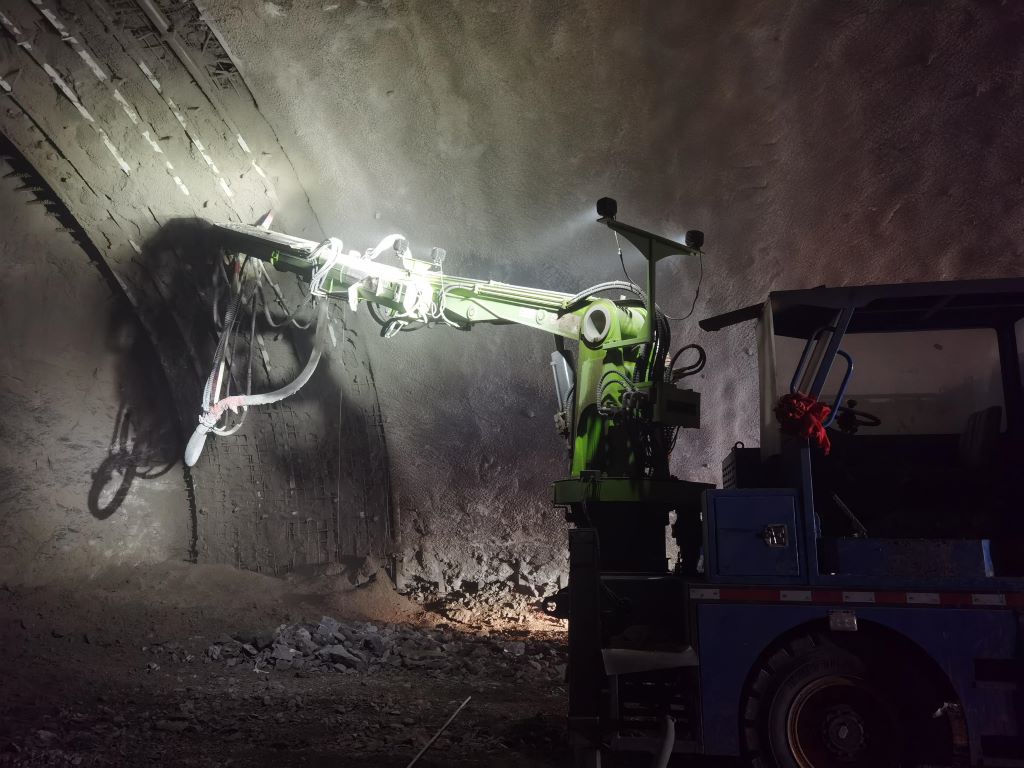
How to adjust the wet spraying manipulator to reduce rebound?
How to adjust the wet spraying manipulator to reduce rebound? To reduce the rebound of the wet spraying manipulator, the following adjustment measures can be taken:
1. Optimize the water-cement ratio:
The best water-cement ratio is determined through experiments. Generally, a higher water-cement ratio can reduce rebound, but it is necessary to ensure that it does not affect the strength and adhesion of the concrete.
2. Adjust the injection pressure:
Reduce the injection pressure. Excessive pressure may cause increased concrete rebound. However, too low pressure may affect the injection effect and coverage.
3. Improve the nozzle design:
Choose a nozzle suitable for the wet spraying process, such as a specially designed anti-rebound nozzle to reduce rebound.
Adjust the opening size of the nozzle to control the injection flow and particle size to reduce rebound.
4. Optimize the injection parameters:
Adjust the injection speed and angle so that the concrete can evenly cover the working surface and reduce local over-injection and rebound.
5. Improve construction skills:
Train operators to familiarize them with wet spraying technology and equipment operation to accurately control injection parameters and reduce rebound.
6. Use additives:
Add an appropriate amount of water reducer or other additives to the concrete to improve its workability and reduce rebound.
7. Improve the construction environment:
Try to reduce the wind speed at the construction site, such as setting up shelters when the wind is strong, or adjusting the construction time to avoid periods with high wind speeds.
8. Regular maintenance:
Regularly clean and maintain the wet spraying manipulator to ensure the cleanliness of the nozzle and other parts to prevent rebound caused by blockage.
By implementing the above measures, the rebound during the wet spraying process can be effectively reduced and the construction quality and efficiency can be improved. During the adjustment process, the rebound rate and spraying effect should be continuously monitored to ensure the best construction effect.
