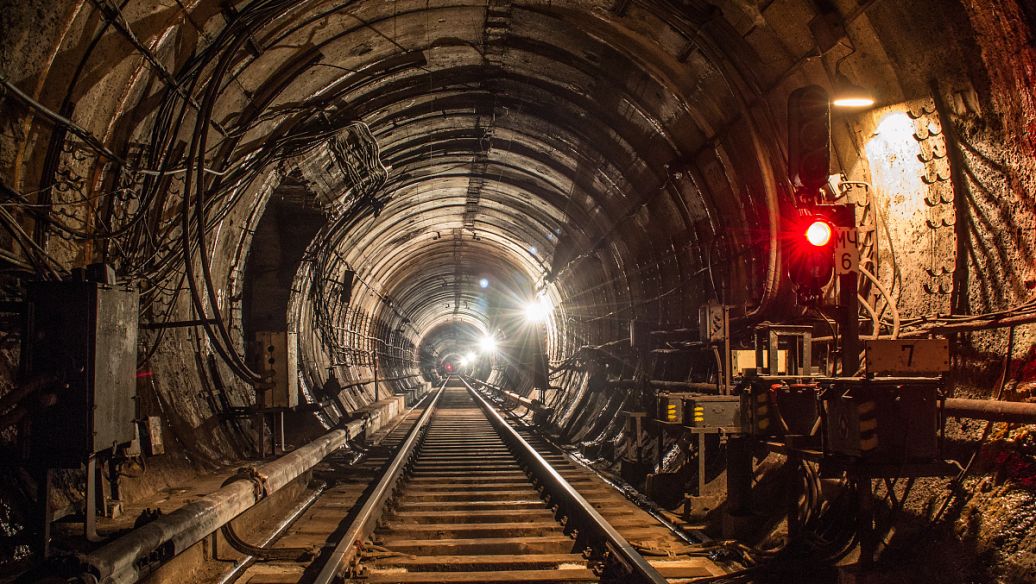
The Development History of Modern Tunnel Construction in China: From Drill-and-Blast Method to Modern Tunnel Boring Machines
Tunnels are not merely transportation facilities; they are the crystallization of human wisdom, a perfect fusion of technology and natural forces. The history of tunnels can be traced back to ancient times, but real breakthroughs occurred in modern times. At the end of the 19th century, with the advancement of the Industrial Revolution, tunnel engineering began to be widely applied. The history of tunnel construction in China also unfolds as a story of continuous innovation and progress.
The 1950s and 1960s: Difficult Exploration with the Drill-and-Blast Method
In the 1950s and 1960s, China mainly used the drill-and-blast method, relying on manual labor and small machinery for rock drilling and loading in tunnel construction. This period was marked by extremely arduous conditions and low construction efficiency. A typical example is the Liangfengya Tunnel on the Chuanqian Railway, which is 4270 meters long. The construction of this project required immense manual labor and effort.
The 1970s: Formation of Independent Construction Techniques
Building on the experiences of the 1950s and 1960s, the 1970s saw the development of a complete set of independent tunnel construction techniques in China, ushering in an era of proactive tunnel construction. The Yimaling Tunnel on the Jingyuan Railway, spanning 7032 meters, is a representative work of this period. This era marked the maturity of China's tunnel construction technology and an enhancement in its ability for independent innovation.
The 1980s: Introduction of Hydraulic Drilling Technology
In the early 1980s, China imported a series of advanced equipment such as hydraulic drilling jumbos from Nordic countries, significantly improving the level of mechanized tunnel construction. The Dayao Mountain Double-track Tunnel on the Hengguang Railway, with a length of 14295 meters, exemplifies the improved mechanization of this period.
The 1990s: Achieving International Standards
In the 1990s, China made remarkable progress in tunnel construction technology, covering in 20 years what took developed countries 50 to 100 years, reaching international standards. The Qinling Tunnel on the Xikang Railway, stretching 18460 meters, is an important representative work of this stage, signifying China's integration with global tunnel construction technologies.
2008: First Crossing of the Yangtze River
In 2008, the Wuhan Yangtze River Highway Tunnel was officially opened, marking the construction of China's first tunnel crossing the Yangtze River and opening a new chapter in China's tunnel construction.
2017: Crossing the Sea
In 2017, the world's longest underwater immersed tube tunnel, the Hong Kong-Zhuhai-Macao Bridge immersed tube tunnel, was successfully completed, symbolizing China's world-leading capability in underwater tunnel construction. This project demonstrated China's outstanding technology in underwater tunnel construction.
2018: Conquering the Tianshan Mountains
In 2018, the world's longest highway tunnel, the Tianshan Shengli Tunnel from Urumqi to Yining, began construction, extending 22 kilometers. This milestone marked China's ability to overcome challenges in high-altitude and cold environments, showcasing determination and capability in constructing tunnels under complex geological conditions.
2020: Commencement of the Pearl River Estuary Tunnel on the Shenjiang Railway
In 2020, construction began on the Pearl River Estuary Tunnel on the Shenjiang Railway, which features the greatest depth and highest water pressure among China's underwater tunnels. This project represents a new level of China's "underground" technology, highlighting further breakthroughs in underwater tunnel construction.
