
What are the common forms of tunnel support? Introduction to several common forms of tunnel support
What are the common forms of tunnel support? Common forms of tunnel support mainly include the following:
1. Shotcrete Support: Concrete is sprayed onto the tunnel wall under high pressure to form a solid protective layer. Shotcrete can quickly cover the surface of the surrounding rock, close rock cracks, prevent weathering and water erosion, and increase the overall stability of the surrounding rock. It can be used as temporary support or permanent support.
2. Steel Arch Support: A frame structure made of steel or steel grid is installed inside the tunnel to provide support for the surrounding rock. Steel Arch Support can be used alone or in combination with shotcrete to form a more solid composite support system.
3. Rock Bolting or Cable Anchoring: By drilling holes in the surrounding rock, inserting high-strength steel bars or steel strands, and pouring and fixing with materials such as cement slurry, the stress inside the surrounding rock is transferred to the deep stable rock mass, thereby improving the self-bearing capacity of the surrounding rock.
4. Lining Support: After the tunnel is excavated, a permanent structure made of concrete or other materials is poured to withstand the ground pressure and water pressure for a long time to ensure the stability and durability of the tunnel. The lining can be cast-in-place concrete or prefabricated concrete segments or masonry structures.
5. Prefabricated Support: Use prefabricated concrete slabs, arch blocks and other components to assemble in the tunnel to form a support structure. This method is suitable for tunnel projects with better conditions and can speed up the construction progress.
6. Grillage Support: A grille-like structure welded from steel bars or steel bars, usually used in combination with shotcrete to form a lightweight support system, suitable for the initial support of weak surrounding rock.
7. Soil Nailing: Drill holes in the soil or soft rock, then insert steel bars or steel pipes, and grout them to make them tightly bonded with the surrounding soil, forming an effect similar to that of anchor rods, enhancing the overall stability of the soil.
8. Freezing Method: In special circumstances, such as crossing an aquifer or soft stratum, the stratum can be artificially frozen to temporarily harden it, facilitating tunnel excavation and support.
9. Grouting Reinforcement: It is a commonly used auxiliary support method to inject cement slurry or other chemical slurry into the surrounding rock to fill cracks and improve the density and bearing capacity of the surrounding rock.
