
How to reduce rebound and dust when spraying concrete?
How to reduce rebound and dust when spraying concrete? When spraying concrete, the following measures can be taken to reduce rebound and dust:
Measures to reduce rebound:
1. Optimize the mix ratio: Use a reasonable mix ratio of cement, aggregate, water and admixtures to improve the cohesion and sprayability of concrete.
2. Control the spray distance and angle: The distance between the nozzle and the sprayed surface should be 0.6-1.2 meters, and the spray angle should be as perpendicular to the sprayed surface as possible.
3. Appropriate wind pressure and water pressure: According to the performance of the sprayer and the transportation distance of the concrete, adjust the appropriate wind pressure and water pressure. Generally, the wind pressure is controlled between 0.1-0.15MPa.
4. Layered spraying: The layer thickness should not be too large, generally 5-10 cm. Layered spraying can make the concrete adhere better to the sprayed surface.
5. Strengthen operator training: Improve the technical level and experience of operators so that they can master the spraying skills.
Measures to reduce dust:
1. Strengthen ventilation: Set up good ventilation equipment in the spraying operation area to discharge dust in time.
2. Wet spraying process: The wet spraying concrete process can significantly reduce the generation of dust.
3. Control the spraying speed: Avoid too fast spraying speed to reduce the dust generated by the friction between concrete and air.
4. Install water rings on the nozzles: Install water rings at the nozzles to suppress dust flying by spraying water.
5. Wear protective equipment: Construction workers wear effective dust masks, goggles and other protective equipment.
6. Humidification of raw materials: Appropriately humidify the aggregates before mixing to reduce the generation of dust.
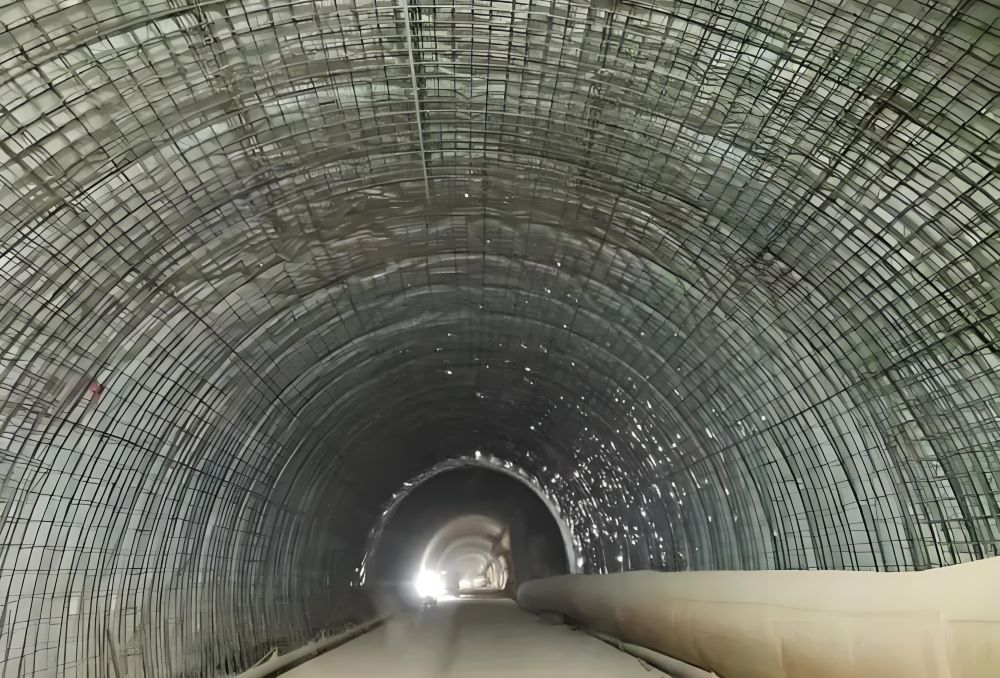
Types, functions and construction considerations of tunnel lining
Tunnel lining is a key technology in tunnel engineering. It is not only related to the structural safety of the tunnel, but also directly affects the service life and operational efficiency of the tunnel. The main function of tunnel lining is to support the surrounding rock and prevent the deformation and collapse of the surrounding rock. At the same time, it can also play a role in waterproofing and anti-seepage, ensuring the dryness and safety of the tunnel.
Types of tunnel lining
Tunnel lining can be mainly divided into the following types according to its construction method and structural characteristics:
1. Sprayed concrete lining: This is a fast and flexible construction method suitable for tunnel construction under various geological conditions. By spraying high-pressure concrete onto the surface of the tunnel surrounding rock, a protective layer is formed, which can quickly seal the surrounding rock and prevent further deformation of the surrounding rock.
2. Cast concrete lining: After the tunnel excavation is completed, concrete is poured using a formwork to form a lining with a more stable structure and better waterproof performance. The thickness and strength of this lining can be designed according to the specific needs of the tunnel.
3. Prefabricated assembled lining: Prefabricated concrete blocks or steel plates are produced in the factory and then transported to the tunnel site for assembly. This type of lining has a fast construction speed and is easy to control in quality, but the cost is relatively high.
