
How to judge whether the impact frequency of the pneumatic impact bolter is too high?
How to judge whether the impact frequency of the pneumatic impact bolter is too high? The following methods can help to judge whether the impact frequency of the pneumatic impact bolter is too high:
1. Observe the wear of parts: Frequent and high impact frequency will cause the moving parts, such as pistons and connecting rods, to wear more. If you find that the wear rate of these parts is abnormally fast, it may be caused by too high impact frequency.
2. Feel the vibration and noise: Too high impact frequency often causes the machine to produce strong vibration and loud noise. If the operator feels that the vibration is abnormally strong and the noise is too loud during operation, which exceeds the normal acceptable range, it may mean that the impact frequency is too high.
3. Check energy consumption: Too high impact frequency will increase the consumption of gas source. By monitoring the use of gas source, if it is found that the consumption rate is significantly higher than the normal level, it may be that the impact frequency is too high.
4. Evaluate the drilling quality: Too high impact frequency may lead to a decline in drilling quality, such as uneven hole wall and excessive wear of drill bit. If such a situation occurs, and other factors are excluded, it should be considered whether the impact frequency is too high.
5. Comparison of work efficiency: Under the same working conditions, if the drilling speed does not increase significantly, but the equipment failure frequency increases, it may be caused by unreasonable and too high impact frequency settings.
Too high impact frequency of pneumatic impact anchor bolter may have the following effects:
1. Increased wear of parts: Too high impact frequency will cause the moving parts inside the machine, such as pistons and connecting rods, to bear greater impact and friction, resulting in faster wear and shortening the service life of parts.
2. Increased energy consumption: Too high impact frequency often means that more gas source energy supply is required, which increases energy consumption and increases the cost of use.
3. Reduced working stability: It may cause the machine to produce greater vibration and noise, affecting the operator's operating comfort and work efficiency, and may also reduce the overall stability and reliability of the equipment.
4. Affected drilling quality: Too high impact frequency may not give the drill bit enough time to cut the rock, resulting in a rough and irregular surface of the borehole, and may even cause problems such as hole wall collapse, affecting the drilling quality.
5. The equipment is prone to heat: Rapid and frequent impacts will generate more heat. If the heat is not dissipated in time, it may cause the equipment to overheat, affecting its normal operation and service life.
6. Damage to connected parts: Strong and frequent impacts may cause excessive stress and fatigue damage to other parts connected to the anchor bolter, such as drill rods, connecting hoses, etc., increasing the risk of damage.

How does an anchor drill work? Working process of an anchor drill
An anchor drill is a drilling device specially used in geotechnical engineering. It is mainly used to drill holes in rocks or soil in order to install anchor rods or anchor cables to reinforce structures such as slopes, tunnels, and dams. So how does an anchor drill work? Let's talk about the working process of an anchor drill.
1. Positioning and fixing: First of all, the anchor drill needs to accurately locate the drilling position according to the design requirements, and stably fix the machine on the working surface through its own support system (such as legs).
2. Drilling: Start the power system of the drilling rig and drive the drill rod and drill bit to rotate by hydraulic or electric means. The drill bit is usually made of cemented carbide and has high wear resistance and cutting ability. While the drill bit rotates, it applies downward pressure through the propulsion mechanism to enable the drill bit to cut into the rock and soil layer.
3. Deslagging: As the drill bit goes deeper, the rock and soil are broken into small pieces. These debris need to be discharged from the hole in time to ensure the smooth progress of drilling. Anchor drilling rigs are usually equipped with a slag removal system, which can blow the debris out of the drill pipe through compressed air generated by an air compressor, or use a mud pump to bring the debris out through mud circulation.
4. Depth control: During the drilling process, the operator needs to monitor the depth of the drill hole to ensure that the designed depth is reached. This is usually achieved through a depth gauge or an electronic control system.
5. Drilling completion: When the hole reaches the predetermined depth, the drilling is stopped and the drill pipe and drill bit are removed from the hole. At this time, the hole may need to be cleaned to ensure the smooth installation of the subsequent anchor or anchor cable.
6. Installing anchor or anchor cable: After the drilling is completed, the prefabricated anchor or anchor cable is inserted into the hole, and then grouting material (such as cement slurry) is injected to fix the anchor or anchor cable and provide the required bearing capacity.