These support forms can be used alone or in combination according to specific engineering needs and geological conditions to achieve the best support effect.
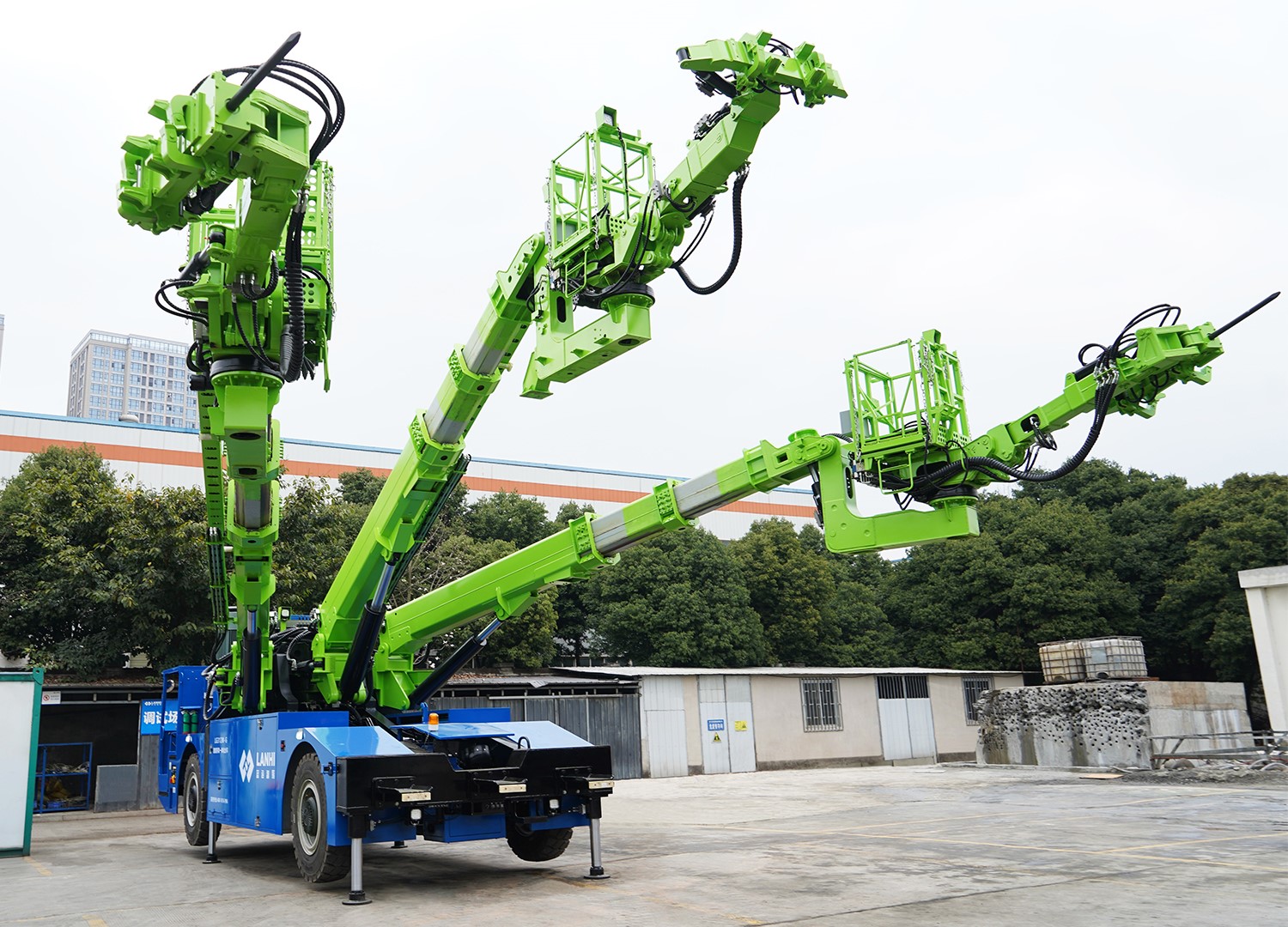
What are the advantages of the three-arm arch installation trolley in tunnel construction?
In the infrastructure industry, the three-arm arch installation trolley is an important construction equipment. It is widely used in the construction of large-span, high-rise or complex structures. With its unique structural design and efficient working performance, this equipment provides construction workers with a convenient and safe working environment. The three-arm arch installation trolley has many advantages in tunnel construction, including:
High efficiency: The three-arm arch installation trolley can realize fast and continuous arch installation operations, significantly reducing manual operation time and improving construction efficiency.
High precision: The trolley adopts an advanced control system to ensure that the installation position and angle of the arch are accurate, thereby ensuring the structural quality of the tunnel.
Safety: The design of the trolley takes into account the complex environment of the construction site and is equipped with necessary safety protection measures to reduce safety accidents during the construction process.
Strong adaptability: The three-arm arch installation trolley can be adjusted according to the construction needs of tunnels of different diameters and lengths, and has good adaptability.
Save human resources: Due to the high degree of automation of the trolley, it can reduce the labor demand at the construction site and reduce labor intensity.
Cost reduction: Although the initial investment is relatively large, the overall construction cost can be reduced in the long run due to improved construction efficiency and reduced accident losses.
Environmental protection and energy saving: reducing noise and dust pollution during the construction process, which is beneficial to protecting the environment.
Easy maintenance: The trolley has a reasonable structural design, which facilitates daily maintenance and troubleshooting.
Improve construction quality: Through precise control, construction quality problems caused by human factors can be reduced and the overall project quality can be improved.
Flexibility: When encountering complex geological conditions, the trolley can flexibly adjust the construction strategy to ensure construction progress.
