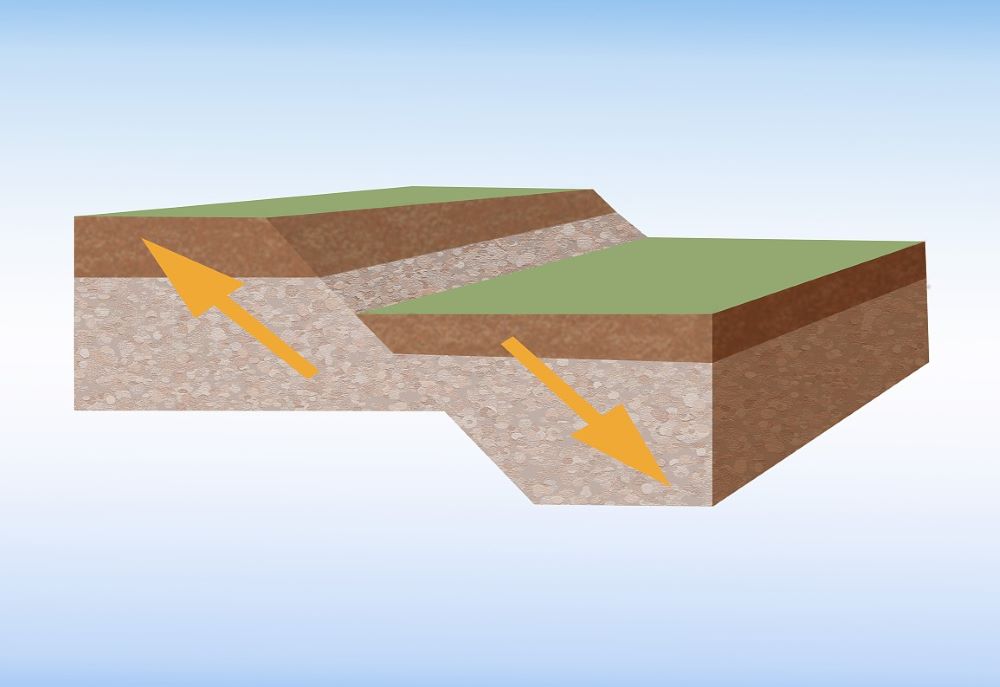
What is a normal fault? What are the characteristics of a normal fault and its common combinations?
What is a normal fault? A normal fault is a common geological structure in the earth's crust. It is a fracture phenomenon caused by the horizontal tensile stress on the crustal rocks. During the formation of a normal fault, the rocks in the upper part of the crust are vertically displaced relative to the rocks in the lower part along a fracture plane. After the fault is formed, the upper plate drops relatively and the lower plate rises relatively. This type of fault usually appears as a cliff or steep slope in the topography.
1. Characteristics of a normal fault
1.1 The fault plane is inclined and the upper plate rises relatively.
1.2 The inclination of the fault plane is usually steep, generally above 45 degrees.
1.3 The rocks on both sides of the fault may be dislocated due to fracture and displacement.
1.4 Normal faults are often associated with extension areas of the crust, such as rift valleys, basins and other geological structures.
The inclination of the cross section of a normal fault is steep, generally about 45 to 90 degrees, often greater than 45 degrees; the space occupied by the two plates of rock in the horizontal direction perpendicular to the fault direction is elongated. The rock fragmentation in the normal fault zone is relatively weak, breccias are mostly angular, ultra-fractured rocks are less obvious, and there are usually no complex small folds formed by strong compression.
Most normal faults are believed to be formed under the action of gravity and horizontal tension, so they are also called gravity faults. It can develop alone, or it can form a specific combination of a series of faults within a certain range and on a specific geological background. Common combinations include:
1.1 Graben: mainly composed of two normal faults with basically the same strike and tilted in opposite directions, with a common descending plate between the two normal faults;
1.2 Horst: mainly composed of two normal faults with basically the same strike and opposite tilt directions, with a common ascending plate between the two normal faults;
1.3 Step fault: composed of several normal faults with basically the same strike, and the upper plates of each fault fall in the same direction in turn, forming a step shape;
1.4 Ring fault: several arc-shaped semi-ring faults are arranged around a center or in concentric circles;
1.5 Radial fault: several faults are arranged toward a center or radially;
1.6 En echelon fault: several nearly parallel normal faults are staggered in an oblique manner;
1.7 Block fault: Two groups of large and medium-sized normal faults with different directions cut each other to form rectangular grid-shaped or diamond-shaped fault blocks.