4. Composite lining: Combining the characteristics of shotcrete and cast concrete, a layer of concrete is first sprayed as the initial support, and cast concrete is poured after the surrounding rock is stable to form a composite lining. This lining can better adapt to the deformation of the surrounding rock and improve the safety and stability of the tunnel.
The role of tunnel lining
The role of tunnel lining mainly includes:
Bearing loads such as surrounding rock pressure and groundwater pressure to ensure the stability and safety of the tunnel structure.
Preventing weathering, loosening and collapse of surrounding rocks, and reducing deformation of surrounding rocks around the tunnel.
Preventing groundwater infiltration and maintaining a dry environment inside the tunnel.
There are many types of tunnel linings, such as integral linings and composite linings. Their design and construction need to be comprehensively considered based on factors such as the geological conditions and use requirements of the tunnel.
Construction considerations for tunnel lining
The design of tunnel lining needs to comprehensively consider factors such as geological conditions, tunnel size, and use functions. During the construction process, the concrete mix ratio, pouring speed and maintenance conditions should be strictly controlled to ensure the quality of the lining. At the same time, it is also necessary to regularly inspect and maintain the tunnel lining to promptly detect and deal with problems such as lining cracks and water seepage to ensure the long-term safe operation of the tunnel.

Rock drilling rig, a powerful tool for drilling blasting holes in underground mining and tunnel construction
In the field of underground mining and tunnel construction, efficient drilling techniques are key to project progress and safety. As an important innovation in this field, rock drilling rigs have become indispensable equipment in underground engineering due to their excellent performance and adaptability. This article will delve into the design concept, working principle, technical advantages, and application of rock drilling rigs in modern underground construction.
Design concept and working principle
The design concept of rock drilling rig originates from a profound understanding of the complex underground environment. They are usually equipped with high-precision drilling systems and powerful power systems, which can quickly and accurately drill blast holes in various rocks. During operation, the trolley precisely controls the position and angle of the drill bit through advanced positioning systems and drilling arm adjustments, ensuring that the depth and direction of the borehole meet engineering requirements. At the same time, the trolley is also equipped with efficient dust removal and cooling systems to protect the normal operation of equipment in harsh environments.
Technical advantages
1. High efficiency and accuracy: Compared with traditional manual drilling, rock drilling rigs can complete drilling tasks at higher speed and accuracy, greatly improving the efficiency of underground construction.
2. Safety and Environmental Protection: Automated operations reduce personnel exposure to hazardous environments, while efficient dust removal systems reduce dust pollution and have minimal impact on the environment.
3. Flexibility and adaptability: The rock drilling rig can adapt to various complex underground environments, including narrow tunnels and irregular rock structures, ensuring the smooth progress of the project.
4. Cost effectiveness: Although the initial investment is high, in the long run, the rock drilling rig can save a lot of costs for the project by improving efficiency and reducing labor requirements.
Modern applications
The application of rock drilling rigs is becoming increasingly widespread in modern underground mining and tunnel construction. Whether it is the mining of metal mines or the excavation of highways and railway tunnels, their presence can be seen. Through precise drilling of blasting holes, the rock drilling rig provides a solid foundation for subsequent blasting operations, ensuring the safety and progress of the project.
