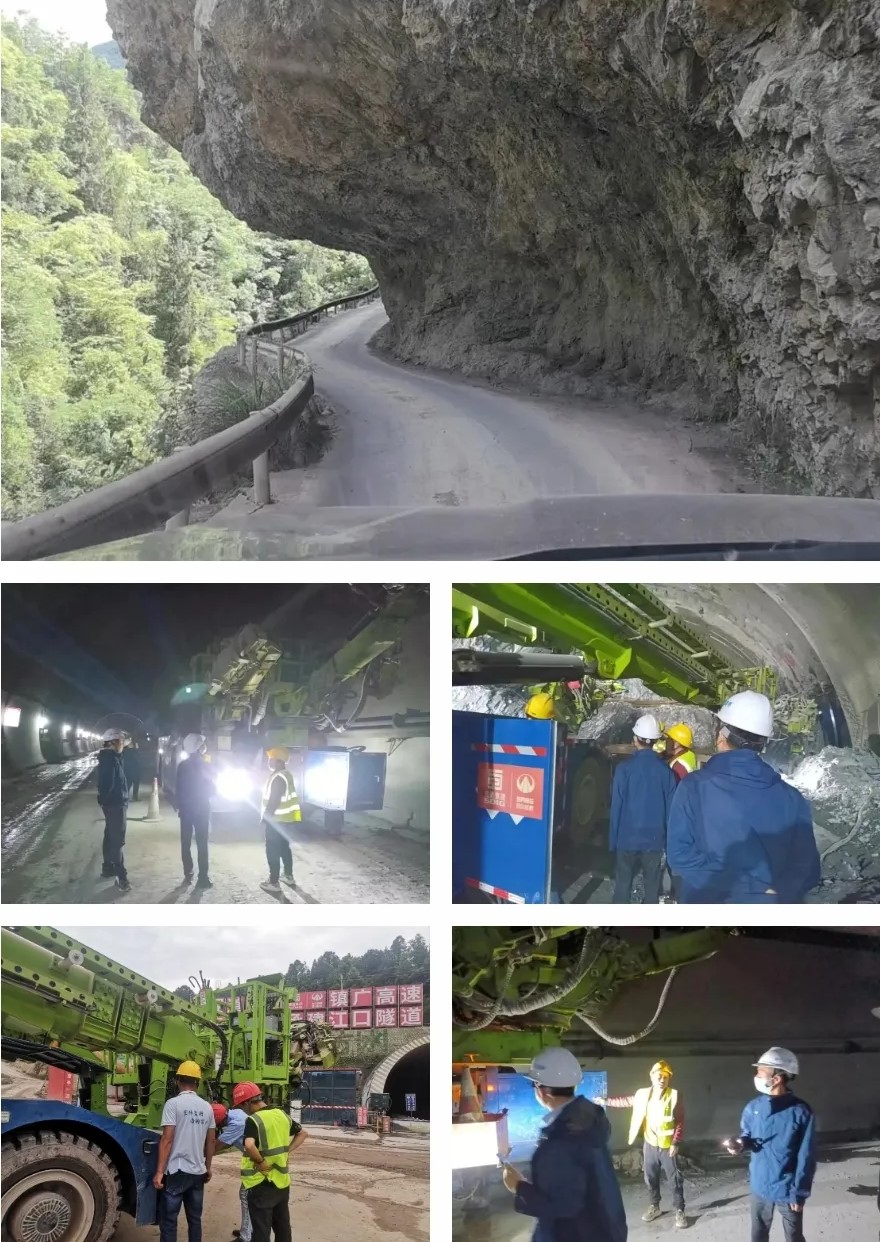
Speak with service! Focus on the highlights of LANHI's after-sales inspection!
LANHI2024 "Crossing Mountains and Rivers, Service Accompanying, Satisfied Companion" inspection service has been in full swing for half a month. There is such a group of unknown heroes who leave their warm families and run around in various remote construction sites day and night, not afraid of rugged mountain roads and harsh environments, and provide strong guarantees for the stable operation of customers' equipment.