Normal faults in nature vary in size, ranging from the dislocation of rock layers to the formation of mid-ocean ridges across the ocean. Some large-scale normal fault combinations are the result of regional extension, reflecting tectonic extension. In terms of landforms, large normal faults often form rifts, gullies, river valleys and lakes. For example, the Great Rift Valley of East Africa was formed in a tensile environment caused by plate movement, and normal faults are on both sides of it. In addition, in the Basin and Range region of the western United States, there are also landforms with alternating basins and mountains formed by normal faults.

What is the reason for the rebound of shotcrete? How to control the rebound amount of shotcrete?
Do you know what causes the rebound of shotcrete? How to control the rebound of shotcrete?
What causes the rebound of shotcrete?
The main reasons for the rebound of shotcrete are as follows:
1. Improper spraying operation:
- The spraying distance is too large: the impact force of concrete during the spraying process is weakened, and it cannot effectively adhere to the sprayed surface, resulting in increased rebound.
- The spraying angle deviation: The angle between the spray gun and the sprayed surface is not appropriate, so that the concrete cannot vertically impact the sprayed surface, reducing the bonding force and increasing the rebound.
2. Unreasonable wind pressure control: If the wind pressure is too high, the speed of the sprayed concrete will be too fast, and it will rebound after impacting the sprayed surface; if the wind pressure is too low, the concrete spraying will be weak and easy to rebound.
3. Mix ratio problem:
- Improper water-cement ratio: If the water-cement ratio is too large, the concrete slurry will be too thin, easy to flow and rebound; if the water-cement ratio is too small, the concrete will be too dry and hard, which is not conducive to bonding with the sprayed surface.
- Unreasonable sand ratio: Too high or too low sand ratio will affect the workability of concrete and increase rebound.
4. Raw material quality:
- Poor aggregate grading: Aggregate particle size is too large or too small, and grading is uneven, which will affect the performance of concrete and increase rebound.
- Unstable cement quality: Cement strength, setting time and other indicators do not meet the requirements, affecting the strength and bonding properties of concrete.
5. Condition of sprayed surface:
- Uneven sprayed surface: The surface is uneven, making it difficult for concrete to adhere evenly and easy to rebound.
- There are debris or floating dust on the sprayed surface: It affects the bonding between concrete and the sprayed surface, resulting in increased rebound.
6. Improper use of accelerator: The type and dosage of accelerator are not appropriate, which affects the setting time and early strength of concrete, thereby increasing rebound.
How to control the rebound of shotcrete?
Here are some ways to control the rebound of shotcrete:
1. Choose the right mix ratio: Determine the optimal ratio of cement, sand, stone, water and admixtures through experiments to improve the workability and cohesion of concrete.
2. Optimize the spraying process:
- Control the spraying distance: The distance between the nozzle and the sprayed surface should be kept at 0.6-1.2 meters. Too close or too far will increase the rebound.
- Master the spraying angle: The spray gun should be perpendicular to the sprayed surface, and the deflection angle should not exceed 10°.
- Control the spraying air pressure: According to factors such as the spraying distance and the length of the feed pipe, the air pressure should be reasonably adjusted, generally 0.1-0.15 MPa.
3. Improve the skills of operators: Train operators to master the spraying technology.
4. Improve the conditions of the sprayed surface: Remove pumice, debris, etc. on the sprayed surface to ensure that the sprayed surface is flat and clean to reduce rebound.
5. Segmented and pieced spraying: Spray in a certain order to avoid repeated spraying and missed spraying.
6. Use appropriate spraying equipment: choose a sprayer with good performance and uniform discharge.
7. Control the spraying speed: spray evenly and continuously to avoid fast and slow.
8. Add admixtures: such as using viscosity enhancers, accelerators, etc. to improve the performance of concrete and reduce rebound.