From the initial drill-and-blast method to advanced modern excavation techniques, China's tunnel construction has undergone multiple stages of technical accumulation, independent innovation, and international integration. Each milestone project not only represents advancements in China's tunnel construction technology but also attests to the wisdom and effort of Chinese engineers. Through the continuous introduction and development of new technologies, China's tunnel construction has now reached the forefront of the world, demonstrating strong engineering prowess and technical expertise.
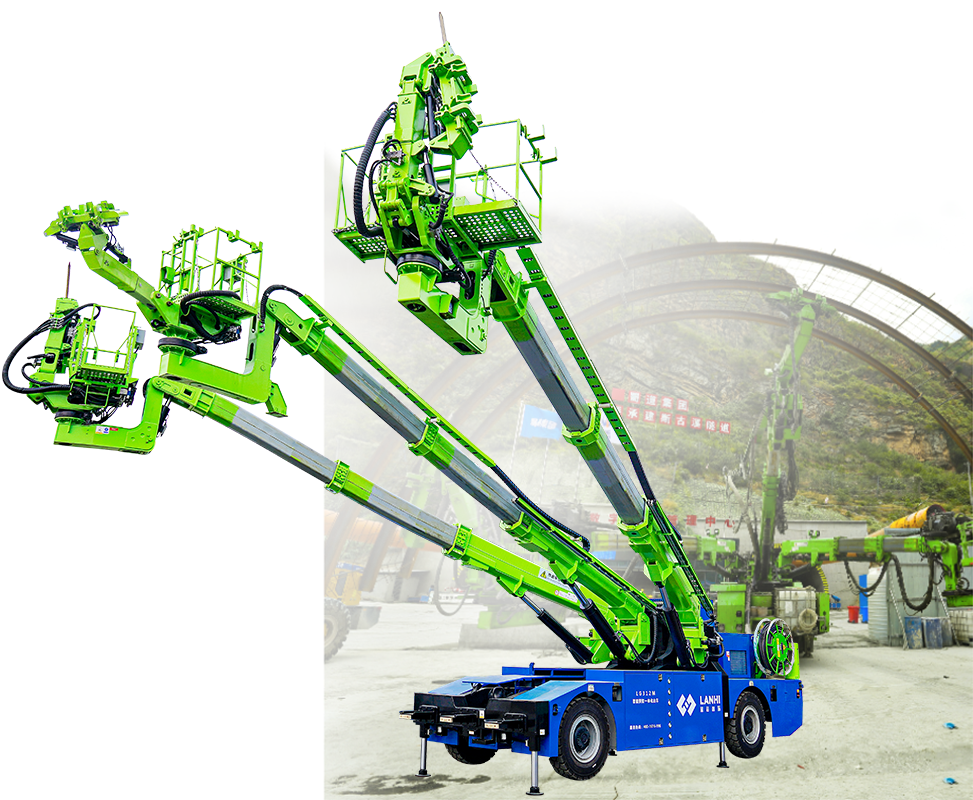
Multifunctional Applications of Arch Installation Trolleys in Tunnel Construction
The arch installation trolley is a multifunctional piece of construction equipment that plays a crucial role in tunnel construction. This equipment not only improves construction efficiency but also enhances safety. Here are the main functions of the arch installation trolley in tunnel construction.
1. Steel Frame Installation
One of the primary functions of the arch installation trolley is to install steel frames inside tunnels. The steel frame acts as the skeleton of the tunnel structure, supporting its stability and safety. By using the installation trolley, the steel frames can be accurately positioned and quickly installed, increasing work efficiency and installation precision.
2. Mesh Installation
In addition to steel frames, the arch installation trolley is also used for installing mesh. The mesh is part of the tunnel lining, used to distribute and absorb ground stress, preventing rock loosening and collapse. The installation trolley can carry and secure the mesh, allowing it to be installed quickly and accurately.
3. Connecting Bar Installation
Connecting bars are crucial components between steel frames and mesh, ensuring the integrity and stability of the entire support structure. The arch installation trolley assists in the installation of connecting bars, ensuring each connection point is firm and reliable.
4. Assisting in Inspection and Hazard Mitigation
Safety inspections and hazard mitigation are vital during tunnel construction. The arch installation trolley is equipped with relevant devices and tools, assisting construction personnel in conducting safety inspections and hazard mitigation work, promptly identifying and addressing potential dangers to ensure construction safety.
5. Under-excavation Handling
During tunnel excavation, under-excavation may occur, where the actual excavation size is smaller than the design size. The arch installation trolley can assist construction personnel in handling under-excavation, ensuring the tunnel cross-section meets design requirements.
6. Explosive Installation
In tunnel construction requiring blasting operations, the installation of explosives is a critical step. The arch installation trolley is equipped with safety protection devices and operation platforms, aiding construction personnel in safely and accurately installing explosives, ensuring the safety and effectiveness of blasting operations.
7. Rock Bolt Installation
Rock bolts are a crucial part of tunnel support, used to stabilize the surrounding rock and prevent collapses. The arch installation trolley can carry rock bolts and installation equipment, assisting construction personnel in installing rock bolts, thereby improving construction efficiency and safety.