They are LANHI's service engineers.
Build bridges in communication, find problems in inspections, solve problems in repairs, optimize equipment in maintenance, and improve work efficiency in training. Faced with complex and urgent work tasks, they are not afraid of difficulties, face them head-on, and solve them in time, using professionalism and enthusiasm to escort customers' equipment.
On the construction site with dust and yellow mud, in the complex environment surrounded by mountains and gullies, they are busy with their heads down, focused and determined. They create value with communication, demonstrate skills with efficiency, win recognition with dedication, and win trust with sincerity. Providing customers with full support after-sales service has also won LANHI the respect and trust of customers.
After-sales service is a long journey, and service is on the front line. LANHI's service engineers go all out and persevere. They work day and night, in the wind and rain, and they are down-to-earth and forge ahead.

Two types of tunnel boring machines classified by the shape of the machine head
The tunnel boring machine is a special mechanical equipment used for underground projects such as tunnel construction and mining. According to the different shapes of the tunnel boring machine head, the tunnel boring machine is mainly divided into arm-type tunnel boring machine and cutter-type tunnel boring machine. These two types of tunnel boring machines have their own characteristics in structure, function and applicable scenarios.
1. Arm-type tunnel boring machine
The head shape of the arm-type tunnel boring machine is like a long arm, usually composed of a multi-degree-of-freedom mechanical arm and a cutting tool. This design gives the arm-type tunnel boring machine the following characteristics:
High flexibility: The arm-type tunnel boring machine can adapt to different working surfaces by adjusting the angle and position of the mechanical arm, so it performs well in tunneling operations with complex and irregular shapes.
High operating accuracy: The multi-degree-of-freedom design of the mechanical arm enables it to accurately control the motion trajectory of the cutting tool, which is suitable for engineering projects that require precise excavation.
Wide scope of application: The arm-type tunnel boring machine is suitable for tunnel excavation in underground mines such as coal mines and metal mines, as well as tunnel projects with complex geological conditions.
However, the structure of the boom-type TBM is relatively complex, the maintenance cost is high, and the efficiency is relatively low when excavating large-section tunnels.
2. Cutterhead TBM
The head of the cutterhead TBM is shaped like a disc, on which a large number of cutting tools are installed. Its main features are as follows:
High excavation efficiency: The cutterhead TBM continuously cuts rocks or soil layers by rotating the cutterhead, which is suitable for long-distance and large-section tunnel excavation projects.
Good stability: The cutterhead TBM has high stability during the excavation process and can cope with high-strength and high-hardness geological conditions.
High degree of automation: Modern cutterhead TBMs are equipped with advanced control systems and sensors, which can realize automated operation and improve the safety and efficiency of excavation.
However, the cutterhead TBM has poor flexibility when facing irregular terrain and complex geological conditions, and the initial investment is high. It is mainly used in tunnels and underground projects with relatively stable geological conditions.
Boom-type TBMs and cutterhead TBMs each have unique advantages and applicable scenarios. With its flexibility and high operating precision, the boom-type TBM is suitable for underground projects with complex shapes and variable geological conditions; the cutterhead TBM is widely used in large-section tunnels and engineering projects with relatively stable geological conditions due to its high efficiency, stability and high degree of automation.
Diversity and selection of TBMs
With the continuous growth of demand for underground engineering and mining, the technology of TBMs is also constantly improving. To choose the appropriate type of TBM, it is necessary to comprehensively consider the specific needs of the project, geological conditions and economic costs. By rationally selecting and using TBMs, it is possible to effectively improve the efficiency of tunneling, reduce construction risks and promote the development of underground engineering.