The rock drilling rig has become an indispensable and efficient drilling tool in underground engineering due to its unique design, excellent performance, and wide application. With the continuous advancement of technology, future rock drilling rigs will become more intelligent and environmentally friendly, providing stronger support for the rapid development of underground engineering.
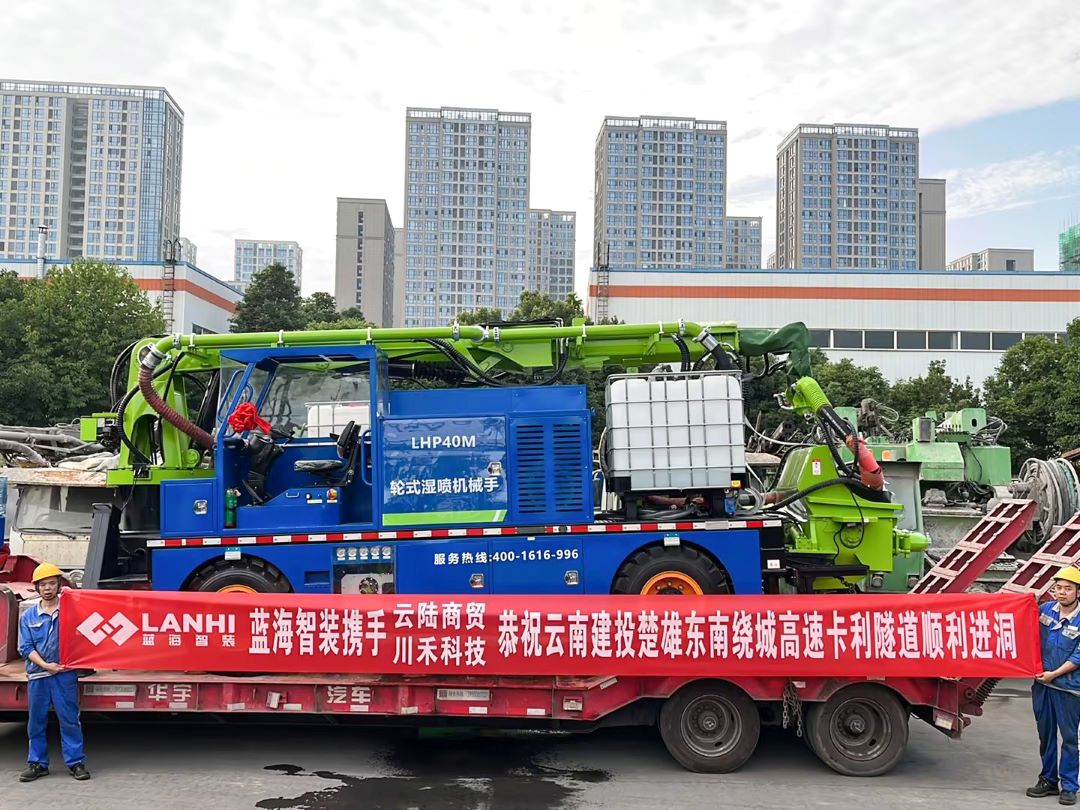
Five reasons for the rapid development of concrete wet spraying trucks in recent years
In recent years, the application of concrete wet spraying trucks has rapidly developed and received widespread attention in various engineering projects. The reasons for its rapid development can be mainly attributed to the following five aspects:
1. Significant advantages of wet spraying technology
Wet spraying technology has demonstrated numerous advantages during the construction process. Compared with traditional dry spraying techniques, wet spraying technology has four significant advantages. Firstly, wet spraying technology can significantly reduce the dust concentration on construction sites, effectively eliminating potential hazards to workers' health. Secondly, the production efficiency of the concrete wet spraying trolley is extremely high, capable of spraying 10 to 30 cubic meters of concrete per hour, greatly accelerating the construction progress. In addition, the rebound rate of wet spraying technology is relatively low, which can reduce the rebound rate of concrete to below 10%, reduce material waste, and save costs. Finally, the wet spraying process, due to its easily controllable water cement ratio, can significantly improve the uniformity of concrete and ensure higher construction quality.
2. Strict environmental requirements and policy support
With the increasingly strict domestic environmental regulations, the demand for mechanized construction is becoming more urgent. National policies and relevant industry standards clearly encourage and support the use of wet spraying technology, which not only meets environmental requirements but also promotes the improvement of construction efficiency and quality. Therefore, the application of wet spray trucks has been strongly promoted at the policy level and has become the preferred equipment for many engineering projects.
3. Rising labor costs drive mechanization
In recent years, labor costs have continued to rise, and traditional manual construction methods have gradually lost their advantages in terms of cost and efficiency. In contrast, the mechanized operation method of concrete wet spraying trolley not only improves construction efficiency, usually more than twice that of manual labor, but also reduces dependence on labor, reduces personnel risks and management costs. Therefore, using wet spray trucks for construction has become a wise choice for more and more projects.
4. Technological progress and market maturity of domestic manufacturers
Domestic concrete wet spraying truck manufacturers have made significant progress in research and technological innovation. With the gradual maturity of product technology, standardized and serialized wet spray truck products have emerged in the market. These technological advancements not only improve the reliability and stability of equipment, but also make products more competitive in the market and widely favored by customers.
5. A comprehensive after-sales service system
The continuous improvement of the after-sales service system provides strong support for the widespread application of concrete wet spraying trucks. Manufacturers provide comprehensive operational training, technical support, and maintenance services to make equipment use and maintenance more convenient, effectively extending the service life of the equipment. This comprehensive after-sales service further promotes the popularization and application of wet spray trucks in various construction projects.
The concrete wet spraying trolley, with its technological advantages, policy support, cost-effectiveness, technological progress, and comprehensive after-sales service, has achieved rapid development in modern engineering construction and gradually become an indispensable key equipment in tunnel construction and other fields.