The arch installation trolley integrates several key processes in tunnel construction. Its multifunctional applications significantly enhance construction efficiency, quality, and safety. The widespread use of this equipment provides solid support for tunnel construction.
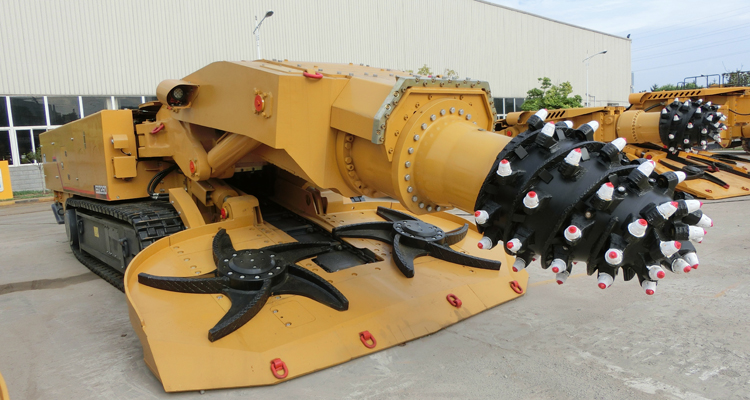
What is the Maintenance Schedule for a Cantilever Roadheader? Daily, Weekly, Monthly, and Annual Maintenance Tasks
The maintenance schedule for a cantilever roadheader varies depending on the specific model and usage frequency. Generally, the following are common maintenance tasks and their suggested intervals:
Daily Maintenance:
Check all fasteners for looseness and tighten if necessary.
Clean the machine's surface and interior to remove dust and dirt.
Inspect the lubrication system to ensure all lubrication points have sufficient oil.
Check the electrical system, including cables and connectors, for wear or damage.
Record daily operating data and note any abnormalities.
Weekly Maintenance:
Lubricate all movable parts.
Inspect the wear of the cutting head and tools, and replace them if necessary.
Check the functionality of the support and propulsion systems.
Inspect the hydraulic system, including oil levels, leaks, and pressure gauge readings.
Check the cooling system to ensure proper coolant flow and temperature.
Monthly Maintenance:
Conduct a more thorough inspection, including the motor and gearbox.
Inspect the electrical control cabinet to ensure all components are functioning properly.
Check the hydraulic pumps and valves for leaks or performance degradation.
Perform preventive testing on electrical circuits, including insulation testing.
Inspect spare parts to ensure they are in good condition.
Quarterly Maintenance:
Perform a comprehensive inspection of the entire machine, including structural and key components.
Lubricate and inspect all bearings.
Conduct a detailed inspection of the electrical system, including cable integrity and connector contacts.
Thoroughly inspect the hydraulic system, including oil quality and filters.
Perform a thorough inspection of the cooling system, including pumps and radiators.
Annual Maintenance:
Conduct an extensive maintenance procedure, including in-depth inspection and necessary replacement of all components.
Perform a complete cleaning and sanitization of the machine.
Calibrate and test all electrical equipment.
Perform performance tests on all hydraulic equipment.
Inspect and replace all spare parts as needed.
Please note that the above intervals are for reference only. The actual maintenance schedule should be adjusted based on the manufacturer's recommendations and actual usage conditions. Regular maintenance not only extends the equipment's lifespan but also improves work efficiency and safety. Before performing any maintenance work, ensure compliance with relevant safety regulations and operating guidelines.
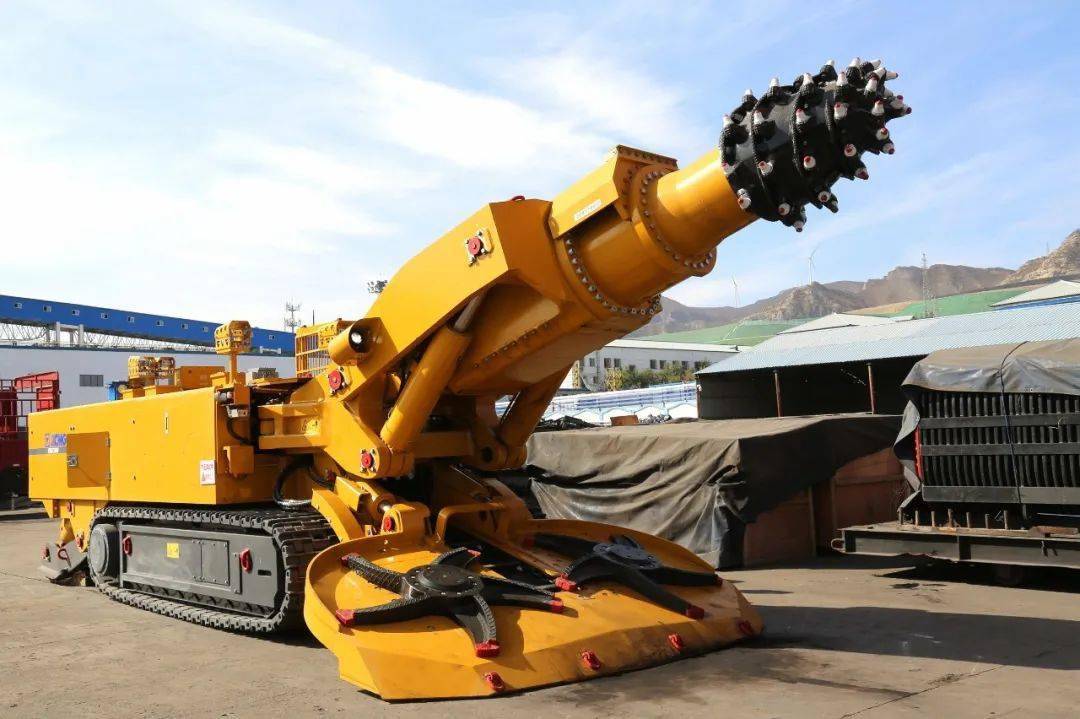
The Cantilever Roadheader: A High-Efficiency Tool in Tunnel Construction
In the field of tunnel engineering, the cantilever roadheader (Tunnel Boring Machine, TBM) is an indispensable piece of machinery due to its efficiency, safety, and precision. This article will detail the working principles, advantages, and application cases of cantilever roadheaders, highlighting their crucial role in modern tunnel construction.