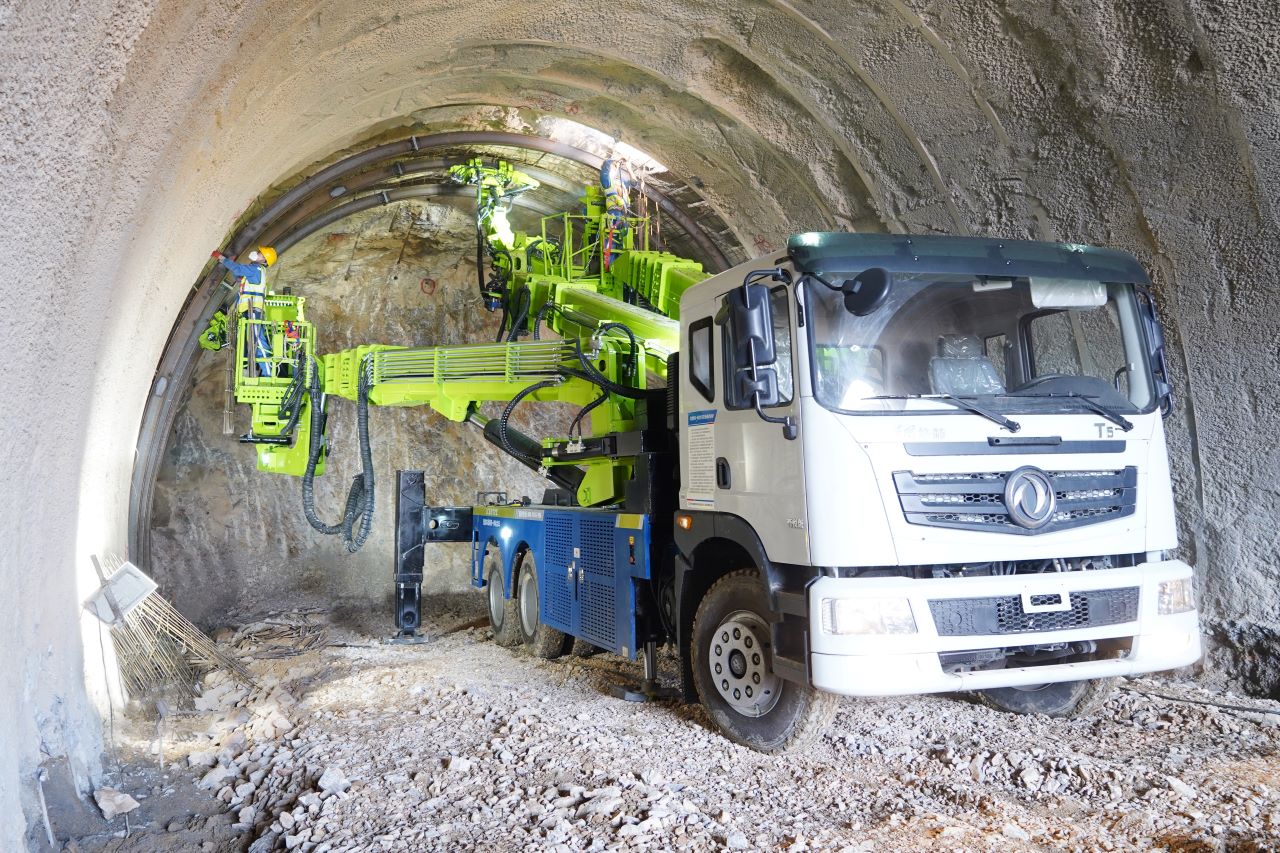
Applicable scenarios of Lanhi's arch frame integrated installation trolley
Lanhi's arch frame integrated installation trolley is exquisitely designed and powerful, suitable for a variety of construction scenarios:
1. Highway tunnel construction: Whether it is a two-lane or three-lane highway tunnel construction, this trolley can easily complete the arch frame installation task.
2. High-speed rail tunnel construction: For single-line or double-line high-speed rail tunnels, Lanhi's arch frame integrated installation trolley also performs well, ensuring efficient and accurate arch frame installation.
3. Under-excavation treatment: In tunnel construction, under-excavation treatment is an important link. This trolley can accurately complete this task and ensure the stability of the tunnel structure.
4. Charging operation: For blasting operations in tunnel construction, the trolley can safely and efficiently load charges to reduce construction risks.
5. Tunnel inspection: During and after the construction process, the quality inspection of the tunnel is crucial. Lanhi's arch frame integrated installation trolley is equipped with advanced testing equipment to ensure that the tunnel quality meets the standards.
6. Static high-altitude work: When performing static high-altitude work in the tunnel, this trolley provides a safe and stable platform to ensure the safety of construction workers.
