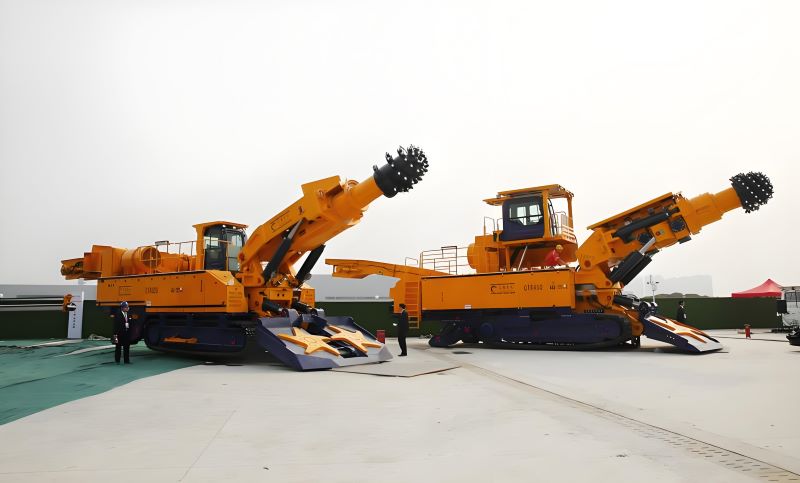
Two Types of Tunnel Boring Machines Based on Tunnel Face Conditions
Tunnel boring machines (TBMs) are essential equipment for tunnel and underground engineering excavation. Depending on whether the tunnel face requires pressure stabilization, TBMs can be categorized into open-type TBMs and pressurized TBMs. These two types play significant roles under different engineering conditions.
1、Open-Type TBMs
Open-type TBMs are suitable for tunneling environments that do not require special pressure stabilization. Their primary features include simple structure, easy operation, and low maintenance costs. These machines are widely used in tunnel projects with relatively stable geological conditions, such as hard rock and dry soil layers. The working principle of open-type TBMs involves mechanical breaking or cutting to achieve tunnel excavation, making them ideal for medium to short-distance tunnel projects.
2、Pressurized TBMs
Pressurized TBMs are used in complex geological environments requiring pressure stabilization, such as soft soil, sand layers, and underwater tunnels. These machines apply pressure to the tunnel face to prevent collapses or water ingress during excavation. Pressurized TBMs have complex internal structures, including pressure chambers, sealing systems, and slurry treatment systems, allowing them to work safely and efficiently under high water pressure and high ground stress conditions.
Comparison of the Two Types of TBMs
There are significant differences between open-type TBMs and pressurized TBMs in terms of application scenarios, structural complexity, and costs. Open-type TBMs are suitable for projects with simpler geological conditions and offer advantages of lower cost and easier maintenance. In contrast, pressurized TBMs have irreplaceable advantages in complex geological conditions. Although their costs are higher, they effectively ensure the safety and progress of the project.
TBMs play a crucial role in tunnel and underground engineering. Choosing the right type of TBM based on specific project requirements can significantly enhance construction efficiency and safety. In future tunnel projects, as technology continues to advance, TBMs will become more intelligent and efficient, further driving the development of underground engineering.
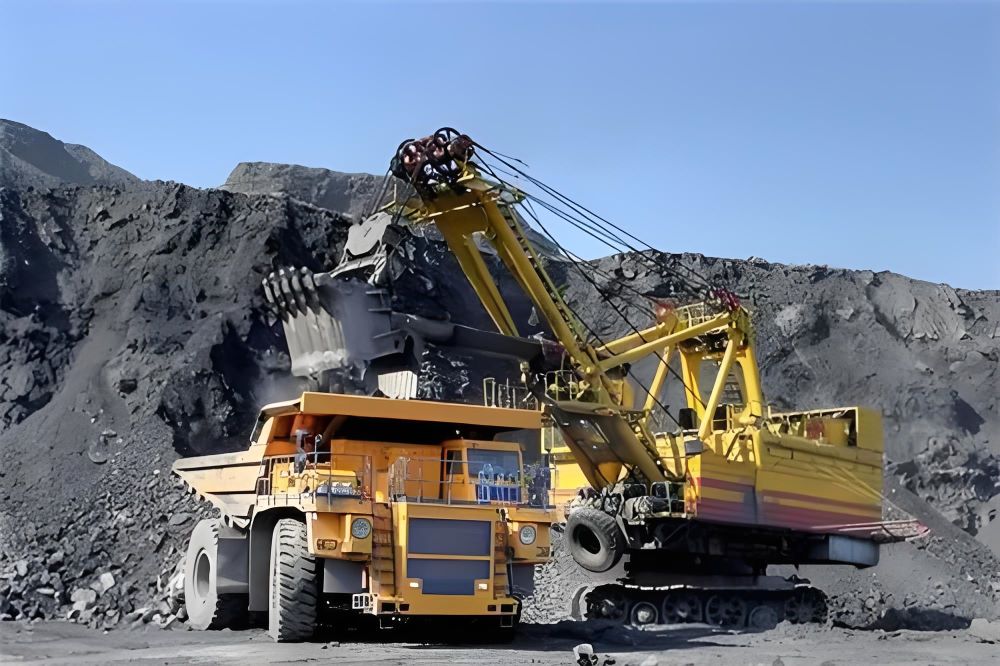
What Are the Types of Mining Machinery? An Overview of Various Mining Machinery Equipment
Mining machinery refers to various machines and tools used during the extraction of mineral resources. These machines play crucial roles at different stages of mining, including drilling, loading, transportation, hoisting, and crushing. Below are some common categories of mining machinery and their representative equipment:
1. Drilling Equipment:
- Drill Rig: Used for drilling geological formations to obtain geological data or to drill mine ventilation holes, drainage holes, etc.
