
How to improve the service life of concrete spraying machine (can be started from 4 aspects)
As an indispensable and important tool in construction, the stability and durability of concrete spraying machine directly affect the quality of the project and construction efficiency. In order to ensure that the concrete spraying machine can operate efficiently for a long time, it is crucial to take a series of comprehensive measures. This article will explore effective ways to improve the service life of concrete spraying machine, from operating specifications to daily maintenance, to environmental adaptability considerations, to fully guarantee the health of the equipment.
Develop a scientific equipment maintenance plan
First, the operator needs to fully understand the equipment status and formulate a detailed maintenance plan for the spraying machine equipment. This includes regular inspections, preventive maintenance and necessary parts replacement. At the same time, any maintenance or procurement decisions should be strictly supervised to ensure that each operation can achieve the expected results and avoid unnecessary waste and delays.
2. Strengthen daily maintenance and maintenance
Daily maintenance is the basis for ensuring the normal operation of the spraying machine. In addition to routine cleaning, lubrication and tightening, a complete daily inspection mechanism should be established. The inspection content is not limited to past maintenance records and parts replacement history, but should also cover the actual use status and workload of the equipment. Through data analysis, potential problems can be discovered in advance, failures can be effectively prevented, and the safe and stable operation of the equipment can be guaranteed.
3. Improve the professional quality of operators
Strengthening the professional and technical training of operators and strictly abiding by safety operating procedures are key links in improving the life of the spraying machine. The implementation of the "two-fixed and three-guarantee" system (i.e. fixed personnel, fixed machines, guaranteed use, guaranteed storage, and guaranteed maintenance) helps to clarify responsibilities, ensure that each equipment has a dedicated person in charge, and reduce damage caused by human factors. In addition, combined with the concept of target cost management, linking the economic interests of operators with the maintenance of the equipment they use can stimulate the enthusiasm of employees and promote the refined management and maintenance of equipment.
4. Pay attention to the impact of environmental factors
It cannot be ignored that the harsh working environment has a significant impact on the service life of the concrete spraying machine. Given that the spraying machine often operates under variable and harsh conditions, its performance is easily restricted by factors such as temperature, humidity, and geology. Therefore, when designing and selecting the spraying machine, full consideration should be given to environmental adaptability, such as enhancing corrosion resistance and optimizing the heat dissipation system, so as to reduce the negative impact of external conditions on the function of the equipment.
In short, extending the service life of the concrete spraying machine cannot be achieved by the efforts of a single link, but involves a systematic project involving operation, maintenance, management and environmental adaptation. Only by taking comprehensive measures can the reliability and economic benefits of the equipment be truly improved, providing solid technical support for the smooth progress of the construction project.

Three key factors to improve the quality of wet spraying trolley shotcrete
In the field of modern tunnel and underground engineering construction, wet spraying trolleys are favored for their excellent operating flexibility, wide range of applications and significant improvement in work efficiency. However, to ensure the best quality of shotcrete, it is necessary to start from the professional ability of operators, the selection of mechanical equipment and the quality of raw materials. This article will explore these key factors in depth.
I. Cultivate a high-quality operation team
Responsibility awareness and skill level: The operator's sense of responsibility and technical proficiency directly affect the quality of shotcrete. Ideal staff should not only have a solid theoretical foundation, but also have rich practical experience.
II. Optimize high-performance wet spraying trolleys
The stable performance wet spraying manipulator can not only ensure high-quality spraying effects, but also greatly improve the efficiency of spray anchor work. Therefore, when purchasing, be sure to pay attention to the technical maturity and stability record of the product.
III. Strictly select high-quality raw materials
1. Standards for cement and aggregates: Use cement of no less than 42.5 grade, ensure that the particle size of coarse aggregate (such as crushed stone or pebbles) does not exceed 15mm, and the fineness modulus of fine aggregate (medium and coarse sand) exceeds 2.5, which are the basis for achieving high-quality concrete.
2. Scientific use of accelerator: Compatibility test of accelerator and cement, as well as solidification test of cement paste should be carried out, and the proportion of accelerator addition should be reasonably controlled at 3%-5% to achieve the best hardening speed and strength performance.
Improving the quality of wet spraying trolley sprayed concrete is not achieved by the efforts of a single link, but requires comprehensive measures from the quality of operators, equipment selection to raw material standards. Through the refined management of the above three dimensions, not only can the final quality of sprayed concrete be significantly improved, but also the overall construction efficiency and safety can be effectively improved, thereby promoting the smooth progress of the entire project.