The design concept of Lanhi's arch frame integrated installation trolley is to combine efficiency and safety. While increasing the construction speed, the various safety measures of the trolley also provide reliable protection for construction workers. Through the intelligent control system, operators can easily perform various operations, reduce errors in human operation, and improve the overall quality of construction.
Lanhi's arch frame integrated installation trolley has become an essential equipment in modern tunnel construction with its multi-functional, efficient, safe and intelligent characteristics. Whether it is highway or high-speed rail tunnel construction, this trolley is competent and provides a strong guarantee for the smooth completion of the project. With the continuous development of tunnel construction technology, Lanhi's arch frame integrated installation trolley will continue to play its important role and lead tunnel construction into a new era of intelligence.
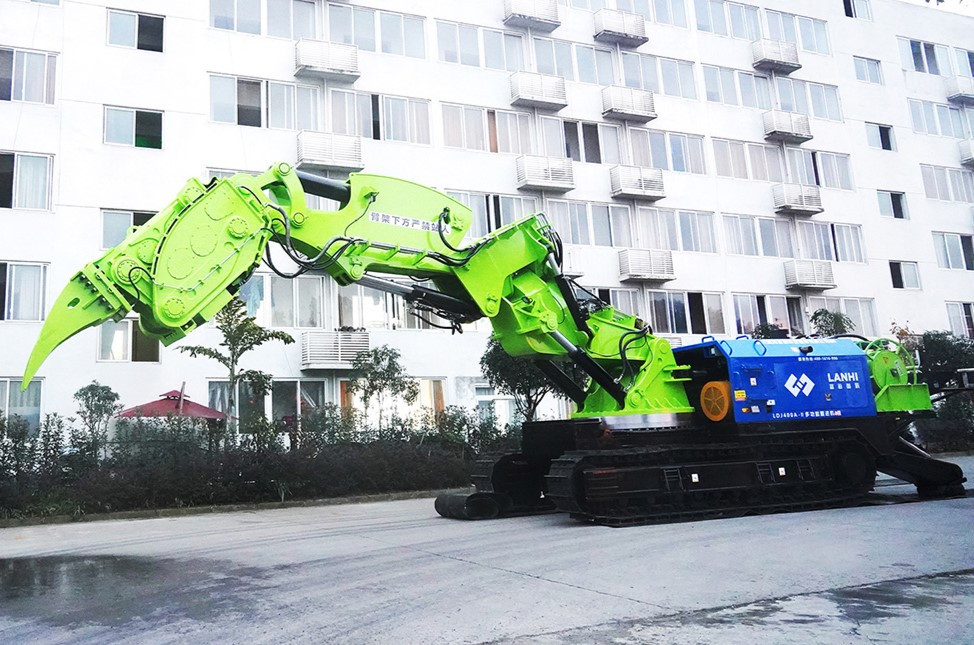
TBM tunnel boring machine has many advantages, which can efficiently and safely excavate various types of strata
TBM tunnel boring machine is an advanced underground tunnel construction equipment that can efficiently and safely excavate various types of strata, and is widely used in tunnel construction projects such as urban subways, railways, and highways.
The working principle of TBM tunnel boring machine is based on mechanical excavation and rock fragmentation technology. It mainly consists of a cutterhead, a propulsion system, a support system, and a control system. The cutterhead is the core component of TBM, equipped with multiple cutting tools for cutting and crushing rocks. After the TBM is started, the cutterhead will rotate at a certain speed, cutting the rock and transporting it outside the tunnel through a conveyor belt. At the same time, the propulsion system generates thrust through hydraulic cylinders to push the TBM forward. The support system reinforces and supports the tunnel wall in real-time during the TBM advance process to ensure construction safety. The control system is responsible for monitoring and controlling various parameters of the TBM to ensure its normal operation.
TBM tunnel boring machine has many advantages, such as fast construction speed, high quality, safety and reliability. Compared with traditional blasting methods, TBM can reduce the damage to the surrounding environment, and lower the impact of noise and vibration. In addition, TBM can also achieve automated control, improve construction efficiency and management level.
TBM tunnel boring machine has many advantages, which can efficiently and safely excavate various types of strata
The Blue Ocean Intelligent Installation LDJ400 series multifunctional tunneling machine is a specialized equipment used for non explosive excavation of tunnels. It mainly utilizes the high-frequency hammer or breaking hammer of the working department to impact and break rocks, the wedge or drill rod to pry and break rocks in the surrounding rock, and the heavy force of the free face under the surrounding rock. The high-frequency hammer is mainly used for rocks below 40MPa; the breaking hammer is used for mining rocks with higher hardness and poor development. (). The local control of mining+remote control of mining line can adapt to the excavation of 6-9.5 ? tunnels, and integrate the functions of frequent rock breaking, soft ? fast excavation, contour trimming, spray dust removal, etc. into the ? body. It is suitable for the construction of restricted blasting sections (such as airports, residential areas and wild ? animal protection areas), with strong adaptability. It can be applied to various types of surrounding rocks, and reduce over excavation and collapse. and so on.