- Drill Rod: Connects the drill rig to the drill bit, transmitting rotational and drilling force.
- Drill Bit: Directly acts on the rock to perform cutting operations.
2. Loading Equipment:
- Excavator: Used for excavating ore, soil, and other materials. They can be tracked or wheeled.
- Loader: Used for loading loose materials such as ore and coal. They can be front-loaded or rear-loaded.
- Bucket: Mounted on loading machinery for grabbing and transporting materials.
3. Transportation Equipment:
- Mine Cart: Used for transporting ore and waste rock within the mine, usually driven by electric or diesel engines.
- Mining Dump Truck: Has a large load capacity for transporting large quantities of materials.
- Conveyor Belt: Used for continuous material transport, available as ground conveyors or underground conveyors.
4. Hoisting Equipment:
- Winch: Uses steel wire ropes to pull objects, enabling vertical or horizontal transportation.
- Hoist: Used for vertical lifting of materials in mines, such as lifting mine carts and personnel.
- Elevator: Installed in mine shafts for personnel transport.
5. Crushing Equipment:
- Jaw Crusher: Uses the compressive force between two metal plates to crush materials.
- Hammer Crusher: Uses high-speed rotating hammers to strike and crush materials.
- Cone Crusher: Uses a conical crushing chamber to compress and crush materials.
6. Screening Equipment:
- Vibrating Screen: Uses vibration principles to screen materials, available as linear vibrating screens or circular vibrating screens.
- Rotary Screen: Uses a rotating drum to screen materials.
7. Washing and Sorting Equipment:
- Jig: Uses the buoyancy difference between water and materials for separation and washing.
- Spiral Classifier: Uses spiral motion for material classification.
8. Auxiliary Equipment:
- Pump Station: Provides necessary liquid pressure and flow for the mine.
- Compressor: Supplies compressed air for pneumatic tools and equipment.
- Ventilation Equipment: Ensures air quality in the mine, removing harmful gases.
9. Safety Equipment:
- Self-Rescuer: Provides respiratory protection in case of underground fires or toxic gas leaks.
- Rescue Equipment: Used for underground rescue operations, including life-saving cabins and rescue robots.
These machines may vary based on the specific needs and operational environment of the mine. They may also be equipped with other specialized features such as automated control systems and monitoring devices to enhance productivity and safety.

Some Considerations When Handling Rock Drill Malfunctions
When dealing with rock drill malfunctions, here are some important considerations:
1. Safety First
- Ensure all operators are away from the malfunction area, especially when checking electrical or hydraulic systems.
- Use appropriate personal protective equipment, such as safety glasses, gloves, and earplugs.
2. Power Off Operations
- Always cut off the power supply to the rock drill before performing any repairs to prevent electrical accidents.
- For equipment with an automatic restart feature, ensure this function is locked to prevent accidental startup during repairs.
3. Correct Diagnosis
- Utilize the rock drill’s fault diagnostic system (if available) to help pinpoint the problem.
- Avoid dismantling parts without a thorough understanding of the fault, as this could lead to further issues.
4. Tools and Equipment
- Use the correct tools and equipment for repairs to avoid causing additional damage with inappropriate tools.
- Ensure all tools and equipment meet safety standards.
5. Spare Parts Management
- Ensure an adequate inventory of spare parts for quick replacement of damaged components when needed.
- For critical components, consider using original or equivalent quality replacements.
6. Recording and Feedback
- Keep detailed records of the malfunction occurrence, diagnosis process, and measures taken. This information is crucial for future fault prevention and repair work.
- Provide feedback on the malfunctions to the manufacturer so they can understand the product’s performance and potential issues.
7. Training and Qualification
- Ensure personnel handling the malfunction have the necessary skills and qualifications through professional training.
- Regularly assess skills and provide updated training to ensure repair personnel's skills are up-to-date with the latest repair techniques.
8. Preventive Maintenance
- Implement a regular preventive maintenance plan to reduce the likelihood of malfunctions.
- Perform maintenance according to the equipment’s usage and the manufacturer’s recommendations.
By following these considerations, rock drill malfunctions can be addressed timely, effectively, and safely, while also reducing the risk of future malfunctions.