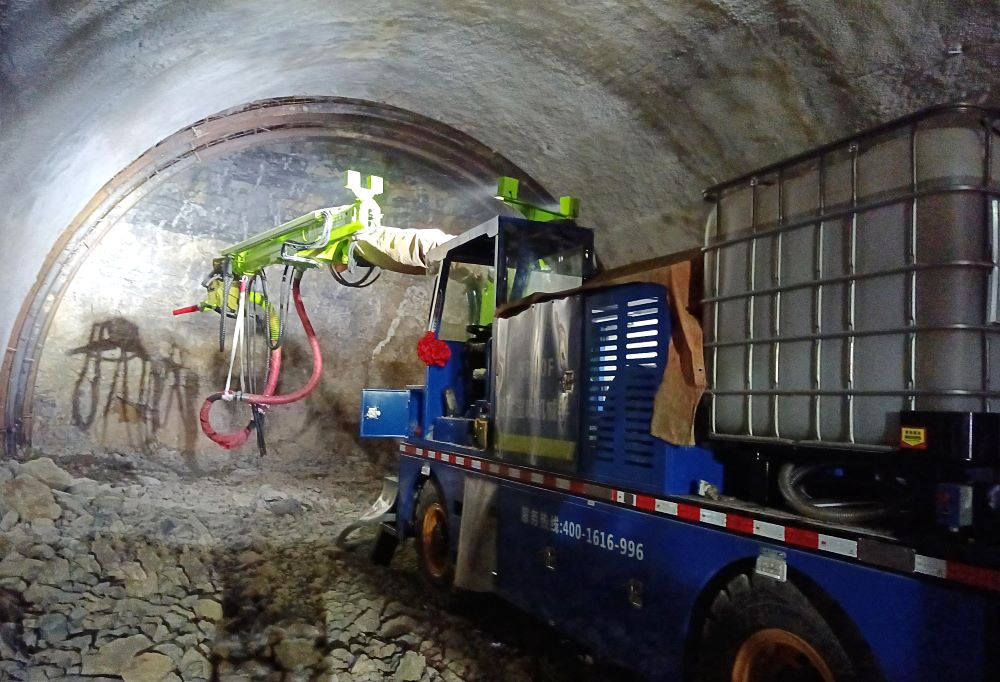
How to judge whether the spraying effect of a wet spraying manipulator meets the standard?
How to judge whether the spraying effect of a wet spraying manipulator meets the standard? To judge whether the spraying effect of a wet spraying manipulator meets the standard, it can be evaluated from the following 6 aspects:
1. Spraying uniformity:
Observe whether the wet spraying manipulator can form a uniform covering layer when spraying concrete, without obvious leakage or accumulation.
Check whether the spraying surface is flat and has no obvious unevenness to evaluate the uniformity of spraying.
2. Bonding strength:
Through laboratory testing or field tests, evaluate the bonding strength between the sprayed concrete and the base layer to ensure that it meets the design requirements.
Check whether the concrete after spraying is easy to fall off or hollowing, which is an important indicator for judging the bonding strength.
3. Rebound rate:
Measure the rebound rate of sprayed concrete, that is, the percentage of the weight of concrete that is not adhered to the construction surface to the total spraying weight.
According to relevant standards and specifications, the rebound rate should be controlled within a certain range. Too high a rebound rate may mean a waste of materials and energy.
4. Humidity control:
Ensure that the spraying humidity of the wet spraying manipulator is appropriate, neither too dry nor too wet, to ensure the workability of the concrete and the final construction quality.
Through on-site measurement and observation, evaluate the evaporation and absorption of water during the wet spraying process to ensure that the humidity is controlled in the best state.
5. Construction efficiency:
Evaluate the working efficiency of the wet spraying manipulator, including the spraying volume per unit time, the convenience of operation, and the contribution to the construction progress.
Compare the working efficiency of wet spraying manipulators of different brands and select those that can improve construction efficiency.
6. Comply with regulatory requirements:
Ensure that the use and operation of the wet spraying manipulator comply with local building regulations and construction standards, including safety regulations, environmental protection requirements, etc.