The working efficiency and performance of the anchor drilling rig are affected by many factors, including the power of the rig, the material and design of the drill bit, and the geological conditions of the working surface. In actual applications, operators need to select appropriate drilling rigs and drilling tools according to specific circumstances and adopt appropriate operating methods to ensure project quality and safety.

What are the common forms of tunnel support? Introduction to several common forms of tunnel support
What are the common forms of tunnel support? The common forms of tunnel support mainly include the following:
1. Shotcrete Support: High pressure concrete is sprayed onto the tunnel wall to form a strong protective layer. Shocked concrete can quickly cover the surface of surrounding rock, seal rock cracks, prevent weathering and water erosion, and increase the overall stability of surrounding rock. It can be used as temporary or permanent support.
2. Steel Arch Support: A frame structure made of steel or steel grating, installed inside the tunnel to provide support for the surrounding rock. Steel frame support can be used alone or in combination with shotcrete to form a more robust composite support system.
3. Rock Bolting or Cable Anchoring: By drilling holes in the surrounding rock, inserting high-strength steel bars or steel strands, and fixing them with materials such as cement slurry, the internal stress of the surrounding rock is transmitted to the deep and stable rock mass, thereby improving the self-supporting capacity of the surrounding rock.
4. Lining Support: A permanent structure made of poured concrete or other materials after tunnel excavation, used to withstand long-term ground pressure and water pressure, ensuring the stability and durability of the tunnel. The lining can be cast-in-place concrete, prefabricated concrete pipe segments, or masonry structures.
5. Prefabricated Support: Assemble precast concrete slabs, arches, and other components inside the tunnel to form a support structure. This method is suitable for tunnel projects with good conditions and can accelerate the construction progress.
6. Grille Support: A grid like structure welded from steel bars or steel bars, usually used in combination with shotcrete to form a lightweight support system, suitable for initial support of weak surrounding rock.
7. Soil Nailing: Drilling holes in soil or soft rock, inserting steel bars or pipes, and tightly bonding them with the surrounding soil through grouting to form an effect similar to anchor rods, enhancing the overall stability of the soil.
8. Freezing Method: In special circumstances, such as crossing aquifers or weak strata, artificial freezing of the strata can be used to temporarily harden them for tunnel excavation and support.
9. Grouting reinforcement: Injecting cement slurry or other chemical slurry into the surrounding rock to fill cracks, improve the compactness and bearing capacity of the surrounding rock, is a commonly used auxiliary support method.
These support forms can be used separately or in combination according to specific engineering requirements and geological conditions to achieve the best support effect.

Tunnel concrete wet spraying machine, a construction tool for the key link of initial support
In modern tunnel construction, concrete wet spraying machine, as an efficient construction equipment, plays a vital role, especially in the initial support stage. Initial support is a basic and key work in tunnel construction. Its purpose is to quickly support the surrounding rock after tunnel excavation to prevent deformation and collapse of the surrounding rock and provide a safe and stable working environment for subsequent construction. The emergence of concrete wet spraying machine has greatly improved the construction efficiency and quality of initial support and has become a "weapon" in tunnel construction.
Working principle of concrete wet spraying machine
Concrete wet spraying machine is a construction equipment that fully mixes concrete materials with water before spraying. It uses a high-pressure pump to transport the pre-mixed concrete slurry to the nozzle, and then sprays the concrete onto the construction surface through the compressed air at the nozzle. Compared with traditional dry spraying or semi-wet spraying, this construction method has the advantages of uniform mixing, low rebound rate, less dust and high construction efficiency.
Application in initial support
In the initial support of tunnels, wet spraying concrete machines are mainly used to spray concrete to form an initial support layer. This layer of concrete can not only immediately support the surrounding rock and prevent deformation of the surrounding rock, but also form a good bond with the surrounding rock to enhance the stability of the surrounding rock. In addition, the high density and good waterproof performance of wet spraying concrete also enable the initial support layer to effectively prevent the infiltration of groundwater, providing a good foundation for the subsequent waterproof layer construction.
Advantages of wet spraying concrete machines
1. High efficiency: wet spraying concrete machines can achieve fast and continuous concrete spraying, greatly improving the construction speed of initial support and shortening the tunnel construction period.
2. High quality: wet spraying concrete has good workability and density, can form a uniform and dense support layer, and improve the support effect.
3. Environmental protection: The wet spraying process reduces dust and rebound during the construction process, reduces the impact on the health of construction workers, reduces material waste, and is more environmentally friendly.
