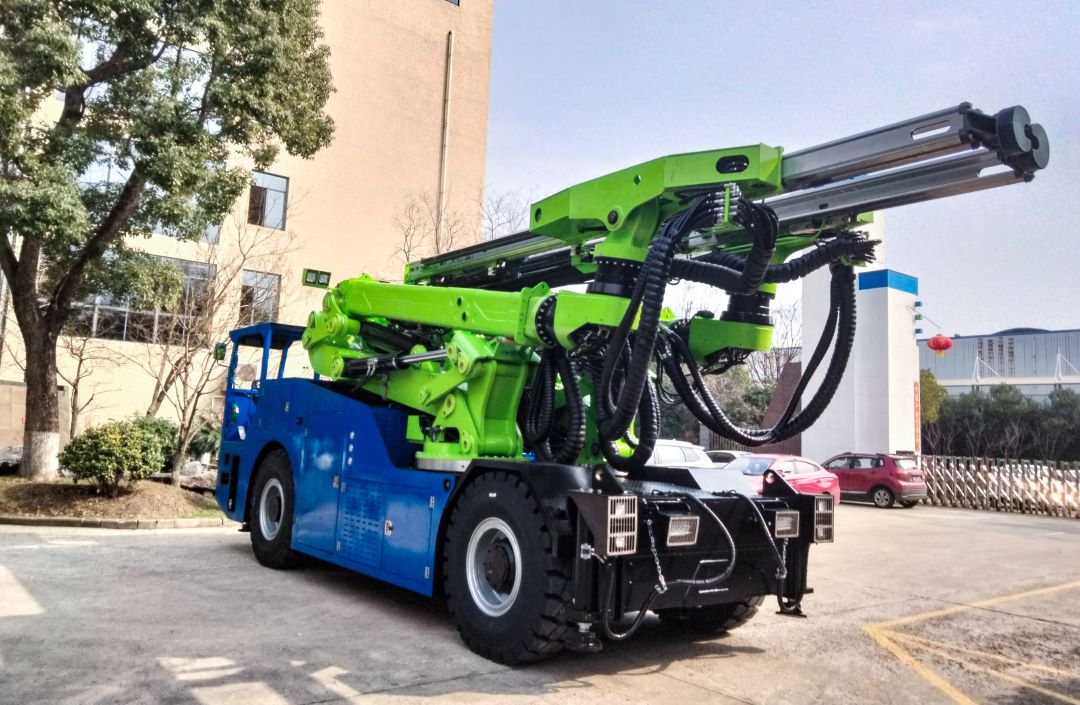
What are the differences between different types of rock drilling rigs?
There are significant differences in design, performance, application environment, and operational efficiency among different types of rock drilling rigs, which are mainly reflected in the following points:
1. Homework environment:
-Open pit rock drilling rig: Designed to adapt to open spaces, usually with a large volume, strong stability and power, suitable for open environments such as open-pit mines and large construction sites.
-Underground rock drilling rig: compact structure, emphasizing safety and flexibility, suitable for operation in narrow and limited ventilation conditions of mines, equipped with specialized ventilation and lighting systems to ensure the safety of underground operations.
2. Walking mechanism:
-Tire type rock drilling rig: With fast movement speed and flexible steering, it is suitable for working environments with flat and hard terrain, such as highway construction and open-pit mines.
-Crawler rock drilling rig: With stronger grip and passing ability, it is suitable for stable operation on soft ground, steep slopes, or rugged terrain, such as forests and swamps.
3. Quantity of rock drills installed:
-Single arm rock drilling rig: usually has a simple structure and flexible operation, suitable for working environments that require high-precision drilling or limited space, such as tunnel construction.
-Two arm and multi arm rock drilling rigs: equipped with multiple rock drills, capable of drilling multiple points simultaneously, greatly improving operational efficiency, suitable for large-scale mining, large-scale tunnel excavation and other engineering projects that require rapid advancement.
4. Power system and energy type:
-Different types of rock drilling rigs may also have different power systems, such as diesel engines, electric motors, etc. Electric rigs are more common in underground operations because they reduce harmful gas emissions and are more environmentally friendly and safe.