TBM tunnel boring machine is an advanced tunnel construction equipment with broad application prospects. In future tunnel construction projects, with the continuous advancement and innovation of technology, TBM will play a greater role in promoting the development of the tunnel construction industry.
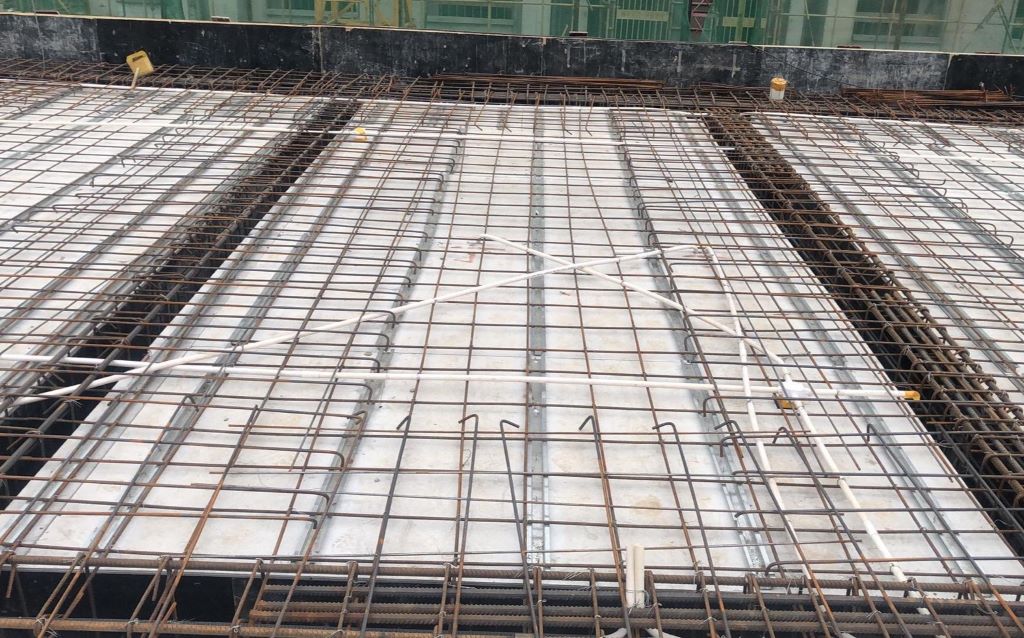
Guidelines for optimizing concrete construction under low temperature conditions in winter
In the cold winter, concrete construction faces many challenges, such as material freezing and increased construction difficulty. To ensure construction quality and efficiency, the following are some key optimization measures.
1、 Concrete raw materials and temperature control measures for mixing
1. Raw material selection and processing
Use conventional Portland cement and add admixtures to enhance frost resistance, with specific proportions determined based on the concrete mix ratio. All raw materials must be cleaned to avoid mixing with ice, snow, and minerals that are easily affected by temperature. Additives should use chlorine free antifreeze to prevent corrosion of steel bars. Construction water needs to be stored in an insulated tank to maintain an appropriate temperature and minimize water usage. Water reducing agents can be added to reduce freezing damage.
2. Concrete mixing technology
Add appropriate additives to improve the workability and strength of concrete, accelerate the hydration process of cement at low temperatures, reduce drying shrinkage performance, and enhance freeze-thaw resistance. Ensure that antifreeze does not affect the subsequent strength of concrete, and prohibit the mixing of water reducing agents and antifreeze on site.
2、 Temperature control measures for concrete transportation and pouring
1. Transportation insulation measures
The dump truck compartment needs to be sealed with insulation rolls, and the top should be covered with canvas or thin iron sheet. The tank truck compartment also needs insulation treatment. The time for concrete to be unloaded from the mixer to the construction site should not exceed 90 minutes, and the pumping pipeline should be insulated to prevent concrete segregation, surface freezing, or collapse. During transportation, the temperature drop rate of concrete should be controlled at no more than 5 ℃ per hour, and the molding temperature should not be lower than 10 ℃.