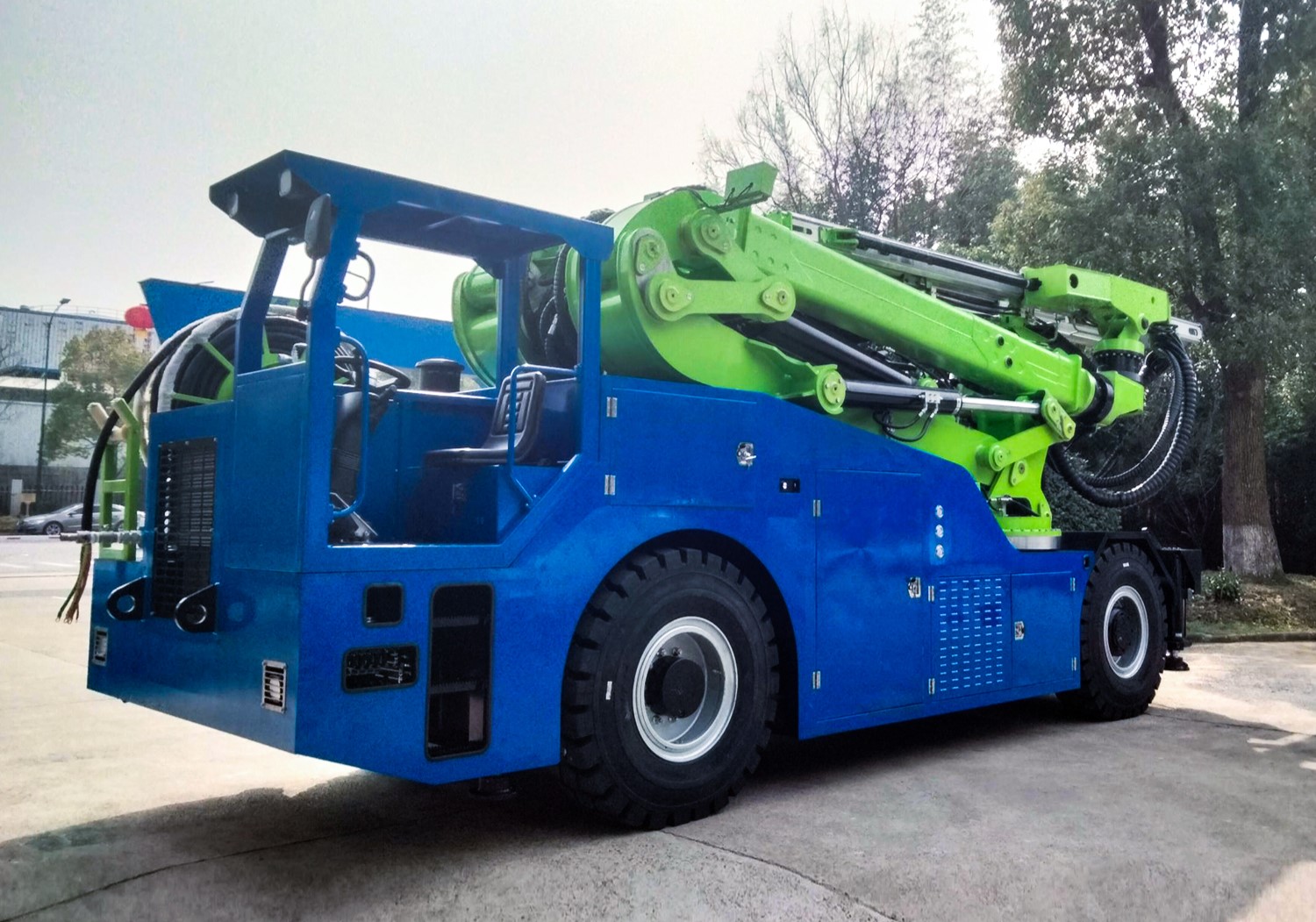
Four major advantages of rock drilling rigs in tunnel construction
In modern tunnel and mining projects, the application of rock drilling rigs has become one of the key technologies to improve construction safety, efficiency and quality. This advanced mechanical equipment, with its unique advantages, is gradually replacing the traditional manual drilling method, leading the industry to a more intelligent and automated direction.
1. A leap in safety performance
In tunnel excavation operations, the safety of operators is always the primary consideration. The rock drilling rig is equipped with a dedicated anti-rockfall cab, which provides operators with a safe working environment away from the face. This design not only avoids direct contact with potential rockfall hazards, but also reduces health risks caused by harsh environments, greatly improving the safety of operations.
2. Double guarantee of construction efficiency and speed
Compared with traditional manual drilling methods, rock drilling rigs show significant advantages in construction efficiency. Its drilling speed is far higher than that of manual drilling, and it can quickly complete drilling operations, greatly shortening the construction period. Especially in large-scale tunnel excavation projects, this efficient operation method can significantly improve the progress of the overall project and save valuable time for the project.
3. Effective control of labor costs
Using drilling rigs for drilling operations can significantly reduce dependence on manpower. The increase in automation means that fewer operators can complete more work, which effectively reduces labor costs. In addition, due to the improvement in construction efficiency, the overall cost of the project can be optimized, bringing higher economic benefits to engineering contractors.
4. Revolutionary improvement in construction quality
The precise positioning and stable propulsion capabilities of the drilling rig make it far superior to manual operation in terms of drilling quality. Once the drill rod is fixed, high-precision propulsion can be achieved regardless of horizontal or specific inclination angles to ensure that the drilling position is accurate. This not only reduces the amount of over-excavation, but also ensures the accuracy of excavation and forming, making the final tunnel structure more in line with design requirements and improving the overall quality of the project.
In summary, the application technology advantages of the drilling rig are significant, which not only improves the safety and efficiency of tunnel and mining projects, but also effectively controls costs and improves construction quality. With the continuous advancement of technology, the drilling rig will play a more important role in future engineering practices and become a key force in promoting industry innovation and development.