5. Level of automation and intelligence:
-Modern rock drilling rigs are increasingly adopting automation control and intelligent technologies, such as GPS positioning, remote monitoring, automatic drilling, etc. The application of these technologies significantly improves operational accuracy and efficiency, while also reducing the labor intensity and risks of manual operations.
Different types of rock drilling rigs have their own focuses, and choosing the appropriate model of rock drilling rig is crucial for improving operational efficiency, ensuring operational safety, and reducing operating costs. In practical applications, comprehensive consideration should be given to the specific working environment, project scale, and requirements to achieve the best construction effect.
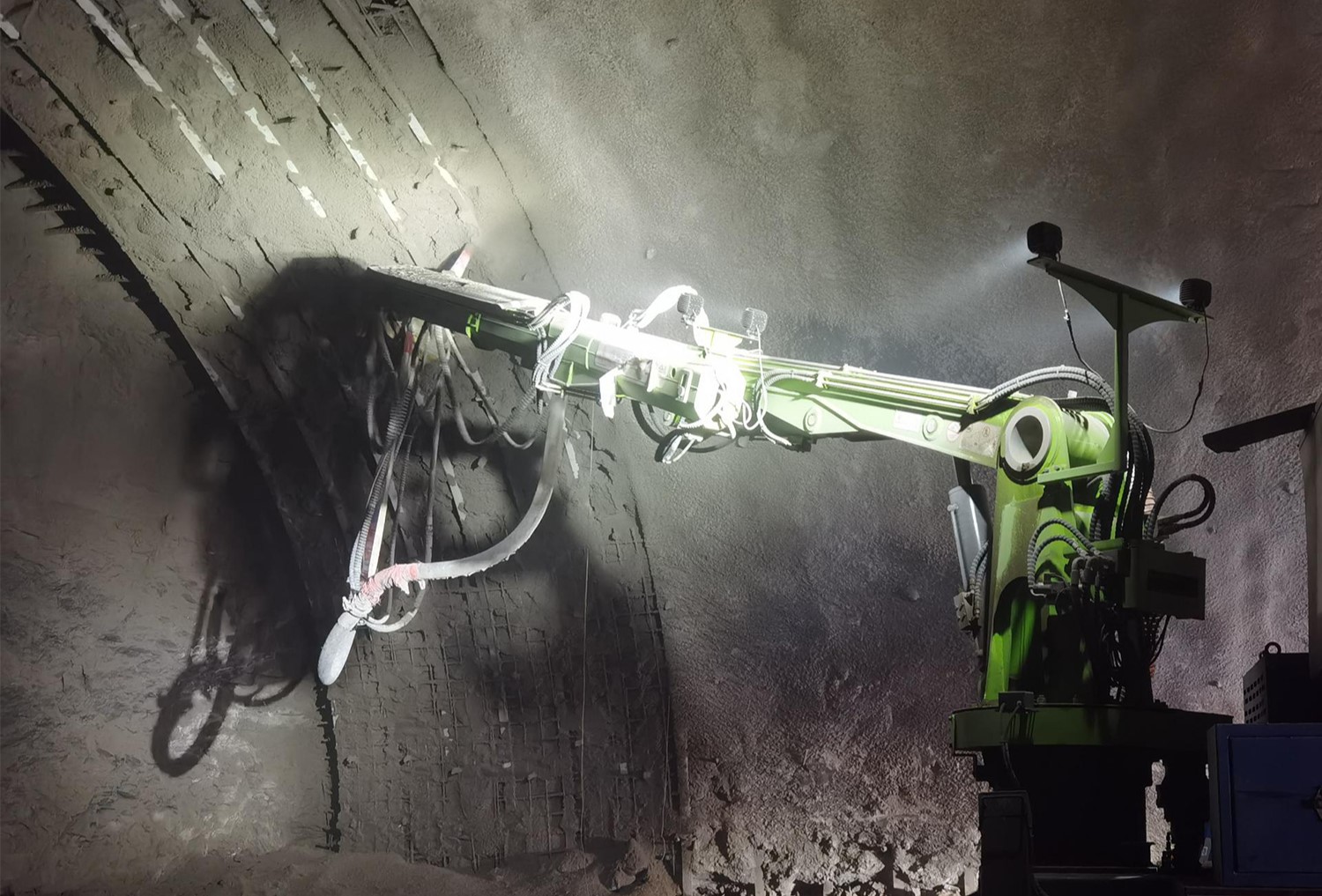
Concrete wet spraying machine plays a role of high safety, high environmental protection and high efficiency in the initial support of tunnels
In the initial stage of tunnel construction, the choice of support technology is directly related to the safety, environmental protection and economy of the project. In recent years, with the continuous advancement of tunnel construction technology, concrete wet spraying machine has been used more and more widely in the initial support of tunnels. Its high safety, high environmental protection, high efficiency and low cost characteristics are gradually becoming the preferred solution for the initial support of tunnel construction.
