
The application of wet spraying concrete technology and wet spraying manipulators has gradually become an important technical means in tunnel construction
With the continuous improvement of construction efficiency and quality requirements of tunnel projects, wet spraying manipulators are increasingly widely used in tunnel construction, reflecting their unique advantages.
The application of wet spraying concrete technology and wet spraying manipulators has gradually become an important technical means in tunnel construction (Figure 1)
Wet spraying concrete technology has many significant advantages in the initial support construction of tunnels:
High safety factor: wet spraying concrete technology reduces the need for high-altitude operations and reduces the risk of workers being injured.
Low dust volume: Traditional dry spraying concrete will produce a lot of dust, while wet spraying technology greatly reduces the generation of dust, which helps to protect the health of workers.
High concrete strength: The material ratio of wet spraying concrete is more scientific, and the strength of concrete after construction is higher, ensuring the structural safety of the tunnel.
Low rebound rate: The rebound rate of wet spraying concrete is low, which reduces material waste and improves construction efficiency.
Stable quality: The material of wet spraying concrete is uniform during the construction process, avoiding the problem of unstable quality caused by material separation of dry spraying concrete.
Compared with traditional manual construction, the concrete wet spraying manipulator has the following significant advantages:
Flexible movement: The wet spraying manipulator can operate flexibly in a narrow tunnel space, covering a wide construction range with almost no dead corners.
High construction efficiency: The use of the manipulator greatly improves the construction efficiency, shortens the construction period, and reduces the project cost.
Improve the working environment: The manipulator operation reduces the chance of direct contact with harmful substances by humans, improves the working environment of workers, and protects their health.
Improve construction quality: The manipulator sprays concrete more evenly and meticulously, avoids quality problems caused by manual operation, and improves the consistency of construction quality.
In the initial support concrete construction of the tunnel, the use of wet spraying machines greatly improves the construction environment and ensures the safety and health of the operators. This construction method not only requires fewer operators and reduces the loss of materials, but also conforms to the concept of environmentally friendly construction, and gradually becomes an important technical means in tunnel construction.
The application of wet spraying concrete technology and wet spraying manipulators not only improves the environment of the initial support construction of the tunnel, ensures the health and safety of the construction workers, but also improves the construction efficiency and quality, which conforms to the green, environmentally friendly and economical concepts of modern tunnel construction.

Wet spraying technology in tunnel engineering: the key to improving construction efficiency and safety
In tunnel engineering construction, excavation technology is one of the core technologies of tunnel construction, and concrete spraying in the initial support of tunnels is one of the key processes of tunnel construction. With the further acceleration of the pace of infrastructure construction in my country, the application of wet spraying technology in large-scale engineering construction has become more and more extensive.
Advantages of wet spraying technology
The wet spraying process replaces the traditional dry spraying process, bringing many significant advantages. First, the wet spraying process reduces the generation of dust during construction by pre-mixing water and concrete before spraying, greatly improving the working environment of tunnel construction workers. This not only helps to protect the health of construction workers, but also reduces pollution to the surrounding environment.
Secondly, the application of wet spraying technology significantly reduces labor intensity. The traditional dry spraying process requires workers to operate manually, which is labor-intensive, while the wet spraying process relies on automated equipment, such as concrete wet spraying trolleys. This equipment not only reduces the workload directly involved by workers, but also improves the accuracy and efficiency of construction.
Improving construction efficiency and saving costs
The introduction and popularization of wet spraying technology has greatly improved the efficiency of tunnel construction. Due to the better adhesion and fluidity of wet spraying concrete, it can be more evenly and firmly attached to the tunnel wall during the spraying process, thereby improving the quality and stability of the support. In addition, the wet spraying process simplifies the construction process and speeds up the construction progress, thereby shortening the project period.
In terms of cost, the wet spraying process also shows significant advantages. The traditional dry spraying process not only requires a lot of manual operation, but also often leads to material waste and equipment loss due to dust problems. The mechanization and automation of the wet spraying process not only reduces material waste and equipment wear, but also reduces labor costs, saving construction costs overall.