Through the above evaluation methods, it is possible to comprehensively judge whether the spraying effect of the wet spraying manipulator meets the standards, providing a basis for subsequent construction quality control.

What are the functions of tunnel support? Introduction to several aspects of tunnel support
What are the functions of tunnel support? The functions of tunnel support are mainly reflected in the following aspects:
1. Stabilize surrounding rock: After tunnel excavation, the original geological stress balance is broken, and the surrounding rock may loosen, crack or even collapse. Tunnel support helps the surrounding rock maintain a new stress balance by providing external support force, prevents or slows down the deformation and damage of the surrounding rock, and ensures the stability of the tunnel.
2. Control deformation: Tunnel excavation will cause displacement and deformation of the surrounding strata. Excessive deformation may cause damage to the tunnel structure or affect its normal use. The support structure can limit the development of these deformations, maintain the geometry and size of the tunnel section, and meet the design and use requirements.
3. Waterproof and anti-seepage: Tunnel support not only plays a structural support role, but also often has a waterproof function. Especially in areas with complex hydrogeological conditions, the support structure can effectively prevent the infiltration and erosion of groundwater and protect the tunnel structure from the influence of moisture.
4. Provide a safe construction environment: During the tunnel construction process, timely and effective support can provide a safe working space for construction personnel and reduce the risk of safety accidents caused by the instability of the surrounding rock.
5. Extend the service life of the tunnel: Good support design can enhance the overall strength and durability of the tunnel, resist the erosion and damage of the external environment, and thus extend the service life of the tunnel.
6. Optimize the construction plan: According to different geological conditions and tunnel types, choosing the appropriate support method can optimize the construction plan, improve construction efficiency, and reduce engineering costs.
7. Adapt to complex geological conditions: When encountering complex geological conditions such as faults, weak interlayers, and high ground stress areas, appropriate support measures can help the tunnel pass through these areas smoothly and ensure the smooth progress of the project.
8. Work together with the surrounding rock: Make the surrounding rock and support structure form an overall bearing system to give full play to the bearing capacity of the surrounding rock itself.
In short, tunnel support is an important means to ensure the safe, stable and efficient construction of tunnel projects, and it plays an irreplaceable role in improving the quality and benefits of tunnel projects.

The development history and application achievements of China's full-section boring machines
China started late in developing full-section boring machines, but after years of development, it has made remarkable achievements. In 1966, the former Shanghai Marine Machinery Factory produced China's first open boring machine with a diameter of 3.4 meters and reached the practical stage. However, due to limitations in technical performance and product quality at that time, research and development work was stalled for a time. Since the early 1990s, with the increase in the number of domestically imported boring machines, China has increased technology introduction and technical cooperation. This period marks that China's full-section boring machine technology has entered a new stage of development.
Employ technology introduction and independent research and development simultaneously
In the early 1990s, domestic infrastructure construction demand grew rapidly, and the application of full-section boring machines gradually became a trend. By introducing advanced foreign technologies and carrying out technical cooperation, many domestic manufacturers have begun to develop and produce full-section boring machines, and have achieved good social and economic benefits. At this stage, China's full-section boring machine technology has been rapidly improved.
Application of boring machines in major engineering projects
With the continuous expansion of the scale of China's infrastructure engineering construction, full-section boring machines have been widely used in many major engineering projects. For example, projects such as the Qinling Railway Tunnel, the Water Diversion Tunnel from Da Da to Qin, the Wanjiazhai Water Diversion Tunnel from Yellow River to Shanxi, the Tianshengqiao II Hydropower Station Water Diversion Tunnel, and the Dahuofang Water Diversion Tunnel all use boring machines for construction. Through the implementation of these projects, China's tunnel boring machine construction technology has made great progress.
Refresh world records and economic benefits
In the process of practical application, some projects have set new world records for full-section boring machines and created significant economic benefits. For example, some tunnel boring machines achieved unprecedented tunneling speeds and tunneling lengths during the construction process, providing valuable experience for the implementation of subsequent projects. These successful cases have laid a solid foundation for the promotion and use of full-section boring machines in China, forming a virtuous cycle.