Safety: Building a lifeline
Concrete wet spraying machine adopts wet spraying process. Compared with the traditional dry spraying process, it can effectively reduce the dust concentration during the construction process and reduce the health hazards to construction workers. At the same time, wet spraying concrete has better adhesion and strength, can quickly form a stable support structure, and provide a safer working environment for tunnel construction workers.
Environmental protection: practice of green construction
During the construction process, the wet spraying concrete process greatly reduces the impact on the surrounding environment due to its low dust emission and low noise characteristics, which is in line with the concept of green construction in modern tunnel construction. In addition, the wet spraying process can effectively control the amount of concrete used and reduce material waste, further reflecting the practice of environmentally friendly construction.
High efficiency: accelerating the progress of the project
The wet spraying machine has a high degree of automation, can achieve continuous operation, and significantly improves the construction efficiency. The concrete of the wet spraying process is evenly mixed and has a fast spraying speed. It can complete a large area of ??support work in a short time, greatly shortening the tunnel construction cycle, and plays an important role in accelerating the progress of the project.
Low cost: significant economic benefits
The wet spraying concrete process also performs well in reducing construction costs. Due to its fast construction speed and high material utilization rate, it can effectively control costs. At the same time, the wet spraying process reduces dependence on labor, reduces labor costs, and improves the economic benefits of the entire tunnel project.
In summary, the application of wet spraying machines in the initial support of tunnels not only improves the safety and environmental protection of construction, but also significantly improves construction efficiency and reduces costs. It is a technological innovation in the field of tunnel construction. In the future, with the continuous advancement of technology, the role of wet spraying machines in the initial support of tunnels will become more prominent, providing a stronger guarantee for the safe, efficient and green construction of tunnel projects.

What is the construction process of shotcrete? Shotcrete construction process (8 steps)
In modern construction and civil engineering, shotcrete technology is widely used because of its high efficiency, flexibility and strong adaptability. This article will introduce the construction process of shotcrete operation in detail, aiming to provide construction personnel with a clear operating guide to ensure construction quality and safety.
I. Construction preparation
Construction preparation is the first and key step in shotcrete operation. This includes the assessment of the site environment, the inspection of equipment and the training of personnel. The construction team needs to conduct a detailed survey of the operation area, understand the geological conditions, and formulate a reasonable construction plan. At the same time, ensure that all construction equipment is in good condition and that construction personnel are familiar with the operating procedures and safety regulations.
II. Treatment of the sprayed surface
The treatment of the sprayed surface is an important link in improving the bonding strength and construction quality of shotcrete. First of all, loose materials, oil stains and accumulated water on the sprayed surface should be removed to ensure that the sprayed surface is clean and dry. If necessary, the sprayed surface should be roughened to increase the contact area between the sprayed concrete and the sprayed surface and improve the bonding effect.
III. Bury the marking nails of the sprayed layer thickness
In order to control the thickness of the sprayed concrete, marking nails should be buried on the sprayed surface before construction as a reference for the spraying thickness. The marking nails should be evenly distributed, and the spacing should be adjusted according to the construction requirements to ensure that the thickness of the sprayed concrete is uniform and meets the design requirements.
IV. Machinery is in place
Construction machinery, including sprayers, concrete mixers, transportation equipment, etc., should be in place in advance and debugged to ensure normal operation during the construction process. In addition, it is necessary to check the connection of wind, water and electricity to ensure that the operation will not be interrupted due to equipment failure during the construction process.