I. Working Principle of the Cantilever Roadheader
The cantilever roadheader primarily consists of a cutting head, support system, propulsion system, and control system. Its working principles are as follows:
Cutting Head: The cutting head of the cantilever roadheader is equipped with multiple rotating tools, which can be selected and replaced according to the hardness and type of rock. When the machine is activated, the cutting head rotates at high speed to cut the rock, breaking and removing it.
Support System: To ensure the stability of the cutting process, the cantilever roadheader is equipped with an advanced support system. This system can adjust the support force according to the hardness and shape of the rock, ensuring stable operation even under complex geological conditions.
Propulsion System: The propulsion system drives the machine forward. It generates thrust through hydraulic cylinders or electric motors, allowing the machine to advance into the tunnel while cutting the rock.
Control System: The control system of the cantilever roadheader integrates advanced sensors and computer technology to monitor the machine's operating status and environmental changes in real-time. Through precise data analysis and processing, the control system can automatically adjust various parameters of the machine to ensure operational efficiency and safety.
II. Advantages of the Cantilever Roadheader
Compared to traditional tunnel excavation methods, the cantilever roadheader has the following significant advantages:
Efficiency: The cantilever roadheader uses mechanized operations, greatly increasing the speed of tunnel excavation. It can excavate longer tunnel sections within the same period.
Safety: The operation of the cantilever roadheader is controlled by an advanced control system, reducing the risks associated with manual operation. Additionally, its enclosed working environment effectively lowers the safety risks for construction personnel.
Precision: The cantilever roadheader can precisely excavate the tunnel cross-section according to design drawings and geological conditions, ensuring the quality and dimensional accuracy of the tunnel.
Adaptability: The cantilever roadheader can adapt to various geological conditions, whether hard rock or soft soil, efficiently completing excavation tasks.
Environmental Protection: The construction process of the cantilever roadheader produces less noise and dust, minimizing its impact on the surrounding environment and meeting the requirements for green construction.
III. Application Cases of the Cantilever Roadheader
The cantilever roadheader is widely used in tunnel construction projects around the world. Here are some typical application cases:
Europe: In many high-speed railway and urban rail transit projects in Europe, cantilever roadheaders are extensively used for tunnel excavation. For example, the high-speed railway TGV project from Paris to Lyon in France used cantilever roadheaders for tunnel construction.
Asia: In Asia, China’s high-speed rail construction is particularly notable. Projects such as the Beijing-Shanghai High-Speed Railway and the Beijing-Guangzhou High-Speed Railway employed cantilever roadheaders for tunnel excavation. Additionally, India’s Mumbai-Ahmedabad High-Speed Railway project also used cantilever roadheaders for tunnel construction.
North America: In North America, several tunnel projects in Canada and the United States have utilized cantilever roadheaders. For instance, the Montreal Metro construction in Canada and the New York Subway expansion project in the United States used cantilever roadheaders for tunnel excavation.
As a high-efficiency tool in modern tunnel construction, the cantilever roadheader has been widely applied globally. Its efficiency, safety, and precision have brought revolutionary changes to tunnel construction. With continuous technological advancements and growing application demands, the performance of cantilever roadheaders will continue to be optimized, and their application fields will further expand.