Promote the mechanization process of tunnel construction
The emergence of concrete wet spraying trolleys is an important symbol of tunnel construction mechanization. With the development of science and technology, the design and function of wet spraying trolleys have been continuously optimized, making tunnel construction more efficient and safe. These devices are equipped with advanced spraying systems and control systems, which can achieve high-precision operations and further improve construction quality and efficiency.
The application of wet spraying technology has played an important role in tunnel engineering construction. It not only improves the construction environment, reduces labor intensity, and improves work efficiency, but also saves construction costs and promotes the mechanization process of tunnel construction. With the continuous advancement of my country's infrastructure construction, wet spraying technology will continue to play a key role in future tunnel projects and contribute more to my country's infrastructure construction.

Application and advantages of wet concrete spraying trolleys in tunnel engineering
Wet concrete spraying trolleys are increasingly used in modern construction, especially in spraying concrete support operations in railway tunnels, highway tunnels, water conservancy culverts, mine tunnels, dam slopes, building foundation pits and military engineering. In the initial support operations of long and large tunnels, the advantages of wet concrete spraying trolleys are particularly prominent, which has strongly promoted the application of mechanized construction in tunnels.
Application fields of wet concrete spraying trolleys
1. Railway tunnels: In railway tunnel construction, wet spraying trolleys can quickly complete initial support and improve the safety and efficiency of tunnel construction.
2. Highway tunnels: Highway tunnel projects have high requirements for construction speed and quality. The application of wet spraying trolleys meets these requirements and ensures the progress of the project.
3. Water conservancy culverts: In water conservancy projects, wet spraying trolleys can efficiently spray concrete to ensure the stability and durability of culverts.
4. Mine tunnels: The mine operating environment is complex, and the flexibility and rapidity of wet spraying trolleys make them perform well in mine tunnel support.
5. Dam slope: The wet spraying trolley can effectively prevent the slope from sliding and enhance the overall stability of the slope in the application of the dam slope.
6. Building foundation pit: In the support operation of the building foundation pit, the wet spraying trolley can quickly build the initial support structure to ensure the safety of the foundation pit.
7. Military engineering: In military engineering, the wet spraying trolley can quickly build a protective structure to improve the protection capability of the project.
Advantages of concrete wet spraying trolley
Compared with traditional small wet spraying machines, concrete wet spraying trolleys have significant advantages:
1. Operation flexibility: The wet spraying trolley can operate flexibly in a complex construction environment and adapt to various terrains and construction requirements.
2. Rapidity: The wet spraying trolley has high spraying efficiency and can complete large-area spraying operations in a short time.
3. Convenience: The wet spraying trolley integrates multiple functions, is easy to operate, and reduces the complexity of manual operation.
4. Economic efficiency: Due to its high spraying efficiency and good quality, the wet spraying trolley can reduce construction costs and improve economic benefits.
5. Safety: The wet spraying trolley has a high degree of automation, which reduces the labor intensity and construction risks of operators.
Improvement of quality and efficiency
The wet spraying trolley has obvious advantages in improving the quality of tunnel shotcrete. By accurately controlling the spraying amount and spraying angle of concrete, the wet spraying trolley can ensure the uniformity and density of the spraying layer, thereby improving the structural strength and durability of the tunnel. At the same time, the efficient operation capacity of the wet spraying trolley greatly improves the construction efficiency and speeds up the progress of the entire project.
The wide application of the wet spraying trolley of concrete not only overcomes the problems of traditional concrete spraying machines, but also significantly improves the construction efficiency and quality, reduces labor intensity and construction costs, and promotes the development of mechanized construction in tunnels and other fields.

Classification of wet concrete spraying machines and their applications in construction projects
The main function of wet concrete spraying machines is to spray concrete onto the target surface through high pressure to form a protective layer or support structure. It is the core equipment in shotcrete construction and has been widely used in various shotcrete support projects. Let's take a look at the classification and application scenarios of wet concrete spraying machines.
1. Classification of wet concrete spraying machines
Common wet concrete spraying machines are usually divided into the following categories according to their working principles and application scenarios:
Hydraulic wet concrete spraying machine: This equipment is driven by a hydraulic system and generates high pressure through a hydraulic pump to spray the concrete mixture onto the construction surface. The hydraulic wet spraying machine has the characteristics of stable pressure and uniform spraying, and is suitable for large-area and long-distance spraying construction.