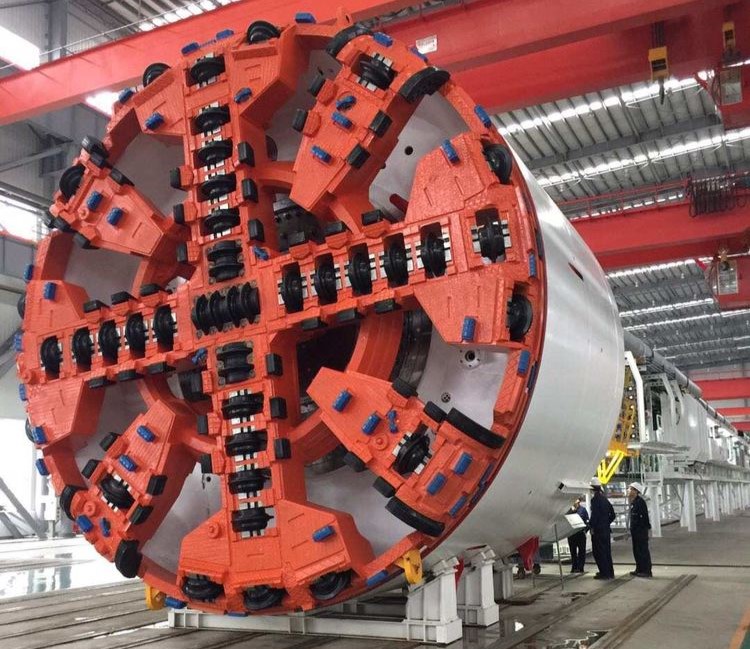
What Breakthroughs Has China Achieved in Shield Machine Technology?
China has made significant breakthroughs in various aspects of shield machine technology. These advancements have not only propelled the rapid development of the Chinese shield machine industry but also had a profound impact on global tunneling construction technology. Here are some specific areas of breakthroughs:
1、Cutterhead Design Technology
Chinese researchers have made important progress in cutterhead design, developing efficient and durable cutterheads with independent intellectual property rights. These cutterheads can adapt to various complex geological conditions, improving the working efficiency and service life of shield machines.
2、Earth Pressure Balance and Slurry Balance Technology
China has achieved critical breakthroughs in Earth Pressure Balance (EPB) and Slurry Balance (TBM) shield machine technology, particularly in adaptability and control technology for complex strata.
3、Intelligent and Automated Control Systems
Chinese shield machine companies have made significant advancements in the development of intelligent control systems, achieving precise positioning, intelligent monitoring, and remote control of shield machines, thereby enhancing construction safety and efficiency.
4、Environmental Protection and Energy-saving Technology
In terms of environmental protection and energy-saving, the development of Chinese shield machine technology focuses on reducing energy consumption and emissions during construction, such as adopting electric drive systems and optimizing cooling systems, thus minimizing environmental impact.
5、Large Diameter Shield Machine Technology
China has successfully developed large diameter shield machines, with diameters exceeding 15 meters. These machines can meet the needs of large projects such as urban rail transit and cross-sea tunnels, showcasing China's manufacturing prowess in the field of large diameter shield machines.
6、Adaptability to Complex Geological Conditions
Chinese shield machine technology has achieved broad adaptability to different geological conditions, including hard rock, soft soil, and composite strata, allowing stable construction in extreme geological environments.
7、Customized and Modular Design
Based on the characteristics of different projects, Chinese shield machines offer customized and modular solutions, enabling flexible configuration to meet personalized construction needs.
8、International Cooperation and Technology Export
Chinese shield machine enterprises actively participate in international cooperation. Through technology export and project contracting, they promote Chinese shield machine technology in the global market, enhancing the international influence of the Chinese shield machine industry.
9、After-sales Service and Technical Support
Chinese shield machine companies have established comprehensive after-sales service systems, providing all-round technical support and maintenance services to ensure the long-term stable operation of shield machines.
These technological breakthroughs have not only improved the overall level of the Chinese shield machine industry but also provided more efficient, safer, and environmentally friendly construction solutions for global tunneling projects. With continuous technological progress and sustained industry development, it is expected that Chinese shield machine technology will achieve more innovative results in the future.
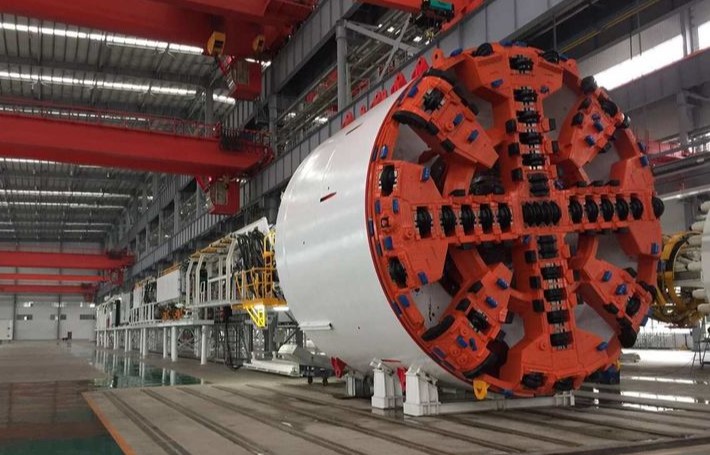
How did China's shield tunneling machine technology develop?