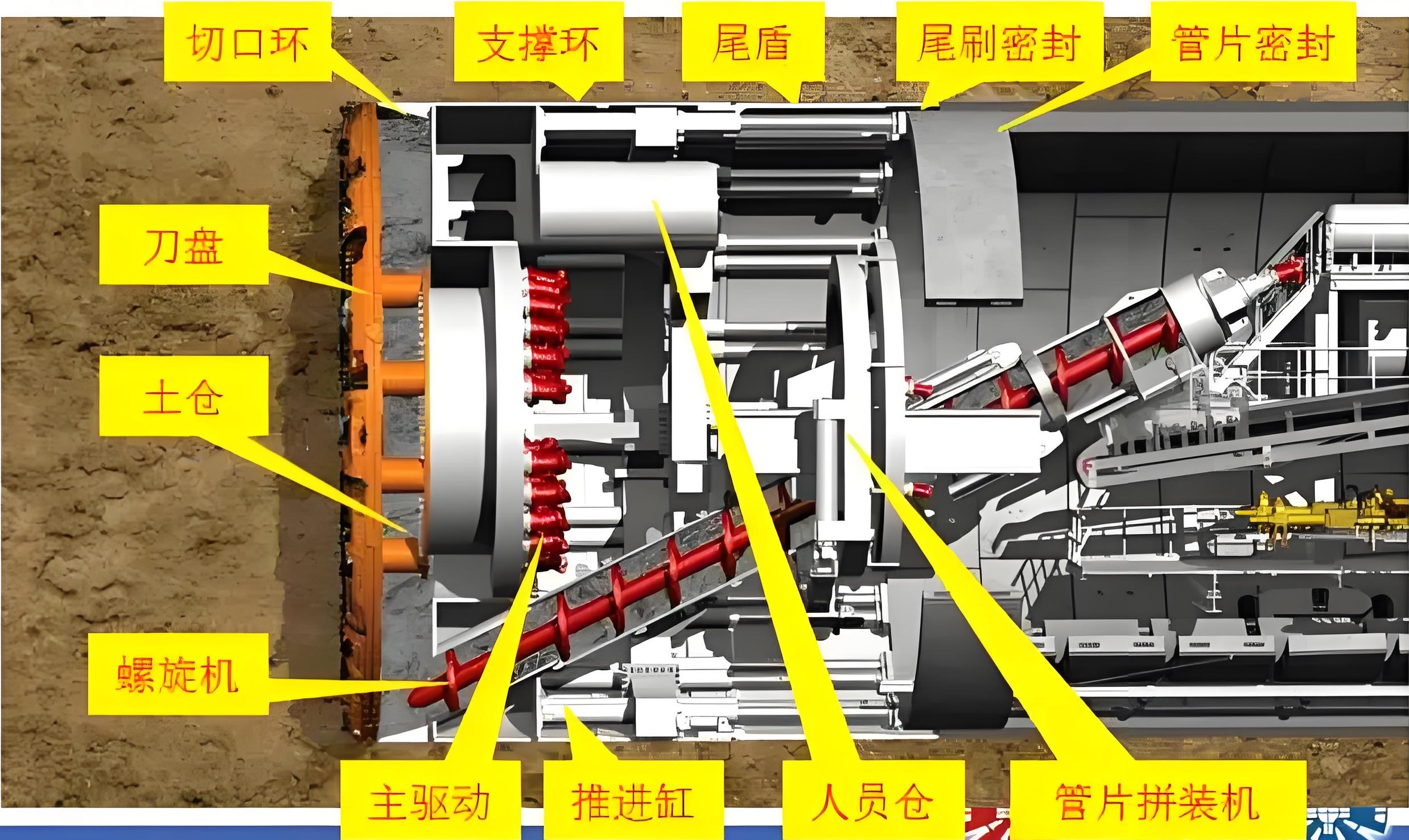
What is the general structure of a shield machine? The four major structural components of a shield machine
A shield machine is a heavy mechanical equipment widely used in tunnel construction. Its complex structure and efficient working principle make it an important tool in modern engineering. A shield machine consists of four main parts: a shield shell, a propulsion system, an excavation system, and an assembly system.