The application of wet concrete spraying machine in the initial support construction of tunnels not only improves construction efficiency and quality, but also reflects the advanced and environmentally friendly nature of modern tunnel construction technology.

Working principle, application and advantages of hydraulic concrete wet spraying machine
Hydraulic concrete wet spraying machine is a mechanical equipment widely used in engineering fields such as tunnel construction and mine roadway reinforcement. Its main function is to transport and spray concrete onto the sprayed surface through a hydraulic system, forming a stable support layer. This article will provide a detailed introduction to the working principle and various components of the hydraulic concrete wet spraying machine.
Working principle of hydraulic concrete wet spraying machine
The core working principle of hydraulic concrete wet spraying machine is to use the thrust generated by the hydraulic system to transport concrete from the hopper to the nozzle and spray it onto the sprayed surface. The specific process is as follows:
1. Hydraulic pump operation: After the hydraulic pump is started, it pushes the piston in the working cylinder of the oil cylinder to perform reciprocating motion.
2. Concrete transportation: Under the push of the piston, concrete is transported through the conveying pipeline to the mixing pipe.
3. Compressed air action: At the mixing pipe, compressed air further dilutes the concrete and transports it to the nozzle through the pipeline.
4. Addition of quick setting agent: Add quick setting agent in a certain proportion at the nozzle to quickly set the concrete after spraying onto the sprayed surface.
5. Spray molding: Concrete is uniformly sprayed onto the sprayed surface under the combined action of compressed air and quick setting agent, forming the required support layer.
Application and advantages of hydraulic concrete wet spraying machine
Hydraulic concrete wet spraying machine is widely used in various projects that require concrete spraying due to its high efficiency and stable performance. The main advantages include:
-Easy to operate: The equipment has a high degree of automation, is easy to operate, and reduces manual intervention.
-Good spraying effect: The concrete is sprayed evenly, with strong bonding force, ensuring construction quality.
-Strong adaptability: Suitable for various complex construction environments, especially tunnels and underground engineering.
-Easy maintenance: The device has a compact structure, is easy to maintain and upkeep, and has low operating costs.
As an advanced construction equipment, hydraulic concrete wet spraying machine plays an important role in engineering construction with its unique working principle and superior performance. By reasonable use and maintenance, construction efficiency and quality can be significantly improved, providing strong guarantees for the smooth progress of engineering projects.
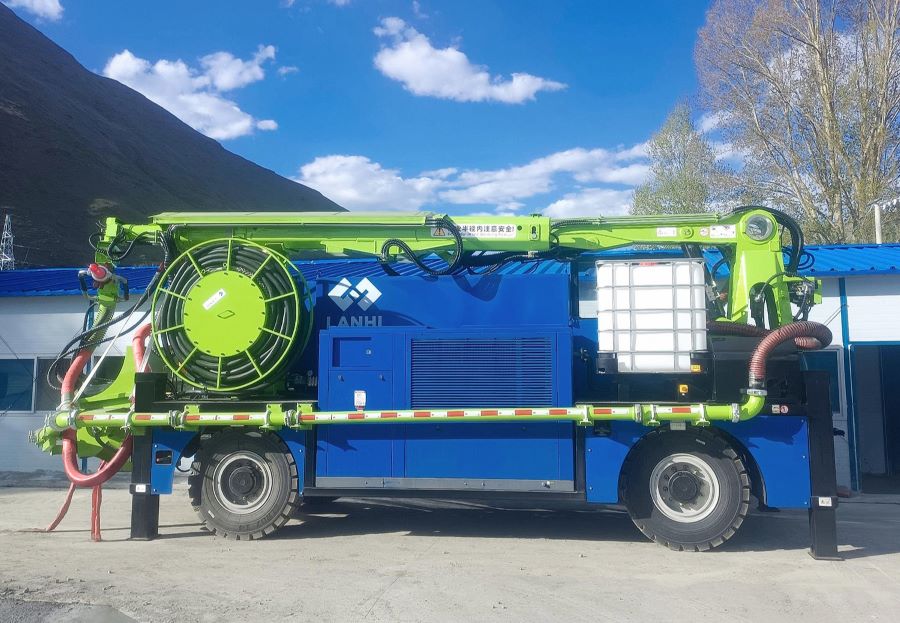
Efficient initial support equipment for modern tunnel construction: advantages and applications of concrete wet spraying robotic arms
Concrete wet spraying robotic arm is an important equipment for initial support operations in modern tunnel construction, and its performance in improving construction efficiency and working environment is particularly outstanding. This article will explore in detail the advantages and wide applications of concrete wet spraying robotic arms in initial concrete spraying.