China's shield tunneling machine technology developed through a process of introducing, assimilating, and independently innovating on foreign technologies. In the early 1990s, China began importing advanced shield tunneling machine technology from abroad, which was then absorbed and re-innovated. Initially, shield tunneling machines were mainly imported, which was expensive and difficult to maintain. To change this situation, the Chinese government took a series of measures to encourage domestic enterprises and research institutions to strengthen independent research and development (R&D) and technological innovation.
On the policy level, the Chinese government introduced a series of supportive measures for the shield tunneling machine industry, including financial subsidies and tax incentives, providing a favorable development environment for enterprises. At the same time, the government strengthened the regulation and management of the shield tunneling machine industry, promoting healthy and orderly development.
At the enterprise level, Chinese shield tunneling machine companies continuously improved the performance and quality of their products by introducing advanced foreign technology, strengthening independent R&D, and technological innovation. Some companies have acquired the capability to independently develop and manufacture high-end shield tunneling machines. Their products not only meet the domestic market demand but are also exported overseas, making them strong competitors in the international market.
At the research institution level, Chinese research institutions have made a series of significant breakthroughs in the R&D of shield tunneling machine technology. They have conducted in-depth studies on the working principles, materials, and processes of shield tunneling machines, developing core technologies and key components with independent intellectual property rights, providing strong support for the industry's development.
Additionally, China has emphasized industry-university-research collaboration to promote the transformation and industrialization of research achievements. By establishing collaboration platforms, exchanges and cooperation between enterprises, universities, and research institutions are facilitated, jointly tackling technical challenges and driving continuous innovation and development in shield tunneling machine technology.
After years of effort, China’s shield tunneling machine technology has made significant progress. It not only dominates the domestic market but also holds a competitive position in the international market. In the future, with continuous technological advancements and sustained industry development, it is believed that China’s shield tunneling machine technology will achieve even greater success, contributing more significantly to global tunnel construction.
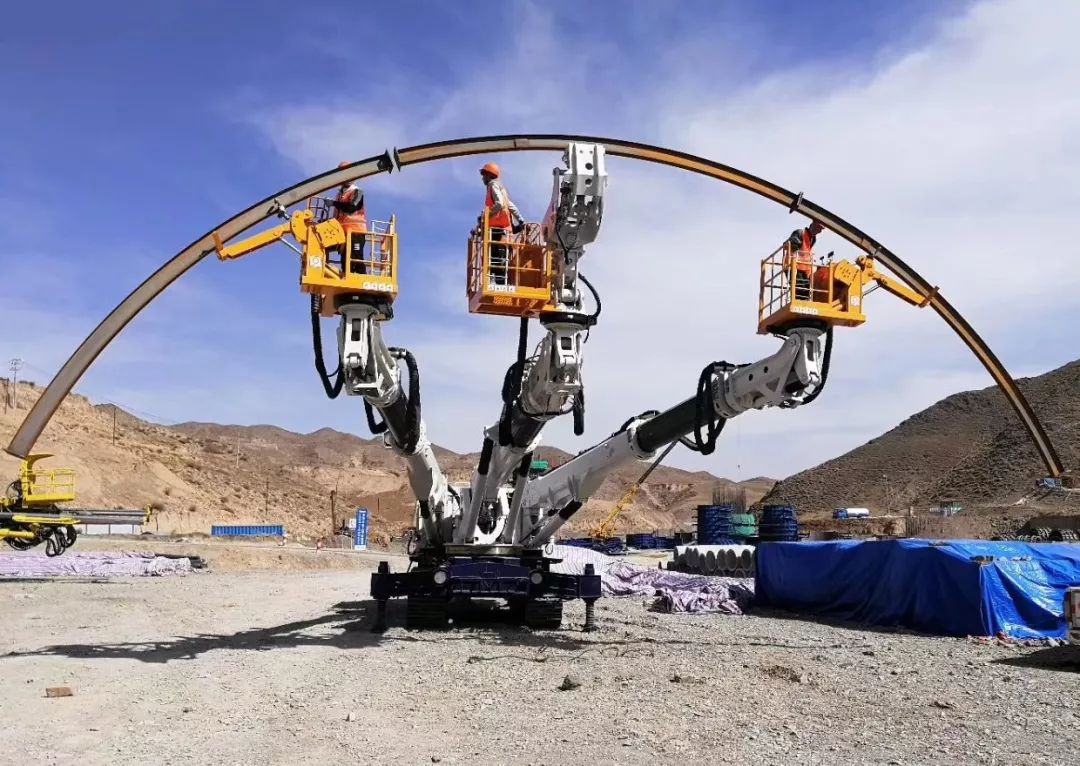
Tunnel Three-Arm Arch Installation Trolley: A High-Efficiency, Safe Tunnel Construction Equipment
In modern tunnel construction, the three-arm arch installation trolley is a high-efficiency, safe construction equipment. It is primarily used for the installation of arches inside tunnels, significantly improving construction efficiency and quality through precise control and stable support.
