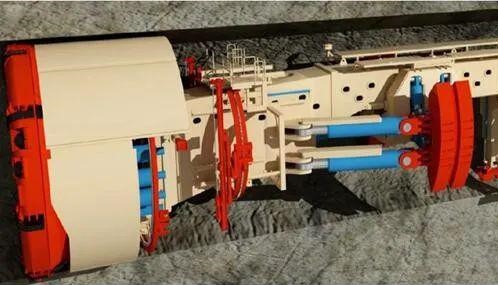
Structural composition and application scope of open rock tunnel boring machine
Open rock tunnel boring machine (abbreviated as open TBM) is an important equipment in modern tunnel construction, which is specially used for rock tunnel excavation projects with good rock stability and less weak surrounding rock. Under geological conditions with high stratum integrity and high uniaxial compressive strength, this equipment shows extremely high construction efficiency and cost-effectiveness, becoming a popular choice in the engineering industry.
Structural composition of open TBM
The main structure of open TBM is complex and precise, mainly composed of the following key parts:
1. Cutterhead: responsible for cutting rock, it is the core component of TBM. The cutterhead cuts the rock in front through rotational motion, allowing the tunnel to move forward continuously.
2. Drive system: provides power to drive the cutterhead to rotate and ensure the normal operation of the equipment.
3. Shield: located behind the cutterhead, protects the equipment and operators from rock collapse.
4. Main beam: connects and supports all parts of the entire equipment, providing structural stability.
5. Saddle: provides support and positioning for the cutterhead and drive system to ensure cutting accuracy.
6. Shoes: provide additional stability and support, especially during excavation.
7. Rear support: support and fix the tail of the tunnel boring machine to maintain overall balance.
Scope of application and advantages
Open TBM is particularly suitable for strata with good rock integrity and high uniaxial compressive strength. These strata usually have the following characteristics:
- Good rock stability: The rock strata are strong and not easy to collapse, and the risk during excavation is low.
- Less weak surrounding rock: There are fewer weak surrounding rocks encountered during excavation, and the construction difficulty is relatively low.
Under such geological conditions, open TBM can play its greatest advantages:
1. High construction efficiency: Due to good stratum conditions, the excavation speed is fast and the construction period is greatly shortened.
2. Low cost: The equipment maintenance and operation costs are low, and the economic benefits are significant.
With its high efficiency and low cost, the open rock tunnel boring machine has become the best choice for tunnel excavation under suitable geological conditions. Its wide application not only improves construction efficiency, but also effectively reduces engineering costs, making an important contribution to the tunnel construction industry.
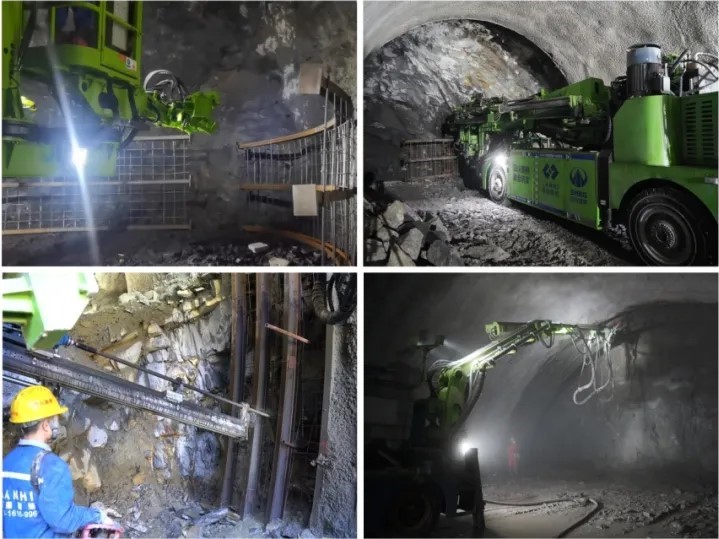
LANHI's engineering machinery is unique in the field of smart construction
In recent years, LANHI's engineering machinery has made remarkable achievements in the field of smart construction and has become a leader in the industry. Through continuous innovation and research and development, the company has launched a series of efficient and intelligent engineering machinery equipment, including multi-functional tunnel boring machines, intelligent arch-anchor integrated trolleys and intelligent arch frame integrated trolleys, providing strong support for engineering construction.
1. Multi-functional tunnel boring machine: a powerful tool for tunnel construction
The multi-functional tunnel boring machine is a star product of LANHI. It integrates multiple functions in one. It can not only perform tunneling operations, but also complete a variety of complex underground construction tasks. This equipment is equipped with an advanced automatic control system, which can achieve high-precision and high-efficiency tunneling operations. Its strong adaptability and flexibility enable it to perform well under various geological conditions, greatly improving construction efficiency and reducing labor costs.
2. Intelligent arch-anchor integrated trolley: improving construction safety and construction efficiency
The intelligent arch-anchor integrated trolley is a device specially designed by LANHI to improve the safety of tunnel construction. The trolley integrates arch frame installation and anchor construction, and can automatically complete the positioning and installation of the arch frame and the drilling and installation of the anchor. The application of the intelligent control system not only improves the construction speed, but also ensures the accuracy and safety of the construction. Especially in complex geological environments, the advantages of the intelligent arch-anchor integrated trolley are more obvious, effectively reducing the construction risk.