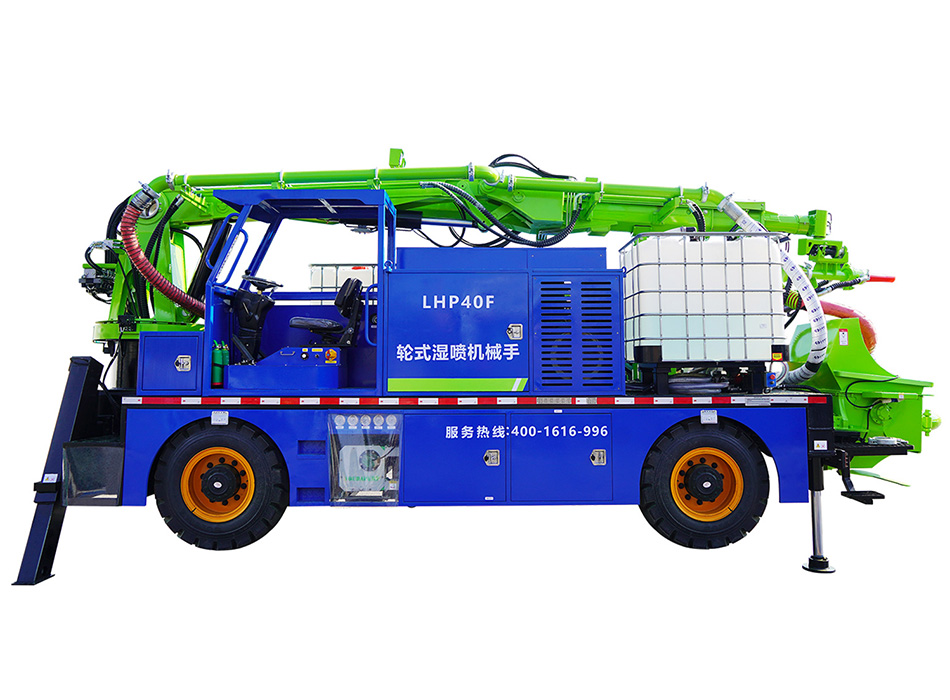
How to Choose the Right Robotic Shotcrete Machine? Key Factors to Consider
Selecting the appropriate robotic shotcrete machine involves considering several key factors:
1. Construction Requirements: Clearly define the specific requirements of the construction project, including the work environment, operational scope, spray thickness, and type of concrete. These factors will directly influence the selection of the machine.
2. Performance Parameters: Examine the main performance parameters of the machine, such as working radius, spray speed, spray distance, and arm length, to ensure it meets the operational needs of the construction site.
3. Operational Flexibility: Choose a machine that is easy to operate and highly flexible, allowing operators to quickly master the usage techniques and improve work efficiency.
4. Reliability: Consider the manufacturing quality, durability, and failure rate of the machine. Opt for well-known brands and products with a good reputation to ensure stability and reliability during the construction process.
5. After-Sales Service: Understand the after-sales service system provided by the supplier, including warranty period, repair services, and technical support. Good after-sales service can effectively ensure the long-term use of the machine.
6.Economic Efficiency: Conduct a cost-benefit analysis to choose a machine with a high cost-performance ratio while meeting construction needs.
7. Environmental Factors: Consider the environmental performance of the machine, such as noise control and dust emission, and choose products that comply with environmental standards.
By comprehensively evaluating these factors, you can select the most suitable robotic shotcrete machine for the specific construction project, ensuring construction quality and efficiency while reducing costs.
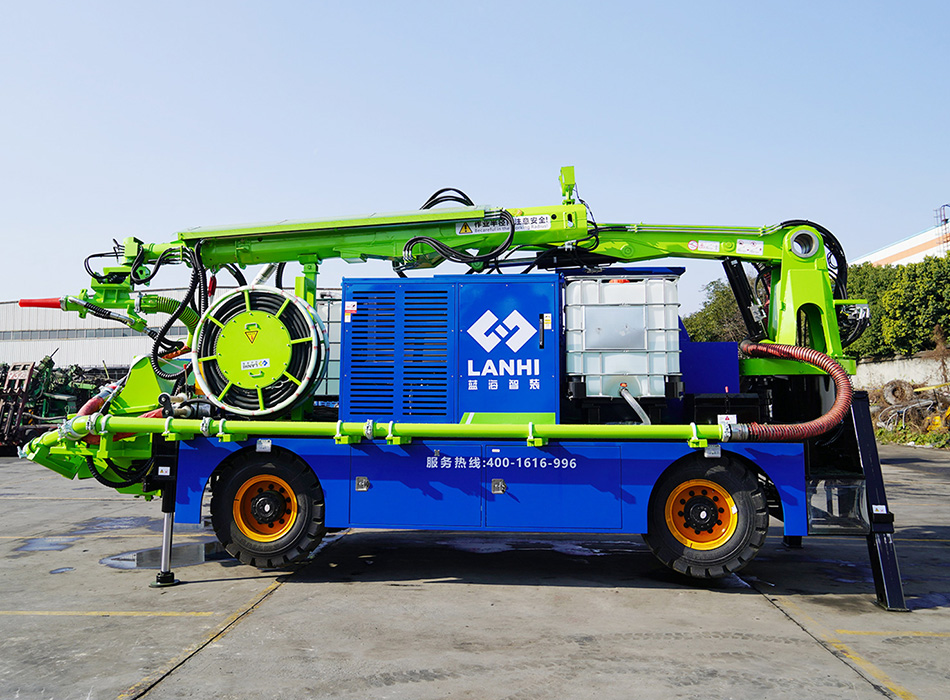
Applications and Advantages of Robotic Shotcrete Machines
With the continuous development of construction technology, shotcrete has become widely used as an efficient and environmentally friendly construction method. In this transformation, robotic shotcrete machines play a crucial role. This article will explore the advantages, application fields, and future development trends of robotic shotcrete machines.