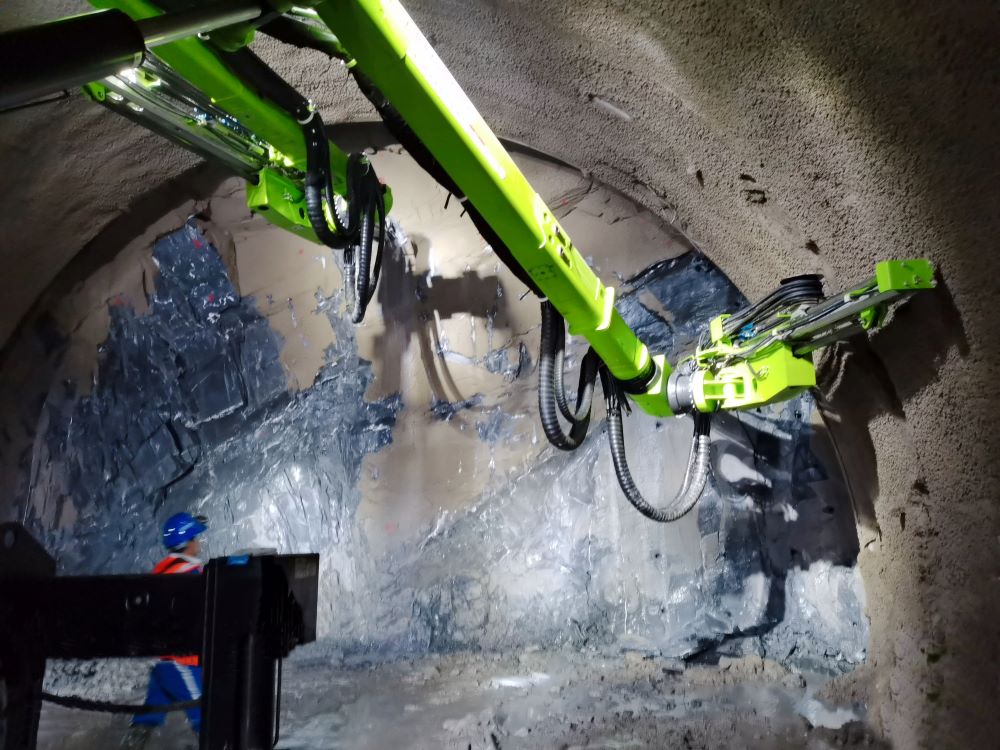
Analysis and prevention strategies of the five major reasons for drill rig stuck drill
In rock excavation projects such as mines and tunnels, drill rigs are key equipment, and their efficient operation directly affects the progress and cost of the project. However, drill stuck problems frequently plague construction personnel, not only reducing work efficiency, but also causing equipment damage. This article will explore the five major causes of drill stuck drills and propose corresponding prevention and solution strategies.
1. Improper anti-stuck pressure setting
The anti-stuck device is an effective tool to prevent drill stuck, but if the anti-stuck pressure setting value is too high, the equipment will not respond in time when the drill is really stuck. The correct setting value should ensure that when the drill stuck pressure reaches a certain threshold, the anti-stuck device can be quickly activated and the drill bit can be safely pulled out of the rock hole through reverse feeding.
2. Drill bit wear and damage
New drill bits or newly repaired drill bits have a certain taper, which helps drilling operations. However, in abrasive rocks, such as those with a high quartz content, the wear around the drill bit will gradually form an inverted cone. In severe cases, the drill bit will form a barb, which is difficult to withdraw from the rock hole, causing the drill to get stuck.
3. The influence of rock cracks
The cracks in the rock are like natural drill traps. When the drill bit enters these cracks, the squeezing effect of the rock will significantly increase the rotational resistance, causing the drill bit to get stuck and making it difficult to continue to advance or withdraw.
4. Insufficient drilling flushing
The flushing water is not only used to remove rock debris in the borehole, but also plays a role in cooling the drill bit and reducing friction. If the flushing water pressure is too low and the rock debris is not completely removed, the friction encountered by the drill bit during drilling will increase, the rotational resistance will increase, and eventually the drill bit will get stuck in the rock hole.
5. Hydraulic oil selection and ambient temperature
The viscosity of the hydraulic oil is significantly affected by temperature. In a low temperature environment, the viscosity of the hydraulic oil increases, which may cause the rotational resistance to exceed the set rotational pressure, thereby causing the drill to get stuck. Therefore, it is crucial to select hydraulic oil suitable for the current ambient temperature to maintain the stable operation of the hydraulic system.
The drill bit sticking problem of the drilling rig involves multiple factors, including equipment settings, drill bit status, geological conditions, flushing system efficiency and hydraulic oil selection. By comprehensively considering these factors, reasonably setting the anti-stuck pressure, regularly checking and maintaining the drill bit, optimizing the flushing water system, and selecting suitable hydraulic oil, the drill bit sticking phenomenon can be effectively prevented, the normal operation of the drilling rig can be guaranteed, and the engineering efficiency and safety can be improved.

System inspection process of wet concrete spraying machine equipment
As an indispensable and important equipment in modern tunnel engineering, the stability of its performance directly affects the quality and progress of construction. Therefore, regular systematic inspection and maintenance of wet concrete spraying machine equipment is the key to ensure its normal operation and extend its service life. This article will introduce in detail how to conduct a comprehensive system inspection of wet concrete spraying machine equipment before construction to ensure smooth construction.