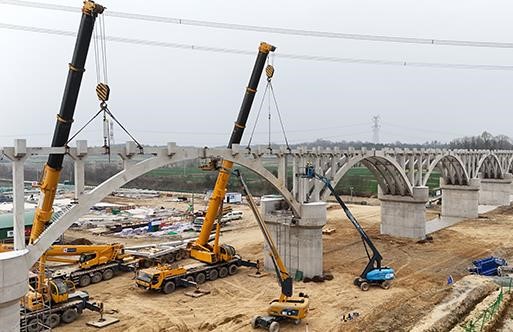
What does an arch mean? What is the length of an arch frame in meters?
What does an arch mean? "A frame" in "an arch frame" is pronounced as "p ǐ n" and is a quantifier, usually referring to a frame composed of arches and supporting structures, used to describe the structural framework of a house or building.
In construction engineering, arches are a common structural form that consists of arches and columns or walls that support the arches. Arches can be used in structures such as bridges, tunnels, and roofs to withstand large loads and provide stable support.
The specific shape and size of an arch may vary depending on design requirements and usage scenarios. It can be a simple arched structure or a complex framework composed of multiple arches and supports. During the construction process, it is necessary to accurately manufacture and install the arch according to the design drawings and construction process requirements to ensure the stability and safety of its structure.
What is the length of an arch frame in meters?
The length of an arch varies depending on its specific purpose and design requirements, usually ranging from a few meters to several tens of meters. For example, the single prefabricated arch of the 1 # aqueduct of the Taisu Canal in the Hualiangting Irrigation District is about 16 meters long, the wooden arch of the cloud dome has a span of 45-120 meters, and the arch of the GTC roof structure has a span of 45-120 meters.

Performance and advantages of Lanhi LJMYT-315 crushing anchor digging and protecting machine
Lanhi LJMYT-315 crushing anchor excavation and anchor protection machine is an innovative equipment that integrates crushing, excavation and loading functions. It is especially suitable for the construction of hard rock excavation anchors with medium and large cross-sections from 4.5m x 4.5m to 6m x 6m. , widely used in the mining industry. The design of this equipment fully considers the needs of compact structure, convenient operation and work efficiency, and shows a number of significant performance features and advantages.
Structure and design
The anchoring mechanisms of LJMYT-315 are placed on both sides of the fuselage, ensuring the compactness of the equipment while providing a broad operating field of view. The anchor system has fast drilling speed, high anchor and anchor anchor operation efficiency, and the drilling process has good stability. The equipment can advance 3 to 5 meters per shift, and the construction efficiency is high.
Energy Saving and Cost Effectiveness
Compared with traditional open-pit excavators, LJMYT-315 has the advantage of low power consumption, and the cost of use is about 800 yuan per meter. In addition, anchor protection and excavation are interlocked, and the airborne temporary support system effectively protects the safety of workers and reduces construction risks.
Multifunctional and efficient operation
Multiple airborne anchor drilling rigs have the ability to work with multiple degrees of freedom. They can complete all anchor drilling operations in the tunnel without moving equipment, replacing manual drilling operations and significantly reducing the number of workers and labor intensity. At the same time, the equipment has a slag removal function to achieve rapid discharging of ore. In terms of operation mode, it supports local and remote control dual driving, further improving construction safety and working environment.
Workers and efficiency
The excavation operation of LJMYT-315 is completed by 2 people/shift, and the bolt support is completed by 4 people/shift. Compared with traditional methods, labor costs are significantly saved. The non-explosive excavation function of the equipment takes into account the various excavation needs of hard rock and soft rock through its own breaker/high-frequency hammer. The excavation efficiency of hard rock can reach 25m?/h, and the excavation efficiency of soft rock is even higher.
Equipment maintenance and replacement
The equipment's breaker hammer model is 230, which can achieve 120MPa rock crushing and excavation performance. The breaking hammer and the high-frequency hammer can be quickly replaced (the hammer replacement is realized through the movement of the boom and the vehicle body tooling, and can be completed within half an hour by two people without any lifting equipment), which greatly improves the maintenance and operation efficiency of the equipment.
Lanhi LJMYT-315 crushing anchor excavation and protection integrated machine provides an integrated solution for the excavation and anchor construction in the mining industry with its characteristics of high efficiency, safety, energy saving and multi-function. Welcome to consult our company for more information Device details.