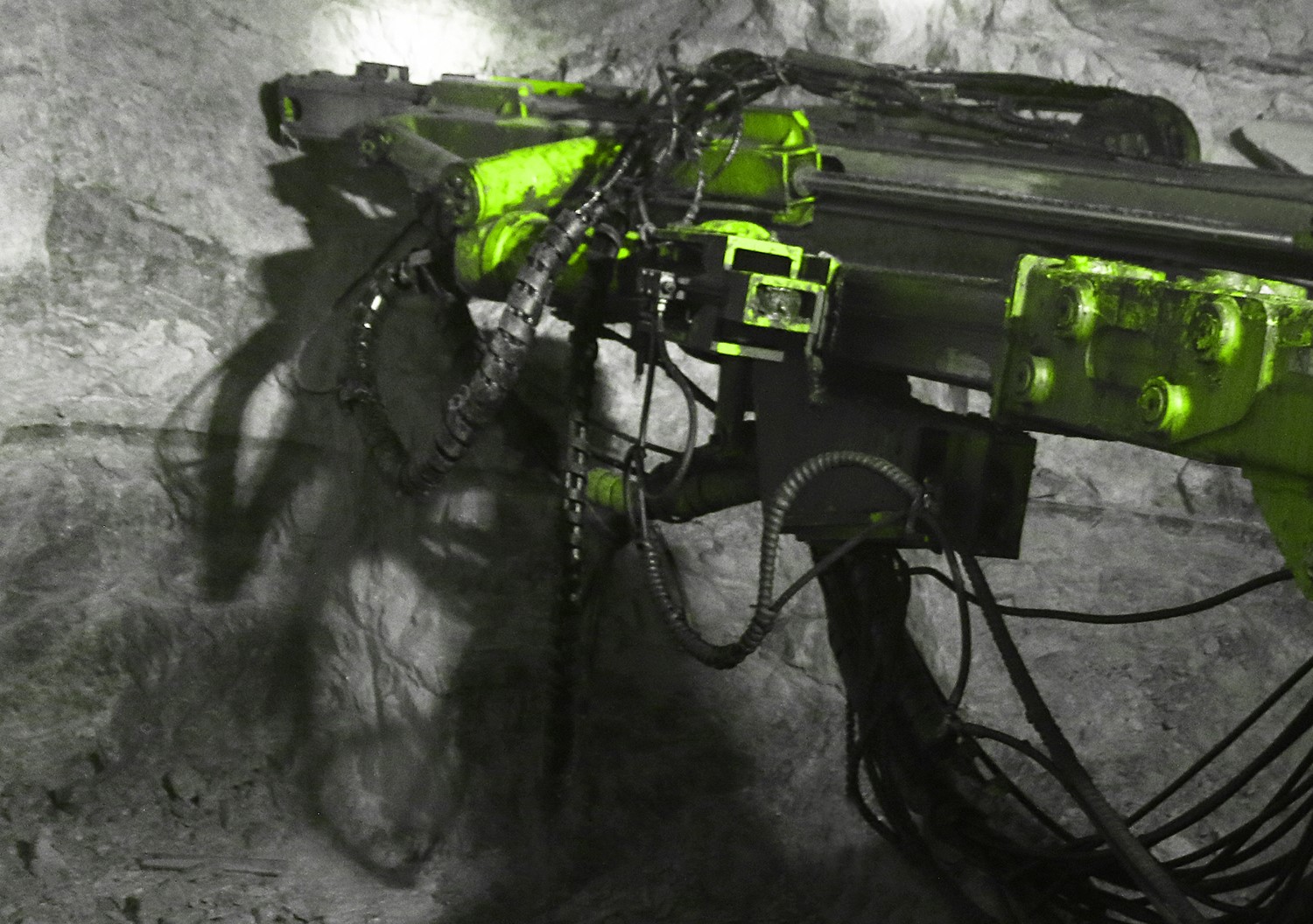
What are the common uses of rock drills in coal mining?
In the field of coal mining, rock drills are widely used, mainly including the following aspects:
1. Drilling operation: This is the most basic use of rock drills. In the process of coal mining, drilling operations need to be carried out first for subsequent blasting operations. Rock drills can quickly and accurately drill holes of the required depth and diameter, providing the necessary conditions for blasting.
2. Blasting operation: After the drilling is completed, blasting operations are required to break the coal seam. Rock drills can be used in conjunction with blasting equipment such as detonators and explosives for blasting operations. Through blasting operations, coal seams can be quickly broken, providing convenience for subsequent coal mining work.
3. Tunnel support: In the process of coal mining, in order to ensure the stability and safety of the tunnel, tunnel support work is required. Rock drills can be used in conjunction with other support equipment, such as anchor rods, anchor cables, etc., to carry out tunnel support work. Through support work, tunnels can be effectively reinforced to prevent accidents such as collapse.
4. Coal mining operations: In some coal mining methods, such as comprehensive mining, rock drills can directly participate in coal mining operations. Through the crushing action of the rock drill, the coal seam can be broken into small pieces, which is convenient for subsequent loading and transportation.
5. Other auxiliary operations: In addition to the above main uses, rock drills can also be used for other auxiliary operations, such as clearing obstacles in the roadway, drilling ventilation holes, etc. These operations help improve the working environment of coal mines and improve production efficiency.
Rock drills play an important role in coal mining and are one of the indispensable key tools for coal mining. With the continuous advancement of science and technology and the emergence of new materials, the performance and efficiency of rock drills will be further improved.