I. Pumping system inspection
1. Hydraulic system inspection
- Hydraulic pipeline connection: First check whether there is oil seepage or oil leakage at the connection points of each pipeline in the hydraulic system. If any leakage is found, stop using it immediately, find the oil leakage point and repair it in time.
- Oil stain inspection: Whether there is oil stain on the ground is also an important basis for judging whether the equipment is normal. Oil stains on the ground usually indicate that the equipment is leaking oil, which should be given enough attention.
2. Hydraulic oil tank oil level inspection
- Oil level monitoring: The oil level in the hydraulic oil tank must be within the range required by the level gauge. If the oil level is lower than the standard, the equipment may not operate normally, so the oil must be replenished in time to ensure that the hydraulic system of the equipment can maintain normal pressure.
3. Pumping system water tank inspection
- Water volume monitoring: Check whether there is enough clean water in the water tank to ensure the normal operation of the cooling and lubrication system when the equipment is running. If the water volume is insufficient, it should be replenished in time.
II. Lubrication system inspection
1. Automatic lubrication pump inspection
- Lubricating oil level: Check whether the lubricating oil in the oil box of the automatic lubrication pump is sufficient. Insufficient lubricating oil may cause wear of the equipment when it is running under high load. Pay attention to replenishing sufficient lubricating oil during each inspection.
2. Manual lubrication point maintenance
- Grease gun operation: Use a grease gun to lubricate the manual lubrication points on the equipment to ensure that all moving parts are in good lubrication condition. This operation helps to reduce the wear rate of the equipment and extend its service life.
III. Accelerator system inspection
- Accelerator box inspection: The adequacy of the accelerator directly affects the spraying effect of the concrete. Therefore, before each construction, the reserve in the quick-setting agent box should be checked. If it is insufficient, it should be replenished in time to ensure that the concrete can set quickly during construction.
IV. Inspection of other key components
1. Nozzle inspection
- Check whether the concrete nozzle is worn. The wear of the nozzle will directly affect the spraying effect of the concrete and needs to be replaced in time.
2. Inspection of the delivery pipeline
- Concrete delivery hose and steel pipe: Check whether the concrete delivery hose and steel pipe have wear, cracks or other signs of damage to ensure the integrity of the pipeline.
- Hydraulic oil pipe and air duct: Check the hose and steel pipe parts of the hydraulic oil pipe and air duct. If they are severely worn, they should be replaced in time to prevent the equipment from malfunctioning during high-pressure operation.
System inspection of concrete wet spraying machine equipment is an important part of ensuring construction quality and safety. Through a comprehensive inspection of the pumping system, lubrication system and key components, equipment failure can be effectively prevented, construction efficiency can be improved, and the smooth progress of the project can be ensured. Regular maintenance and inspection not only extend the service life of the equipment, but also reduce the risk of downtime due to equipment failure during construction.

Good news! Lanhai has won three consecutive honors! Quality intelligent manufacturing, scaling new heights!
Recently, after going through processes such as certification review and public announcement, Lanhai has won three consecutive honors at the provincial, municipal, and district levels!
1. 2024 Sichuan Province Industrial Quality Benchmark
The recognition of industrial quality benchmarks in Sichuan Province focuses on five trillion level pillar industries, including electronic information, equipment manufacturing, food and beverage, advanced materials, and energy and chemical industries, aiming to create a quality improvement atmosphere of "setting benchmarks, learning from benchmarks, and surpassing benchmarks" throughout the province. In the 2024 certification event, based on lean management experience throughout the product lifecycle and outstanding innovative achievements in the industry, Lanhai Honor was listed as the "2024 Sichuan Province Industrial Quality Benchmark". This honor not only recognizes Lanhai's long-term commitment to quality and continuous innovation, but also deeply reflects the company's business philosophy of "focusing on quality and creating the future together".
2. 2024 Chengdu New Economy Demonstration Enterprise
The recognition of Chengdu's new economy demonstration enterprises is aimed at all new economy enterprises in the city, focusing on the ideas of "technology recognition, market recognition, capital recognition, and green development", with the aim of selecting enterprises with more innovative capabilities and market competitiveness throughout the city. Enterprises participating in this selection must meet the conditions of winning provincial-level or above scientific and technological awards, possessing valid invention patents, leading the development of international or national standards, and obtaining provincial-level or above technology platform recognition. Based on its profound accumulation of R&D strength and innovative achievements, Lanhai has finally been awarded the title of "2024 Chengdu New Economy Demonstration Enterprise". This is not only a recognition of the company's R&D innovation and breakthrough capabilities, but also a recognition of Lanhai's equipment market competitiveness.
3. Gazelle Enterprises in Wenjiang District in 2024
According to the "Identification Measures for Young Eagle Enterprises and Gazelle Enterprises in Wenjiang District, Chengdu (2024 Edition)", gazelle enterprises refer to innovative enterprises with strong innovation capabilities, high development potential, a certain scale, and explosive growth. The successful recognition of Lanhai as the "2024 Wenjiang District Gazelle Enterprise" is not only a double recognition of the company's innovative spirit and development potential, but also a powerful proof of Lanhai's future high-quality development prospects.