The three-arm arch installation trolley features a unique structural design, comprising three main parts: the main structure, mechanical arms, and the installation platform. The main structure serves as the foundation of the trolley, providing stable support; the mechanical arms are responsible for moving and positioning the arches; and the installation platform is where workers operate, equipped with the necessary tools and equipment.
The working principle of the trolley involves an electric drive system that controls the movement of the mechanical arms, accurately placing the arches in the designated positions. Meanwhile, workers on the installation platform can perform welding, fastening, and other operations to ensure the quality of the arch installation.
Compared to traditional manual installation methods, the three-arm arch installation trolley has significant advantages. Firstly, it greatly improves construction efficiency and reduces labor input. Secondly, due to the stability and precision of the trolley, it can significantly reduce construction risks and enhance construction quality. Lastly, the trolley can adapt to tunnel construction needs of different diameters and lengths, offering high versatility.
In practical applications, the three-arm arch installation trolley has become an indispensable piece of equipment in tunnel construction. It not only improves construction efficiency but also provides a safe working environment for construction personnel. With continuous technological advancements and innovations, it is believed that the three-arm arch installation trolley will become more intelligent and automated in the future, contributing even more to tunnel construction.
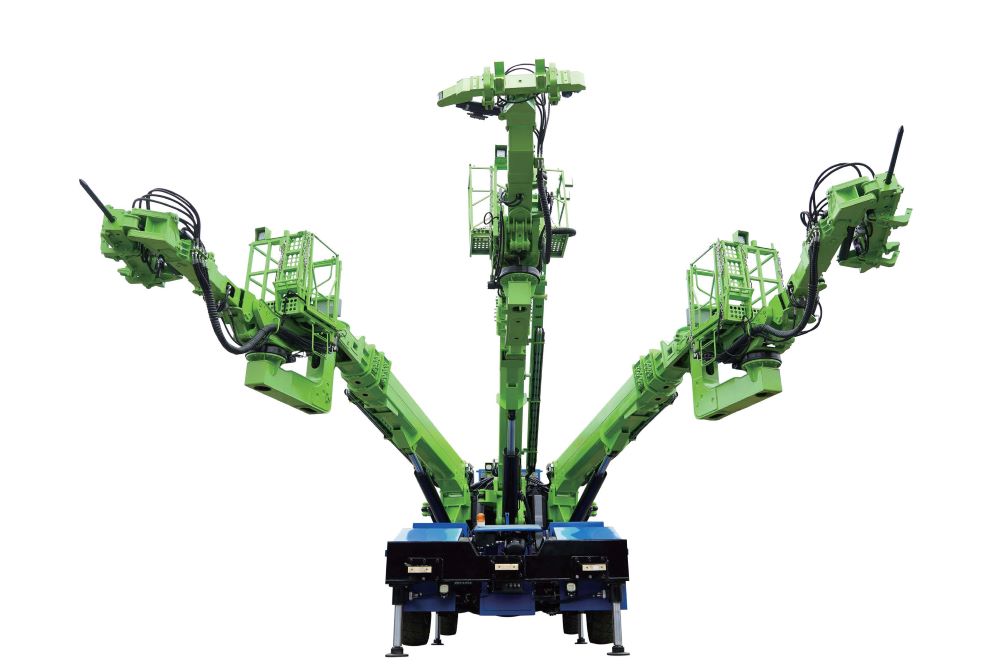
Three-Arm Arch Installation Trolley: An Indispensable Role in Bridge and Tunnel Construction
The three-arm arch installation trolley plays an irreplaceable role in the construction of bridges, tunnels, and other large structures. As a crucial piece of modern construction equipment, its unique structure and outstanding performance significantly enhance construction efficiency while ensuring quality and safety, making it an essential part of contemporary architectural engineering.
Core Advantages: Stability and Flexibility
The primary advantages of the three-arm arch installation trolley lie in its stability and flexibility. Its distinctive three-arm design allows the trolley to maintain stability in complex construction environments, effectively resisting various external interferences and pressures. This stability ensures precision and reliability throughout the construction process, providing a safe and efficient working platform for construction personnel. Additionally, the trolley's flexibility is evident in its adjustability and mobility. Thanks to meticulous design and manufacturing, the trolley can be quickly adjusted and moved according to construction needs, saving significant time and boosting efficiency.
Efficiency and Economic Benefits
Beyond stability and flexibility, the three-arm arch installation trolley is also characterized by its efficiency and economic benefits. It utilizes advanced materials and manufacturing techniques, resulting in a lightweight design that reduces the burden on the construction site. Its modular design facilitates easy disassembly and assembly, reducing maintenance costs. Furthermore, the trolley's efficient performance minimizes labor input and shortens construction periods, lowering overall project costs and achieving a win-win situation for both economic and social benefits.