Rotor wet concrete spraying machine: This type of equipment adopts a rotor structure, and the concrete mixture is driven to be sprayed through the rotation of the rotor. The rotor wet spraying machine has a simple structure and is easy to maintain. It is often used in small and medium-sized projects and construction projects with special spraying requirements.
Vehicle-mounted wet concrete spraying machine: The vehicle-mounted equipment installs the wet concrete spraying machine on a vehicle, which has high mobility and is suitable for projects that require frequent movement of construction sites, such as municipal roads and bridge maintenance.
Concrete wet spraying manipulator: This is a highly intelligent device, usually equipped with a mechanical arm, which can accurately control the spraying direction and angle, and is suitable for projects with complex structures and fine construction, such as large tunnels and mining projects.
2. Application scenarios of wet concrete spraying machine
Concrete wet spraying machine plays an important role in multiple engineering fields:
Construction engineering: It is used for wall reinforcement, foundation construction and spraying of protective layers of buildings to improve the durability and stability of buildings.
Municipal engineering: In the construction and maintenance of municipal infrastructure such as roads, bridges, and underground pipelines, it is used to spray concrete to improve structural strength and corrosion resistance.
Railway and highway tunnels: In tunnel construction, wet spraying machines are used to spray concrete support layers to prevent landslides and ensure construction safety.
Foundation pit support: During the excavation of the foundation pit, wet spraying machines are used to spray concrete to form support walls to prevent foundation pit collapse.
Mining Engineering: In mining, wet spraying machines are used to spray concrete walls, protect mine structures, and ensure operational safety.
Slope management: In slope reinforcement projects, sprayed concrete forms a protective layer to prevent landslides and soil erosion.
As an important equipment in modern construction technology, wet concrete spraying machines have become an indispensable tool for various types of sprayed concrete projects due to their high efficiency, flexibility, and strong adaptability. With the continuous advancement of technology, wet concrete spraying machines will further improve construction efficiency and project quality, and provide more reliable technical support for building and infrastructure construction.

What are the pipe jacking equipment? Introduction to common pipe jacking equipment
Pipe jacking equipment is a mechanical equipment used for trenchless construction. It can lay pipelines, cables, etc. through obstacles without damaging the ground. So, what are the pipe jacking equipment? The following are some common pipe jacking equipment:
1. Pipe jacking machine: This is the core equipment in pipe jacking construction. It crushes soil or rock through a rotating cutting head and discharges the crushed materials while pushing the pipeline forward.
2. Main jacking cylinder: Provides the thrust required for jacking and pushes the pipe jacking machine and pipeline forward.
3. Relay room: When the jacking distance is long, a relay room is needed to increase the force and distance of jacking.
4. Mud system: Used to transport and discharge mud to maintain the stability of the excavation face and reduce friction.
5. Guiding system: Helps control the direction and position of the pipe jacking machine to ensure that the pipeline is laid according to the design requirements.
6. Back wall: Provides reaction force to support the jacking of the pipe jacking machine and pipeline.
7. Lifting equipment: used for lifting and transporting pipe jacking equipment and pipelines.
When selecting pipe jacking equipment, it is necessary to consider factors such as geological conditions, pipeline diameter, and jacking distance, and make reasonable selection and configuration according to actual conditions. At the same time, it is also necessary to pay attention to the quality and performance of the equipment to ensure the safety and efficiency of construction.