Shield shell
The shield shell is the external structure of the shield machine, which is mainly composed of a cutout ring, a support ring, horizontal and vertical partitions, and a shell steel plate. In the initial stage of engineering construction, the foundation pit needs to be excavated first, and the shield machine needs to be installed at the designated location and debugged. The shield shell not only provides structural support for the entire equipment, but also plays a protective role during the construction process to ensure the safety of the internal machinery and operators.
Propulsion system
The propulsion system is the power source for the shield machine to move forward, and is mainly composed of shield jacks and hydraulic equipment. These jacks are distributed in a circular shape along the support ring, and push the shield machine forward by applying pressure to the segments. The efficient operation of hydraulic equipment enables the shield machine to move forward steadily under various geological conditions, ensuring the continuity and safety of tunnel construction.
Excavation system
The excavation system is responsible for transporting the excavated soil and rock out of the tunnel. The cutter of the shield machine cuts the soil in front, and the cut soil is transported to the back of the machine through the conveyor and then transported out of the tunnel. This process not only improves excavation efficiency, but also reduces the clutter on the construction site, helping to maintain a clean working environment.
Assembly system
The assembly system is an important component of the shield machine, equivalent to the "skeleton" of the machine. The factory produces a series of ring-shaped segments according to the specifications of the shield machine. These segments are assembled in the tunnel through a ring assembly machine to form a continuous support structure. The installation of the segments not only provides the necessary support for the tunnel, but also ensures the safe excavation of the shield machine, making the entire construction process more stable and reliable.
Summary
The efficient operation of the shield machine depends on its complex structure and the close cooperation of various systems. The shield shell provides the necessary external protection and support, the propulsion system provides the power for the equipment to move forward, the excavation system is responsible for transporting the excavated soil and rocks, and the assembly system ensures the structural stability of the tunnel. These systems work together to enable the shield machine to play an irreplaceable role in tunnel construction, significantly improving engineering efficiency and construction safety.
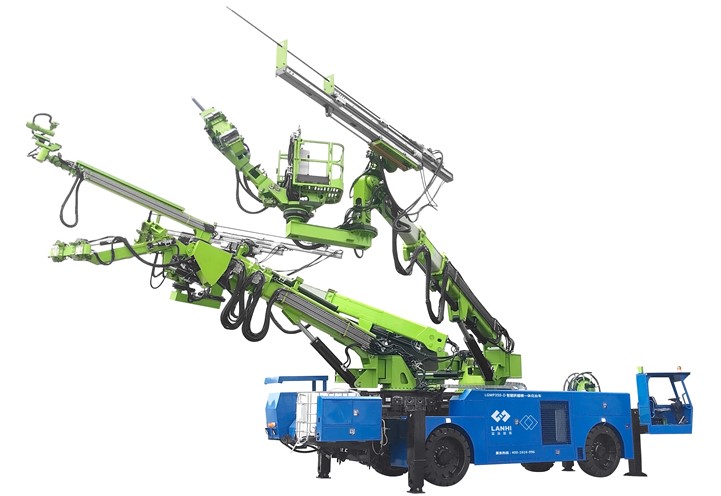
In tunnel engineering, choosing the right anchor drilling rig is crucial
In tunnel engineering, choosing the right anchor drilling rig is crucial to ensure construction quality and safety. So, how to choose the right anchor drilling rig? Here are some suggestions to help you make a wise choice:
1. Understand the geological conditions: Different geological conditions require different types of anchor drilling rigs. For example, soft rock geology may require a light drilling rig, while hard rock geology requires a heavier and more powerful drilling rig. Therefore, before choosing, be sure to understand the geological conditions of the tunnel in detail, including rock type, hardness, cracks, etc.
2. Consider drilling needs: According to the design requirements of the tunnel and the stability analysis of the surrounding rock, determine the required drilling diameter, depth and angle. This will directly affect the specifications and performance of the anchor drilling rig you choose. Make sure that the selected drilling rig can meet these requirements and has sufficient accuracy and stability.