How to judge the quality of a second-hand concrete spraying robot? Methods for evaluating the condition of second-hand concrete spraying robot equipment
How to judge the quality of a second-hand concrete spraying robot? Judging the quality of a second-hand concrete spraying robot requires a comprehensive inspection and evaluation. The following is a method for evaluating the condition of second-hand concrete spraying robot equipment.
1. Appearance inspection:
- Carefully observe the overall appearance of the equipment to check whether there are obvious deformations, cracks, rust or paint peeling.
- Check whether the welding parts are firm and whether there are signs of cracking.
2. Mechanical parts inspection:
- Check the flexibility and wear of moving parts such as telescopic arms, joints, and slewing mechanisms, and observe whether there are jams, abnormal noises or looseness.
- Check the wear and tension of chains and belts.
3. Hydraulic system inspection:
- Check whether there is oil leakage in the hydraulic pipeline and whether the joints are loose.
- Start the equipment and observe whether the pressure of the hydraulic system is stable and the movement is smooth when it is working.
4. Electrical system inspection:
- Check the insulation of wires and cables for damage and aging.
- Test whether various electrical components, controllers and sensors are working properly.
5. Spray system inspection:
- Check the wear of the nozzles and whether they are blocked.
- Check the wear and blockage of the concrete delivery pipeline.
6. Operation test:
- Perform actual operation to test the functions of the equipment, including the speed, accuracy and coordination of various actions.
- Check whether the control system responds sensitively.
7. Working hours and usage records:
- Check the working hours record of the equipment to understand its usage intensity.
- Request the repair, maintenance and fault records of the equipment to understand its historical maintenance.
8. Engine inspection (if any):
- Check the engine's starting performance, whether it runs smoothly, and whether there is abnormal noise and smoke.
- Check the level and quality of the engine oil and coolant.
9. Chassis and travel system inspection:
- Check the structural integrity of the chassis for deformation or damage.
- Test the driving performance, braking effect and steering flexibility of the walking system.
10. Professional inspection:
- If conditions permit, you can ask a professional equipment inspection agency to conduct a comprehensive inspection and evaluation.
Through the above steps, you can have a more accurate judgment on the quality of the second-hand concrete spraying robot. Remember, it is very important to conduct a thorough inspection and test before purchase to ensure that the robot can operate stably and reliably in future work.

What is the New Austrian Tunnel Construction Method? Characteristics of the New Austrian Tunnel Construction Method and Three Excavation Methods
A brief explanation of the New Austrian Tunnel Construction Method and the New Austrian Tunnel Construction Method. The concept of the New Austrian Tunnel Construction Method was proposed by Austrian scholar Professor Rabsiweiss in the 1950s. It is a construction method based on tunnel engineering experience and rock mechanics theory, combining anchors and shotcrete as the main support means. The New Austrian Tunnel Construction Method is generally divided into the following excavation methods according to the wind block conditions of the section and the order of excavation: first, full-section excavation method, second, step method, and third, partial excavation method.
The New Austrian Tunneling Method and the New Austrian Tunnel Construction Method (NATM) are a construction method based on tunnel engineering experience and rock mechanics theory. This concept was proposed by Austrian scholar Professor Rabsiweiss in the 1950s. NATM mainly supports through the combination of anchors and shotcrete, controls the deformation and relaxation of the surrounding rock, makes the surrounding rock an integral part of the support system, and guides the methods and principles of tunnel engineering design and construction through the measurement and monitoring of the surrounding rock and support.
1. The main features of the New Austrian Tunneling Method include:
1. Give full play to the self-bearing capacity of the surrounding rock and minimize the disturbance to the surrounding rock.
2. Carry out initial support in time so that the surrounding rock and support can bear the load together.
3. Implement measurement and monitoring, and adjust the support parameters and construction methods according to the feedback of measurement data.
2. New Austrian Tunneling Method Excavation Method
1. According to the different conditions of the tunnel section and the construction sequence, NATM can be divided into the following main excavation methods:
2. Full-section excavation method: It is suitable for tunnel sections with good surrounding rock stability. The entire section is excavated at one time. The construction speed is fast, but it requires higher surrounding rock conditions.