1. High degree of mechanization and significant improvement in construction efficiency
The concrete wet spraying robotic arm replaces traditional manual spraying with mechanized operations, significantly improving construction efficiency. Compared to manual operation, wet spraying robots can complete larger areas of spraying operations in a shorter time. This not only reduces construction time, but also lowers labor costs, allowing construction units to complete projects within a shorter period of time.
2. Large spraying range and strong construction flexibility
The wet spraying robotic arm has a wide spraying range and can complete large-scale spraying without the need to set up a spraying operation platform. Its flexible operational performance enables the equipment to adapt to various complex tunnel environments, especially in high-altitude and difficult to access areas, making the advantages of wet spraying robotic arms more apparent. The fast spraying speed and wide coverage greatly shorten the time for initial concrete support in the tunnel.
3. High quality spraying effect, high material utilization rate
The concrete sprayed by the wet spraying robot has good adhesion and compactness, with low rebound rate, which not only improves the quality of sprayed concrete, but also reduces the waste of raw materials. In traditional spraying operations, the rebound rate of concrete is high and material waste is serious. However, wet spraying robots significantly reduce material loss and improve economic benefits through precise spraying control.
4. Improve the working environment and enhance construction quality
The use of concrete wet spraying robotic arms can liberate workers from heavy physical labor and harsh construction environments. By using modern scientific methods to automate the dosage of accelerators, the construction quality has been significantly improved. At the same time, the use of wet spraying robots greatly improves the working environment on construction sites, reduces dust and noise pollution, and makes construction more humane, scientific, and mechanized.
Concrete wet spraying manipulator, as an efficient and environmentally friendly initial support equipment, is increasingly being used in tunnel construction due to its high degree of mechanization, high construction efficiency, good spraying effect, and high material utilization rate.
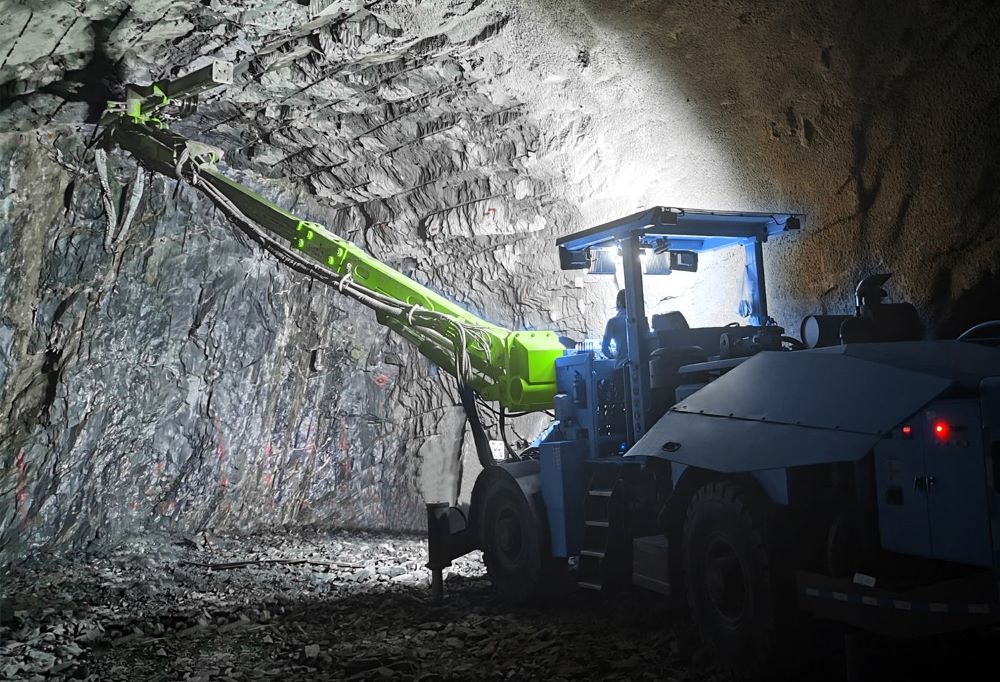
What are the mining drilling equipment? The purpose and introduction of common mining equipment
Mining drilling equipment is an indispensable and important tool in mining operations, mainly used for geological exploration, ore body mining, tunnel excavation, grouting in goaf, gas drainage and other operations. With the development of technology, mining drilling equipment is constantly upgrading towards high efficiency, intelligence, and environmental protection. Next, we will delve into mining drilling equipment from the perspectives of equipment types, working principles, and development trends.
