
Chinese Enterprises Open a New Era of Shield Tunneling Construction in Chile
With the continuous acceleration of urbanization and the increasing demand for transportation, underground engineering construction, especially tunnel projects, plays an increasingly important role in urban transportation construction. In South America, an eye-catching subway project—the Santiago Metro Line 7 in Chile—used a new type of tunnel boring machine for excavation in April of this year. This project, undertaken by China Railway Construction Group, has a total machine length of 110 meters, a excavation diameter of 10 meters, and a target excavation length of 6.6 kilometers. This marks the first subway project in South America where Chinese enterprises have adopted shield tunneling construction.
At the project initiation ceremony, Chilean President Sebastián Pi?era Echenique stated that the launch of this project is of great significance to Chile's transportation construction. China Railway Construction is responsible for Section 1 of the project, which is also the first subway project in South America where a Chinese company has adopted shield tunneling construction, promoting the entry of Chinese equipment into the South American subway market.
During the specific implementation of the project, the debut of China Railway Construction's "Matucana" shield tunneling machine attracted widespread attention. Shield tunneling machines are hailed as the "kings of engineering machinery," and "Matucana" was independently developed and produced by China Railway Construction, with a total machine length of 105 meters and an excavation diameter of 9.8 meters. The naming of this tunneling machine was presided over by Juan Carlos Mu?oz, the Minister of Transport and Telecommunications of Chile, and symbolizes "Mother Earth," blessing underground construction.
The project manager introduced that the project faces a series of challenges, including complex geological environments and high requirements for turning capabilities. To address these challenges, China Railway Construction has independently developed a series of core key technologies and innovatively designed the cutterhead and turning mechanism to ensure safe and efficient long-distance excavation of the shield tunneling machine.
The Santiago Metro Line 7 in Chile, with a total length of 27 kilometers and 19 stations, connects seven districts in the capital city of Santiago and is a key project of the Chilean government in recent years. Section 1 of the Santiago Metro Line 7, undertaken by China Railway Construction, is the most important section of the entire line. After the project is completed, it will significantly reduce the commuting time for residents along the line, providing convenient travel services for over 1.36 million residents.
The launch of this project marks further development of Chinese enterprises in the subway field in South America and injects new vitality into underground transportation construction in Chile. With the introduction and application of this advanced technology, Chile's urban transportation network will usher in more convenient and efficient development.

How to Choose Tunnel Construction Partners? What Conditions Should Excellent Tunnel Construction Companies Have?
When selecting partners for tunnel construction, a crucial consideration is whether the company provides high-quality after-sales service. So, what conditions should an excellent tunnel construction company have? Let's take Blue Ocean Intelligent Equipment Manufacturing Co., Ltd. as an example to introduce the after-sales service that an excellent tunnel company should have.
Firstly, Blue Ocean Intelligent Equipment has a comprehensive training mechanism for after-sales service. They offer various forms of training, including on-site and field training. On-site training involves regularly scheduled operator training classes, while field training involves sending after-sales specialists for installation, commissioning, and providing operational training and construction guidance to construction personnel after equipment delivery.
Secondly, Blue Ocean Intelligent Equipment emphasizes the establishment of service organizations and personnel configuration for after-sales service. They establish after-sales service points and parts warehouses in various locations when the number of equipment reaches a certain level. They also equip professional after-sales engineers and service vehicles to respond promptly to service needs. Currently, they have established after-sales service points in multiple regions and have over 200 after-sales personnel who conduct regular maintenance on equipment in designated areas.
Moreover, the after-sales service provided by Blue Ocean Intelligent Equipment is extensive. They dispatch experienced technicians to provide on-site guidance and technical support upon equipment delivery, assist customers in formulating construction plans, and conduct regular follow-ups while offering free technical consultations. Additionally, they provide a one-year warranty period for equipment quality, followed by lifetime paid services after the warranty period.
In conclusion, an excellent tunnel construction company should have a complete after-sales service system. Blue Ocean Intelligent Equipment, as a leading domestic underground engineering complete equipment integrator, has won the trust of customers with its high-quality after-sales service. Their after-sales service not only guarantees product quality but also maintains important customer relationships. In the future, they will continue to strive to improve their after-sales service level, create greater value for customers, and become long-term trusted partners for customers.