Adaptability and Expandability
The three-arm arch installation trolley also boasts excellent adaptability and expandability. It can be customized and modified to meet diverse construction requirements, performing well in high-altitude, low-temperature, high-temperature, or humid environments. This adaptability ensures the trolley's exceptional performance in various types of construction projects, demonstrating its robust vitality.
Future Development and Prospects
With continuous technological advancements and innovations in the construction industry, the three-arm arch installation trolley will continue to play a vital role in the future. It will integrate with new materials and technologies to continually enhance its performance and functions. For instance, the introduction of intelligent control systems could enable remote monitoring and intelligent scheduling, further improving construction efficiency and safety. Additionally, as the concept of green building becomes more prevalent, the trolley will evolve towards being more environmentally friendly and energy-efficient, contributing to sustainable development.
Conclusion
In summary, the three-arm arch installation trolley, with its stability, flexibility, efficiency, economic benefits, and excellent adaptability and expandability, plays an indispensable role in modern architectural engineering. Its presence not only drives progress in the construction industry but also contributes positively to the prosperity and development of human society. Looking ahead, we have every reason to believe that with ongoing technological innovation and expanding applications, the three-arm arch installation trolley will continue to create new milestones, injecting fresh vitality into the construction industry's development.
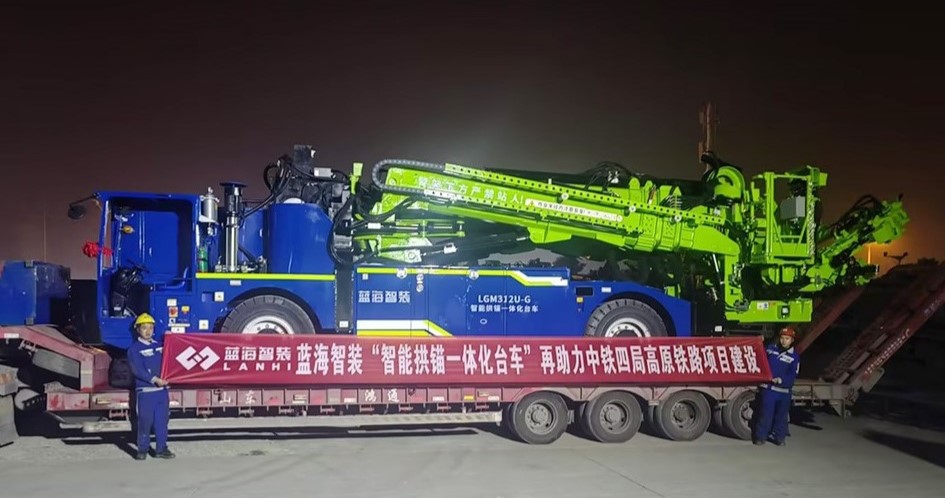
Intelligent Arch Anchor Integrated Trolley: An Efficient Solution for Modern Tunnel Construction
LANHI has introduced the Intelligent Arch Anchor Integrated Trolley, an advanced piece of equipment built on an engineering chassis. This trolley features a dual anchor system and comes with four-wheel steering, four-wheel drive, and bi-directional driving capabilities. It is equipped with a dual-power system that includes both electric and diesel options, allowing for electric-powered construction and diesel emergency operation. Its tri-arm remote control system makes it exceptionally versatile in various tunnel construction scenarios, particularly suitable for prefabricated arch installation and multiple bench construction methods.
The Intelligent Arch Anchor Integrated Trolley integrates several construction processes, including measurement and marking, under-excavation, arch installation, anchor net installation, pre-support, system anchor construction, and optional anchor grouting functions. The tri-arm, tri-gripper basket structure allows the central arm to lift up to 3 tons, enabling all frame erection processes to be completed within an hour.
This equipment incorporates LANHI's independently developed patented technology, offering two installation processes: multi-piece prefabricated arch and multi-piece prefabricated foldable arch. These arches are manufactured outside the tunnel, significantly reducing hazardous operation time and construction risks, thereby greatly improving construction efficiency. The maximum drilling depth of the equipment reaches 4.5 meters, and the left and right arm frames can simultaneously perform foot locking, system anchoring, and pre-support anchoring operations, further enhancing construction flexibility and efficiency.
Additionally, the Intelligent Arch Anchor Integrated Trolley is equipped with an expandable basket, providing more operating space for loading explosives and anchors. The optional grouting system allows for quick grouting operations after anchor installation. The entire set of equipment can be operated by only 3-4 people, whereas traditional methods typically require more than 8 people.
The equipment also includes a breaker and welder, allowing for under-excavation and welding operations during arch installation. The intelligent design features cluster management, positioning functions, video monitoring, intercom functions, warning/alarm functions, data management capabilities, as well as tunnel BIM technology and digital twin, construction report management, tunnel contour scanning, and remote control functions. The integration of these features greatly enhances construction safety, efficiency, and management levels, making LANHI's Intelligent Arch Anchor Integrated Trolley an ideal choice for modern tunnel construction.