V. Connecting ventilation, water and electricity and testing the machine
Connecting ventilation, water and electricity is a necessary step before construction to ensure the power supply during the construction process. After connecting ventilation, water and electricity, all equipment should be tested, the operating status of the equipment should be checked, and faults should be eliminated in time to avoid unexpected shutdowns during the construction process.
VI. Initial spraying operation
The initial spraying operation is the first stage of spraying concrete construction, which is mainly used to form the foundation layer. During the initial spraying, the spraying angle and distance should be controlled to ensure that the concrete evenly covers the sprayed surface and forms a stable base layer. After the initial spraying operation is completed, the initial setting of the shotcrete needs to be checked to ensure that the concrete can quickly form strength and lay the foundation for subsequent operations.
VII. Re-spraying concrete operation
The re-spraying operation is carried out after the initial spraying layer reaches a certain strength, mainly used to increase the thickness of the shotcrete to meet the design requirements. During the re-spraying operation, the spraying parameters should be adjusted according to the construction progress and the solidification of the shotcrete to ensure the continuity and uniformity of the shotcrete.
VIII. Quality inspection
After the construction is completed, a quality inspection should be carried out immediately, including the thickness, strength, and appearance quality of the shotcrete. Quality inspection is a key link to ensure the quality of shotcrete construction. Any parts that do not meet the design requirements should be repaired in time to ensure the quality of the entire project.
Through the above steps, we can see the refinement and standardization of the construction process of shotcrete operations, which not only improves the construction efficiency, but also ensures the construction quality. The construction team should strictly abide by the construction process, pay attention to every detail, and ensure the safety and efficiency of the shotcrete operation.

General process flow and key points of initial tunnel support construction
In the construction process of tunnels and underground projects, initial support is a key link to ensure the safety and stable progress of the project. It not only provides safety for subsequent construction, but also directly affects the quality and progress of the entire project. This article will discuss in detail the general process flow of initial support construction and the importance of each step.
I. Initial spraying of concrete after excavation
After the excavation of the tunnel is completed, the first step is to carry out the initial spraying of concrete. This link aims to quickly close the rock surface, prevent the loosening of the surrounding rock and soil erosion, and provide a stable working surface for subsequent support work. Initial spraying of concrete usually adopts wet spraying to ensure the density and strength of the concrete, thereby effectively resisting the initial stress release of the surrounding rock.
II. System support construction
System support construction is the core link of initial support, mainly including the installation of anchor rods, steel mesh and steel frame. This process ensures the safety of the tunnel in the subsequent construction process by enhancing the stability of the surrounding rock.
1. Anchor construction: Anchors penetrate deep into the rock layer to tightly combine the surrounding rock with the support structure, thereby improving the self-stabilizing ability of the rock mass. The arrangement of anchors should be carried out according to geological conditions and design requirements to ensure that they can effectively resist the deformation of the surrounding rock.
2. Laying of steel mesh: The laying of steel mesh can enhance the crack resistance of shotcrete and improve the integrity of the support structure. Combined with anchors and steel frames, the steel mesh can form a complete support system to effectively control the displacement of the surrounding rock.
3. Steel frame installation: As the skeleton of the support structure, the steel frame can provide rigidity and support. Especially in areas with complex geological conditions and poor surrounding rock stability, the installation of the steel frame is particularly important.
III. Re-spraying concrete to the designed thickness
After completing the system support construction, re-spraying concrete is required to achieve the support thickness required by the design. This link can not only further enhance the strength of the support structure, but also ensure the integrity and waterproof performance of the support structure, providing guarantee for the long-term stable operation of the tunnel.
Key points:
Ensure that the concrete is sprayed evenly to avoid weak points.
The thickness of the re-sprayed concrete should be strictly controlled according to the design specifications to ensure the long-term stability of the tunnel.
The initial support construction is a key step in the tunnel project. It builds the "first line of defense" for tunnel safety through a series of processes such as initial spraying of concrete after excavation, system support construction (including the installation of anchor rods, steel mesh, and steel frames), and re-spraying of concrete to the designed thickness. Each link needs to be carefully designed and constructed to ensure the safety and quality of the entire project. Through scientific and reasonable initial support construction, the deformation of the surrounding rock can be effectively controlled, creating favorable conditions for subsequent construction and ensuring the smooth progress of the tunnel project.