3. Intelligent arch frame integrated trolley: improve construction safety and construction efficiency
The intelligent arch frame integrated trolley is another innovative equipment launched by LANHI to further improve the efficiency of tunnel construction. The trolley can automatically complete the assembly and installation process of the arch frame, reducing the tedious steps of manual operation. The intelligent operating system enables it to operate flexibly in a small construction space, significantly improving the overall efficiency of construction. The intelligent arch frame integrated trolley not only saves time, but also reduces construction costs. It is an indispensable tool for modern tunnel construction.
LANHI's engineering machinery has taken the lead in the field of smart construction through continuous technological innovation and product upgrades. Its multifunctional tunnel boring machine, intelligent arch-anchor integrated trolley and intelligent arch frame integrated trolley have not only greatly improved construction efficiency and safety, but also led the industry's intelligent development direction. In the future, LANHI will continue to uphold the spirit of innovation and continuously launch more efficient and intelligent construction equipment to help smart construction reach a new level.
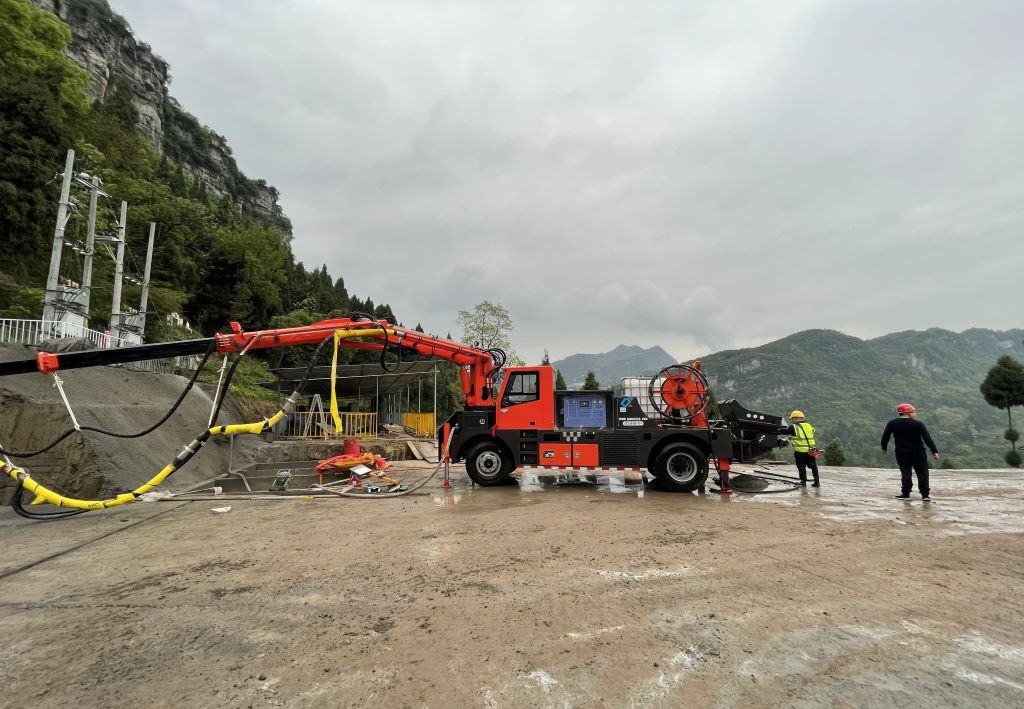
Concrete wet spraying trolleys not only improve construction efficiency and quality, but also protect the health of workers
As the main equipment for spraying anchor support operations, concrete wet spraying trolleys have been widely used in the construction of mine tunnels, railway and highway tunnels, water conservancy culverts, various underground projects, high-rise building foundation pits, military projects, etc. Compared with traditional dry spraying machine operations, the use of wet spraying trolleys brings significant advantages.
First of all, wet spraying trolley operations can significantly reduce the dust concentration at the construction site. During the operation of traditional dry spraying machines, dust will diffuse in large quantities beside the machine and outside the nozzle, seriously endangering the health of workers. The wet spraying trolley effectively reduces the generation of dust by adding water during the spraying process, thereby providing workers with a safer working environment.
More importantly, the wet spraying trolley operation significantly improves construction efficiency. The concrete rebound rate of the traditional dry spraying process is high, which usually causes material waste. The wet spraying trolley reduces the rebound rate of concrete to about 15%, greatly reducing material loss and improving construction efficiency. In addition, since the water-cement ratio in the wet spraying process is easy to control, the quality of shotcrete can be better guaranteed, improving the overall effect of the project.
The use of wet spraying trolleys not only improves construction efficiency and quality, but also reduces the labor intensity of workers. Due to the high degree of automation of equipment operation, workers only need to perform simple equipment operation and maintenance during the construction process, which greatly reduces the input of physical labor. At the same time, since the wet spraying process reduces material waste and dust control costs, the overall project cost is saved.