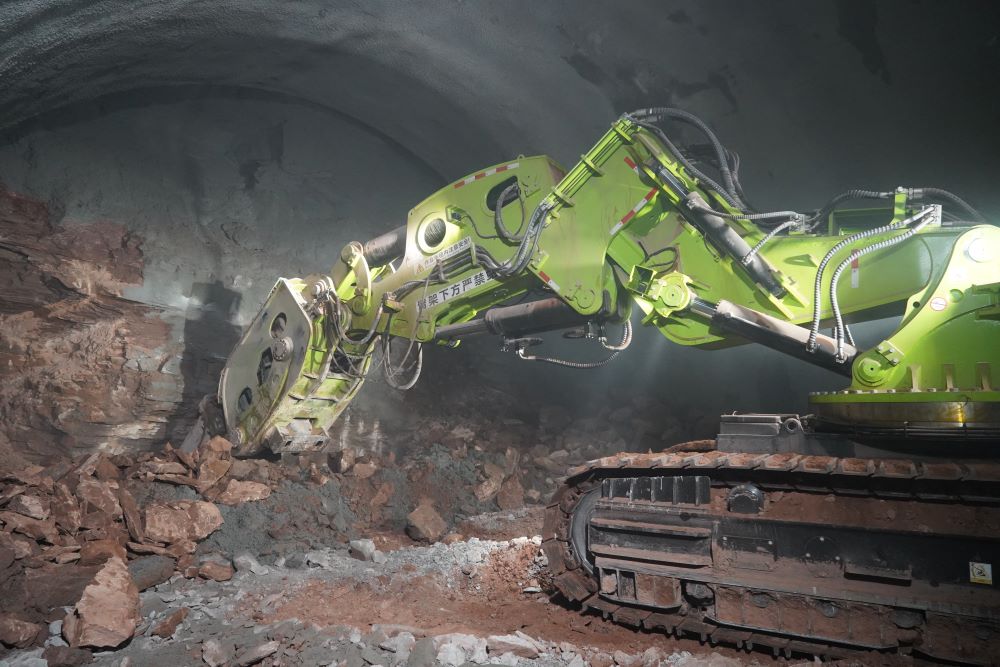
What is a dual-mode TBM? Types, technical features and applications of dual-mode TBMs
What is a dual-mode TBM? A dual-mode TBM is a highly efficient equipment designed for tunnel projects with large geological differences and long construction distances. This type of TBM can switch modes according to changes in hydrogeological conditions during construction, thereby increasing construction speed and reducing construction costs.
Dual-mode TBMs have two slag discharge modes or two pressure balance modes. At present, common dual-mode TBMs have the following two combinations:
1. Earth pressure and mud water dual-mode TBM: This type of TBM can switch between earth pressure balance and mud water balance modes, and is suitable for geological conditions with large changes in water content.
2. Earth pressure and rock dual-mode TBM: This type of TBM can switch between earth pressure balance and rock excavation modes, and is suitable for tunnel projects with alternating soft and hard geology.
Technical features of dual-mode TBMs
Dual-mode TBMs are a derivative of balanced shield and shield rock TBMs, and have the technical features of these two different types of TBMs. During the construction process, when the geological conditions change significantly, the dual-mode TBM can quickly switch to the appropriate working mode. This flexibility not only ensures the safety of construction, but also improves the overall efficiency of construction.
1. Strong adaptability: The dual-mode TBM can cope with various complex geological conditions, whether it is soft soil with high water content or hard rock, it can work effectively.
2. High construction efficiency: Through mode switching, the TBM can maintain efficient operation under different geological conditions, reducing the time loss caused by equipment replacement or adjustment.
3. Cost saving: Since there is no need to frequently replace equipment or stop work for adjustment, the dual-mode TBM can significantly reduce construction costs in long-distance tunnel construction.
Application Cases
In some large-scale tunnel projects, the dual-mode TBM has demonstrated its excellent performance. For example, in the construction of mountain tunnels with drastic geological changes, the dual-mode TBM successfully overcame the challenges brought by the alternation of soft and hard geology by flexibly switching between earth pressure mode and rock mode, significantly improving the construction speed and ensuring the quality of the project.
With the advancement of science and technology, the technology of dual-mode TBM is also constantly improving. In the future, this equipment will be widely used in tunnel projects with more complex geological conditions, providing more reliable and efficient solutions for engineering construction. Through flexible mode conversion, the dual-mode tunnel boring machine not only improves construction efficiency, but also effectively reduces construction costs, and has broad application prospects.