Advantages of Robotic Shotcrete Machines
1. Improved Construction Efficiency: Traditional manual spraying methods are not only inefficient but also labor-intensive. Robotic shotcrete machines can work continuously, significantly reducing construction time.
2. Enhanced Construction Quality: Robots can precisely control the spraying pressure and speed, resulting in more uniform and dense shotcrete, thereby improving the quality of the construction.
3. Reduced Labor Costs: Using robotic machines reduces the number of workers needed, thus lowering labor costs. Additionally, due to their high efficiency, robotic machines can shorten project durations, further reducing costs.
4. Better Working Environment: The shotcreting process generates a lot of dust and waste, impacting the environment. Robotic machines can minimize the emission of these pollutants, improving the working environment.
Application Fields of Robotic Shotcrete Machines
1. Infrastructure Construction: In the construction of highways, railways, bridges, and other infrastructure projects, shotcrete is widely used for tunnel lining, bridge piers, and other parts.
2. Water Conservancy and Hydropower Projects: In large-scale water reservoirs, hydropower stations, and other water conservancy projects, shotcrete is used for dams, spillways, and other constructions.
3. Mine Support: During mining operations, shotcrete is used for tunnel support and slope stabilization, enhancing mine safety.
4. Building Decoration: In high-rise buildings, villas, and other architectural decoration projects, shotcrete can be used to create complex shapes, providing architects with more creative freedom.
Intelligent Development: With the continuous advancement of artificial intelligence technology, robotic shotcrete machines will achieve more advanced intelligent operations, such as automatic navigation and intelligent recognition, enhancing construction precision and efficiency.
Robotic shotcrete machines, as advanced construction equipment, have demonstrated their unique advantages in various fields. With ongoing technological innovation and the expansion of their application range, it is believed that robotic shotcrete machines will have a brighter future, injecting new momentum into the development of the construction industry.
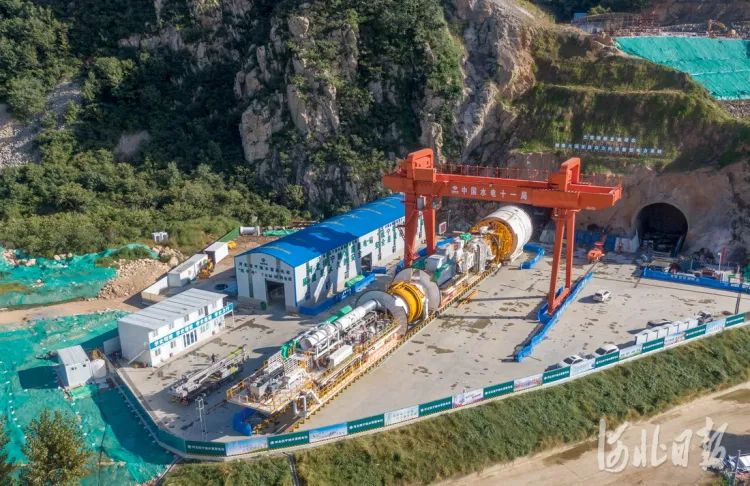
How to Handle Hard Rock and Soft Soil During Underground Construction with a Tunnel Boring Machine
The methods for handling hard rock and soft soil during underground construction with a tunnel boring machine (TBM) differ significantly due to the varying demands these geological conditions place on the TBM's operation and equipment performance.
Handling Hard Rock:
1. Adjust Cutterhead Configuration: Use cutting tools suitable for hard rock, such as carbide or diamond tools. Optimize the cutterhead configuration based on the hardness and distribution of the rock.
2. Enhance the Thrust System: Hard rock requires a robust thrust system, potentially necessitating increased thrust and torque to ensure the TBM can advance smoothly.
3. Control Earth Pressure Balance: In hard rock layers, it is crucial to manage the earth pressure balance carefully to avoid excessive slurry extraction and prevent ground subsidence.
4. Monitor Cutterhead Rotation Speed and Advance Rate: Adjust the cutterhead rotation speed and advance rate according to the cutting conditions in the hard rock to maintain optimal cutting efficiency and advance rate.
Handling Soft Soil:
1. Use Appropriate Cutterhead and Cutting Tools: In soft soil layers, use softer cutting tools, such as soil cutters or rotary brushes, to reduce wear on the cutterhead.
2. Strengthen Earth Pressure Balance Control: Strictly control the earth pressure balance to prevent ground subsidence and tunnel collapse, potentially using grouting techniques to enhance soil bearing capacity.
3. Control Advance Rate and Cutterhead Rotation Speed: A high advance rate may cause ground subsidence, while a slow rate may lead to cutterhead clogging. Adjust these parameters based on actual conditions.
4. Utilize Auxiliary Equipment: If necessary, use auxiliary equipment such as slurry pumps and mixers to improve the working environment and assist the TBM in advancing smoothly.
5. Enhance Cutterhead Maintenance: Although soft soil causes less wear on the cutterhead, it is essential to regularly clean the cutterhead and cutting tools to maintain good working condition.
The TBM operation team must possess extensive experience and professional knowledge to adjust construction parameters and take appropriate measures promptly, ensuring safety and efficiency. Additionally, it is necessary to develop detailed construction plans and emergency response plans based on specific geological conditions.