3. Evaluate drilling rig performance: Understand the performance characteristics of anchor drilling rigs of different brands and models, including power, speed, torque, drilling speed, etc. Compare their advantages and disadvantages and choose those with stable performance and high reliability. At the same time, consider the maintenance and upkeep costs of the drilling rig, as well as whether it is easy to operate and repair.
4. Consider the construction environment: Tunnel construction environments are often complex and changeable, including small spaces, high humidity, poor ventilation and other problems. Therefore, when choosing an anchor drilling rig, consider its adaptability and durability. Choose rigs that can work normally in harsh environments and are easy to carry and install.
5. Reference experience and reputation: Understand the situation of anchor drilling rigs used in other tunnel projects, including brand, model, performance, etc. Refer to the evaluation and reputation in the industry and choose those products that are widely acclaimed. At the same time, communicate with experienced engineers and technicians and listen to their suggestions and opinions.
6. Consider after-sales service: Choose brands and suppliers that provide perfect after-sales service. Make sure they can provide technical support, spare parts supply and maintenance services in a timely manner to ensure the normal operation of the drilling rig and construction progress.
7. Comprehensive budget and cost-effectiveness: Finally, weigh the budget and cost-effectiveness of the project. Consider not only the purchase cost, but also the cost of long-term operation and maintenance. Choose anchor drilling rigs that meet project requirements and are economical.
When choosing a suitable anchor drilling rig, you need to consider multiple factors, including geological conditions, drilling requirements, drilling rig performance, construction environment, experience and reputation, after-sales service, and budget. By carefully evaluating and comparing, choosing the most suitable anchor drilling rig for your tunnel project will provide a strong guarantee for construction quality and safety.
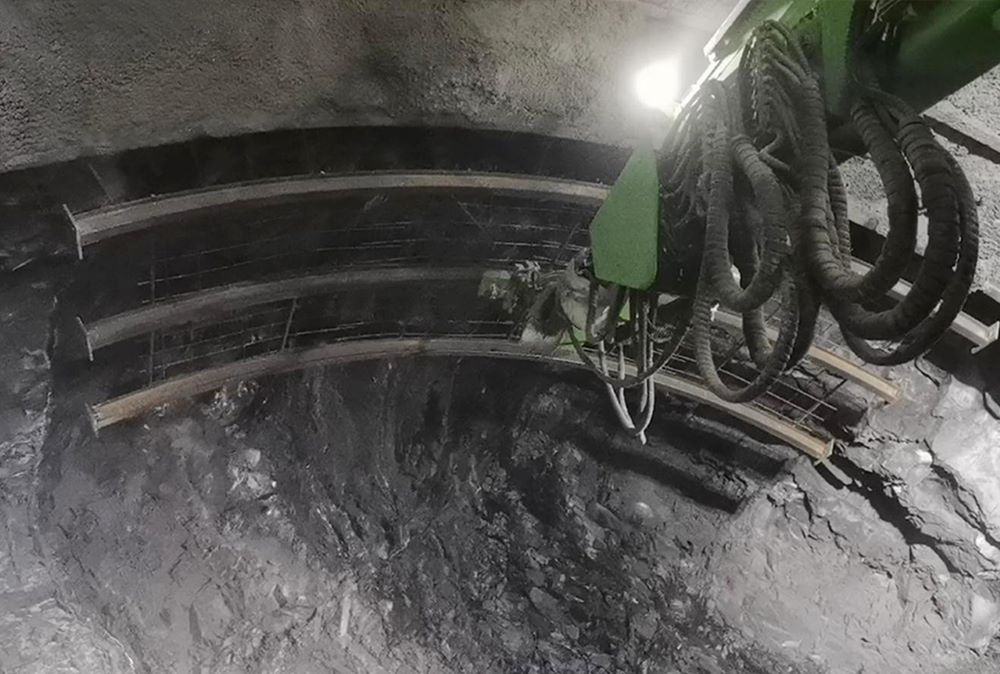
Anchor drill, one of the key equipment indispensable in tunnel and underground engineering
In the world of tunnel and underground engineering, every inch of excavation is full of challenges. In this context, anchor drill, with its unique functions and roles, has become one of the key equipment indispensable in these projects, and is widely used in engineering fields such as coal mines, tunnels, and slopes.