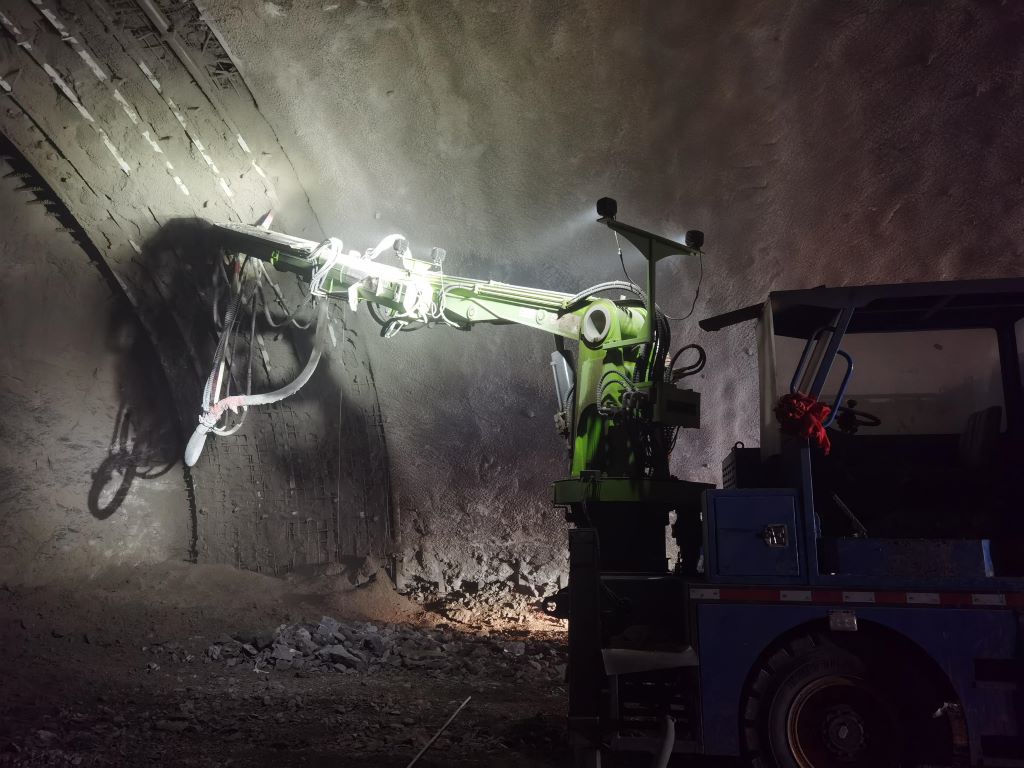
6 major advantages and 4 major application areas of concrete wet spraying trolleys
As a modern construction equipment, concrete wet spraying trolleys are widely used in large-scale engineering projects due to their many advantages. This article will discuss in detail the main advantages of concrete wet spraying trolleys and their applications in various projects.
Six major advantages of concrete wet spraying trolleys
1. High degree of construction mechanization
The concrete wet spraying trolley adopts advanced mechanized construction technology, which can greatly improve construction efficiency and construction quality. Compared with traditional manual operation methods, mechanized construction not only reduces labor costs, but also significantly improves construction speed.
2. High work efficiency
The concrete wet spraying trolley can complete concrete spraying operations continuously and quickly, effectively shortening the construction period. This efficient construction method is particularly significant in large-scale projects and can greatly improve the progress of the overall project.
3. Small rebound
In the process of concrete spraying, rebound is an important indicator to measure construction quality. The concrete wet spraying trolley adopts optimized spraying technology, which can significantly reduce the rebound of concrete, thereby improving material utilization and construction quality.
4. Strong construction safety
The wet concrete spraying trolley reduces the chances of construction workers directly contacting the spraying area through remote control and automated operation, thereby improving construction safety. Especially in dangerous and complex environments, the use of automated equipment can effectively avoid accidents.
5. Good working environment
Traditional concrete spraying operations are prone to generate a lot of dust and noise, affecting the health and work efficiency of construction workers. The wet concrete spraying trolley adopts advanced dust and noise reduction technology, which significantly improves the working environment and improves the working comfort of construction workers.
6. Significant economic benefits
Although the initial investment of the wet concrete spraying trolley is high, the long-term economic benefits brought by its high efficiency, low loss and safety are significant. Taking into account the labor cost, material cost and construction period, the use of the wet concrete spraying trolley can bring higher economic benefits to the project.
4 major application areas of concrete wet spraying trolleys
Due to its many advantages, concrete wet spraying trolleys have been widely used in various large-scale engineering projects, mainly including the following aspects:
- Railway tunnels and highway tunnels
In the construction of railway and highway tunnels, the high-efficiency spraying capacity and excellent construction quality of concrete wet spraying trolleys make it the preferred equipment for tunnel support operations.