Sichuan Lanhai Intelligent Equipment Manufacturing Co., Ltd. has been committed to the research and development, production, and sales of complete sets of intelligent equipment for underground engineering and mining since its establishment in 2011. It has successively passed certifications such as High tech Enterprise, Specialized and Innovative "Little Giant" Enterprise, National Intellectual Property Advantage Enterprise, Sichuan Enterprise Technology Center, and Chengdu Academician (Expert) Innovation Workstation. More than 410 patents have been applied for, including over 90 invention patents.
The company's main products include underground engineering and mining complete sets of intelligent equipment such as tunneling machines, arch/arch anchor trolleys, drilling arch trolleys, wet spraying trolleys, rock drilling trolleys, etc. It has served multiple highway, railway, water conservancy, mining and other projects such as plateau railways, Chongqing Kunming high-speed railways, and Yiban Expressway. In the future, the company will continue to take innovation as the wing, quality as the rudder, continuously improve product and service quality, provide customers with more outstanding underground engineering solutions, and create greater value for partners!
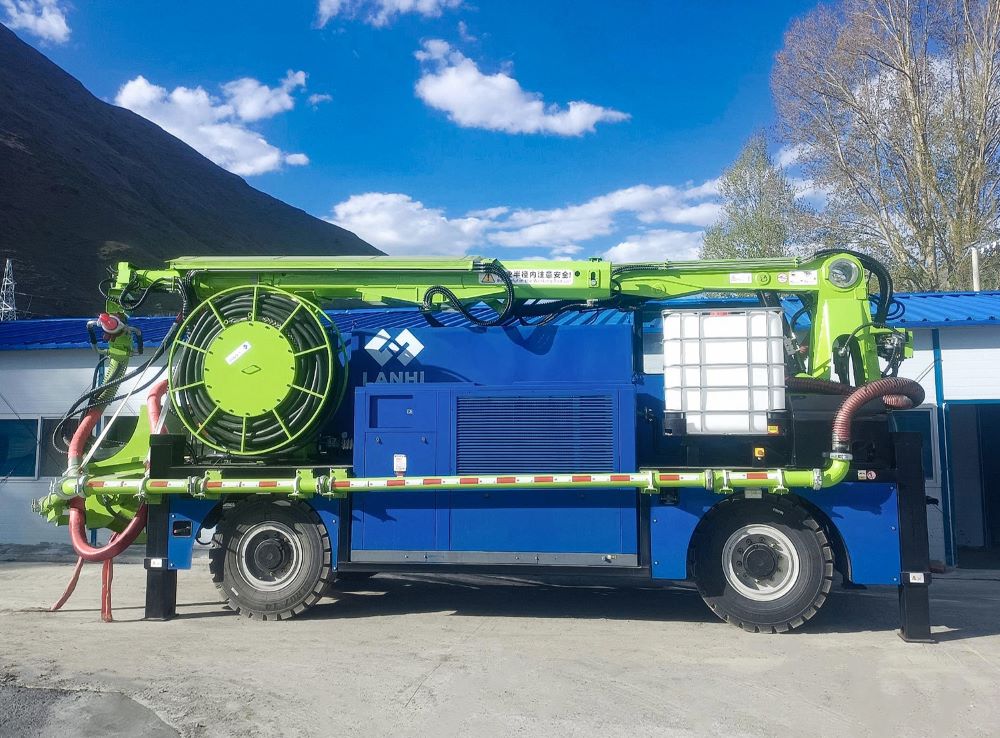
Concrete spraying machine, a construction equipment specially used for spraying concrete onto the tunnel wall
Concrete spraying machine is a construction equipment specially used for spraying concrete onto the tunnel wall. This equipment plays a key role in tunnel construction, especially in providing initial support and structural reinforcement.
Concrete spraying machine can be divided into two categories: dry spraying machine and wet spraying machine
- Dry spraying machine: Dry spraying machine transports dry mixture to the nozzle through a pipe, and then mixes it with water at the nozzle and sprays it onto the tunnel wall. Dry spraying machine equipment is relatively simple and suitable for small-scale spraying operations, but it is easy to generate a lot of dust during the spraying process, and the construction environment is relatively harsh.
- Wet spraying machine: Wet spraying machine transports wet concrete that has been mixed with water to the nozzle through pumping, and then sprays it onto the tunnel wall with the help of compressed air. The advantages of wet spraying machine are less dust, better construction environment, more uniform spraying effect, higher cohesion and density of concrete, so it has been widely used in modern tunnel construction.
Main features of concrete spraying machine
- Efficient construction: concrete spraying machine can spray concrete quickly and over a large area, which improves construction efficiency.
- Uniform spraying: The thickness of the sprayed concrete layer is uniform and can form a solid protective layer.
- Construction safety: Compared with traditional manual spraying, the use of spraying machine for construction can reduce the time that construction workers are exposed to dangerous environments and improve construction safety.