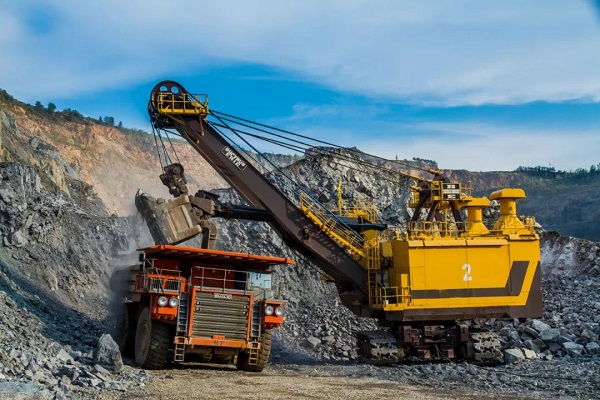
What Are the Latest Technologies in Intelligent Mine Construction?
With continuous advancements in technology, the latest technologies in intelligent mine construction are constantly emerging and evolving. Here are some of the cutting-edge technologies currently in use:
1. Autonomous Driving Technology: The application of autonomous driving technology in mining is gradually expanding. Autonomous vehicles and equipment enable automated transport and loading/unloading operations at mining sites, enhancing production efficiency, reducing labor intensity, and minimizing safety incidents.
2. Remote Control Technology: Remote control technology allows for the remote monitoring and management of underground equipment and personnel. Through remote control centers, real-time underground conditions can be monitored, work plans and parameters can be promptly adjusted, thereby improving production efficiency and management levels.
3. Internet of Things (IoT) Technology: IoT technology enables real-time positioning and tracking of mining equipment and personnel. By installing sensors and identification devices, the real-time monitoring of equipment operational status and fault warnings can be achieved, facilitating personnel scheduling and materials management for managers.
4. Artificial Intelligence (AI) Technology: AI technology is becoming increasingly widespread in the mining sector. Through machine learning and deep learning algorithms, intelligent predictions and evaluations of ore deposits can be made, optimizing extraction plans and enhancing resource utilization.
5. Virtual Reality (VR) Technology: VR technology can simulate mining production processes, aiding managers in decision-making and planning. It provides an intuitive understanding of production conditions at mining sites, helps identify potential problems and risks, and allows for preemptive measures.
6. Robotics Technology: The application of robotics technology in mining is gradually increasing. Robots can replace humans in performing dangerous and complex tasks such as drilling and sampling, improving efficiency and safety.
7. Digitalization Technology: Digitalization is the foundation of intelligent mine construction. It enables the collection, storage, processing, and analysis of mining data, supporting intelligent management and decision-making.
8. Cloud Computing Technology: Cloud computing offers robust computing power and data storage capabilities for intelligent mine construction. Through cloud platforms, centralized management and processing of mining data can be achieved, facilitating data sharing and collaborative work.
9. 5G Communication Technology: 5G technology, with its high speed and low latency, meets the communication needs of intelligent mine construction. It allows for real-time monitoring and management of underground equipment and personnel, enhancing production efficiency and safety.
10. Green Energy Technology: With increasing environmental awareness, green energy technologies are gaining importance in intelligent mine construction. Clean energies such as solar and wind power are gradually replacing traditional fossil fuels, providing sustainable energy supplies for mining operations.
The application of these latest technologies will help propel intelligent mine construction to higher levels, enhancing production efficiency and management standards, reducing production costs and safety risks, and injecting new vitality into the sustainable development of the mining industry.

Factors Affecting TBM Construction Quality and Efficiency: An Analysis
What factors affect the quality and efficiency of TBM construction? Several key aspects influence TBM (Tunnel Boring Machine) construction quality and efficiency, including:
1. Geological Conditions: Geological conditions are the primary factors affecting TBM construction quality and efficiency. Different geological types, rock hardness, and groundwater conditions directly or indirectly impact TBM operations. For example, hard rock formations can accelerate tool wear, while weak formations may increase the risk of collapses.
2. TBM Equipment Performance: The performance and quality of TBM equipment are directly related to construction quality and efficiency. High-quality, high-performance TBM equipment can better adapt to complex and variable geological conditions, reduce failure rates, and improve construction efficiency. Conversely, poor performance or defective equipment can lead to construction interruptions or decreased quality.
3. Construction Technology: Construction technology is a crucial factor influencing TBM construction quality and efficiency. Reasonable construction processes, advanced operation techniques, and management experience can significantly enhance construction quality and efficiency. For example, optimizing cutter configurations, improving thrust systems, and perfecting support systems can all increase TBM work efficiency and construction quality.
4. On-Site Management: On-site management levels directly affect TBM construction quality and efficiency. Good on-site management ensures orderly construction processes, reducing unnecessary delays and accidents. Additionally, effective material management and personnel scheduling are key factors in improving construction efficiency.
5. Personnel Quality: The quality and skill level of operators have a significant impact on TBM construction quality and efficiency. High-quality, experienced operators can better master TBM operation techniques and maintenance knowledge, thereby improving construction quality and efficiency.
6. Environmental Factors: Environmental factors such as temperature, humidity, and ventilation also affect TBM construction. Extreme environmental conditions can increase equipment failure rates or reduce construction quality. Therefore, appropriate measures must be taken to adapt to and improve the construction environment.