3. Step method: Divide the tunnel section into two parts, the upper half is excavated first, and then the lower half is excavated. This method is suitable for medium surrounding rock conditions and is conducive to controlling surrounding rock deformation.
4. Partial excavation method: Divide the tunnel section into several parts, and excavate and support them step by step. It is suitable for situations with poor surrounding rock conditions and can better control surrounding rock deformation and construction risks.
III. Advantages of the New Austrian Tunneling Method
The New Austrian Tunneling Method is widely used in various tunnel projects due to its flexibility and strong adaptability. Its main advantages include:
1. Improve the utilization rate of surrounding rock: By rationally utilizing the self-bearing capacity of the surrounding rock, the dependence on the support structure is reduced, thereby saving construction costs.
2. High construction safety: Through real-time monitoring and timely adjustment of construction methods, the surrounding rock deformation can be effectively controlled and construction risks can be reduced.
3. Strong adaptability: According to different surrounding rock conditions and tunnel sections, appropriate excavation methods can be selected to flexibly respond to various complex construction environments.
This construction method has the advantages of flexible construction, strong adaptability, and economic efficiency, and has been widely used in tunnel projects.

Shotcrete robot improves the quality and efficiency of spraying and improves the working environment of workers
The shotcrete manipulator is a specially designed and manufactured device that replaces the traditional manual spraying method, can reduce the labor intensity of shotcrete operations and improve working conditions. The equipment consists of an operating arm, a nozzle and other parts. The operating arm is usually equipped with telescopic, lifting, rotating and flipping mechanisms, and is operated by hydraulic or mechanical transmission. Some shotcrete manipulators are also equipped with independent walking mechanisms to achieve full mechanization of the shotcrete operation, thereby improving the quality and efficiency of the shotcrete and improving the working environment of the workers.
Composition and working principle of shotcrete manipulator
Concrete shotcrete manipulators mainly include walking system, control system, hydraulic system, power system, concrete pumping system, lubrication system and working device. Its working principle is to transport cement, aggregate, water and admixtures mixed evenly according to the construction ratio to the spraying site through a concrete transport tanker and add them to the sprayer. The sprayer pumps the concrete to the nozzle, mixes it with the quick-setting agent controlled by the computer's fully automatic ratio, and then sprays it with high-pressure air.
Structure and function of shotcrete manipulator
Concrete shotcrete manipulators consist of an upper working device and a lower chassis. The lower chassis is equipped with motors, hydraulic oil tanks, optical cable coils, control rooms, water tanks, oil tanks, hydraulic pipelines, quick-setting agent boxes, hoppers and other devices. The general manipulator has eight degrees of freedom, including waist rotation, arm pitch, arm pitch, arm telescopic, horizontal arm telescopic, horizontal arm swing, wrist rotation and gun bar posture adjustment, to ensure that the spray gun is perpendicular to the sprayed surface and maintains the best distance. According to needs, the working device can be installed on different chassis.
Characteristics of different types of shotcrete manipulators
In actual applications, different types of concrete spraying manipulators have their own characteristics. For example, a large-scale shotcrete manipulator can spray up to 30 to 40 cubic meters per hour, significantly improving the construction progress. The wet spraying process is used to make the concrete more adherent, more uniform and dense, and ensure the construction quality. Only 2 to 3 main operators are required, with a high degree of mechanization, which significantly improves the construction efficiency. The operation range is large, suitable for large-area construction, and has a wide range of applications. It can effectively control the rebound rate and quality of the spraying, and the spraying effect is good. Mechanized operation is far away from the face, with high safety and little impact on the surrounding environment and construction personnel.
Application of shotcrete manipulator
Concrete shotcrete manipulator is widely used in shotcrete support construction in transportation tunnels, hydraulic tunnels, mine tunnels, underground projects and building foundation pits. Research on it is also constantly improving at home and abroad, mainly focusing on structural updates, new admixtures and shotcrete development, material research, miniaturization and multifunctionality, improving the degree of automation, long-distance concrete transportation, and intelligent and self-checking function research.