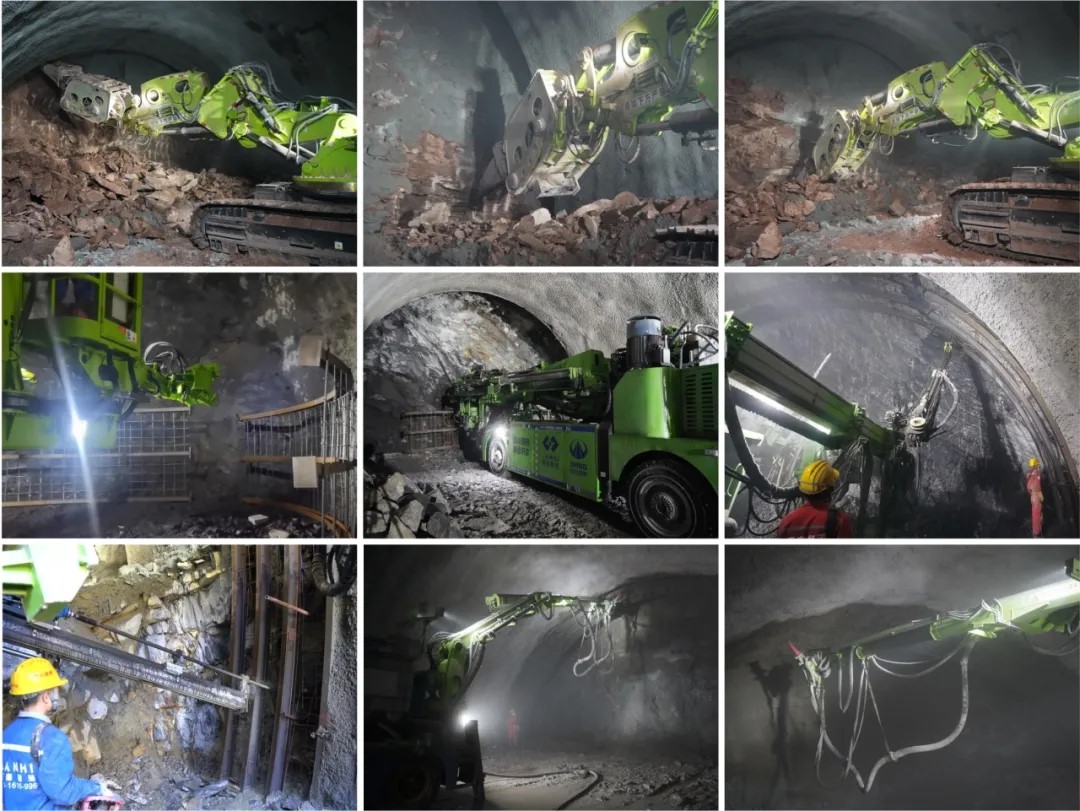
Armored Machinery fight fiercely in Zhen-Guang-LANHI helps Zhen-Guang Expressway to make progress on multiple projects
Spring brings vitality, and with it, significant progress in various construction sites of the provincial key project, Zhen Guang Expressway. LANHI’s "Iron Armored Soldiers" are demonstrating their strength and pioneering spirit, driving major advancements in multiple tunnel projects and creating a dynamic and efficient construction blueprint.
1、Pingchang Tunnel
As a pilot project for fully mechanized equipment construction, the Pingchang Tunnel stretches 5,600 meters and is a long, low-gas tunnel. With a lengthy construction period, poor geological conditions, and high safety risks, LANHI has provided six intelligent pieces of equipment for this project. These include the LG312M intelligent arch installation vehicles and 40F wet spraying manipulators, fully implementing the concept of "mechanization reduces labor, automation replaces labor" by Shudao Group. This has effectively reduced construction safety risks and the number of workers in the tunnel face, significantly improving construction quality and efficiency.
At the beginning of this year, the Pingchang Tunnel, a key project in the C3 section of the Tongguang segment, successfully surpassed the 2,000-meter mark in its advancement.
2、Baiyi No. 2 Tunnel
The Baiyi No. 2 Tunnel project is a control project from Yuejia Town to Hanshui Town on the Zhen Guang Expressway. With significant construction difficulty, LANHI’s multifunctional tunneling machine was brought in for non-explosive mechanical excavation, wireless remote control operation, minimal surrounding rock disturbance, high intelligence, low dust, and the ability for two workers to complete the excavation. This has effectively reduced construction safety risks and the number of workers.
At the C6 section of the Baiyi No. 2 Tunnel construction site, workers are remotely operating LANHI's multifunctional tunneling machine, pushing forward with the tunneling work vigorously.
3、Guangna Tunnel
The Guangna Tunnel, with a length of 3,426 meters, consists mainly of siltstone and sandstone and has surrounding rock grades of IV and V. It is the only high-gas tunnel along the entire route, facing high risks such as high gas, shallow burial, landslides, water inrush, and crossing under a reservoir. LANHI’s LG312M intelligent arch installation vehicles were brought in to support mechanized operations, enhancing safety at the tunnel face, accelerating construction progress, and reducing labor costs, laying a solid foundation for early completion.