The development history of China's full-section boring machines has evolved from a late start to a gradual maturity, and has experienced the process of technology introduction, independent research and development and large-scale application. Through successful application in many major engineering projects, full-section boring machine technology has developed rapidly in China and achieved good economic and social benefits. This series of achievements not only improved China's technical level in the field of full-section boring machines, but also provided strong support for the implementation of subsequent projects, forming a virtuous cycle for the promotion and application of full-section boring machines in China.

What are the construction methods of tunnel support? Introduction to common tunnel support construction methods
What are the construction methods of tunnel support? There are many construction methods for tunnel support. Here are some common construction methods for tunnel support:
1. Anchor support: By drilling holes in the tunnel surrounding rock, inserting anchors, and using the tensile properties of anchors to enhance the stability of the surrounding rock. Anchors can be made of metal parts, polymer parts or other materials. The special structure of their heads and rods can play the role of suspension, composite beams and reinforcement.
2. Sprayed concrete support: After the tunnel is excavated, concrete is immediately sprayed on the surface of the surrounding rock to close the excavation surface and prevent the surrounding rock from loosening and deformation. Sprayed concrete can provide a certain support force and form a whole with the surrounding rock to jointly bear the surrounding rock pressure.
3. Steel support support: Steel structures such as steel arches and steel grids are used as supports, and are used in combination with sprayed concrete or anchors to enhance the support capacity of the tunnel. Steel support can provide greater rigidity and bearing capacity, and is suitable for situations with poor geological conditions or large deformation of the surrounding rock.
4. Advance support: Before tunnel excavation, the surrounding rock in front of the face is pre-reinforced to improve the stability and self-bearing capacity of the surrounding rock. Common advance support methods include advance small pipe grouting, advance anchor rods, etc.
5. Pre-reinforcement technology: The surrounding rock is pre-reinforced by grouting, soil nails, anchor cables and other means to improve its strength and stability. Pre-reinforcement technology can be carried out before or during tunnel excavation.
6. Secondary lining: After the initial support is completed, secondary lining construction is carried out to increase the durability and stability of the tunnel. Secondary lining can be made of materials such as concrete or reinforced concrete.
In actual construction, the appropriate support method should be selected according to the geological conditions, design requirements and construction conditions of the tunnel, and the construction should be carried out strictly in accordance with the construction process and quality requirements to ensure the safety and stability of the tunnel.
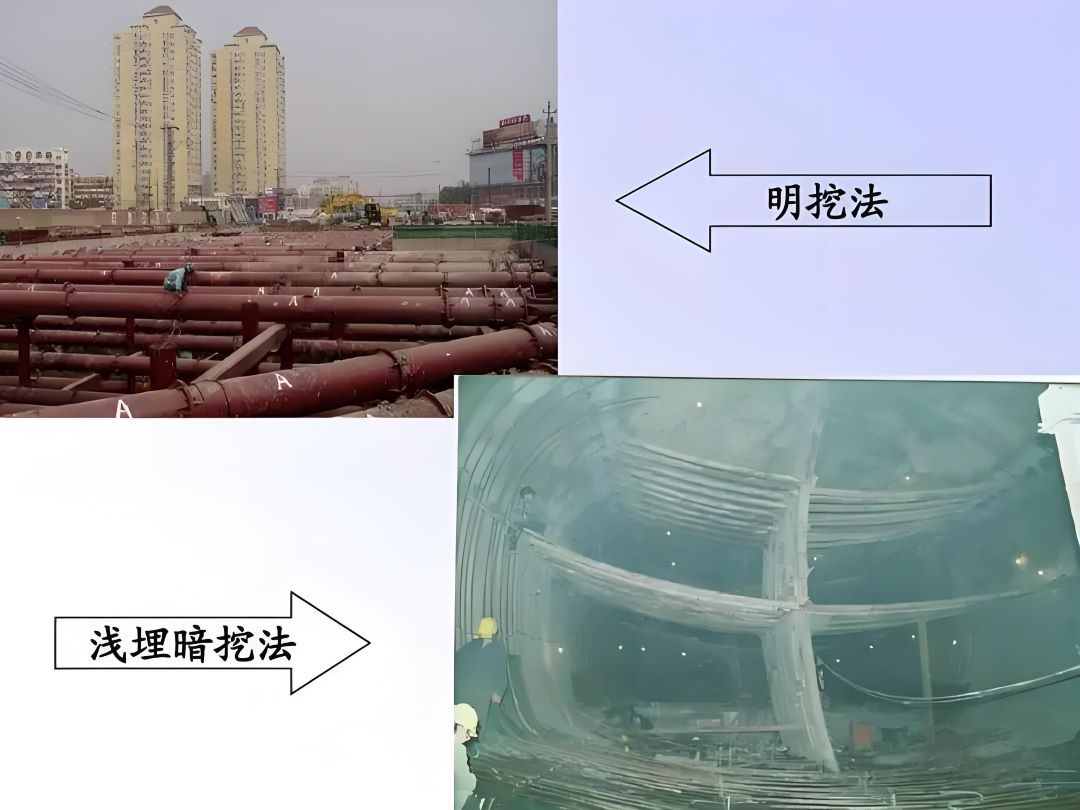
The characteristics and application scenarios of open and hidden excavation methods in underground engineering construction
Open cut and dark cut are two different underground construction methods, which play an important role in urban construction and infrastructure construction. Below I will introduce the characteristics and application scenarios of these two methods in detail.