The application of concrete wet spraying trolleys in various engineering construction not only improves construction efficiency and quality, ensures the health of workers, but also effectively reduces construction costs. It has broad application prospects and significant economic benefits.
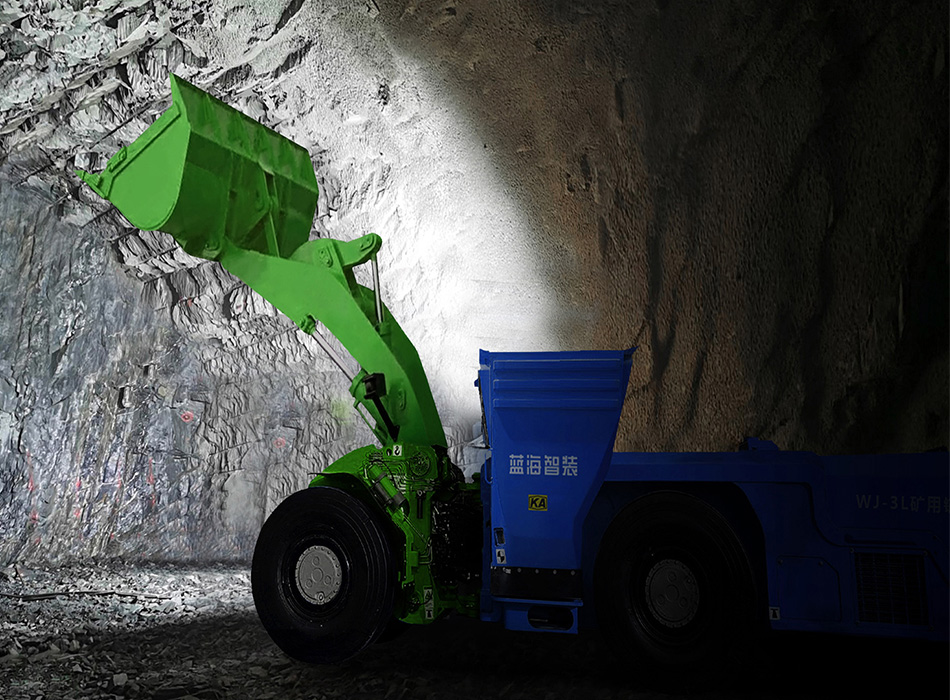
Three Main Types of Mining Loading Equipment: Excavators, Loaders, and Buckets
Mining loading equipment plays a crucial role in the mining industry, enhancing both work efficiency and safety while facilitating ore handling. This article will provide a detailed introduction to the three main types of mining loading equipment: excavators, loaders, and buckets.
1. Excavators
Excavators are the most common type of mining loading equipment, primarily used for digging materials such as ore and soil. Depending on their mobility, excavators can be categorized into two types: tracked and wheeled.
- Tracked Excavators: These excavators use tracks for movement, making them suitable for rugged terrain and harsh environments. They offer better stability and are particularly suitable for large-scale earthwork and mining operations.
- Wheeled Excavators: Compared to tracked excavators, wheeled excavators are more flexible and suitable for flat work sites. They excel in urban construction and small to medium-sized mining operations.
Excavators, with their powerful digging force and flexible working arms, can efficiently carry out ore extraction and loading.
2. Loaders
Loaders are used for loading loose materials such as ore and coal. Depending on the loading position, loaders can be classified into two types: front loaders and backhoe loaders.
- Front Loaders: These loaders have a bucket located at the front of the machine, offering easy operation and good visibility. They are suitable for most mining and construction sites, capable of quickly loading and transporting large quantities of materials.
- Backhoe Loaders: Compared to front loaders, backhoe loaders have a bucket installed at the rear of the machine, typically used for operations under specific conditions, such as loading work in narrow spaces.
Loaders are widely used in various mining and construction projects due to their efficient loading capacity and strong maneuverability.
3. Buckets
Buckets are essential components installed on loading machinery, specifically designed for grabbing and transporting materials. Different types of buckets can be installed on excavators and loaders to meet diverse operational needs.
- Standard Buckets: Used for general earthwork operations, suitable for grabbing and transporting common ores and soil.
- Reinforced Buckets: Made with thickened steel plates and wear-resistant materials, these are suitable for high-intensity digging and transporting operations, such as handling hard ores and construction debris.
- Specialized Buckets: Designed for specific operational needs, such as grabbing loose coal, sand, or performing precise ore screening.
The diversity and flexibility of buckets enable loading equipment to adapt to various mining operational environments, enhancing equipment utilization and work efficiency.
Mining loading equipment, including excavators, loaders, and buckets, each has unique functions and application scenarios. Together, they form a crucial part of mining operations, improving the efficiency of ore extraction and handling while significantly ensuring the safety and sustainability of mining activities. In modern mining production, the reasonable selection and use of this equipment are vital for enhancing production efficiency and reducing costs.