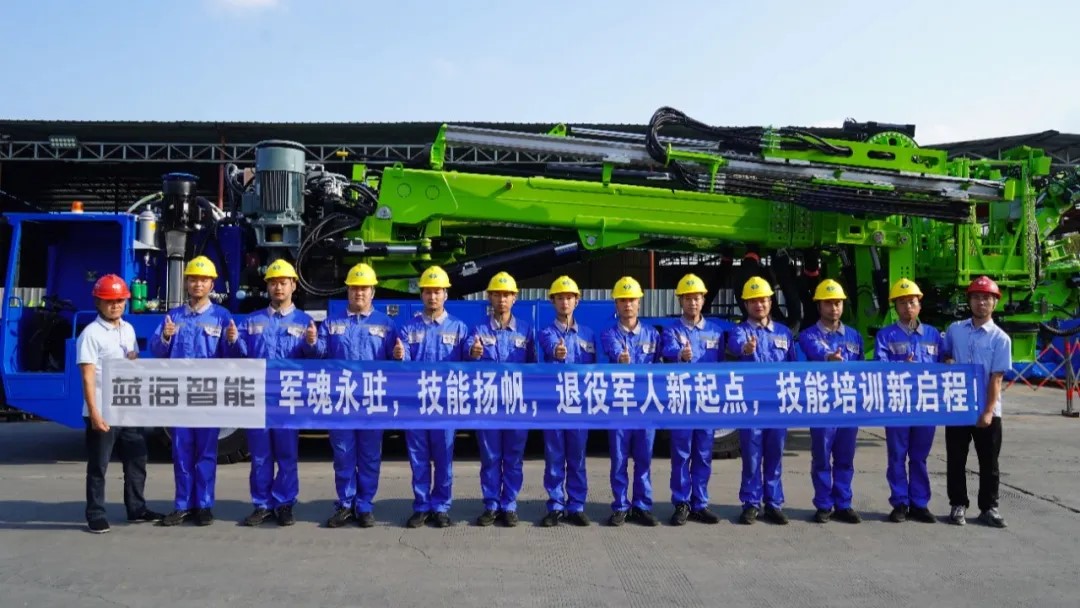
Skills sail | LANHI conducts induction training for a new batch of veterans in 2024
In order to standardize the induction training management of LANHI's new employees, optimize the employment adaptation of retired talents, and continue to create an entrepreneurial atmosphere of striving for excellence and striving for excellence, LANHI recently launched a 7-day pre-job skills training for a new batch of retired soldiers. Lan Bing, general manager of the company, Tang Jie, deputy director of the research institute, and others attended the training symposium and had cordial exchanges with 11 retired soldiers on the spot.
Leadership empowerment
At the meeting, General Manager Lan Bing extended a warm welcome to all the newly recruited retired soldiers, hoping that they would always maintain their military qualities, promote first-class style and embody first-class standards, bravely take on the responsibility, familiarize themselves with the business as soon as possible, actively integrate into the company, and open up new work situations; in new jobs, they should work hard and overcome difficulties, and truly achieve "retirement without fading, retirement without retreating", showing the style of outstanding retired soldiers in the new era.
Tang Jie, deputy director of the research institute, who also joined LANHI for 10 years as a retired soldier, combined his own work experience to explain the job prospects of joining LANHI to his comrades. Tang Jie said that the qualities of perseverance and courage tempered in the army will be a valuable asset for comrades in their careers. He hopes that comrades will continue to carry forward the glorious tradition of being particularly able to endure hardships, fight and dedicate themselves, and successfully complete the transformation from soldiers to corporate people; at the same time, the company also provides everyone with a higher starting point. I hope everyone will cherish the opportunity, continue to grow and improve, and move their lives to a higher level.
Pre-job training
LANHI arranged a 7-day induction training for the retired soldiers who reported this time, covering 6 professional fields including after-sales, maintenance, machine operation, production, warehouse management, and safety and environmental protection. It focuses on company systems and business practices, supplemented by comprehensive quality training such as company corporate culture, professional theory, safety knowledge, professional skills of various positions, and military training.
The trainees did not forget their military qualities. With full enthusiasm and perseverance, they actively engaged in the practical learning of a series of intelligent equipment such as intelligent arch frame/anchor trolleys, rock drilling trolleys, and wet spraying manipulators, achieving both theoretical and technical improvement, laying a solid foundation for subsequent entry into front-line positions.
Win-win future
Retired soldiers are a valuable asset of the Party and the country. LANHI is committed to training retired soldiers into the new era of new quality productivity, which is a strong support for the employment and resettlement of retired soldiers in the country, and an effective relief for the current shortage of intelligent manufacturing talents, injecting fresh vitality into the replacement of old and new industrial workers.
In the future, the company will take multiple measures to attract more retired soldiers to join the company, help retired soldiers to set posts and plan career paths, and introduce a series of preferential measures in training and promotion, so that retired soldiers can shine on the broad stage of LANHI and become a reliable force to promote the company's high-quality development. We also wish the newly recruited retired soldiers to forge ahead, live up to their youth, and write the most beautiful chapter of life in LANHI Intelligence!

Preparation work before using the wet spraying trolley, and matters needing attention during use
As an efficient tunnel support and slope reinforcement equipment, the wet spraying trolley plays an indispensable role in modern engineering construction. In order to ensure the quality and safety of construction, operators must follow a set of rigorous standard processes, from equipment inspection to specific operation, and then to subsequent maintenance, each link is crucial. The following is a complete set of guidelines based on industry practical experience, which aims to help operators master the various skills of the wet spraying trolley, improve work efficiency and ensure site safety.
I. Preparation work before operation
Qualification review: All operators must receive professional pre-job training and pass the assessment, and have the corresponding operation qualification certificate.
Material verification: Before starting, carefully check whether there are foreign objects in the hopper, confirm that the water tank has sufficient water storage and the water quality is clean, and avoid impurities entering the pipeline to cause failures.