How to judge whether the impact frequency of the pneumatic impact bolter is too high?
How to judge whether the impact frequency of the pneumatic impact bolter is too high? The following methods can help to judge whether the impact frequency of the pneumatic impact bolter is too high:
1. Observe the wear of parts: Frequent and high impact frequency will cause the moving parts, such as pistons and connecting rods, to wear more. If you find that the wear rate of these parts is abnormally fast, it may be caused by too high impact frequency.
2. Feel the vibration and noise: Too high impact frequency often causes the machine to produce strong vibration and loud noise. If the operator feels that the vibration is abnormally strong and the noise is too loud during operation, which exceeds the normal acceptable range, it may mean that the impact frequency is too high.
3. Check energy consumption: Too high impact frequency will increase the consumption of gas source. By monitoring the use of gas source, if it is found that the consumption rate is significantly higher than the normal level, it may be that the impact frequency is too high.
4. Evaluate the drilling quality: Too high impact frequency may lead to a decline in drilling quality, such as uneven hole wall and excessive wear of drill bit. If such a situation occurs, and other factors are excluded, it should be considered whether the impact frequency is too high.
5. Comparison of work efficiency: Under the same working conditions, if the drilling speed does not increase significantly, but the equipment failure frequency increases, it may be caused by unreasonable and too high impact frequency settings.
Too high impact frequency of pneumatic impact anchor bolter may have the following effects:
1. Increased wear of parts: Too high impact frequency will cause the moving parts inside the machine, such as pistons and connecting rods, to bear greater impact and friction, resulting in faster wear and shortening the service life of parts.
2. Increased energy consumption: Too high impact frequency often means that more gas source energy supply is required, which increases energy consumption and increases the cost of use.
3. Reduced working stability: It may cause the machine to produce greater vibration and noise, affecting the operator's operating comfort and work efficiency, and may also reduce the overall stability and reliability of the equipment.
4. Affected drilling quality: Too high impact frequency may not give the drill bit enough time to cut the rock, resulting in a rough and irregular surface of the borehole, and may even cause problems such as hole wall collapse, affecting the drilling quality.
5. The equipment is prone to heat: Rapid and frequent impacts will generate more heat. If the heat is not dissipated in time, it may cause the equipment to overheat, affecting its normal operation and service life.
6. Damage to connected parts: Strong and frequent impacts may cause excessive stress and fatigue damage to other parts connected to the anchor bolter, such as drill rods, connecting hoses, etc., increasing the risk of damage.

How does an anchor drill work? Working process of an anchor drill
An anchor drill is a drilling device specially used in geotechnical engineering. It is mainly used to drill holes in rocks or soil in order to install anchor rods or anchor cables to reinforce structures such as slopes, tunnels, and dams. So how does an anchor drill work? Let's talk about the working process of an anchor drill.
1. Positioning and fixing: First of all, the anchor drill needs to accurately locate the drilling position according to the design requirements, and stably fix the machine on the working surface through its own support system (such as legs).
2. Drilling: Start the power system of the drilling rig and drive the drill rod and drill bit to rotate by hydraulic or electric means. The drill bit is usually made of cemented carbide and has high wear resistance and cutting ability. While the drill bit rotates, it applies downward pressure through the propulsion mechanism to enable the drill bit to cut into the rock and soil layer.
3. Deslagging: As the drill bit goes deeper, the rock and soil are broken into small pieces. These debris need to be discharged from the hole in time to ensure the smooth progress of drilling. Anchor drilling rigs are usually equipped with a slag removal system, which can blow the debris out of the drill pipe through compressed air generated by an air compressor, or use a mud pump to bring the debris out through mud circulation.
4. Depth control: During the drilling process, the operator needs to monitor the depth of the drill hole to ensure that the designed depth is reached. This is usually achieved through a depth gauge or an electronic control system.
5. Drilling completion: When the hole reaches the predetermined depth, the drilling is stopped and the drill pipe and drill bit are removed from the hole. At this time, the hole may need to be cleaned to ensure the smooth installation of the subsequent anchor or anchor cable.