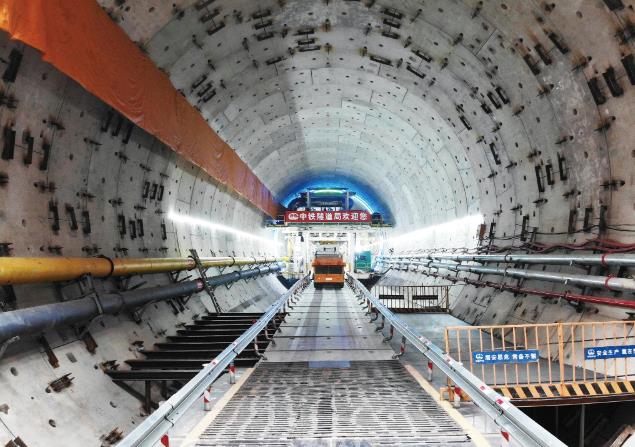
Traditional tunnel construction is transitioning towards intelligence and informatization
With the rapid development of technology, traditional tunnel construction methods are undergoing profound changes, accelerating towards intelligence and informatization. This transformation not only enhances construction efficiency but also greatly improves construction safety, while positively impacting the quality and environmental protection of tunnel projects.
The core of intelligent construction lies in the optimization of construction processes using advanced information technology, automation technology, and robotics. For example, by introducing Building Information Modeling (BIM) technology, engineers can create virtual models of tunnels on computers, simulate construction processes, predict potential issues, and formulate solutions in advance. This reduces errors and delays during actual construction, thus improving work efficiency.
The application of automated equipment in tunnel construction is also becoming increasingly widespread. For instance, the use of Tunnel Boring Machines (TBMs) has significantly reduced the need for manual excavation. Modern TBMs are equipped with advanced sensors and navigation systems, enabling precise tunnel positioning and orientation, reducing reliance on traditional support methods. Additionally, automated monitoring equipment can real-time monitor the stability of tunnels, promptly detecting cracks and leaks to ensure construction quality.
In terms of informatization, the application of big data and cloud computing technologies enables the collection, storage, and analysis of data in tunnel construction. By analyzing vast amounts of data generated during the construction process, construction plans can be optimized, resource utilization efficiency improved, such as rational scheduling of materials and equipment to reduce downtime. Furthermore, through cloud platforms, project team members can share information in real-time, enabling them to access the latest construction progress regardless of their location, thus improving team collaboration efficiency.
Intelligence and informatization also provide strong support for safety management in tunnel construction. For example, various sensors installed inside the tunnel can real-time monitor environmental parameters such as temperature, humidity, harmful gas concentrations, as well as tunnel deformation and crack development. Once abnormal data is detected, the system will immediately issue alerts, reminding workers to take appropriate safety measures. Additionally, through Virtual Reality (VR) and Augmented Reality (AR) technologies, immersive training experiences can be provided for workers, allowing them to learn operational skills and safety knowledge in simulated environments, thus enhancing their emergency response capabilities.