Which industries use concrete spraying robots? Which are suitable for concrete spraying operations?
Concrete spraying manipulators are widely used in many industries due to their high efficiency and flexibility, especially in situations where large-scale concrete spraying operations are required. The following are some of the main industries that use concrete spraying manipulators:
1. Transportation tunnel construction industry: including railway tunnels, highway tunnels, etc., used for concrete spraying support on the inner wall of the tunnel to enhance the stability and safety of the tunnel structure.
2. Hydraulic tunnel construction industry: In the construction of tunnels in water conservancy projects, concrete spraying is used to reinforce the tunnel wall.
3. Mining industry: such as coal mines, metal mines, etc., tunnel support and reinforcement operations will be used.
4. Underground engineering field: such as the construction of underground parking lots, underground pipe galleries, etc.
5. Building foundation pit support industry: concrete spraying on the side walls of the foundation pit to prevent soil collapse.
The application of concrete spraying manipulators is not limited to the above industries. With the advancement of technology and the diversification of market demand, its application field is still expanding. Because of its ability to provide high-quality concrete structures while reducing manual labor intensity, the role of concrete spraying robots will become increasingly important in the future construction and engineering fields.

How to solve the problem of unstable spraying effect of wet spraying manipulator?
How to solve the problem of unstable spraying effect of wet spraying manipulator? To solve the problem of unstable spraying effect of wet spraying manipulator, the following measures can be taken:
1. Check equipment settings:
Make sure that all settings of the wet spraying manipulator, including water-cement ratio, spraying pressure, nozzle size, etc., are properly adjusted to meet the design specifications.
Recalibrate the equipment to ensure that all sensors and control systems work properly without errors.
2. Optimize the mixing system:
Check and clean the mixing system of the wet spraying machine, including the mixing barrel, pump and pipeline, to ensure that there is no blockage or wear that affects the quality and delivery of the mixture.
3. Replace worn parts:
Check and replace worn nozzles, seals and other consumables, the wear of which may cause unstable spraying effect.
4. Adjust spraying parameters:
Adjust the spraying pressure, flow rate and angle according to the actual situation on site to obtain a more stable spraying effect.
Try different water-cement ratios to find the mixing ratio that best suits the current construction conditions.
5. Improve operating skills:
Provide operating training to ensure that operators understand how to properly use and maintain the wet spraying manipulator.
Guide operators on how to adjust equipment settings according to construction conditions to adapt to different construction environments.
6. Control environmental factors:
Minimize wind speed and temperature changes at the construction site, which may affect the wet spraying effect.
When necessary, adjust the construction plan to avoid wet spraying operations under extreme weather conditions.
7. Regular maintenance and inspection:
Establish a regular maintenance plan, including daily inspection and regular maintenance of the wet spraying manipulator to prevent potential failures.
Record maintenance and troubleshooting to track problems and take preventive measures.
8. Use high-quality materials:
Ensure that standard concrete materials are used. High-quality materials help improve the stability of the spraying effect.
9. Consult manufacturer technical support:
If the problem persists, contact the manufacturer of the wet spraying manipulator for professional technical support and solutions.
The above measures can effectively solve the problem of unstable spraying effect of the wet spraying manipulator and improve construction quality and efficiency. During the implementation process, the spraying effect should be continuously monitored and the strategy should be adjusted according to actual conditions.