- Hydraulic culverts and mine tunnels
The construction environment of hydraulic culverts and mine tunnels is usually more complex. The mechanized operation of wet spraying trolleys can greatly improve construction safety and efficiency and ensure project quality.
- Dam slopes and building foundation pits
In the support operations of dam slopes and building foundation pits, concrete wet spraying trolleys can provide stable and reliable sprayed concrete support, effectively preventing the collapse of slopes and foundation pits.
- Military engineering
Military engineering usually needs to complete high-intensity construction tasks in a short time. The high-efficiency performance and safety guarantee of concrete wet spraying trolleys have made it widely used in military engineering.
The concrete wet spraying trolley has become an indispensable and important equipment in modern large-scale engineering projects due to its high degree of mechanization, high work efficiency, low rebound, high safety, good working environment and significant economic benefits. Its wide application in railway tunnels, highway tunnels, water conservancy culverts, mine tunnels, dam slopes, building foundation pits and military engineering has fully demonstrated its important value in engineering construction.
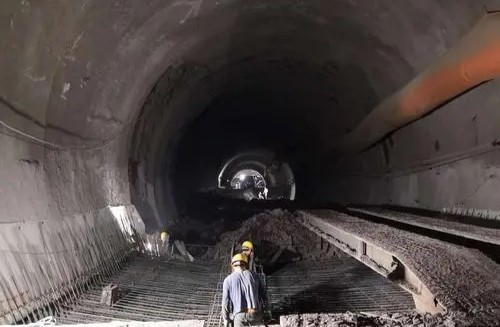
What should be done when encountering leakage problems during tunnel invert construction?
What should be done when encountering leakage problems during tunnel invert construction? In tunnel invert construction, leakage is a common problem that needs to be solved in a timely manner. Here are some recommended steps to deal with it:
1. Locate the leakage point immediately:
- Use penetration detection technology, such as infrared thermal imaging, acoustic detection, etc., to quickly and accurately determine the location of the leakage point.
- For large-scale tunnel projects, it may be necessary to set up a special leakage monitoring system to monitor the leakage in real time.
2. Preliminary treatment:
- If conditions permit, you can first use temporary plugging materials (such as fast-curing concrete, waterproof tape, etc.) to initially plug the leakage point to slow down the leakage rate.
- During this period, a professional team should be organized as soon as possible to conduct detailed on-site investigations and plan discussions.
3. Detailed analysis of the causes:
- Conduct a comprehensive analysis of the causes of leakage, including but not limited to construction quality problems, waterproof material defects, changes in geological conditions, etc.
- Understand the structural details near the leakage point, such as whether there are cracks, voids, etc., which may be potential causes of leakage.
4. Develop a detailed repair plan:
- According to the severity of the leakage, the results of the cause analysis and the actual situation on site, develop a targeted and detailed repair plan.
- The plan should include the required materials, tools, human resources and the expected repair time.
5. Perform repair work:
- According to the repair plan, organize a professional team to carry out on-site repair work. This may include cleaning the leakage area, replacing damaged waterproof materials, repairing cracks, reinforcing the structure, etc.
- During the repair process, the construction specifications should be strictly followed to ensure the quality of construction.
6. Quality inspection and subsequent monitoring:
- After the repair is completed, strict quality inspection is carried out to ensure that the leakage problem is completely solved.
- Even if the problem is solved, leakage monitoring should continue for a period of time to ensure that the repair effect is long-lasting and stable.
7. Recording and feedback:
- Record the entire process in detail, including the materials used, methods, difficulties encountered and the final repair effect.
- Feedback the handling experience to relevant departments and teams as a reference for handling similar problems in the future.
8. Preventive measures:
- Analyze the root cause of the leakage problem, improve the construction process and quality control measures to prevent similar problems from happening again.
- Strengthen the training of construction personnel to improve their professional skills and quality awareness.