System detection:
Verify whether the wind pressure and voltage parameters are in the normal range to ensure that all indicators of the machine meet the standards.
Adjust the tension of the tie rod, confirm the correct direction of the rotor, check the status of the vibration motor, metering pump and quick-setting agent pipeline, and ensure that all key components operate normally.
Establish a clear communication protocol and agree on a unified gesture language signal with the sprayer in advance to facilitate real-time communication and coordination.
II. Precautions during construction
Site selection: Ensure that the wet spraying trolley is parked flat and solid, and the tires are all in contact with the ground to provide stable support.
Electrical safety: If an external power supply is required, be sure to check the integrity of the line after power is turned off to avoid the risk of electric shock. The cable should be laid away from the water source, and it is better to hang it in the air.
Real-time monitoring: Pay close attention to the changes in wind pressure during the operation, keep in close contact with the sprayer, and adjust the air volume and quick-setting agent dosage in time according to the on-site feedback to ensure the quality of spraying.
Emergency response: If the pipeline is blocked, stop the high-pressure air immediately, and carefully disassemble the relevant components to prevent the residual gas from being released suddenly and causing harm.
Stop work treatment: After the spraying task is completed, use high-pressure air to blow the spray pipe and quick-setting agent pipeline to completely empty the residual materials. If the interval is long, a water washing procedure is also required to avoid material solidification and blockage.
III. Shutdown and cleaning steps
When the wet spraying trolley stops spraying, the spray pipe and the quick-setting agent pipeline should be thoroughly cleaned with high-pressure air to avoid residue blockage. If the interval between two sprayings exceeds half an hour, the wet spraying machine, spray pipe and quick-setting agent pipeline must be thoroughly cleaned with water to prevent equipment damage or affect the next operation.
Through the above detailed operating guidelines, not only can the accident rate of wet spraying trolleys at the construction site be greatly reduced, but also the service life of mechanical equipment can be effectively extended, which will escort the smooth implementation of the project.

Types and application fields of concrete spraying machines
Through its efficient spraying function, concrete spraying machines can quickly form a solid concrete layer, thereby improving construction efficiency, improving the construction environment, and helping to save materials and reduce labor intensity. Let's take a look at the types and application fields of concrete spraying machines.
I. Classification of concrete spraying machines
According to the working principle, concrete spraying machines can be divided into three types: dry spraying, wet spraying and semi-dry spraying.
1. Dry spraying concrete spraying machine
Dry spraying equipment mixes dry aggregate, cement and water and directly feeds them into the nozzle for spraying. This method is suitable for construction occasions where the spraying quality requirements are not high. The advantages are simple equipment structure and convenient operation and maintenance, but there is more dust during the spraying process and the working environment is poor.
2. Wet spraying concrete spraying machine
Wet spraying equipment first mixes cement, water and aggregate into wet concrete materials in a mixer truck or mixing station, and then transports them to the nozzle through a pipeline for spraying. This method can effectively control the moisture content, improve the spraying quality and work efficiency, reduce dust, and improve the safety and comfort of the construction environment.
3. Semi-dry spraying concrete spraying machine
Semi-dry spraying equipment is between dry spraying and wet spraying. It adds part of the water to the aggregate for pre-wetting treatment, and then sends it into the nozzle for spraying. This method takes into account the advantages of dry spraying and wet spraying, which can not only improve the spraying quality, but also reduce the complexity of the equipment and the difficulty of operation.
II. Application fields of concrete spraying machine
Concrete spraying machine is widely used in many fields due to its high efficiency and flexibility:
1. Mine support: By spraying concrete, the stability and safety of mine tunnels are improved.
2. Tunnel engineering: quickly form a solid tunnel wall and improve construction efficiency.
3. Roads and bridges: In the construction and maintenance of roads and bridges, it is used to spray protective layers and repair damaged parts.
4. Water conservancy projects: used for the reinforcement and repair of water conservancy facilities, such as dams and levees.
5.Construction engineering: plays an important role in the reinforcement, decoration and protection of buildings.
As an efficient construction equipment, concrete spraying machine plays an indispensable role in modern engineering construction. By reasonably selecting and using concrete spraying machines, the quality of the project and construction efficiency can be significantly improved.