2. Pouring insulation measures
Key areas such as template joints and reinforcement joints require special insulation. Clean the formwork before formal pouring to prevent debris and snow from affecting it. Measures such as setting up scaffolding to prevent the influence of wind and snow, mechanical vibration to ensure the compactness of concrete, layered pouring to ensure the accuracy of the position of steel bars and embedded parts, and a smooth and even concrete surface after demoulding.
3、 Concrete curing and insulation measures inside the tunnel
1. Insulation inside the tunnel
Storage warehouses and mixing stations should use solar heating systems for heating to ensure that the temperature of concrete entering the mold is greater than 5 ℃. Cover the opening with insulation curtains to prevent cold air from entering, and assign a dedicated person to open and close the insulation curtains when transport vehicles enter and exit. The external water supply pipeline and high-pressure water tank need to be insulated, and a furnace should be installed every 50 meters inside the tunnel for heating, and a smoke exhaust pipe should be installed.
2. Concrete curing
After the template is removed, the temperature difference between the outside and the concrete should be controlled at 10-15 ℃, and the concrete surface should be insulated. The formwork can only be removed after the concrete has cooled to below 5 ℃ and the temperature difference with the environment is not greater than 15 ℃.
These measures can effectively improve the quality of winter concrete construction and ensure the smooth progress of the project.

How to use hydraulic concrete wet spraying machine? Construction process of hydraulic concrete wet spraying machine
Hydraulic concrete wet shotcrete machines are widely used in modern construction engineering for shotcrete operations, and are highly favored for their high efficiency and precision. Proper operating procedures and maintenance measures are crucial to ensure the normal operation and prolong the service life of the equipment. This article will provide a detailed introduction to the usage method and precautions of hydraulic concrete wet spraying machine.
1、 Preparation work
1. Hydraulic oil filling: Before using the hydraulic concrete wet spraying machine, it is necessary to first check the oil tank and fill it with sufficient hydraulic oil to ensure the normal operation of the hydraulic system.
2. Add water: Add water to the sink for use during machine testing and cleaning.
3. Check the motor: Turn on the machine and check whether the forward and reverse rotation of the motor is normal, ensuring that the motor can operate normally.
4. Equipment installation: Install sandblasting pipes, nozzles, rapid setting agent pipes, and air ducts to ensure that all components are securely connected.
5. Start the air compressor: Start the air compressor and check if it is running properly to ensure that it can provide sufficient air pressure support.
6. Debugging of accelerator pump: Start the accelerator pump, adjust the variable frequency rotation button to around 30 Hz, and check if the accelerator pump is working properly.
2、 Test process
1. Water lubrication: Before testing the machine, fill the hopper with water, start the main motor and ensure its normal operation.
2. Check the nozzle: Open the air duct and check the working condition of the nozzle to ensure that it can spray normally.
3. Lubrication pipeline: Turn on the positive pump for transportation to lubricate the pipeline. After lubrication is completed, stop the machine and drain the excess water from the hopper.
3、 Concrete spraying operation
1. Feeding: Add commercial concrete into the hopper to ensure that the quality of the concrete meets the requirements.
2. Turn on the accelerator: Turn on the accelerator air, keep the accelerator air on, start the accelerator pump, and wait for the nozzle to release the accelerator.
3. Spray operation: After the rapid setting agent is released from the nozzle, open the air duct first and then start pumping concrete. During the pumping process, the concrete in the hopper should not be lower than the mouth of the material cylinder to avoid affecting the spraying effect.
4、 Cleaning after homework completion
1. Cleaning of accelerator pump: After the spraying operation is completed, clean the accelerator pump pipeline with clean water to ensure that there is no residue in the pipeline.
2. Equipment cleaning: Start the wet spray machine and use a positive pump to repeatedly clean the hopper, S pipe, and sandblasting pipe. They must be thoroughly cleaned to prevent residue from solidifying.
3. Special attention in winter: After cleaning, the reverse pump must be turned on to drain the clean water from the hopper, S pipe, and water tank. At the same time, the water in the accelerator pump must be cleaned to prevent equipment damage caused by freezing.
5、 Precautions
-Operation safety: When operating the hydraulic concrete wet spraying machine, the operator must wear personal protective equipment such as safety helmets, protective goggles, and gloves.
-Regular maintenance: Regularly inspect and maintain key components such as hydraulic systems, air compressors, and accelerator pumps to ensure long-term efficient operation of the equipment.
-Environmental protection: When cleaning equipment, attention should be paid to environmental protection to prevent pollutant emissions.
Through the above steps, the efficient and safe operation of the hydraulic concrete wet spraying machine can be ensured, and the construction quality and efficiency can be improved. I hope this guide will be helpful for operators in practical applications.