1. Open cut method
Open cut method, also known as foundation pit method, refers to the underground construction method of first digging the ground, building lining in the open air, and then covering and backfilling. Open cut method is generally suitable for shallow buried tunnels, with the advantages of simple, fast, economical construction technology and good stress conditions of the main structure. But its disadvantages are also obvious, such as long traffic blocking time, noise and vibration. The construction process of open cut method generally includes foundation pit dewatering, slope reinforcement and foundation pit earthwork.
1.1 Features:
- Simple construction: no complex support system is required, and the construction process is relatively intuitive.
- Low cost: Compared with dark cut method, the construction equipment and technical requirements of open cut method are not high, so the cost is lower.
- Large impact range: The construction process will have a greater impact on ground traffic and the surrounding environment.
- Strong applicability: Suitable for areas with good geological conditions and low groundwater levels.
1.2 Application scenarios:
- Municipal pipeline laying, such as water supply, drainage, gas pipelines, etc.
- Shallow underground space development, such as underground shopping malls, parking lots, etc.
- Basic engineering construction, such as foundation excavation of bridges and buildings.
2. Concealed excavation method
Concealed excavation methods generally include drilling and blasting (mining) method, shield method, pipe jacking method, etc. Among them, the drilling and blasting method is a method of excavating rocks by drilling, charging, and blasting, and is mostly used in tunnel construction. The shield method is a fully mechanized construction method in the construction of concealed excavation. It is to push the shield machine into the ground, support the surrounding rock with the shield shell and pipe segments to prevent collapse into the tunnel, and use a cutting device to excavate the soil in front of the excavation face, transport it out of the cave through the excavation machinery, and pressurize it at the rear with a jack, and assemble prefabricated concrete pipe segments to form a mechanized construction method of tunnel structure. The pipe jacking method is a trenchless construction method that uses a jacking device to push the tool pipe or tunnel boring machine from the working pit through the soil layer to the receiving pit and lift it up. At the same time, the pipeline following the tool pipe or tunnel boring machine is buried between the two pits.
2.1 Features:
- Small impact on the ground: The impact on ground traffic and surrounding buildings during construction is small.
- High technical requirements: Professional tunnel boring machines and complex support systems are required.
- High cost: Due to the particularity of technology and equipment, the cost of the dark excavation method is usually higher than that of the open excavation method.
- Wide applicability: Applicable to various geological conditions, including soft soil, hard rock, etc.
2.2 Application scenarios:
- Metro tunnel construction, such as tunnel construction of urban rail transit.
- Construction of long-distance water and gas transmission tunnels.
- Tunnel projects of highways and railways crossing mountains or cities.
Open excavation and dark excavation have their own advantages. Which method to choose depends on the specific needs of the project, geological conditions, cost budget and consideration of the impact on the surrounding environment. In actual projects, these two methods are sometimes used in combination to achieve the best construction effect.