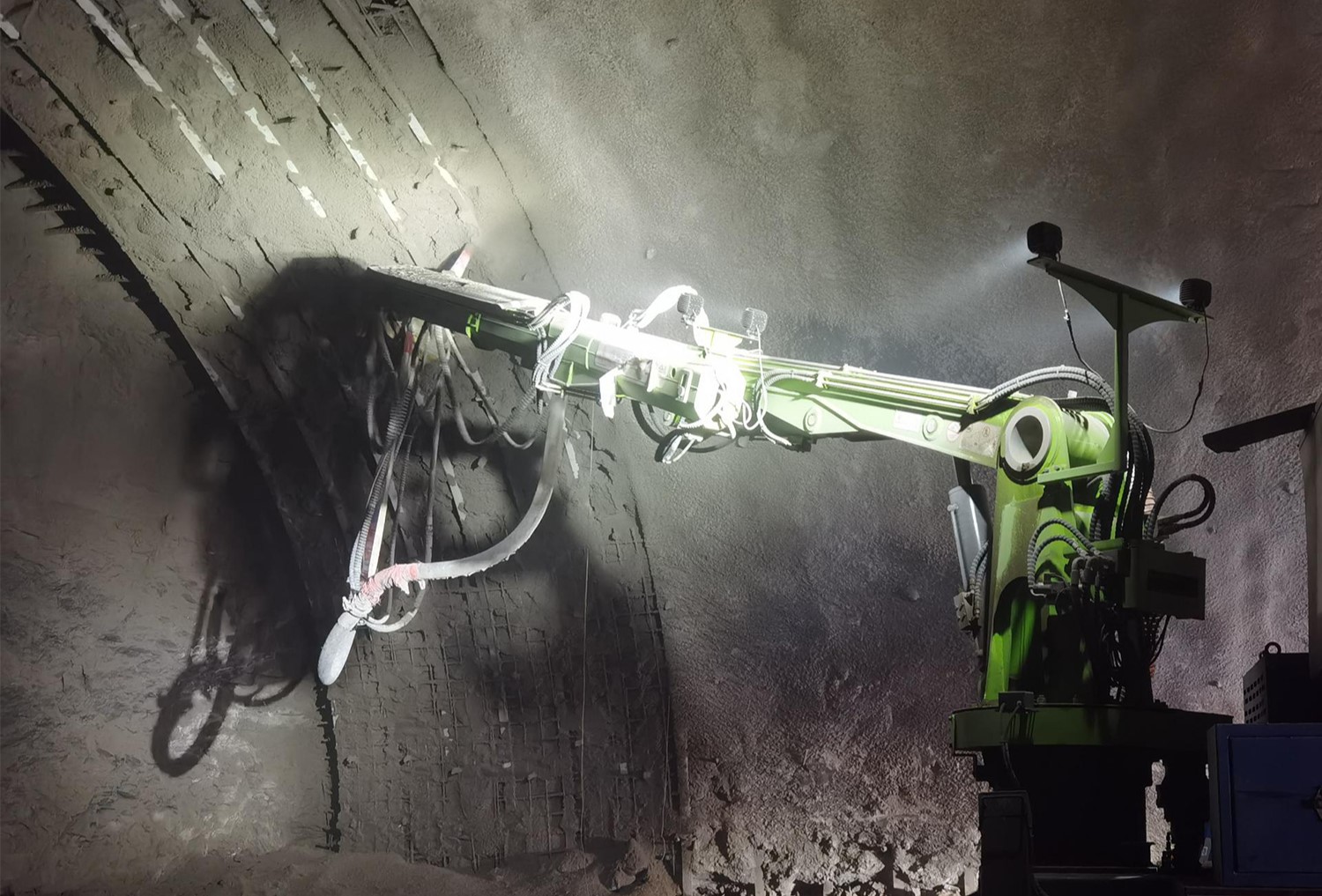
An efficient strategy to reduce the concrete rebound rate during the construction process of concrete wet spraying manipulator
As an efficient means of underground engineering construction, wet spraying technology of concrete is widely used in tunnel construction. However, how to effectively reduce the rebound rate of concrete and improve the quality and economy of operation has always been the focus of the industry. This article will explore how to effectively control the rebound of concrete by combining refined management with operating skills.
1. Strict quality control of raw material selection
All raw materials used for wet spraying must be strictly tested to ensure that they meet engineering standards. In particular, key additives such as accelerators must be properly stored to avoid performance degradation due to moisture, which affects the quality of the final concrete.
2. Accurately control the proportion and mixing
Water-cement ratio control
It is crucial to accurately adjust the water-cement ratio in the concrete mixture. Too high or too low a water-cement ratio will result in poor fluidity or insufficient strength of the concrete, thereby increasing the risk of rebound. Therefore, the construction team needs to regularly check and adjust the injection amount of the accelerator to ensure the stability of the mixture.
Monitoring slump
Before spraying, the slump (fluidity index) of concrete should be between 140 and 180 mm. This range can better balance the fluidity of the material and the density after molding, which helps to reduce the occurrence of rebound.
3. construction operation skills
Distance and angle control
During spraying, the optimal distance and angle between the nozzle and the sprayed surface are the key factors affecting the rebound rate. It is generally recommended to keep an appropriate distance between the nozzle and the working surface, and the spraying direction is as perpendicular to the sprayed surface as possible (about 90°), so as to obtain the maximum compaction effect and the lowest rebound loss.
Circular movement strategy
Use continuous and slow horizontal circular movement to spray, each circle covers half of the area of ??the previous circle, forming a "one circle presses half a circle" mode. This uniform distribution method can effectively reduce gaps and enhance structural stability.
When encountering a situation where a steel frame or steel mesh is covered, moderately adjust the spray angle to no less than 70°, which can avoid obstacles and maintain a good spraying effect.
4. Monitor rebound rate and adjust
During construction, the actual rebound rate of concrete should be monitored in real time and construction parameters should be adjusted in time. The target rebound rate is set as: no more than 15% for the side wall and less than 25% for the arch. Once the exceeding standard is found, the cause should be analyzed immediately and corresponding measures should be taken to correct it.
The implementation of the above comprehensive measures can not only significantly reduce the rebound loss in concrete wet spraying operations, but also improve the safety, efficiency and final project quality of the entire construction process. This requires construction units to achieve fine management and professional operation in every link from raw material preparation to on-site execution, so as to promote the industry to develop in a more environmentally friendly and economical direction.