Anchor drill is a kind of equipment used for anchor support construction, mainly used to drill holes in rocks and soil for installing anchors. It has outstanding advantages in improving support effect, reducing costs, speeding up tunneling, reducing auxiliary transportation, reducing labor intensity, and improving tunnel section utilization.
The main function of the anchor drill is to drill holes in rock or soil and implant anchors into them to form a stable anchor structure. This anchor structure can effectively improve the stability of the surrounding rock and prevent disasters such as collapse and landslides. In the process of tunnel excavation, anchor drill plays a vital role. It can form a solid protective barrier around the tunnel in time to ensure the safety of construction personnel and the smooth progress of the project.
There are many types of anchor drilling rigs, the most common ones are pneumatic anchor drilling rigs, hydraulic anchor drilling rigs, electric anchor drilling rigs, etc. Among them, pneumatic anchor drilling rigs are powered by compressed air, and have the advantages of simple structure, light weight, and easy operation, but the output power is small, and they are suitable for rock formations with lower hardness; hydraulic anchor drilling rigs are powered by hydraulic oil, and have the advantages of large output power, fast drilling speed, and strong adaptability, but the structure is complex and the cost is high; electric anchor drilling rigs are powered by electric motors, and have the advantages of low noise and no pollution, but the output power is small, and they are suitable for small projects.
When choosing an anchor drilling rig, it is necessary to comprehensively consider factors such as specific engineering geological conditions, construction requirements, and budget. At the same time, it is also necessary to pay attention to the quality, performance, reliability, and after-sales service of the anchor drilling rig to ensure the smooth progress of construction and the reliability of engineering quality.

How does the wet spraying robot work? Detailed explanation of the operation process of the wet spraying robot construction site (6 steps)
The wet spraying robot is a high-efficiency equipment for concrete spraying, which is widely used in construction fields such as tunnels and underground projects. It has a high degree of automation, and the construction efficiency and construction quality are significantly improved. The following will introduce the work process of the wet spraying robot in detail.
I. Construction site preparation
Before starting the wet spraying operation, the construction site must be fully prepared first. Make sure the site is flat and clean, and remove any obstacles that may affect the operation of the equipment. At the same time, check whether the water supply and power supply facilities of the site are operating normally to provide guarantees for the subsequent construction.
II. The wet spraying trolley enters the construction site
After the construction site is properly prepared, the wet spraying trolley enters the construction site. The positioning and placement of the trolley need to be carried out in accordance with the requirements of the construction drawings to ensure that it can cover all areas that need to be sprayed. After the trolley is in place, conduct a preliminary inspection of the equipment and prepare for operation after confirmation.
3. Start the equipment
1. Start the hydraulic system: First start the hydraulic system of the wet spraying trolley to ensure its normal operation and provide power support for the next operation.
2. Start the air compressor: Then start the air compressor to ensure that the air pressure meets the spraying requirements.
3. Start the hopper mixing: Start the mixing device in the hopper to maintain the uniformity of the concrete material and prevent the material from separating during the spraying process.
IV. Feeding and spraying surface treatment
1. Hopper feeding: After the mixing device is started and operates normally, the hopper feeding operation is performed. The feeding process should be uniform and continuous to avoid blockage or overload.
2. Spraying surface cleaning: Clean the surface to be sprayed, remove dust, oil and other impurities on the surface, and ensure that the concrete can be firmly attached to the base surface.