6. Installing anchor or anchor cable: After the drilling is completed, the prefabricated anchor or anchor cable is inserted into the hole, and then grouting material (such as cement slurry) is injected to fix the anchor or anchor cable and provide the required bearing capacity.
The working efficiency and performance of the anchor drilling rig are affected by many factors, including the power of the rig, the material and design of the drill bit, and the geological conditions of the working surface. In actual applications, operators need to select appropriate drilling rigs and drilling tools according to specific circumstances and adopt appropriate operating methods to ensure project quality and safety.

What are the common forms of tunnel support? Introduction to several common forms of tunnel support
What are the common forms of tunnel support? The common forms of tunnel support mainly include the following:
1. Shotcrete Support: High pressure concrete is sprayed onto the tunnel wall to form a strong protective layer. Shocked concrete can quickly cover the surface of surrounding rock, seal rock cracks, prevent weathering and water erosion, and increase the overall stability of surrounding rock. It can be used as temporary or permanent support.
2. Steel Arch Support: A frame structure made of steel or steel grating, installed inside the tunnel to provide support for the surrounding rock. Steel frame support can be used alone or in combination with shotcrete to form a more robust composite support system.
3. Rock Bolting or Cable Anchoring: By drilling holes in the surrounding rock, inserting high-strength steel bars or steel strands, and fixing them with materials such as cement slurry, the internal stress of the surrounding rock is transmitted to the deep and stable rock mass, thereby improving the self-supporting capacity of the surrounding rock.
4. Lining Support: A permanent structure made of poured concrete or other materials after tunnel excavation, used to withstand long-term ground pressure and water pressure, ensuring the stability and durability of the tunnel. The lining can be cast-in-place concrete, prefabricated concrete pipe segments, or masonry structures.
5. Prefabricated Support: Assemble precast concrete slabs, arches, and other components inside the tunnel to form a support structure. This method is suitable for tunnel projects with good conditions and can accelerate the construction progress.
6. Grille Support: A grid like structure welded from steel bars or steel bars, usually used in combination with shotcrete to form a lightweight support system, suitable for initial support of weak surrounding rock.
7. Soil Nailing: Drilling holes in soil or soft rock, inserting steel bars or pipes, and tightly bonding them with the surrounding soil through grouting to form an effect similar to anchor rods, enhancing the overall stability of the soil.
8. Freezing Method: In special circumstances, such as crossing aquifers or weak strata, artificial freezing of the strata can be used to temporarily harden them for tunnel excavation and support.
9. Grouting reinforcement: Injecting cement slurry or other chemical slurry into the surrounding rock to fill cracks, improve the compactness and bearing capacity of the surrounding rock, is a commonly used auxiliary support method.
These support forms can be used separately or in combination according to specific engineering requirements and geological conditions to achieve the best support effect.

Tunnel concrete wet spraying machine, a construction tool for the key link of initial support
In modern tunnel construction, concrete wet spraying machine, as an efficient construction equipment, plays a vital role, especially in the initial support stage. Initial support is a basic and key work in tunnel construction. Its purpose is to quickly support the surrounding rock after tunnel excavation to prevent deformation and collapse of the surrounding rock and provide a safe and stable working environment for subsequent construction. The emergence of concrete wet spraying machine has greatly improved the construction efficiency and quality of initial support and has become a "weapon" in tunnel construction.
Working principle of concrete wet spraying machine
Concrete wet spraying machine is a construction equipment that fully mixes concrete materials with water before spraying. It uses a high-pressure pump to transport the pre-mixed concrete slurry to the nozzle, and then sprays the concrete onto the construction surface through the compressed air at the nozzle. Compared with traditional dry spraying or semi-wet spraying, this construction method has the advantages of uniform mixing, low rebound rate, less dust and high construction efficiency.
Application in initial support
In the initial support of tunnels, wet spraying concrete machines are mainly used to spray concrete to form an initial support layer. This layer of concrete can not only immediately support the surrounding rock and prevent deformation of the surrounding rock, but also form a good bond with the surrounding rock to enhance the stability of the surrounding rock. In addition, the high density and good waterproof performance of wet spraying concrete also enable the initial support layer to effectively prevent the infiltration of groundwater, providing a good foundation for the subsequent waterproof layer construction.