How to choose a wet spraying robot manufacturer? You can start from these 3 aspects
Wet spraying robots play an important role in tunnel construction, and their quality and performance directly affect the progress and safety of the project. Therefore, choosing a reliable manufacturer of wet spray robotic arms is crucial. The following suggestions can help you make wise choices.
1. Check the manufacturer's reputation
The reputation of a manufacturer is an important indicator for evaluating its product quality and service level. If a manufacturer produces wet spray robotic arms with excellent quality and a good user experience, then the manufacturer's reputation will naturally be very good. There are several ways to choose a reputable manufacturer:
-Check the official website for construction cases: The official website usually displays successful construction cases, from which you can learn about the performance of the manufacturer's equipment in practical applications.
-Consultation on Used Projects: You can inquire with nearby projects that have used the manufacturer's equipment to understand their user experience and evaluation.
Word of mouth is formed through long-term accumulation and is not easily falsified, so it can be an important reference for choosing manufacturers.
2. Check the manufacturer's after-sales service
The quality and performance of the machine are certainly important, but after-sales service cannot be ignored either. Good after-sales service can provide timely solutions when equipment malfunctions, ensuring the smooth progress of the project. When choosing a manufacturer, the after-sales service can be evaluated from the following aspects:
-After sales response speed: Understand the manufacturer's response speed when equipment problems occur, and whether they can quickly solve the problem.
-Accessory supply: Ensure that manufacturers can provide sufficient spare parts supply to avoid project delays caused by accessory issues.
-Service reputation: You can inquire with other users to understand the quality of the manufacturer's after-sales service.
The after-sales service of small manufacturers is often not comprehensive enough, which may affect the progress and quality of the project. Therefore, choosing a manufacturer with good after-sales service is particularly important.
3. Look at the scale and strength of the manufacturer
The size and strength of the manufacturer are also important factors in the selection. In general, manufacturers with larger scale and stronger capabilities have more assurance in terms of equipment quality and performance. They usually have complete production facilities and strict quality control systems to ensure the stability and reliability of their products. In addition, large manufacturers have strong financial strength and are not easily affected in production and delivery due to financial issues.
-Production capacity: Assess the manufacturer's production capacity to ensure timely delivery and that production issues do not affect the project schedule.
-Quality assurance: Understand the manufacturer's quality control process and certification status to ensure that the equipment produced meets relevant standards and requirements.
Choosing manufacturers with large scale and strong capabilities can reduce procurement risks and ensure the quality and performance of equipment.
When choosing a manufacturer of wet spray robotic arms, it is necessary to comprehensively consider the manufacturer's reputation, after-sales service, scale, and strength. Manufacturers with good reputation usually have higher product quality and service level. Manufacturers with good after-sales service can provide timely solutions when equipment problems occur. Manufacturers with strong scale and strength have more guarantee in equipment quality and production capacity. Based on the comprehensive investigation of the above points, you can choose a reliable manufacturer of wet spray robotic arms to provide strong support for your project.

What are the types of mining machinery and equipment? Introduction to various types of mining machinery and equipment
Mining machinery equipment refers to various mechanical devices and tools used in the process of mineral resource extraction. These devices play important roles in different stages of mining, including drilling, loading, transportation, lifting, and crushing operations. The following are some common classifications of mining machinery and representative equipment:
What are the types of mining machinery and equipment? Introduction to various types of mining machinery and equipment
1. Drilling equipment:
Drilling rig: used for drilling geological rock layers, obtaining geological data, or drilling mine ventilation holes, drainage holes, etc.
Drill rod: connects the drilling rig and drill bit, transmitting rotation and drilling force.
Drill bit: directly acts on rocks to perform drilling operations.
2. Loading equipment:
Excavator: Used for excavating materials such as ore, soil and rock, it can be divided into track type and tire type.
Loader: Used for loading loose materials such as ore, coal, etc., it can be divided into front loading and rear loading types.
Bucket: Installed on loading machinery, used for grabbing and transporting materials.
3. Transportation equipment:
Mine car: used for transporting ore, waste rock, etc. inside mines, usually driven by motors or diesel engines.
Mining dump truck: with a large load capacity, used for transporting large amounts of materials.
Conveyor belt: used for continuous conveying of materials, divided into ground conveyor belt and underground conveyor belt.
4. Upgrade equipment:
Winch: It uses steel wire ropes to pull objects and achieve vertical or horizontal transportation.
Elevator: used for vertical lifting of underground materials, such as lifting mining trucks, personnel, etc.
Elevator: installed inside the shaft for personnel to enter and exit the shaft.
5. Crushing equipment:
Jaw crusher: uses the squeezing effect between two metal plates to crush materials.