V. Start wet spraying operation
After all preparations are completed, start the formal wet spraying operation. According to the design requirements and construction specifications, adjust the spraying parameters (such as spraying pressure, spraying speed, etc.) to ensure the quality and efficiency of spraying. During the operation, closely monitor the equipment operation status and spraying effect, and adjust the spraying parameters and equipment settings in time.
Six, treatment after wet spraying operation
After the wet spraying operation is completed, shut down the machine and clean the equipment and pipelines. During the cleaning process, the residual materials in the pipeline should be thoroughly removed to prevent them from affecting the operation of the equipment during the next use. Finally, perform equipment maintenance, check the wear of each component, and replace damaged parts in time to ensure the long-term normal use of the equipment.
The construction process of the wet spraying manipulator includes site preparation, equipment entry, equipment startup, material addition and spraying surface treatment, wet spraying operation, cleaning and maintenance after the operation. Each link needs to be carried out strictly in accordance with the operating specifications to ensure construction quality and construction safety. Through detailed process management and operating specifications, the high efficiency and automation advantages of the wet spraying manipulator can be fully utilized to improve construction efficiency and construction quality.

Will tunnel crossing faults cause other geological problems?
Will tunnel crossing faults cause other geological problems? Tunnels crossing faults may indeed cause a series of other geological problems, mainly including:
1. Leakage problem: Fault zones are usually accompanied by the development of rock cracks, which may cause leakage inside the tunnel, and in severe cases may even form water flows, posing a threat to the tunnel structure and operational safety.
2. Ground subsidence: Tunnel excavation near faults may cause surface subsidence, especially in areas where fault activity is frequent. Ground subsidence may cause damage to surface buildings and facilities, and also affect the stability of the tunnel.
3. Impact of seismic activity: Tunnels crossing faults may change the original stress state, and may induce or intensify seismic activity, which is a potential risk for the long-term safe operation of tunnels.
4. Failure of support structure: Due to the broken and unstable characteristics of rocks in the fault area, the existing support structure may not be able to effectively resist geological pressure, resulting in failure of the support structure, thereby affecting the stability of the tunnel.
5. Tunnel deformation: Under the influence of faults, the tunnel may bend, twist and other deformation phenomena, which will not only affect the use function of the tunnel, but also may cause driving safety problems.
6. Environmental impact: Tunnel construction and operation may have an impact on the surrounding environment, such as noise, vibration, dust and other pollution, as well as potential impacts on groundwater resources and ecosystems.
In order to reduce these risks, a series of measures need to be taken during tunnel design and construction, including detailed geological surveys, reasonable support design, strict construction monitoring, and later maintenance and monitoring. Through these measures, the possible harm caused by faults to tunnel projects can be effectively prevented and mitigated.

What is the power of LANHI's arch installation trolley?
What is the power of LANHI's arch installation trolley? LANHI's arch installation trolley has two models, one is conventional, suitable for low-altitude areas, and the other is plateau type, suitable for high-altitude areas; the power of the engine of the two models will be different.
Conventional type
Engine highway: 138.5KW
Electrical installed power: 87.5KW
Plateau type
Engine highway: 168KW
Electrical installed power: 87.5KW
LANHI's arch installation trolley is not only suitable for arch installation operations in highways and high-speed railway tunnels, but also covers under-excavation processing, charging operations, tunnel inspections, and static high-altitude operations on site, which greatly improves construction efficiency and safety. LANHI's arch installation trolleys have different powers and prices. You can choose according to the specific conditions of the construction project.

Advantages of wet concrete spraying trolleys over traditional dry spraying machines
In construction, concrete spraying technology is an important link. Compared with traditional dry spraying machine operations, wet concrete spraying trolley operations bring significant advantages, not only outstanding in health and safety, but also showing strong competitiveness in construction efficiency and cost control.