Applicable scenarios of concrete spraying machine
Concrete spraying machine is widely used in the initial support, secondary lining, reinforcement engineering and slope protection of tunnels, mines and underground projects. In tunnel construction, it is mainly used to provide initial support for the tunnel wall to prevent collapse and provide a stable working surface for subsequent support construction.
As an indispensable equipment in tunnel construction, concrete spraying machine greatly improves construction efficiency and safety, while ensuring the quality of concrete spraying.
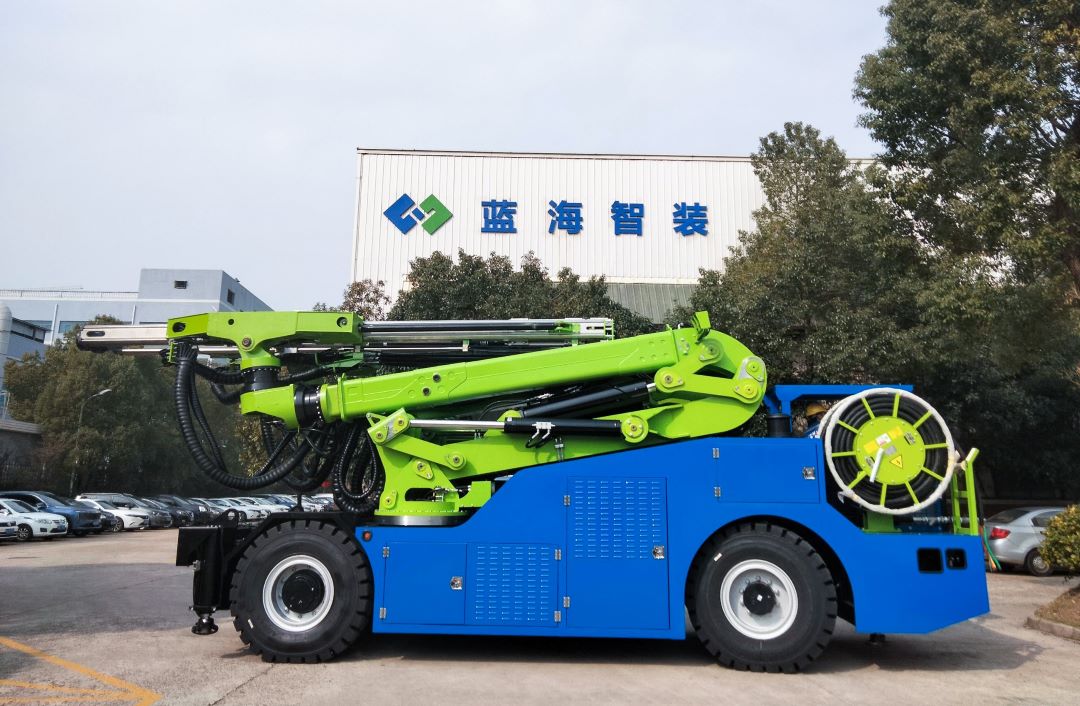
Rock drilling rig, a powerful tool for explosive drilling construction in modern mining and tunnel engineering
With the continuous advancement of technology, the fields of modern mining and tunnel engineering have undergone revolutionary changes, and the widespread application of rock drilling rigs is a microcosm of this change. The rock drilling rig, with its outstanding performance advantages, is reshaping the construction standards of the industry and becoming a key technology for improving construction safety, efficiency, quality, and cost control.
1. Significant improvement in construction safety performance
In traditional manual rock drilling operations, operators often need to directly face the risk of rock falling, and safety issues have always been a major challenge in the industry. The emergence of rock drilling rigs completely changed this situation. It has designed a dedicated anti rockfall cab to ensure that operators work in a safe environment, away from potential hazards in the palm face, greatly reducing safety risks during the construction process and providing a safer working environment for workers.
2. Efficient construction, accelerating project progress
The rock drilling rig not only improves the safety of construction, but its construction efficiency is also remarkable. Compared to traditional manual drilling, the drilling speed of rock drilling rigs is faster, which can significantly shorten the construction period and effectively accelerate the project progress. This not only saves time costs, but also provides the possibility for the project to be completed ahead of schedule, thereby bringing more economic benefits to the owners.
3. Effective control of labor costs
In today's increasingly high labor costs, the advantages of automated operation of rock drilling rigs are becoming more and more apparent. It reduces reliance on manual labor, effectively lowers labor costs, and further shortens the construction period by improving construction efficiency, achieving dual cost control. This is of great significance for improving the overall economic benefits of the project.
4. A leap in construction quality
The introduction of rock drilling rigs has also brought significant improvements in construction quality. Its precise drilling capability ensures that the drill rod advances according to the preset horizontal or fixed inclination angle. Compared with manual control, it greatly improves the accuracy of drilling, reduces overexcavation, and makes excavation more precise. It not only improves engineering quality but also reduces material waste, achieving a win-win situation of economic and environmental benefits.
Rock drilling rigs, with their outstanding performance in construction safety, efficiency, cost control, and quality improvement, are becoming the preferred equipment in modern mining and tunnel engineering fields, leading the industry towards more efficient, safer, and more economical development.