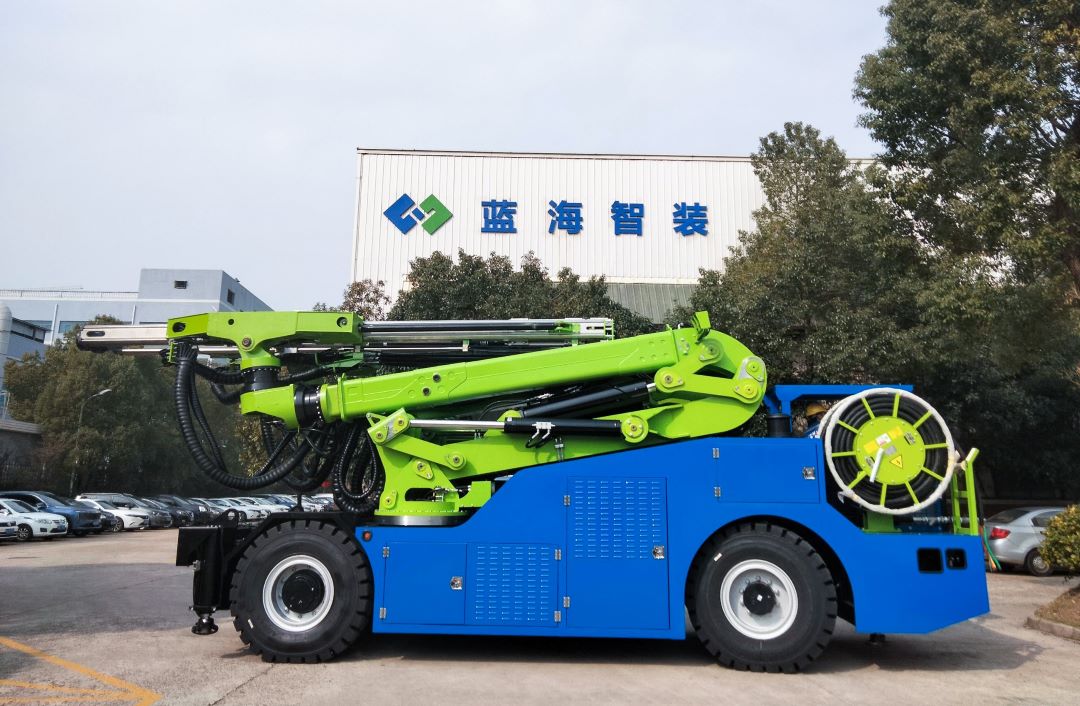
Rock drill, a rock breaking tool in the engineering field, is an indispensable tool in the mining/tunnel/foundation field
In the field of modern engineering, rock drills have become an indispensable key tool in mining, tunnel construction, infrastructure construction, and other fields due to their powerful rock breaking ability and excellent working performance. It not only greatly improves homework efficiency, but also reduces labor intensity, making important contributions to the progress and development of human society.
The working principle of a rock drill is based on the principles of mechanics and materials science in physics. By using a high-speed rotating chisel head to impact and break rocks, efficient mining of rocks can be achieved. At the same time, the rock drill is also equipped with advanced control systems and sensor technology, which can monitor the operation status of the equipment in real time, ensuring the safety and stability of the operation process.
With the continuous progress of technology, rock drills are also constantly innovating and developing. The new type of rock drill not only has higher rock breaking efficiency and better working performance, but also pays more attention to environmental protection and energy-saving design. For example, some modern rock drills adopt electric drive technology, reducing dependence on fuel and reducing exhaust emissions, which is beneficial for environmental protection.
In addition, rock drills have demonstrated extremely high flexibility and adaptability in practical applications. Whether it is hard or soft rock, whether it is large cross-section or small space, rock drills can handle various complex working conditions. At the same time, by cooperating with other mechanical equipment, such as loaders, excavators, etc., an efficient operating system can be formed, further improving engineering efficiency.
As a "rock breaking tool" in the engineering field, rock drills not only play an important role in modern construction, but also will maintain strong innovation momentum and market potential in future development. In the future, with the popularization and application of advanced technologies such as artificial intelligence and the Internet of Things, rock drills will usher in broader development prospects. Intelligent rock drills will have higher levels of autonomy and intelligence, enabling remote monitoring and fault diagnosis, providing engineers with more accurate and reliable data support.