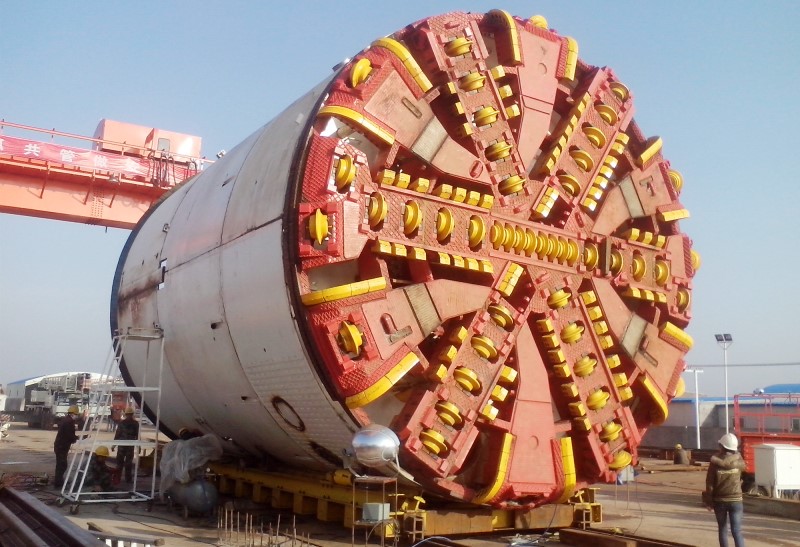
China's infrastructure construction drives the growth of large-diameter TBM market demand
In recent years, China's infrastructure construction has ushered in unprecedented rapid development, covering railway construction, highway transportation, water conservancy and hydropower, urban rail transit, mine construction, and large-scale gas, power, and water transmission projects. These projects have an increasing demand for full-section tunnel boring machines (TBMs), especially large-diameter TBMs. With the continuous advancement of infrastructure projects, the application areas of large-diameter TBMs are becoming more and more extensive, from urban subways to cross-regional transmission pipelines, all aspects benefit from their superior performance and efficient construction capabilities.
Advantages of large-diameter TBMs
The introduction and use of large-diameter TBMs have significantly improved the efficiency and safety of tunneling projects. Compared with traditional tunneling methods, large-diameter TBMs have many advantages:
Safety and efficiency: Traditional tunneling projects are usually accompanied by high-intensity, high-risk and high-pollution problems, while the use of large-diameter TBMs transforms these problems into a relatively safe and efficient green construction mode. Its integrated design can effectively cope with complex geological conditions and ensure the safety and efficiency of the construction process.
Environmental protection: Large-diameter TBM has less impact on the environment during construction, which meets the environmental protection requirements of modern tunnel construction. Its efficient construction capacity and advanced technical means enable it to maintain high-quality engineering construction while reducing environmental damage.
Comprehensive performance: Large-diameter TBM can meet the multiple requirements of modern tunnel construction, including fast, high-quality, efficient, safe and environmentally friendly. These characteristics enable large-diameter TBM to achieve precise construction under various complex engineering conditions, further promoting the development of tunneling technology.
Growth of market demand
With the continuous increase in China's infrastructure construction projects and the continuous improvement of technical levels, the market demand for large-diameter TBM will continue to expand. In addition to traditional fields such as railways, highways, and urban rail transit, large-diameter TBM will also play an important role in cross-regional projects such as gas transmission, power transmission, and water transmission. This is not only because of its efficient construction capacity, but also because it conforms to the current concept of green development and can promote infrastructure construction towards a safer, more environmentally friendly and more efficient direction.
Overall, the widespread application of large-diameter TBM not only improves construction efficiency and quality, but also conforms to the current concept of green development. With the rapid advancement of China's infrastructure construction and the continuous improvement of technology, the market prospects for large-diameter TBMs are very broad. In the future, large-diameter TBMs will play an important role in more fields and help China's infrastructure construction achieve a new leap forward.