7. Safety Management: Safety management is a critical factor influencing TBM construction quality and efficiency. Strict safety management systems and measures ensure a safe and stable construction site, preventing accidents that could cause construction interruptions and quality declines. Additionally, enhancing operators' safety awareness and self-protection capabilities is very important.
8. Policies and Regulations: National and local government policies and regulations also impact TBM construction. For example, environmental regulations may restrict certain construction methods, while safety regulations may impose higher requirements on site management and operations.
9. Economic Factors: Economic factors such as budget, cost control, and investment returns are also important influences on TBM construction quality and efficiency. Reasonable cost control and investment return analysis can help project stakeholders make more scientific and rational decisions, ensuring the quality and efficiency of TBM construction.
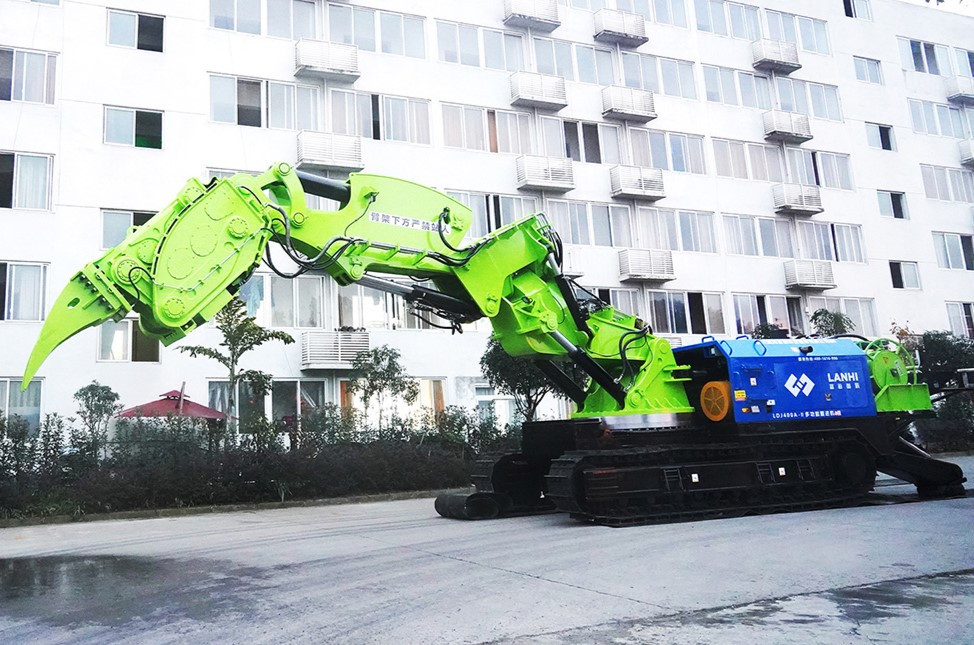
TBM Tunnel Boring Machine: Advantages and Working Principles
The TBM (Tunnel Boring Machine) tunnel boring machine is an advanced underground construction device that can efficiently and safely excavate various types of geological formations. It is widely used in urban subway, railway, highway, and other tunnel construction projects.
The working principle of a TBM is based on mechanical excavation and rock-breaking technology. It primarily consists of a cutter head, thrust system, support system, and control system. The cutter head, the core component of the TBM, is equipped with multiple cutting tools to cut and break rocks. When the TBM starts, the cutter head rotates at a certain speed, cutting the rock and transporting the debris out of the tunnel via a conveyor belt. Simultaneously, the thrust system uses hydraulic cylinders to generate thrust, pushing the TBM forward. The support system reinforces and supports the tunnel walls in real-time as the TBM advances, ensuring construction safety. The control system monitors and controls various parameters of the TBM to ensure its normal operation.
The TBM tunnel boring machine offers many advantages, such as fast construction speed, high quality, and reliable safety. Compared to traditional blasting methods, the TBM reduces damage to the surrounding environment and minimizes noise and vibration impacts. Additionally, the TBM can achieve automated control, enhancing construction efficiency and management levels.
The LanHi LDJ400 series multifunctional tunneling machine is a specialized device used for non-blasting tunnel excavation. It mainly uses high-frequency hammers or breakers to impact and break rocks, bucket teeth or chisels to wedge into the surrounding rock for prying and breaking, and the free surface below the surrounding rock to automatically break the rock through gravity (the high-frequency hammer is mainly used for rocks below 40 MPa; harder, less developed rocks are handled using breakers). This machine employs local control and wireless remote control, adapting to tunnel excavations of 6 to 9.5 meters. It integrates functions such as high-frequency rock breaking, fast soft soil excavation, contour trimming, and dust suppression by spraying, making it suitable for construction in restricted blasting areas (such as airports, residential areas, and wildlife protection zones). It is highly adaptable, meets various surrounding rock construction needs, and reduces over-excavation and collapse incidents.
The TBM tunnel boring machine is an advanced tunnel construction device with broad application prospects. In future tunnel construction projects, as technology continues to advance and innovate, TBMs will play an increasingly significant role, driving the development of the tunnel construction industry.