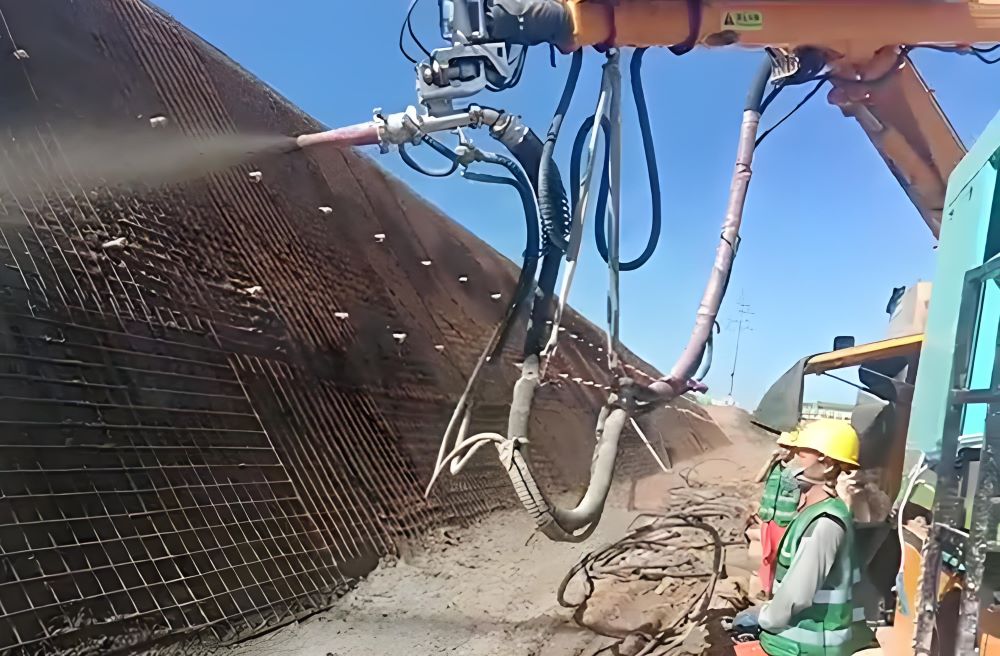
The Three Main Characteristics of Shotcrete and Its Advantages over Ordinary Cast-in-Place Concrete
In construction engineering, shotcrete has become a favored building material due to its unique characteristics and advantages. Shotcrete is highly regarded for its rapid strength development, strong bonding ability, high density, and good impermeability. During its construction process, multiple steps such as conveying, pouring, and compacting are combined into one, eliminating the need for formwork, thus offering the advantage of rapid and efficient construction.
The rapid strength development of shotcrete gives it a unique advantage in engineering. Compared to ordinary cast-in-place concrete, shotcrete can better fill the gaps and voids between rock masses, thereby increasing the overall integrity of the surrounding rock mass and effectively preventing weathering and loosening of the free surface. Moreover, shotcrete can work in conjunction with the surrounding rock mass to form a stable integrated structure, providing reliable assurance for the stability and safety of the engineering project.
Another major reason for the popularity of shotcrete is its strong bonding ability. Through high-pressure spraying, concrete can firmly adhere to the surface of rocks, forming a good bond, making the structure more robust and durable. This strong bonding ability enables shotcrete to be widely used in various engineering fields including rock reinforcement, tunnel support, dam protection, etc.
Furthermore, shotcrete has a high density and excellent impermeability, making it excel in waterproofing and seepage prevention. In construction engineering, shotcrete with high density and good impermeability can effectively prevent water penetration, protecting the engineering structure from erosion and damage by water, thus extending the service life of the project.
With its advantages of rapid strength development, strong bonding ability, high density, and good impermeability, shotcrete has become an indispensable material in construction engineering. Its fast and efficient construction method has led to its widespread application in various types of projects. With the continuous development of technology and the continuous improvement of techniques, it is believed that the position and role of shotcrete in construction engineering will be further enhanced.