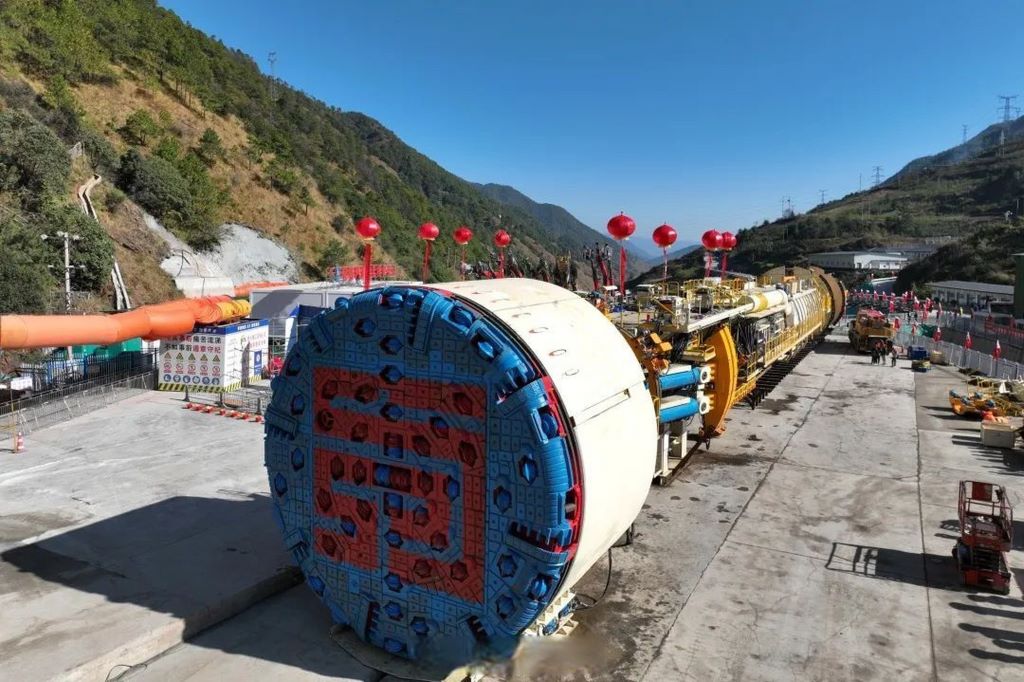
Tunnel boring machine, a powerful tool for modern tunnel construction and its application prospects
In modern engineering construction, tunnel excavation is a complex and arduous task. One of the key equipment to achieve this task is the tunnel boring machine. Tunnel boring machine, referred to as TBM (Tunnel Boring Machine), is an advanced construction machine that uses a rotary cutter to excavate, crush the surrounding rock in the hole and excavate, thereby forming the entire tunnel section.
Working principle of tunnel boring machine
The tunnel boring machine cuts and crushes the rock and soil in front through the rotary cutter installed at the front end. The cut debris is transported out of the tunnel through the conveying system, and the support system at the rear is responsible for supporting and stabilizing the newly excavated tunnel section. The entire excavation process is carried out continuously. The tunnel boring machine not only has to complete the excavation task, but also needs to carry out lining work at the same time to ensure the safety and stability of the tunnel.
Characteristics of tunnel boring machine
1. Fast and efficient: Compared with traditional blasting and manual excavation methods, tunnel boring machines can significantly increase the excavation speed. It has a high degree of automation and can work continuously and uninterruptedly, greatly shortening the tunnel construction period.
2. High safety: Traditional tunnel excavation methods are often accompanied by a lot of dust and explosion hazards, while the use of tunnel boring machines can effectively reduce these dangerous factors. The closed operating environment of the tunnel boring machine can reduce the time workers are exposed to dangerous environments and improve the overall construction safety.
3. Economic benefits: Although the initial investment of the tunnel boring machine is high, its high efficiency and low maintenance cost give it obvious economic advantages in long-term operation. Shorter construction period and less labor demand further reduce the total project cost.
4. High quality: The tunnel boring machine can accurately control the shape and size of the tunnel section to ensure the construction quality of the tunnel. Its high-precision construction method can meet the high requirements of modern engineering for tunnel quality.
Application prospects
Tunnel boring machines play an increasingly important role in the construction of transportation infrastructure. Whether it is a subway tunnel, a highway tunnel or a railway tunnel, the tunnel boring machine has demonstrated its excellent performance and advantages. With the continuous advancement of technology, the scope of application and excavation capacity of the tunnel boring machine are also constantly improving. In the future, it will play an irreplaceable role in more engineering projects.
As a new and advanced tunnel construction machinery, the tunnel boring machine has become an indispensable and important equipment in modern tunnel construction due to its characteristics of speed, safety, economy and high quality.