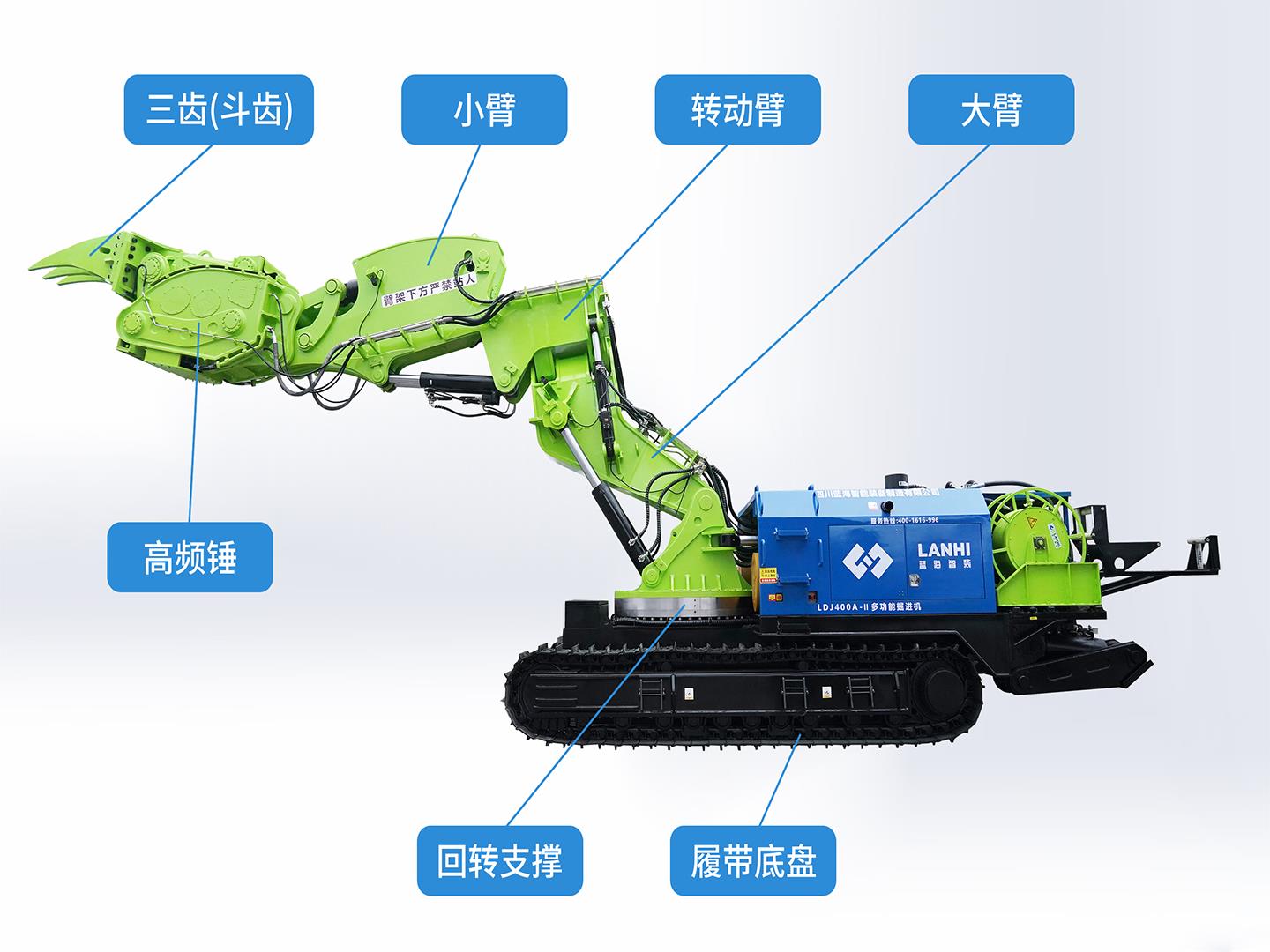
LDJ400 Series Multi-Functional Tunnel Boring Machine - the Pangolin of Non-Explosive Tunnel Excavation
The LDJ400 series multi-functional tunnel boring machine is a piece of equipment designed specifically for non-explosive tunnel excavation, playing a vital role in tunnel construction. Its main working principle involves using high-frequency or breaking hammers for rock fragmentation or utilizing the gravity effect below the surrounding rocks for automatic rock breaking. This series of equipment adopts local control combined with wireless remote control, capable of adapting to tunnel excavations ranging from 6 to 9.5 meters. It integrates functions such as high-frequency rock breaking, fast soil excavation, profile finishing, and spray dust removal, suitable for construction in areas where blasting is restricted, such as airports, residential areas, and wildlife protection zones. It demonstrates strong adaptability, meeting various rock construction requirements and reducing problems such as over-excavation and collapse.
The series includes multiple models, including LDJ400A, LDJ400B, and LDJ400C, each with different configurations and features. For instance, the LDJ400A series can be equipped with various types of hammers, and its dual-power design allows for both electric and diesel-powered operations, ensuring equipment flexibility and versatility. On the other hand, the LDJ400C series is equipped with slag removal function, with a slag removal capacity of up to 180m?/h, improving equipment efficiency in slag removal.