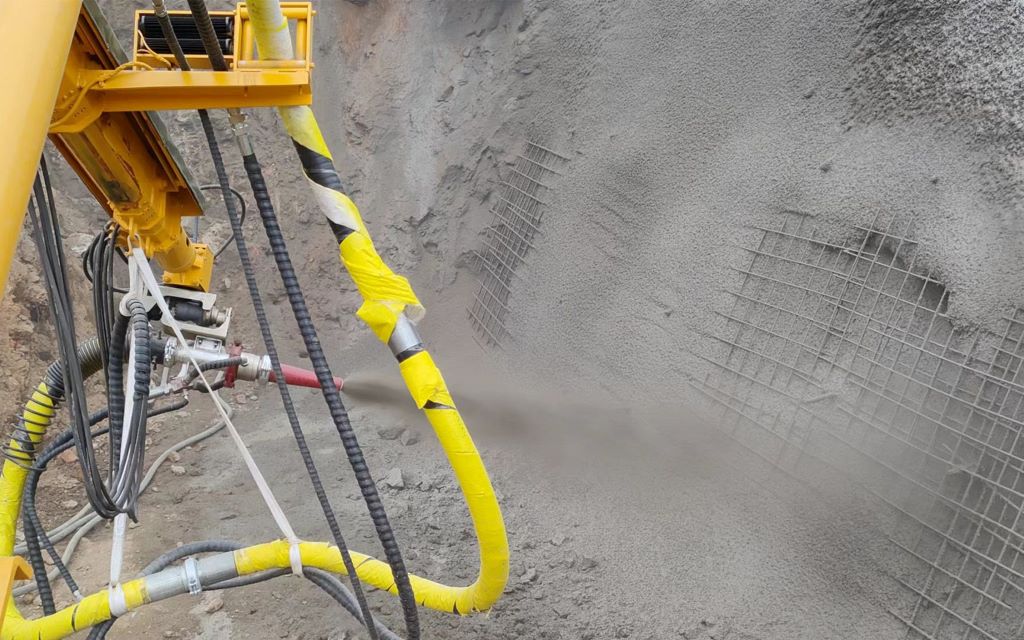
Three Types of Shotcrete Construction Techniques and Corresponding Mechanical Equipment
Shotcrete is a commonly used construction technique, widely applied in tunnel construction, slope reinforcement, and underground engineering, among other fields. Depending on the construction method, shotcrete can be divided into three techniques: dry-mix shotcrete, wet-mix shotcrete, and moist-mix shotcrete. Each technique utilizes different equipment, namely dry-mix shotcrete machines, wet-mix shotcrete machines, and moist-mix shotcrete machines. The primary distinction between these techniques lies in the material feeding process, particularly the timing of adding water and accelerators.
1. Dry-Mix Shotcrete Technique
Dry-mix shotcrete involves conveying dry concrete materials to the nozzle via high-pressure air and then mixing with water at the nozzle before being sprayed onto the construction surface. The main features of dry-mix shotcrete are simple equipment, wide applicability, and fast spraying speed. However, since the material is dry during spraying, it generates a large amount of dust pollution. Additionally, dry-mix shotcrete exhibits high rebound rates and significant material waste, while the dust pollution in the construction environment poses a threat to the health of operators.
2. Wet-Mix Shotcrete Technique
Wet-mix shotcrete involves pre-mixing concrete materials with a certain amount of water before entering the nozzle, then spraying them onto the construction surface using spraying equipment. Compared to dry-mix shotcrete, wet-mix shotcrete can effectively reduce dust pollution and rebound. However, due to the relatively small amount of pre-mixed water, the flowability and workability of concrete are still not as ideal as the moist-mix shotcrete technique.
3. Moist-Mix Shotcrete Technique
Moist-mix shotcrete involves thoroughly mixing concrete materials and water in a mixer before pumping the moist concrete to the nozzle, where it is mixed with accelerators and then sprayed onto the construction surface. The advantages of moist-mix shotcrete lie in its good flowability and workability, enabling more uniform coverage of the construction surface and reducing rebound and material waste. Moreover, moist-mix shotcrete generates less dust pollution, contributing to improved construction environment and operator health protection.
In practical construction, choosing the appropriate shotcrete technique requires comprehensive consideration of specific project requirements, environmental conditions, and economic factors. Although dry-mix shotcrete has simple equipment and low costs, its limitations due to high dust and rebound rates restrict its applicability. While wet-mix shotcrete partially addresses these issues, it still falls short of the ideal performance of moist-mix shotcrete. Although moist-mix shotcrete involves more complex equipment and higher costs, its construction quality and environmental performance are optimal, making it suitable for projects with high requirements for construction quality and environmental standards.
Each shotcrete technique—dry-mix, wet-mix, and moist-mix—has its pros and cons, and the choice of technique should be balanced according to specific project needs. With technological advancements and increasing environmental requirements, the application of moist-mix shotcrete in modern engineering projects is becoming more widespread, and its advantages are becoming increasingly evident.
By understanding and applying different shotcrete techniques, engineers can better select suitable construction methods to ensure construction quality and safety.