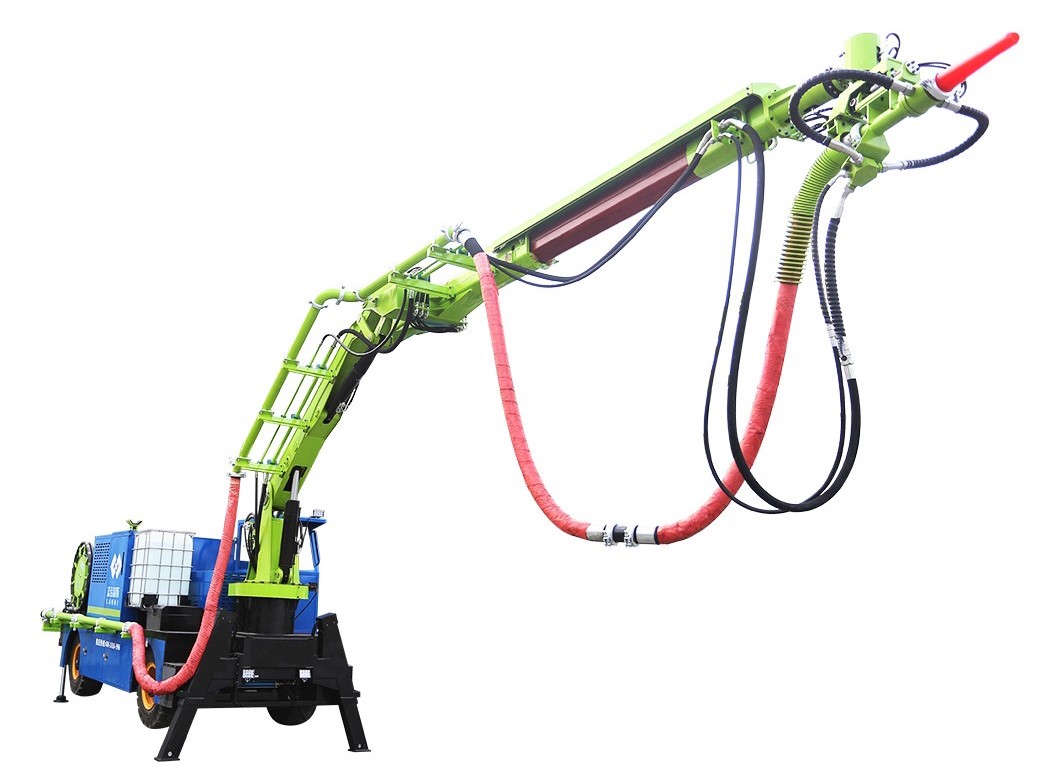
The outstanding performance of LANHI concrete wet spraying trolley is gradually becoming the main equipment in tunnel construction
LANHI concrete wet spraying trolley is a highly intelligent concrete wet spraying equipment, which is widely used in tunnel construction. Its main features include high mechanization, high work efficiency, low springback, high construction safety and a good working environment. These characteristics make the equipment perform well in tunnel construction and significantly speed up the overall construction progress.
Features of LANHI concrete wet spray trolley
1. Efficient construction
The theoretical spraying displacement of LANHI concrete wet spraying trolley can reach 40 cubic meters per hour. This efficient spraying capability greatly improves construction efficiency and enables tunnel construction to progress rapidly. Compared with the traditional manual spraying method, mechanized operation is not only fast, but also has stable quality.
2. Safety and environmental protection
In the initial support operation of long tunnels, the wet spray trolley demonstrated its unique advantages. First of all, mechanized construction reduces the dangers of manual operations and improves construction safety. Secondly, wet spraying technology can effectively reduce dust and noise during the concrete spraying process, improving the working environment at the construction site.
3. Low rebound amount
Another significant advantage of wet concrete spray trucks is their low springback. This means less concrete is wasted during the blasting process, resulting in material cost savings. In addition, low springback reduces the amount of cleaning work required after spraying and improves overall construction efficiency.
4. Intelligent trend
With the continuous improvement of construction efficiency and quality requirements for tunnel projects, the application of intelligent mechanical equipment has become an inevitable trend. The application of Blue Ocean Smart Concrete Wet Spraying Trolley not only improves the construction quality, but also promotes the development of mechanized construction of tunnel projects. In the future, intelligent wet shotcrete equipment will play an increasingly important role in tunnel construction and become an ideal choice for concrete shotcrete anchor support.
LANHI concrete wet spray trolley is gradually becoming the main equipment in tunnel construction due to its high efficiency, safety and environmental protection. With the continuous advancement of technology and the promotion of application, mechanized wet spraying operations will play an increasingly important role in engineering support, pushing tunnel construction into a new intelligent era.