The performance characteristics of this series mainly include high excavation efficiency, minimal disturbance to surrounding rocks, control of over-excavation, spray dust removal, high-frequency rock breaking, remote operation, dual-power design, and high slag removal efficiency. These features make this series of equipment widely applicable in tunnel construction, having been utilized in various tunnel construction projects nationwide, including the Mianyang Municipal Tunnel, Chongqing-Kunming High-Speed Railway, Chengdu-Nanchong Expressway Expansion, Chongqing Metro Project, Tongzi Municipal Tunnel, Leshi Expressway, and Dusi Mountain Light Rail Project, among others. The LDJ400 series multi-functional tunnel boring machine has shown outstanding performance in environmental protection, improving excavation efficiency, reducing labor costs, and ensuring project quality, receiving widespread recognition.
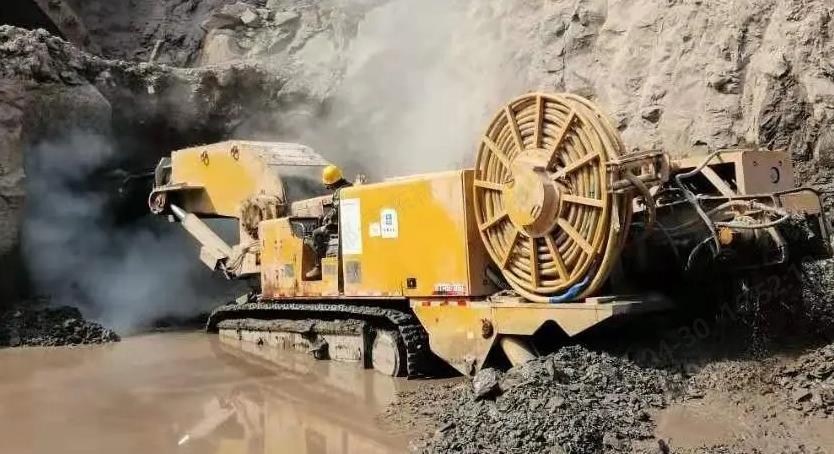
What are the types of TBM (Tunnel Boring Machine)? Introduction to the types of TBM
TBM, short for Tunnel Boring Machine, is an engineering machine used for underground tunnel construction. Depending on different functions and designs, TBMs can be classified into various types. Here are some common types of TBM.
1. Hard Rock TBM:
Hard Rock TBMs are suitable for hard rock geology such as granite and limestone. They are characterized by sturdy construction, typically equipped with high-strength disc cutters and scrapers to withstand high-impact and abrasive rock conditions. The propulsion and support systems of hard rock TBMs are reinforced to meet the challenges of hard rock geology.
2. Soft Rock TBM:
Soft Rock TBMs are suitable for softer geological conditions like soft rock, clay, and sand. Their cutting heads are designed to be more flexible, usually equipped with replaceable cutters and scrapers, as well as adjustable cutting parameters to adapt to different geological changes. The propulsion and support systems of soft rock TBMs are relatively lightweight to accommodate soft rock characteristics.
3. Slurry Shield TBM:
Slurry Shield TBMs are suitable for weak formations with a high presence of groundwater, such as mudstone and silty soil. They use a slurry circulation system to balance the pressure on the cutting face, preventing soil erosion and collapse. The propulsion and support systems of slurry shield TBMs are specially designed to operate in slurry environments.
4. Hybrid TBM:
Hybrid TBMs combine the features of hard rock TBMs and slurry shield TBMs, making them adaptable to complex and changing geological conditions. They are usually equipped with adjustable cutting heads and slurry circulation systems, capable of working in both hard rock conditions and switching modes in soft rock or slurry conditions. The propulsion and support systems of hybrid TBMs are highly adaptable.
5. Mixed Ground TBM:
Mixed Ground TBMs are suitable for tunnel projects with complex geological conditions composed of multiple formations. Their cutter tools and TBM designs typically offer higher flexibility and adaptability.
6. Rectangular TBM:
Rectangular TBMs are suitable for non-circular tunnels requiring larger cross-sections, such as urban underground space development and pedestrian passages.
7. Dual-Mode TBM:
Dual-Mode TBMs can seamlessly switch between hard rock and soft rock modes, adapting to complex and changing geological conditions.