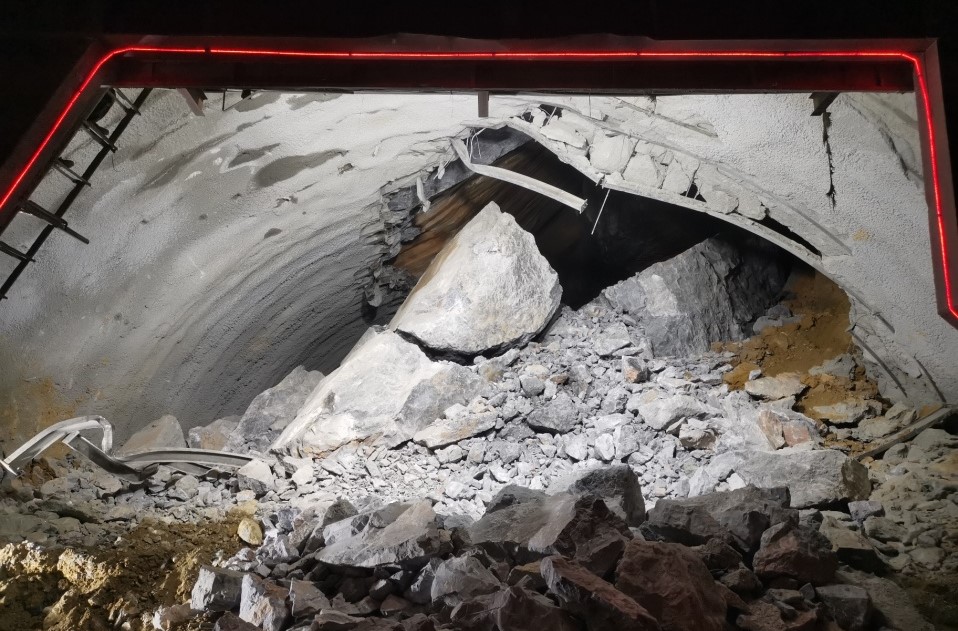
What should be done when encountering faults during tunnel construction? Ensure response measures for construction encountering faults
What should be done when encountering faults during tunnel construction? The treatment method for faults encountered during tunnel construction usually depends on the scale, nature, and construction conditions of the faults. Here are some common handling methods:
Pre detection and evaluation: Before construction, detailed detection and evaluation of faults are carried out through advanced technologies such as geological exploration and geological radar. This helps to understand the scale, direction, and relationship with surrounding rocks of faults, in order to develop appropriate construction plans.
1. Strengthen support: When encountering faults, measures to strengthen support should be taken, such as adding temporary support structures (such as steel supports, wooden supports, etc.) to prevent collapse and sliding. Meanwhile, depending on the scale and nature of the fault, more robust support materials and techniques may be required.
2. Control footage: Reduce the footage of a single excavation to minimize impact and damage to faults. By gradually approaching, gradually crossing the fault area.
3. Grouting reinforcement: Before crossing the fault, grouting technology can be used to reinforce the fault. By injecting materials such as cement slurry and chemical slurry into fault fissures to fill the gaps, the overall strength and stability of the rock can be improved.
4. Adjusting the construction plan: Depending on the specific situation of the fault, it may be necessary to adjust the original construction plan. For example, changing the excavation method (such as using step method instead of full section method), or adjusting the construction sequence.
5. Monitoring and early warning: During the construction process, strengthen monitoring of tunnel deformation, support structure stability, etc. By monitoring data in real-time, potential risks can be identified in a timely manner and corresponding response measures can be taken.
6. Emergency evacuation and rescue: Once a serious geological disaster occurs, such as collapse or flooding, the emergency plan should be immediately activated, personnel should be organized to evacuate to a safe area, and necessary rescue measures should be taken.
The above methods are not used in isolation, but are comprehensively considered based on actual situations and a combination of multiple measures are taken to address the fault problems encountered during tunnel construction. In practical operation, relevant safety regulations and technical standards should be strictly followed to ensure the safety and smooth progress of construction.