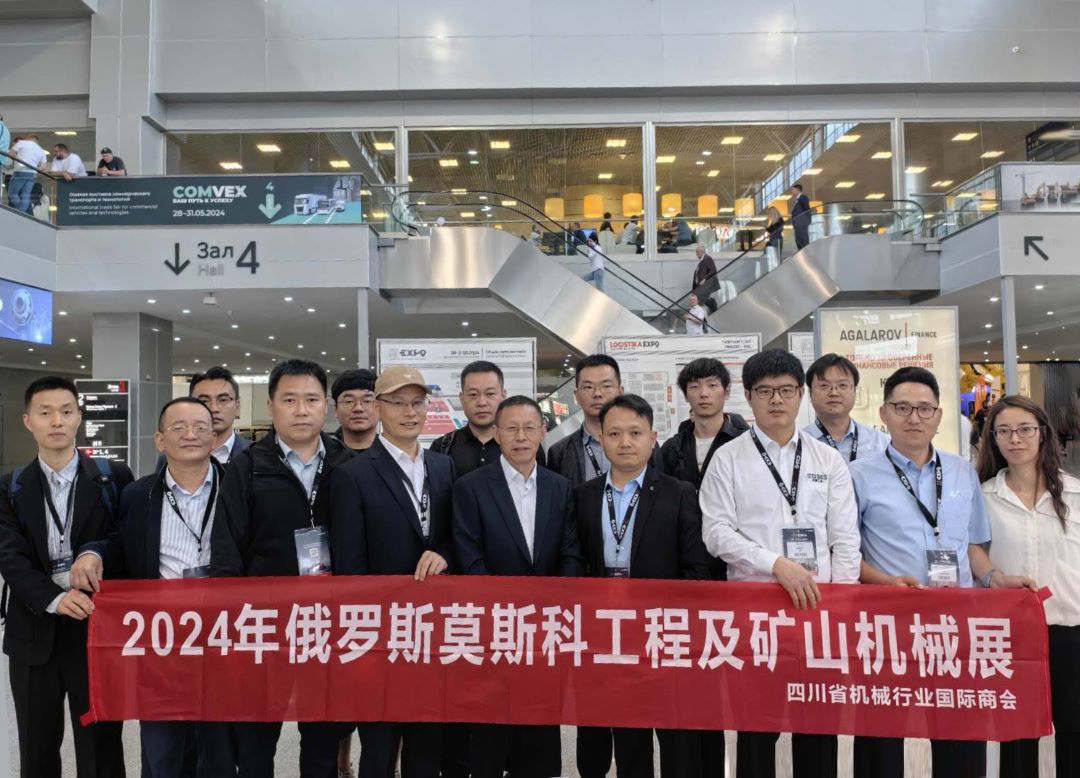
2024 Moscow Engineering and Mining Machinery Exhibition: LANHI's Tunnel Engineering Products Attract Attention
The 25th Russia International Construction and Engineering Machinery Exhibition (CTT-EXPO) in 2024 was grandly held at the Crocus Exhibition Center in Moscow. This exhibition is one of the most significant and influential industry events in Russia and the CIS countries, attracting numerous internationally renowned companies and professional visitors. Among the many exhibitors, LANHI stood out with its innovative tunnel engineering products, becoming a highlight of the exhibition and garnering widespread attention from within and outside the industry.
LANHI's tunnel engineering products are characterized by their high efficiency and intelligence, meeting the demands for efficiency and safety in modern tunnel engineering machinery. These products not only excel in performance but also offer more intelligent operations, providing a solid guarantee for the automation and intelligent development of tunnel engineering. Through continuous technological innovation and R&D investment, LANHI has demonstrated its strong capability and competitiveness in tunnel engineering machinery.
Exhibition Overview
The Russian Mining and Engineering Machinery Exhibition, MINING WORLD RUSSIA, annually showcases the most advanced mining equipment and technology, being regarded as a barometer of industry development. This year's exhibition not only displayed advanced mining machinery and related equipment from around the world but also covered the latest technologies and products in various fields of engineering machinery. The wide range of exhibits included excavation machinery, rock drilling machinery and mining machinery, rebar and prestressing machinery, pneumatic tools, concrete machinery, decoration machinery, electric tools, pile driving machinery, sanitation machinery, motorized industrial vehicles, power devices and accessories, various accessories and electrical components and assemblies, and testing engineering machinery parts, providing visitors with a one-stop procurement platform.
The exhibition provided an excellent platform for industry practitioners, allowing them to learn about the latest technologies and products and engage in face-to-face exchanges and cooperation. Whether for purchasing equipment or technical consultations, visitors could find everything they needed here. During the exhibition, major companies showcased their latest products and technologies, promoted their brands, and expanded their businesses, further driving the industry's development and progress.
The 2024 Moscow Engineering and Mining Machinery Exhibition not only displayed the latest achievements in the industry but also pointed out the direction for future development. LANHI, with its leading technology and products, became the focus of this exhibition, setting a new benchmark for the intelligent development of tunnel engineering machinery.
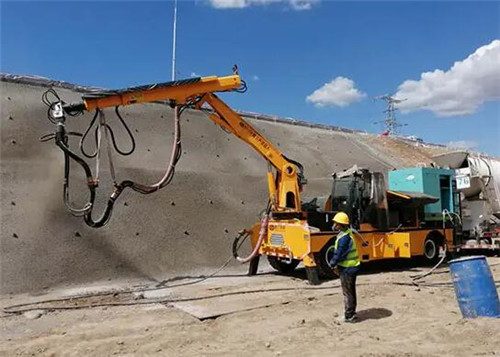
Classification and Characteristics of Shotcrete Construction Techniques
Shotcrete is a construction technology that involves using mechanical equipment to spray concrete at high speed onto a structural surface to form a tightly bonded layer. Based on the state of the concrete and the construction method used during the process, shotcrete construction techniques can be categorized into three types: dry-mix shotcrete, semi-wet mix shotcrete, and wet-mix shotcrete. Each method has its unique features and applications.
1. Dry-Mix Shotcrete
Dry-mix shotcrete involves conveying dry concrete materials to the nozzle, where they are mixed with high-pressure water before being sprayed onto the structural surface. The main characteristics of this method include:
- Flexible Material Control: The water-cement ratio can be adjusted on-site, allowing for better adaptation to varying construction conditions.