There are various types of TBMs, each with unique characteristics and applications. When selecting a TBM, it's essential to consider factors such as geological conditions, tunnel dimensions, construction environment, efficiency, and cost-effectiveness to ensure the most suitable TBM type for the project needs, achieving efficient and safe tunnel construction. With ongoing technological advancements, the performance and functionality of TBMs continue to improve, offering greater convenience and possibilities for tunnel construction.
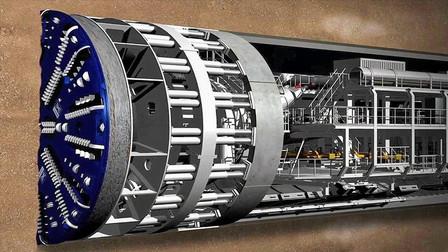
Which is better, Tunnel Boring Machine (TBM) or Shield Tunneling Machine (STM)? Differences between Tunnel Boring Machine and Shield Tunneling Machine
Some people may think that Tunnel Boring Machines (TBMs) and Shield Tunneling Machines are the same product, but they are not. TBMs and Shield Tunneling Machines are two important pieces of equipment used in underground engineering, and they have some significant differences in functionality and application. Let's take a look at which is better between TBMs and Shield Tunneling Machines, as well as the differences between them.
1、Different Definitions:
Tunnel Boring Machine (TBM) is a full-face tunnel construction equipment capable of continuous and efficient excavation of tunnels while simultaneously conducting support operations.
Shield Tunneling Machine (STM) is a tunnel excavation equipment that uses shield tunneling methods. It protects construction personnel and equipment through a shield shell while conducting tunnel support.
2、Different Components:
Tunnel Boring Machines mainly consist of a cutting head, main drive system, propulsion system, support system, measurement and guidance system, and muck handling system.
Shield Tunneling Machines primarily include a shield shell, cutting head, main drive system, propulsion system, support system (such as shield tail sealing system), and measurement and guidance system.
3、Different Designs and Structures:
Tunnel Boring Machines are typically simpler than Shield Tunneling Machines, with cutting tools mounted at the front to directly excavate rock and soil underground. Their design is more suitable for hard rock or firm geological formations.
Shield Tunneling Machines have more complex structures, usually including a shield to protect workers from geological collapse threats. They are equipped with a spraying system at the front to stabilize formations and control underground water flow.
4、Different Working Principles:
Tunnel Boring Machines crush rock or soil by rotating cutting heads while the propulsion system pushes the machine forward. The support system immediately installs prefabricated tunnel lining segments or sprays concrete for support.
Shield Tunneling Machines perform cutting operations within the shield shell. Simultaneously, they use a shield tail sealing system to tightly seal with the excavated tunnel wall, while the support system installs prefabricated tunnel lining segments or sprays concrete.
5、Different Uses:
Tunnel Boring Machines (TBMs) are typically used to excavate tunnels under various geological conditions, including soft soil, rock, and sludge. Their design allows them to directly cut and remove rock and soil underground, then transport excavated material out of the tunnel.
Shield Tunneling Machines are primarily used to excavate tunnels under conditions such as soft soil, slurry, and aquifers. They stabilize formations by injecting liquid materials (such as slurry or concrete) at the front and move forward through a propulsion mechanism.
6、Different Application Fields:
Tunnel Boring Machines are commonly used in tunnel construction for projects such as subways, roads, water conservancy, and urban infrastructure.
Shield Tunneling Machines are mainly used in projects that require tunneling through complex geological conditions, such as urban subways, water conservancy projects, and pipeline construction.
7、Different Construction Efficiency:
Tunnel Boring Machines typically have higher construction efficiency than Shield Tunneling Machines, but Shield Tunneling Machines can achieve faster construction speeds under certain specific conditions.