Currently, the Guangna Tunnel in the C1 section of the Tongguang segment has achieved a cumulative bi-directional advance of over 3,000 meters.
4、Ranjiaba Tunnel
The right line of the Ranjiaba Tunnel is 1,736 meters long, and the left line is 1,743 meters long, located in Tiexi Town, Tongjiang County. It is a low-gas tunnel with surrounding rock grades of IV and V. The entrance location is steep and has a large height difference. LANHI’s LG312M intelligent arch installation vehicles have been deployed to ensure smooth tunnel entrance construction.
In mid-April, the right entrance of the Ranjiaba Tunnel in the B2 project of the Chuanwang segment successfully entered, marking another acceleration in the construction of the B2 project.
To date, LANHI has continuously supported the construction of over 20 tunnels on the Zhen Guang Expressway, deploying more than 30 intelligent pieces of equipment, including multifunctional tunneling machines, intelligent arch/anchor installation vehicles, and wet spraying manipulators. Moving forward, LANHI will continue to support mechanized construction and lead with intelligent operations, further promoting the integration of innovative technologies and construction practices, aiding in the completion and operational efficiency of the entire Zhen Guang Expressway by 2026, thus empowering high-quality economic development.
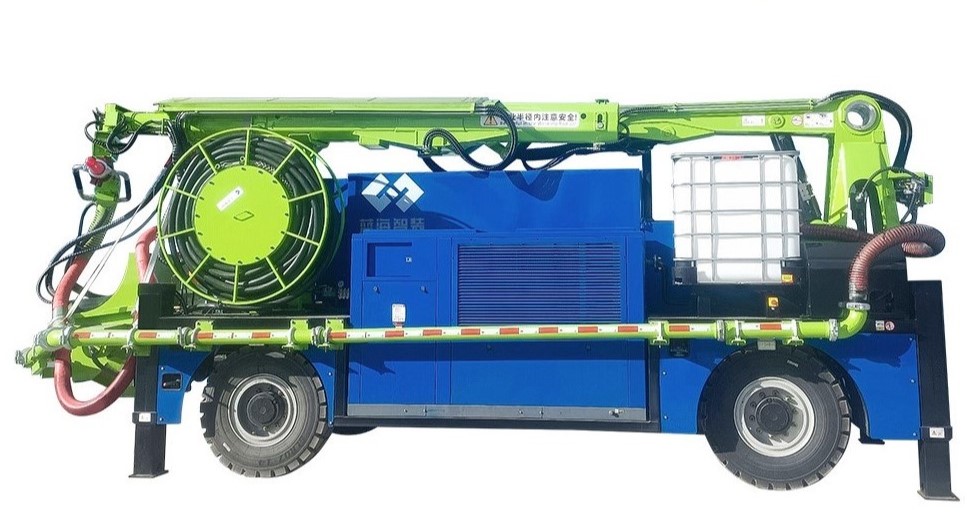
LANHI Wet Spraying Robot: High-Efficiency Construction Solutions for Multiple Fields
The LANHI wet spraying robot is a highly efficient construction device suitable for various engineering types, especially for full-section, half-section, and multi-step shotcrete support in tunnel, hydraulic, municipal, and road and bridge projects. With its outstanding performance and reliability, it has become an essential tool in modern engineering construction.
1. High-Efficiency Spraying with Excellent Performance
The LANHI wet spraying robot boasts a maximum spraying volume of up to 40 cubic meters per hour, ensuring high-efficiency progress in large-scale projects. The equipment is designed with a focus on construction quality, providing stable and reliable spraying effects. It is not prone to clogging, has a low rebound rate, and reduces dust during the construction process, effectively protecting both the environment and workers' health.
2. Multiple Models to Adapt to Different Construction Environments
To meet the needs of construction in different altitudes, the LANHI wet spraying robot offers several model options:
Highland Model: Specifically designed for high-altitude construction, equipped with a high-altitude air compressor, suitable for construction environments above 2000 meters, ensuring the equipment operates normally under highland conditions.
Plain Model: Suitable for construction environments below 2000 meters, equipped with a plain-type air compressor, eliminating the need for external air sources, solving the problem of insufficient on-site air supply, and significantly improving construction convenience, efficiency, and flexibility.
The LANHI wet spraying robot is equipped with a dual-speed accelerator tank with a capacity of 1.5 cubic meters, greatly enhancing the efficiency of shotcrete operations in exceptionally large and long tunnels. The equipment features a dual-mode design (diesel and electric). Regular construction can be performed in electric mode, while in emergency situations, it can switch to diesel mode, ensuring continuity and flexibility in emergency handling.
The LANHI wet spraying robot, with its high efficiency, stability, and strong adaptability, has become an ideal choice for various engineering constructions, providing reliable equipment support and high-quality construction outcomes for construction parties.