- High Rebound Rate: Due to incomplete mixing during spraying, some materials tend to rebound, leading to increased waste.
- High Dust Production: The dry process generates significant dust, impacting the construction environment and workers' health.
2. Semi-Wet Mix Shotcrete
Semi-wet mix shotcrete is a method that falls between dry-mix and wet-mix shotcrete. It involves adding a portion of water to the concrete materials before feeding them into the shotcrete machine, which then uses high-pressure air to spray the mix onto the structural surface. Features of this method include:
- Moderate Material Consistency: Partial water addition reduces dust generation while maintaining a certain level of rebound.
- Simplified Construction: Compared to dry-mix shotcrete, the semi-wet mix method is easier to operate and offers better controllability during construction.
- Wide Applicability: Suitable for various construction environments, especially those with high dust control requirements.
3. Wet-Mix Shotcrete
Wet-mix shotcrete involves spraying already fully mixed wet concrete directly onto the structural surface through delivery pipes. Its main characteristics include:
- Low Rebound Rate: Fully mixed concrete before spraying significantly reduces material rebound, minimizing waste.
- Minimal Dust Production: The wet process generates almost no dust, making it more environmentally friendly and healthier for workers.
- High Construction Quality: The wet-mix method allows for better control of concrete uniformity and adhesion, enhancing construction quality.
The choice of shotcrete construction technique should be determined based on specific construction requirements and site conditions. Dry-mix shotcrete is suitable for sites where material control is crucial but dust impact is not a major concern. The semi-wet mix method offers a balanced approach between dust control and material management. Wet-mix shotcrete, with its high quality, low dust, and low rebound characteristics, is often the preferred choice for high-standard construction projects. Reasonable selection and application of different shotcrete construction techniques can significantly improve construction efficiency and project quality.
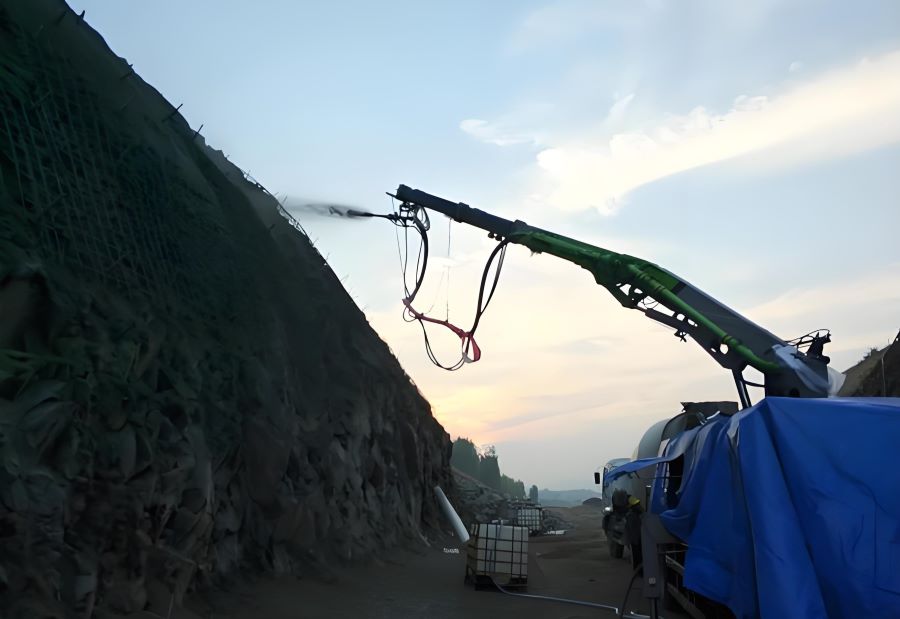
Compared to the traditional dry spraying process, wet spraying technology has significant advantages
Concrete spraying technology is widely used in modern construction projects. With continuous technological advancements, wet spraying technology has shown remarkable superiority over traditional dry spraying methods. Thanks to its advantages in construction dust, production efficiency, rebound rate, and construction quality, wet spraying technology has gradually become the preferred choice in engineering construction.
Firstly, wet spraying technology can significantly reduce dust concentration at construction sites. This not only improves the working environment but also effectively eliminates the health hazards posed by dust to workers. In the traditional dry spraying process, a large amount of dust disperses into the air during spraying, exposing workers to prolonged periods in such an environment, which can easily lead to various occupational diseases. Wet spraying technology, by pre-mixing water into the concrete, greatly reduces the dust generated during construction, significantly safeguarding workers' health.
Secondly, wet spraying technology offers higher productivity. The wet spraying process simplifies on-site operational steps, markedly increasing spraying speed and efficiency. This means that within the same timeframe, the wet spraying process can complete more construction tasks, enhancing the overall progress and effectiveness of the project.
Thirdly, wet spraying technology significantly reduces the rebound rate of concrete. In the dry spraying process, the rebound rate of concrete typically ranges between 15% and 50%, which not only wastes a substantial amount of material but also adds to the cleanup workload. By adopting wet spraying technology, the rebound rate of concrete can be reduced to below 10%, greatly minimizing material waste and construction costs.