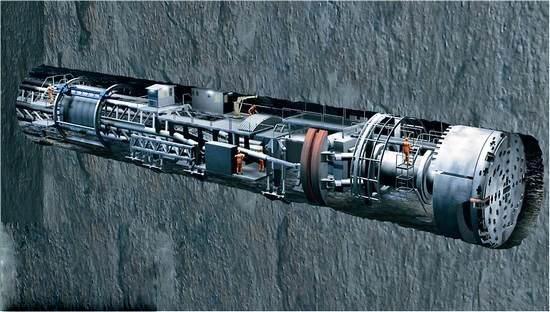
What is a TBM (Tunnel Boring Machine)? Understanding the basic structure, working principle, and applications of TBMs
A Tunnel Boring Machine (TBM) is an advanced tunnel construction equipment that excavates tunnels quickly and safely by rotating a cutting head to crush rocks or soil. Compared to traditional methods like blasting or manual digging, TBMs can excavate tunnels more efficiently and safely. TBMs are increasingly used in tunnel engineering, especially in the construction of long-distance and large-section tunnels.
I. Basic Components of TBM
1. Cutting Head:
The cutting head is the core component of a TBM, equipped with multiple cutting tools such as disc cutters, scrapers, and breakers. The design and configuration of the cutting head depend on geological conditions, with hard rock geologies typically using hard alloy or diamond tools, while soft rock or soil may require rotating blades or scrapers.
2. Main Drive System:
The main drive system provides power for the rotation of the cutting head, usually achieved through electric motors with power reaching several kilowatts.
3. Propulsion System:
The propulsion system pushes the TBM forward using hydraulic cylinders or mechanical devices, ensuring close contact between the cutting head and the tunnel walls.
4. Support System:
While advancing, the support system automatically installs prefabricated tunnel lining segments or sprays concrete to ensure tunnel stability.
5. Measurement and Guidance System:
Utilizing technologies such as lasers, GPS, or inertial navigation systems, the measurement and guidance system monitors the position and direction of the TBM in real-time to ensure accurate excavation according to the design alignment.
6. Muck Handling System:
Collects and transports the debris (muck) generated by cutting, typically including crushers, screw conveyors, and slurry treatment equipment.
7. Auxiliary Systems:
Including ventilation, lighting, power supply, lubrication, and cooling systems to ensure the TBM's normal operation.
II. Working Principle of TBM
TBMs excavate tunnels by placing a large rotating cutterhead or cutting blades at the tunnel face, gradually advancing and excavating the tunnel. Simultaneously, the TBM continuously pushes forward, transporting excavated soil or rock from inside the tunnel to the surface.
Cutting Operation: After starting, the main drive system rotates the cutting head, crushing the rocks or soil ahead.
Propulsion: Pressure from the crushed rock propels the TBM forward, with the propulsion system automatically adjusting thrust to maintain a stable advance speed.
Support: As the TBM progresses, the support system immediately installs prefabricated tunnel lining segments or sprays concrete to stabilize the newly excavated tunnel section.
Measurement and Guidance: The measurement and guidance system monitors the TBM's position and direction in real-time, ensuring accurate excavation along the design route, with necessary adjustments as needed.
Muck Handling: Debris generated during excavation is collected and transported by the muck handling system to designated locations, sometimes requiring crushing and slurry treatment.
III. Applications of TBM
TBMs are widely used in railway tunnels, road tunnels, water conservancy and hydropower tunnels, urban rail transit, mining tunnels, and other projects.

What is a tunnel boring machine (TBM)? Let's take you into the world of TBMs to understand them
A tunnel boring machine is a mechanical device used for underground construction projects, specifically designed for efficient tunnel excavation. It works by breaking up rocks or soil with a rotating cutting head, thereby excavating the tunnel. A TBM mainly consists of three parts: the cutting head, the body, and the propulsion system. The cutting head is equipped with multiple cutting tools, such as disc cutters, breakers, and drill bits, used to directly break up rocks or soil. The body contains motors and hydraulic systems to provide power and control. The propulsion system is responsible for pushing the machine forward, which can be mechanical or hydraulic.
During the tunneling process, the TBM's cutting head rotates to cut through rocks or soil, and the debris is discharged outside the machine through a conveying system. Meanwhile, the propulsion system pushes the machine forward to continue the cutting operation. TBMs are also equipped with guidance and measurement systems for precise control of the tunnel alignment and dimensions.
Depending on the tunneling method, TBMs can be divided into various types such as open-type, shield-type, and hybrid-type. Open-type TBMs are suitable for hard rock tunneling, shield-type TBMs are suitable for soft soil and weak strata tunneling, while hybrid-type TBMs combine the advantages of both open-type and shield-type TBMs and can adapt to various complex geological conditions.