Hammer crusher: uses a high-speed rotating hammer head to strike and crush materials.
Cone crusher: uses a cone crushing chamber to squeeze and crush materials.
6. Screening equipment:
Vibration screen: Using the principle of vibration to screen materials, it is divided into linear vibration screen and circular vibration screen.
Rolling screen: Screening materials by rotating a drum.
7. Washing equipment:
Jig machine: uses the buoyancy difference between water and materials for separation and washing.
Spiral classifier: uses spiral motion to classify materials.
8. Auxiliary equipment:
Pump station: provides necessary liquid pressure and flow for the mine.
Compressor: Provides compressed air for use with pneumatic tools and equipment.
Ventilation equipment: Ensure the air quality underground and eliminate harmful gases.
9. Safety equipment:
Self rescue device: provides respiratory protection in case of fire or toxic gas leakage underground.
Rescue equipment: used for underground rescue operations, including rescue cabins, rescue robots, etc.
These devices may vary depending on the specific needs and operating environment of the mine, and may also be equipped with other special functions such as automation control systems, monitoring equipment, etc., to improve production efficiency and safety.

Multi dimensional control strategies for the quality of tunnel shotcrete construction
In tunnel engineering, shotcrete is an important process for initial support and secondary lining, and its quality has a significant impact on the durability of the tunnel. This article will provide a detailed introduction to the key technical measures that cannot be ignored in shotcrete construction, helping construction personnel ensure the quality of tunnel concrete and guarantee the safety and durability of the project.
1、 Mix proportion design
1. Cement to bone ratio control: Control the cement to bone ratio of sprayed concrete between 1:4 and 1:4.5. Reasonably control the amount of cement used to avoid affecting the initial strength growth rate and shrinkage.
2. Sand ratio adjustment: The sand ratio should be maintained between 45% and 55% to prevent aggregate blockage.
3. Water cement ratio adjustment: The water cement ratio should be between 0.4 and 0.5. Ensure that cement and water are fully hydrated to form a dense cementitious structure, ensuring the strength of sprayed concrete and reducing rebound losses.
4. Addition of accelerators: Reasonably add accelerators, and be careful not to cause a decrease in later strength in order to pursue early strength.
2、 Precautions for construction preparation
1. Equipment inspection: Check the pipelines and joints to ensure that there is no air leakage in the air ducts and no water leakage in the water pipes. Install a valve joint every 40 to 50 meters.
2. Thickness marker embedding: Install shotcrete thickness inspection markers and record their exposed length. Pull the line, level with wooden bars while spraying, control the flatness of the spraying surface, and compact the concrete.
3. Excavation section inspection: Check the excavation section and make up for any under excavation. Reinforce unfavorable geological areas and provide sufficient lighting on the spraying operation surface.
3、 Maintenance measures
1. Initial setting leveling: After the initial setting of concrete, leveling should be carried out to avoid damaging the bonding between the internal structure of fresh concrete and the base layer.
2. Watering and curing after final setting: The last layer of concrete should be watered and cured for no less than 14 days after the final setting of 2 hours.
3. Low temperature maintenance: Water retention maintenance must be carried out when the temperature is below 5 ℃.
4、 Concrete thickness detection
1. Spray thickness inspection: Within 8 hours after the spraying is completed, drill holes to check the thickness of the reinforcement layer. If it is insufficient, it must be sprayed in a timely manner.
2. Thickness error control: The thickness error of the reinforcement layer should be controlled between -5 and+8 millimeters.
5、 Concrete strength testing
1. Sampling of test specimens: Cut or drill concrete specimens without cracks from the site, meeting the requirements of flatness and verticality.
2. Compressive strength test: Control the dispersion of the compressive strength test value of the specimen to ensure the rationality of the data.
3. Appearance inspection: Conduct appearance inspection to eliminate hollowing and cracking areas.
6、 Dust control measures
1. Selection of jet air pressure: Select the jet air pressure through experiments and control the jet force.
2. Spray material mixing * *:
-Uniformly mix the sprayed material to reduce rebound and dust volume.
3. Wet spray secondary mixing: Wet spray secondary mixing is adopted to reduce rebound.
4. Control the dosage of accelerators: Strictly control the dosage of accelerators.
Through reasonable mix design, meticulous construction preparation, effective maintenance measures, rigorous thickness and strength testing, and scientific dust control, the quality of tunnel shotcrete can be significantly improved, ensuring the safety and durability of the project. These technical measures not only provide practical guidance for construction personnel, but also lay a solid foundation for the smooth progress of tunnel engineering.