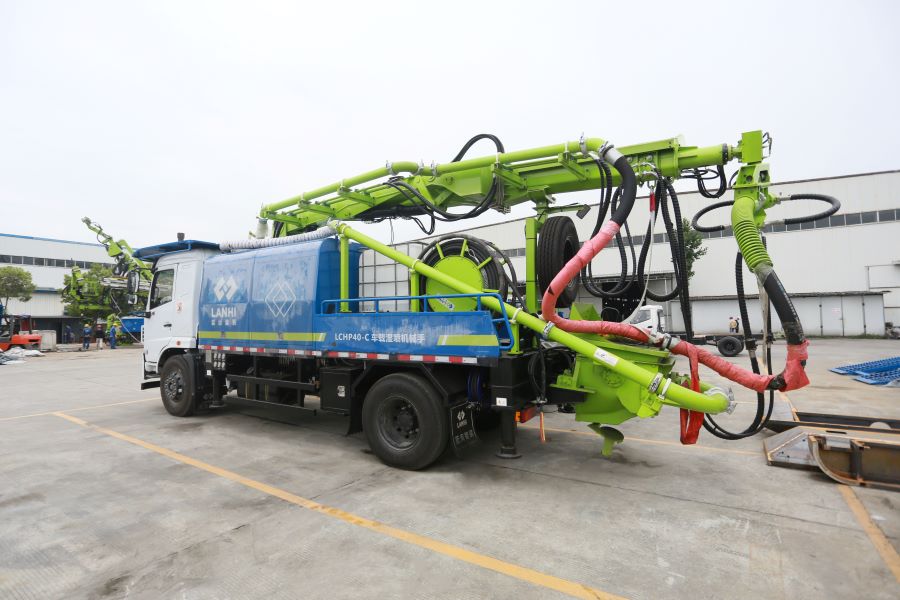
Some important matters needing attention when using the wet spraying robot
Wet spraying manipulators are widely used in concrete construction, but there are many precautions that need to be strictly followed in actual operation to ensure the construction quality and mechanical life. The following are some important points that should be paid attention to during the use of wet spraying manipulators.
1. Equipment lubrication and cleaning
Before spraying concrete, the wet spraying machine and feed pipe should be lubricated with mortar. Lubrication can not only effectively reduce resistance, but also extend the service life of the equipment. After the spraying work is completed, the pipeline must be cleaned with water in time to avoid the residual concrete solidification and clogging the equipment, which is essential to maintain the normal operation of the equipment.
2. Water-cement ratio control
During the construction process, strict control of the water-cement ratio is the key to ensuring the quality of sprayed concrete. The best state of concrete should form a layer of dark and weak luster on its surface. Improper control of the water-cement ratio may lead to insufficient strength or excessive flow of concrete, affecting the quality of the project.
3. Seepage section treatment
When treating the seepage section, if the amount of water is small, it can be blown by high-pressure wind first, and then concrete can be sprayed according to the conventional construction procedure; if the amount of seepage is large, a blind pipe should be buried close to the rock surface and gradually approach the seepage point from a distance. At the same time, the dosage of the accelerator is temporarily increased, but it should be controlled within 6%. This operation can help the concrete to solidify gradually, thereby effectively blocking the water seepage area.
4. Equipment blockage treatment
Once the pipeline is blocked, the machine must be stopped immediately and the gas source must be turned off, and then the pipeline must be checked and cleared in time. Avoid construction interruption due to blockage problems and affect the progress of the project.
5. Post-spraying inspection
After each concrete spraying, a full inspection should be carried out before the next blasting. Usually, the time interval between spraying and blasting should be no less than 4 hours. After blasting, it is necessary to check whether there are cracks on the concrete surface. If there are cracks, the blasting time should be adjusted or the blasting parameters should be changed.
6. Material and accelerator management
Before construction, the quality of the raw materials used should be ensured to be qualified, especially the management of accelerators. Accelerators should be properly stored to avoid moisture failure and affect the construction effect. At the same time, the water-cement ratio of the mixture should be strictly controlled to ensure that the slump of the concrete is between 140 and 180 mm.
7. Operational specifications during spraying
During the spraying process, attention should be paid to the rebound rate and actual mix ratio of concrete. The rebound rate of the concrete side wall should not exceed 15%, and the arch should not exceed 25%. In addition, the sprayer needs to maintain the distance and angle between the nozzle and the sprayed surface during operation to ensure the best compaction effect. The angle between the nozzle and the sprayed surface should be kept as close to 90 degrees as possible, so as to obtain the minimum rebound and maximum compaction effect. When the spraying surface is covered with a steel frame or steel mesh, the nozzle can be slightly tilted, but the angle should not be less than 70 degrees.
Wet spraying manipulators play an important role in projects such as tunnels and mines, but the accuracy of their operation and the maintenance of equipment directly affect construction efficiency and safety. Therefore, when using wet spraying robots, strictly abiding by operating specifications and strengthening equipment maintenance and construction management are the key to ensuring project quality and safety.