TBMs have a wide range of applications, including tunnel construction, mining, hydraulic engineering, urban rail transit construction, and more. With advancements in technology and engineering, modern TBMs are becoming increasingly advanced and have become indispensable equipment for tunnel and underground construction projects.
The design and scale of TBMs vary depending on specific engineering requirements. Some can be operated by personnel, while others use remote control or automation technology. These machines typically have strong excavation capabilities and can operate in various geological conditions.
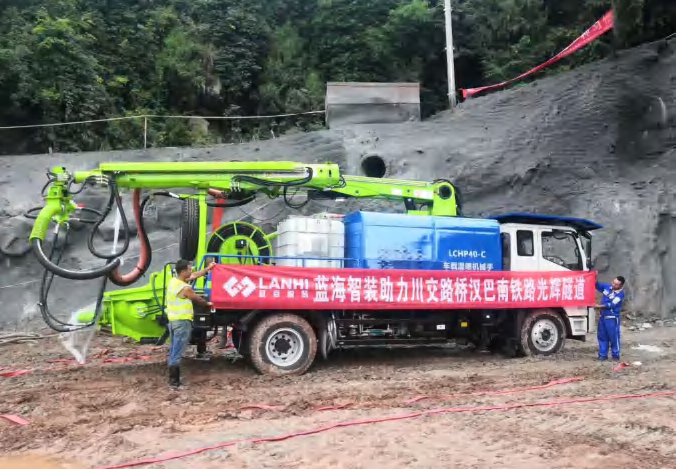
The Wet Spraying Robot Plays a Crucial Role in Tunnel Construction
Tunnel construction for highways and high-speed railways is a complex and challenging task involving many critical engineering aspects. Among these, the wet spraying robot plays an essential role and is considered an indispensable part of modern tunnel engineering.
Firstly, one of the crucial roles of the wet spraying robot in tunnel construction is wet concrete spraying. Concrete spraying is required to reinforce the walls and ceilings of the tunnel, and traditional manual construction methods often suffer from low efficiency. The introduction of wet spraying robots has completely changed this situation, as their efficient spraying capabilities enable rapid completion of construction, significantly shortening construction time and improving efficiency.
Secondly, wet spraying robots also play a key role in reinforcing support structures in tunnel construction. The support structure of the tunnel is an important component ensuring its stability and safety. Wet spraying robots can spray concrete onto support structures, forming sturdy concrete linings, thereby enhancing the tunnel's load-bearing capacity and stability.
Moreover, wet spraying robots also play an important role in waterproofing in tunnel construction. Groundwater leakage is a common problem in tunnel construction and can have a serious impact on tunnel structures. Wet spraying robots can spray waterproof materials such as waterproof concrete or coatings to effectively prevent groundwater leakage, protecting tunnel structures from water erosion and improving durability and reliability.
Finally, the intelligence and informatization of wet spraying robots bring new development opportunities for tunnel construction. With advances in technology, wet spraying robots can be linked with other smart devices and systems to achieve automated construction and remote monitoring, improving construction accuracy and controllability.
In summary, wet spraying robots play an extremely important role in tunnel construction. Through wet concrete spraying, reinforcement of support structures, waterproofing, and other methods, they enhance construction efficiency and quality, ensuring the safety and reliability of tunnel construction.