Lastly, wet spraying technology ensures higher construction quality. In the wet spraying process, the water-cement ratio can be precisely controlled, significantly improving the homogeneity of the concrete, thereby enhancing the overall quality and durability of the structure. In contrast, the quality of the dry spraying process largely depends on the skills and responsibility of the operators, making it difficult to guarantee consistent quality.
In summary, wet spraying technology demonstrates unparalleled advantages in the field of concrete spraying, particularly in terms of construction environment, efficiency, material utilization, and final quality. With advancements in technology and increasing construction demands, wet spraying technology is expected to play an increasingly important role in future construction projects.
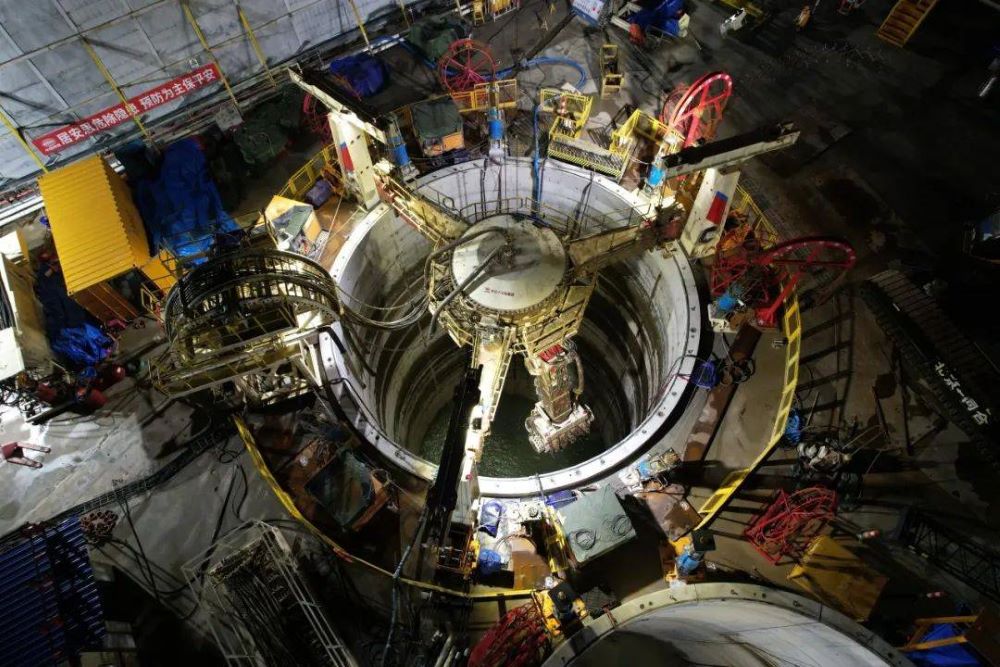
What are the classifications of tunneling machines based on excavation lines? Three main types of tunneling machines based on excavation lines
A tunneling machine is a heavy-duty mechanical device specifically designed for excavating tunnels, mines, and underground spaces. According to the different types of excavation lines, tunneling machines can be classified into three main types: horizontal tunneling machines, vertical shaft tunneling machines, and inclined shaft tunneling machines. Each type of tunneling machine has its unique design and application scenarios, suitable for various types of underground engineering projects.
1、Horizontal Tunneling Machine
Horizontal tunneling machines are primarily used for excavating horizontal or nearly horizontal tunnels and mines. These machines are typically applied in urban subway construction, highway tunnels, water diversion tunnels for hydropower stations, and other engineering projects. Horizontal tunneling machines can operate efficiently and safely in complex geological conditions, boasting fast excavation speeds and high precision. They are crucial equipment in modern underground construction.
2、Vertical Shaft Tunneling Machine
Vertical shaft tunneling machines are specifically designed for excavation in the vertical direction, suitable for digging mine shafts, underground storage spaces, and deep foundation pits. The design of vertical shaft tunneling machines takes into account stability and safety in vertical operations, equipped with powerful drilling heads and support systems, providing reliable assurance in deep shaft excavation. These machines are widely used in coal mines, metal mines, and underground construction.
3、Inclined Shaft Tunneling Machine
Inclined shaft tunneling machines are used for excavating tunnels or mines in inclined directions, suitable for projects that require tunneling along slopes or ramps. The design of inclined shaft tunneling machines incorporates features of both horizontal and vertical shaft tunneling machines, enabling flexible operation on slopes of different angles. They are commonly used in mining transport inclined shafts, underground pipeline installation, and slope tunnels, offering strong adaptability and flexibility.
Tunneling machines, based on the different types of excavation lines, are divided into three categories: horizontal tunneling machines, vertical shaft tunneling machines, and inclined shaft tunneling machines. Each type of tunneling machine has its unique design and application scenarios, meeting the needs of various underground engineering projects. With continuous advancements in technology, the performance and efficiency of tunneling machines are constantly improving, providing strong support for the successful implementation of modern underground engineering.