First, wet concrete spraying trolley operations have obvious advantages in health and safety. Traditional dry spraying machine operations will generate a lot of dust, which not only pollutes the environment, but also causes serious harm to the health of workers. Wet spraying trolley operations effectively reduce the dust concentration beside the machine and outside the nozzle by reducing the dust generation during the spraying process, thereby greatly reducing the risk of workers inhaling harmful dust. This improvement has greatly improved the working environment on the construction site and helped protect the health of workers.
Secondly, wet spraying trolley operations have significantly improved construction efficiency. In traditional dry spraying machine operations, the concrete rebound rate is high and the material waste is serious. With the use of wet spraying trolleys, the concrete rebound rate can be reduced to about 15%, which means that more concrete can be effectively attached to the construction surface and reduce material waste. At the same time, because the water-cement ratio is easy to control, the wet spraying process can better guarantee the quality of concrete, making the performance of shotcrete more stable and superior.
In addition, the wet spraying trolley operation also reduces the labor intensity of workers. Because the spraying process is more efficient and stable, workers do not need to frequently adjust and maintain equipment, and the construction process is smoother and more continuous. This not only improves work efficiency, but also reduces the fatigue of workers caused by operating complex mechanical equipment.
Finally, the wet spraying trolley operation also performs well in cost control. Although the initial investment of the wet spraying trolley may be high, the overall construction cost is effectively controlled due to reduced material waste, improved construction efficiency and reduced equipment maintenance costs. This makes the wet spraying trolley operation an economical and efficient choice, which is favored by more and more construction companies.
Concrete wet spraying trolley operation has significant advantages in improving the construction environment, improving construction efficiency, reducing the labor intensity of workers and saving construction costs. It not only provides workers with a healthier working environment, but also brings higher economic benefits to enterprises. It is an important technological advancement in modern construction.

Application and advantages of arch-anchor integrated machine in modern bridge construction
The arch-anchor integrated machine is an advanced equipment that integrates arch structure and anchor system, which plays a vital role in modern bridge construction. This equipment not only improves construction efficiency, but also ensures the safety and stability of the bridge. The following will introduce the application of arch-anchor integrated machine in bridge construction and its advantages in detail.
The application of arch-anchor integrated machine in bridge construction is very extensive. It is mainly used to make and install the arch structure of the bridge, as well as to provide necessary anchoring support. Due to its structural characteristics, the arch-anchor integrated machine can work under various complex geological conditions, providing strong technical support for bridge construction. For example, in areas with complex terrain such as mountainous areas and canyons, the arch-anchor integrated machine can overcome terrain restrictions and achieve efficient and safe construction. In addition, the arch-anchor integrated machine can also be used in the construction of transportation infrastructure such as highways and railways, providing reliable guarantees for transportation.
The arch-anchor integrated machine has significant advantages in bridge construction. First, it improves construction efficiency. The traditional bridge construction method requires a lot of manpower and time, while the arch-anchor integrated machine greatly shortens the construction period through automated operation. Secondly, it improves the construction quality. The arch-anchor machine uses high-precision measurement and control technology to ensure the precise production and installation of the arch structure, thereby improving the overall quality of the bridge. Finally, it reduces construction costs. Although the initial investment of the arch-anchor machine is high, due to its high efficiency and high-quality construction performance, it can reduce the cost of the entire project in the long run.
The application prospects of the arch-anchor machine in bridge construction are very broad. With the continuous development of science and technology, the functions and performance of the arch-anchor machine will be further improved. For example, more intelligent arch-anchor machines may appear in the future, which can achieve more autonomous construction and further improve construction efficiency and quality. At the same time, with the increasing awareness of environmental protection, the arch-anchor machine will also develop in a more environmentally friendly and energy-saving direction. For example, the research and development of arch-anchor machines driven by clean energy can reduce pollution to the environment.
As an advanced bridge construction equipment, the arch-anchor machine plays an irreplaceable role in modern bridge construction. Its wide application and significant advantages indicate that it will continue to play an important role in future bridge construction. With the continuous innovation and progress of technology, we have reason to believe that the arch-anchor machine will show stronger vitality and potential in future bridge construction.