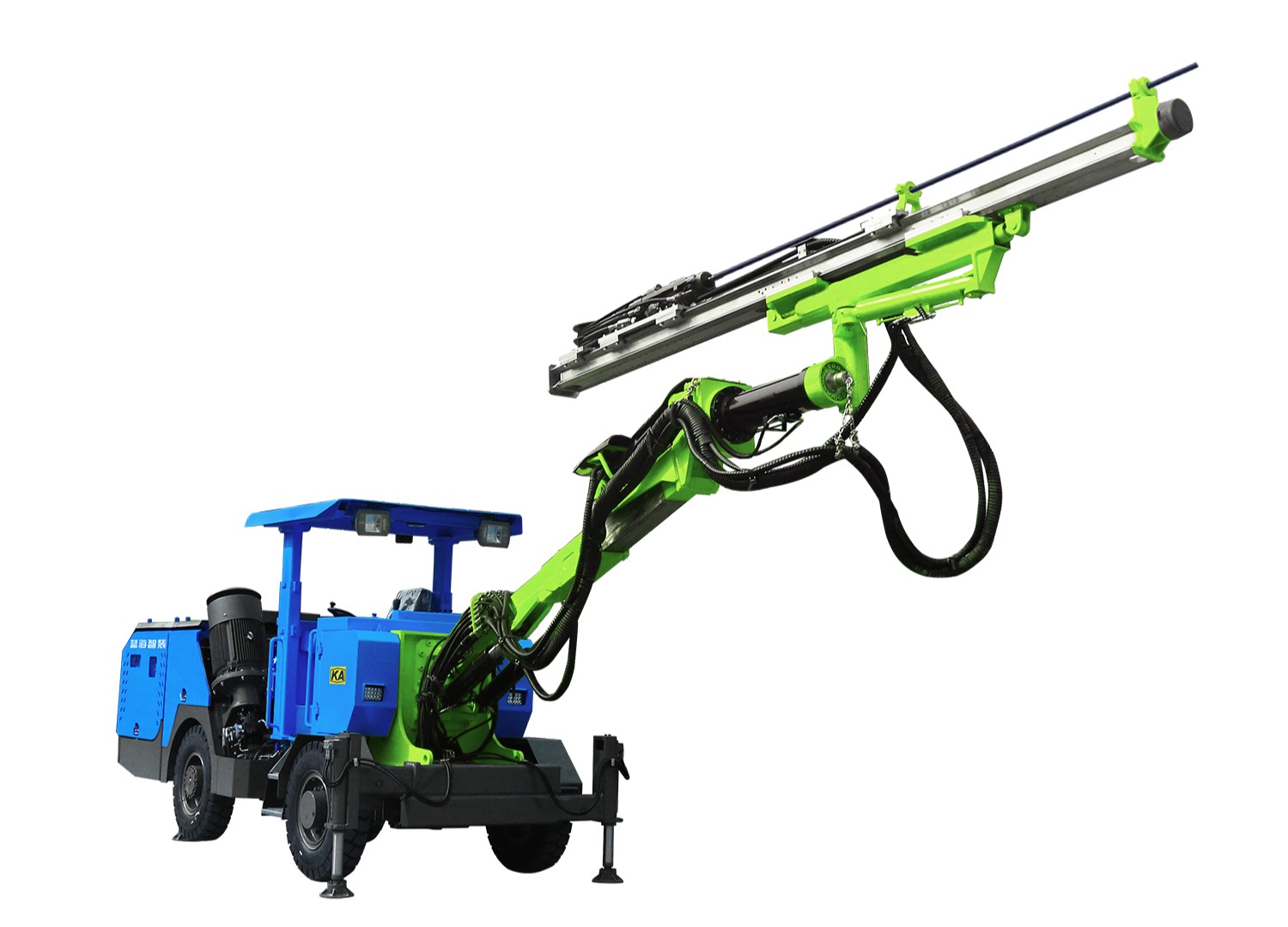
Application and Advantages of Full-Face Tunneling Machines in Coal Mines
With the continuous development of coal mining technology, the use of full-face tunneling machines in mine tunnel construction has become increasingly widespread. As a piece of equipment specifically designed for coal mine rock tunnel projects, the full-face tunneling machine is leading a technological transformation in coal mine tunnel construction, thanks to its efficient and stable performance.
Design and Functionality of the Full-Face Tunneling Machine for Coal Mines
The full-face tunneling machine is a high-tech device used in coal mine tunnel construction. Its design is tailored to handle relatively intact, self-supporting surrounding rock, and it performs exceptionally well in hard rock layers with a rock hardness coefficient greater than f7. This equipment enables full-section excavation of tunnels without relying on traditional roadheaders or the drill-and-blast method.
Enhancement of Construction Efficiency
Compared to traditional methods, the full-face tunneling machine significantly improves construction efficiency. Under the same construction conditions, its efficiency can increase by 4 to 6 times. This remarkable improvement is mainly due to its fully mechanized operation, which reduces manual intervention and auxiliary processes, making the construction process smoother and more efficient.
Driving Technological Transformation
The application of full-face tunneling machines not only boosts construction efficiency but also advances the full mechanization of coal mine tunnel construction. Compared to traditional methods, this equipment offers a safer and more environmentally friendly construction process, reducing the impact of human factors on construction quality. Additionally, its high efficiency allows coal mine tunnel construction to be completed in a shorter timeframe, lowering project costs and increasing economic benefits.