Advantages of wet spraying concrete machines
1. High efficiency: wet spraying concrete machines can achieve fast and continuous concrete spraying, greatly improving the construction speed of initial support and shortening the tunnel construction period.
2. High quality: wet spraying concrete has good workability and density, can form a uniform and dense support layer, and improve the support effect.
3. Environmental protection: The wet spraying process reduces dust and rebound during the construction process, reduces the impact on the health of construction workers, reduces material waste, and is more environmentally friendly.
The application of wet concrete spraying machine in the initial support construction of tunnels not only improves construction efficiency and quality, but also reflects the advanced and environmentally friendly nature of modern tunnel construction technology.

Lanhi has become a star enterprise highly valued and promoted by the government
Under Mr. Lan's advanced planning and top-level structure, Lanhi has become a highly anticipated star enterprise. Its development potential and direction are in line with the policy support for vigorously developing industries, and therefore it has received high attention and strong promotion from the government.
Government support and project promotion
The governments of Chengdu and Changsha have provided strong support for the development of Blue Ocean Smart Clothing. In recent lock-in meetings, the government has prioritized the promotion of blue ocean smart equipment as a key project. Lanhi was able to successfully acquire land resources in both places, laying a solid foundation for its future development.
The core concept of enterprise development
Lanhi's success is attributed to his consistent spirit of hard work and perseverance. Enterprises prioritize customer needs, focus on product quality and innovation, and continuously improve customer satisfaction. Its fighting spirit and strong development ability have also won high praise from all walks of life.
Looking ahead to the future
Lanhi looks ahead to the future with a grand blueprint that embraces all rivers and faces a long and arduous task. The enterprise will continue to maintain a spirit of struggle, committed to achieving higher goals and pursuing greater success. We believe that with the support of the government and unremitting efforts within the company, Lanhi's future will be even brighter.

Working principle, application and advantages of hydraulic concrete wet spraying machine
Hydraulic concrete wet spraying machine is a mechanical equipment widely used in engineering fields such as tunnel construction and mine roadway reinforcement. Its main function is to transport and spray concrete onto the sprayed surface through a hydraulic system, forming a stable support layer. This article will provide a detailed introduction to the working principle and various components of the hydraulic concrete wet spraying machine.
Working principle of hydraulic concrete wet spraying machine
The core working principle of hydraulic concrete wet spraying machine is to use the thrust generated by the hydraulic system to transport concrete from the hopper to the nozzle and spray it onto the sprayed surface. The specific process is as follows:
1. Hydraulic pump operation: After the hydraulic pump is started, it pushes the piston in the working cylinder of the oil cylinder to perform reciprocating motion.
2. Concrete transportation: Under the push of the piston, concrete is transported through the conveying pipeline to the mixing pipe.
3. Compressed air action: At the mixing pipe, compressed air further dilutes the concrete and transports it to the nozzle through the pipeline.
4. Addition of quick setting agent: Add quick setting agent in a certain proportion at the nozzle to quickly set the concrete after spraying onto the sprayed surface.
5. Spray molding: Concrete is uniformly sprayed onto the sprayed surface under the combined action of compressed air and quick setting agent, forming the required support layer.
Application and advantages of hydraulic concrete wet spraying machine
Hydraulic concrete wet spraying machine is widely used in various projects that require concrete spraying due to its high efficiency and stable performance. The main advantages include:
-Easy to operate: The equipment has a high degree of automation, is easy to operate, and reduces manual intervention.
-Good spraying effect: The concrete is sprayed evenly, with strong bonding force, ensuring construction quality.
-Strong adaptability: Suitable for various complex construction environments, especially tunnels and underground engineering.
-Easy maintenance: The device has a compact structure, is easy to maintain and upkeep, and has low operating costs.
As an advanced construction equipment, hydraulic concrete wet spraying machine plays an important role in engineering construction with its unique working principle and superior performance. By reasonable use and maintenance, construction efficiency and quality can be significantly improved, providing strong guarantees for the smooth progress of engineering projects.