How to prevent tunnel collapse? Measures to prevent tunnel collapse
How to prevent tunnel collapse? Preventing tunnel collapse is an important task in tunnel engineering. It is necessary to start from multiple aspects such as design, construction, material selection, and site management, and implement strict preventive measures to ensure the safety of tunnel construction and operation. The following are some effective measures to prevent tunnel collapse:
1. Detailed investigation of geological conditions: Before tunnel construction, conduct a comprehensive geological survey to understand the geological structure, stratum distribution, groundwater conditions, etc., to provide accurate data support for tunnel design and construction.
2. Scientific and reasonable design: According to geological conditions and engineering requirements, adopt advanced design concepts and calculation methods to ensure that the tunnel structure has sufficient safety reserves and resistance.
3. Choose a suitable construction method: Choose a suitable construction method according to geological conditions, such as shield method, TBM (tunnel boring machine) method, traditional excavation method, etc., and take corresponding support measures.
4. Strengthen the design of support structure: According to the geological conditions, design a reasonable support structure, such as steel support, arch frame, shotcrete, etc., to ensure the stability of the tunnel during construction and operation.
5. Strictly control the construction quality: Establish a complete quality management system, strictly control every link in the construction process, and ensure that the materials, equipment and processes used meet the requirements of the specifications.
6. Strengthen on-site management: Establish an effective on-site management system, strengthen the training and management of construction personnel, ensure the safety and order of the construction site, and prevent man-made accidents.
7. Implement real-time monitoring: Install advanced monitoring equipment to monitor the displacement, stress, seepage and other key parameters of the tunnel in real time, timely discover potential dangerous factors, and take corresponding treatment measures.
8. Timely deal with hidden dangers: Take timely measures to deal with cracks, seepage, deformation of support structures and other problems that occur during the construction process to prevent the expansion of problems and collapse.
9. Regular maintenance and inspection: Carry out regular maintenance and inspection of the built tunnels, timely discover and repair problems that may affect the safety of the tunnels, and extend the service life of the tunnels.
Through the comprehensive use of the above measures, the risk of tunnel collapse can be greatly reduced, and the safe construction and smooth operation of tunnel projects can be guaranteed.

Concrete wet spraying manipulator: mainstream and efficient equipment for support operations
Concrete wet spraying robotic arm has become the mainstream equipment for support operations in modern tunnel and mining engineering. Its efficient spraying performance and excellent engineering quality have made it occupy an important position in the fields of civil engineering and construction. This article will introduce the characteristics, application fields, and advantages of concrete wet spraying robotic arms in support operations.
1、 Characteristics of concrete wet spraying manipulator
1. Efficient spraying: The concrete wet spraying robotic arm can achieve continuous and stable spraying operations, improving construction efficiency.
2. Excellent spraying quality: The wet spraying process makes the mixing of concrete and cement slurry more uniform, resulting in high density and strong adhesion of the sprayed concrete.
3. High degree of automation: Equipped with advanced automatic control systems, it can achieve precise control and remote operation, reduce manual intervention, and improve construction safety.
4. Strong adaptability: It can operate stably under various complex geological conditions and is widely used in underground engineering such as tunnels and mines.
2、 Application Fields
1. Tunnel engineering: During tunnel excavation, concrete wet spraying robots are used for initial support and secondary lining, providing a stable support structure.
2. Mining engineering: In mining operations, wet spraying robotic arms are used for roadway support and protection engineering to ensure mining safety.
3. Foundation pit support: In deep foundation pit construction, wet spraying robotic arms are used for slope support to prevent collapse and landslides.
4. Subway construction: In subway construction, wet spraying robotic arms are used to support shield tunnels and underground stations, ensuring construction safety and structural stability.
3、 Advantages in Support Operations
1. Improve construction efficiency: Automated operation and continuous spraying significantly shorten the construction period and improve the overall project progress.
2. Improve support quality: Wet sprayed concrete has high compactness, strong bonding force, significant support effect, and reduces maintenance costs in the later stage.
3. Enhance construction safety: Remote operation reduces the number of times construction personnel enter hazardous areas and lowers safety risks.
4. Adapt to complex environments: Wet spraying robotic arms can operate stably in harsh environments such as high temperature, high humidity, and high dust, ensuring the smooth progress of projects.
The concrete wet spraying manipulator, as the mainstream equipment for support operations, plays an irreplaceable and important role in modern engineering construction with its efficient, high-quality, and safe construction performance. With the continuous advancement of technology, wet spraying robots will demonstrate their advantages in more fields, providing strong guarantees for engineering quality and construction efficiency.