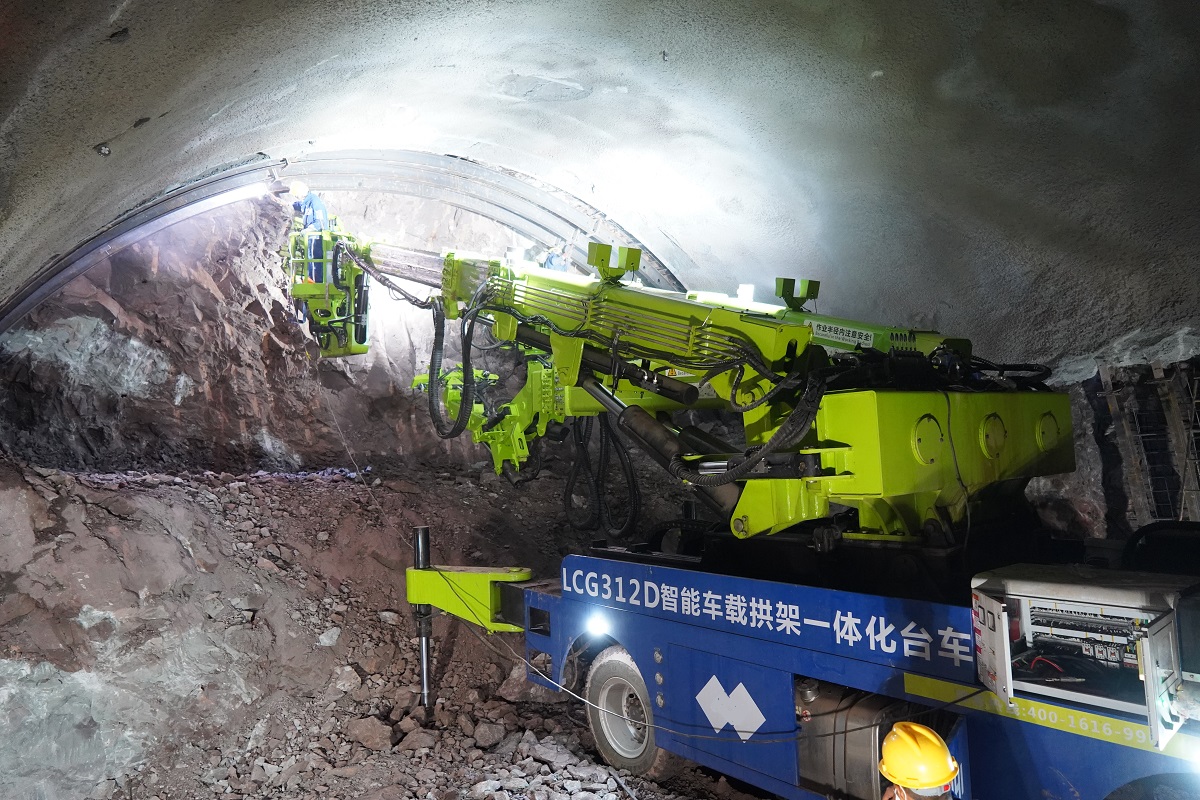
What should be considered during tunnel construction?
Safety is the primary concern in tunnel construction. Tunnels involve high-risk underground engineering activities, thus strict adherence to safety protocols is essential. This includes ensuring that all construction workers wear appropriate personal protective equipment (PPE) such as helmets, safety harnesses, dust masks, and protective eyewear. Additionally, regular safety education and skills training for construction personnel are necessary to keep them updated on the latest safety techniques and operating procedures, as well as how to respond correctly in emergency situations.
Before tunnel construction begins, a comprehensive risk assessment must be conducted to identify potential hazards such as collapses, water damage, fires, toxic gas leaks, etc., and corresponding preventive measures and emergency plans should be developed. Furthermore, ensuring that the temporary support systems for the tunnel comply with design specifications and are reinforced promptly according to geological conditions is crucial to prevent tunnel collapse. Establishing an effective ventilation system is also essential to control air quality inside the tunnel and ensure the safety of construction personnel.
Apart from safety management, geological surveying is also an indispensable aspect of tunnel construction. Prior to construction, thorough geological surveys are required to understand the geological conditions through which the tunnel will pass, including rock types, groundwater conditions, etc., in order to take appropriate construction measures. Designing the construction plan is equally critical, necessitating the development of rational construction plans based on geological conditions, tunnel usage, and other factors, including construction methods, support structures, drainage schemes, etc.
During construction, special attention must be paid to groundwater issues, and suitable drainage systems must be designed to prevent groundwater from entering the construction site, which could affect construction progress and quality. Additionally, selecting appropriate construction equipment and materials is crucial to ensuring construction quality and efficiency. For unique geological conditions, specialized equipment and materials need to be chosen.
Tunnel construction may have an impact on the surrounding environment, so measures should be taken to minimize the environmental impact of construction and protect the surrounding ecological environment. In conclusion, tunnel construction requires comprehensive consideration of factors such as safety, geology, construction plan design, drainage design, support structures, construction equipment and materials, as well as environmental protection, to ensure construction quality and safety.