As an innovative piece of equipment for coal mine tunnel construction, the full-face tunneling machine is promoting the progress of tunneling technology with its outstanding performance and significant efficiency gains. With the ongoing promotion and application of this technology, coal mine tunnel construction is entering a new era, achieving higher efficiency, greater safety, and more environmentally friendly construction goals.
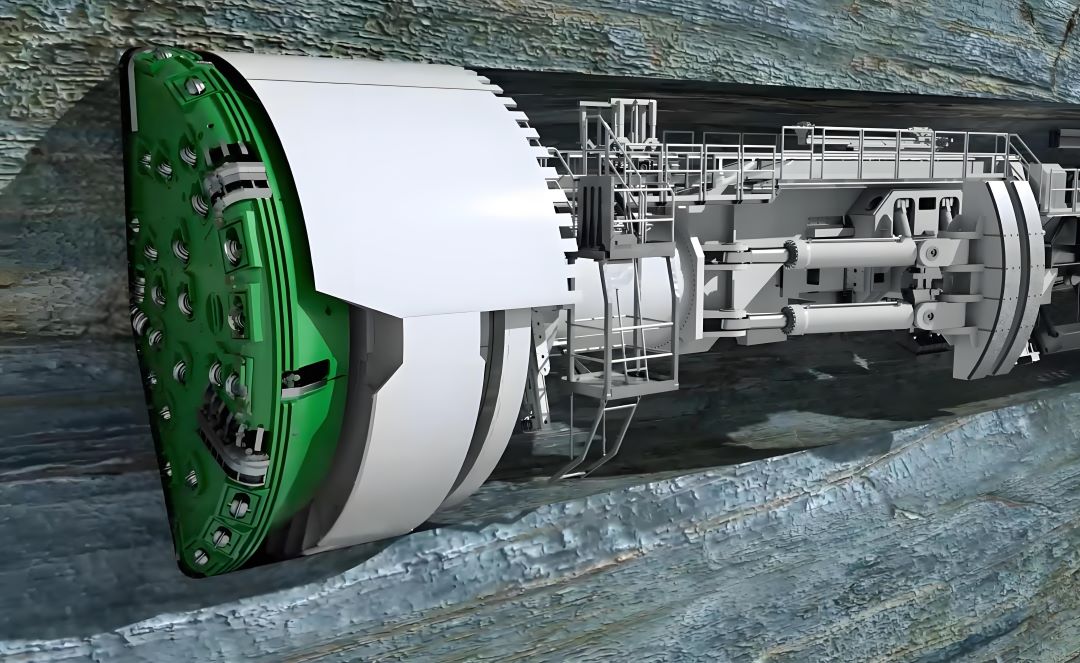
4 different classification methods of full-section tunnel boring machines
As a key equipment in modern tunnel construction, the flexibility of design and application of TBM has greatly improved the efficiency and safety of tunnel construction. The diversified classification of TBM reflects its ability to adapt to different geological conditions and engineering needs. This paper will discuss the classification of TBM from four aspects: cutterhead shape, excavation section shape, working rock hardness and relationship with the tunnel wall, in order to provide reference for engineering design and construction.
1. Different classifications according to cutterhead shape
The cutterhead shape of TBM is an important dimension in its classification. Flat cutterhead TBM is the most common type at present, suitable for a variety of geological conditions, with simple design and flexible operation. Spherical cutterhead TBM and conical cutterhead TBM respectively improve the cutting efficiency and stability in specific geological environments through their unique geometric shapes. These cutterhead designs of different shapes enable TBM to operate efficiently in rocks of different hardness, ensuring the continuity and safety of tunnel excavation.
2. Different classifications according to excavation section shape
The shape of the excavation section directly affects the structural design and construction cost of the tunnel. The circular cross-section full-section TBM is the most widely used type at present. Its advantage is that it can form a stable circular cross-section, which is convenient for subsequent lining operations and is also conducive to groundwater management. The non-circular cross-section full-section TBM can meet the needs of special projects. For example, the rectangular cross-section is suitable for the development of urban underground space, which can make more effective use of underground space and reduce the impact on ground buildings.
3. Different classifications according to the hardness of the operating rock
According to the hardness of the operating rock, TBM is divided into soft rock, medium hard rock and hard rock full-section TBM. Soft rock full-section TBM is suitable for geological environments with a uniaxial compressive strength of less than 100MPa, medium hard rock full-section TBM is suitable for rocks with a uniaxial compressive strength of less than 150MPa, and hard rock full-section TBM can cope with rock hardness up to 350MPa, reflecting the adaptability and flexibility of TBM under different geological conditions.
4. Classification by the relationship between the full-face TBM and the tunnel wall
Open full-face TBM and shield full-face TBM are the two main classifications. When the open full-face TBM is operating, there is no additional protective structure between the TBM and the tunnel wall, which is suitable for relatively stable geological conditions. The shield full-face TBM protects the TBM and construction personnel by setting up a shield. It is suitable for complex and unstable geological conditions. It is further subdivided into single-shield, double-shield and triple-shield full-face TBMs to meet the needs of different projects.
Full-face TBMs can be classified in various ways, and each classification reflects its application advantages in a specific engineering environment. By reasonably selecting and applying different types of TBMs, the efficiency of tunnel construction can be effectively improved and construction risks can be reduced. It is an indispensable and important tool in modern tunnel engineering. With the continuous advancement of technology, the design and application of TBMs will become more diversified, bringing more possibilities for tunnel construction.