Common mining drilling equipment:
Impact drilling rig: using the up and down reciprocating motion of the impactor to drill holes; Suitable for drilling in hard and extremely hard rocks.
Down the hole drilling rig: The drill bit impacts the bottom of the hole, and the equipment is small in size and easy to move; Mainly used for mid to deep hole drilling in mines, quarries, and other places.
Fully hydraulic drilling rig: driven by a hydraulic system, with high efficiency and flexible operation; Has a high degree of automation and work efficiency.
Drilling truck: a comprehensive equipment that integrates drilling, loading, and support functions; Mostly used for excavation and drilling blasting operations in mining.
Impact drilling rig: It uses hammering to drive drill rods and bits into rock formations, suitable for drilling in hard rock formations.
Rotary drilling rig: By rotating the drill rod and using the drill bit to cut rocks, it is suitable for drilling soft and hard rocks.
Down the hole hammer drilling rig: Combining the principles of impact and rotation, the drill bit is equipped with a hammering device inside, suitable for drilling various rock formations.
Hydraulic drilling rig: using high-pressure water flow to wash rocks, suitable for drilling in soft rock layers.
Pneumatic drilling rig: using compressed air to drive drilling tools, suitable for drilling operations in open-pit mines.
Geological core drilling rig: used to obtain core samples of underground rocks for analysis of geological structure and mineral distribution.
As a key equipment for mining, the technological progress and innovation of mining drilling equipment will have a profound impact on the efficiency, safety, and environmental protection of mining operations. In the future, with the continuous advancement of technology, mining drilling equipment will develop towards greater efficiency, intelligence, and environmental friendliness, providing stronger technical support for mining operations.
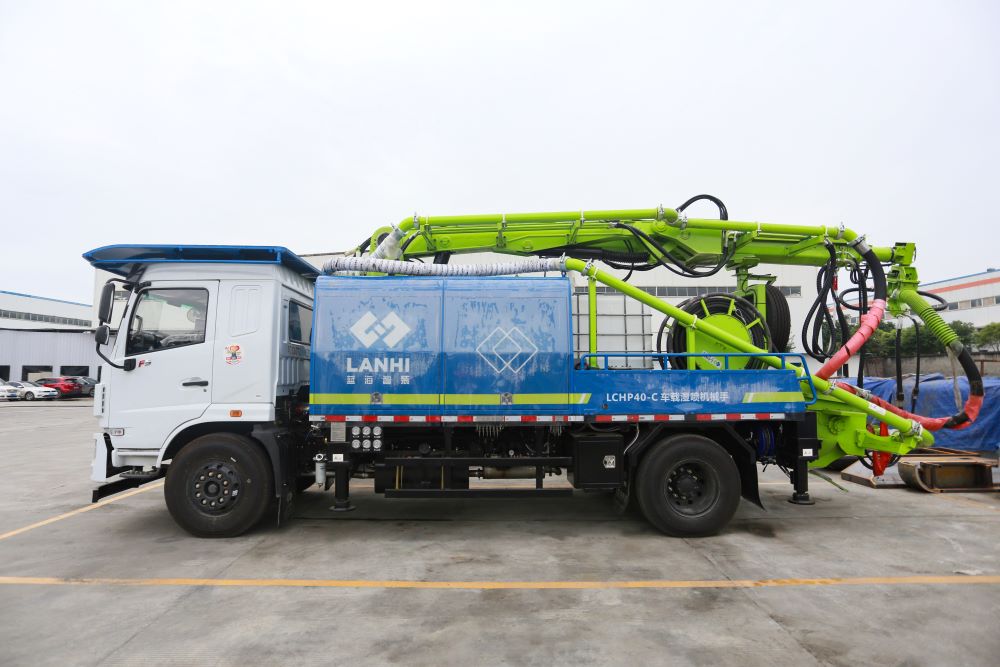
The advantages of concrete wet spraying machine in construction and its positive impact on engineering quality
In modern architecture and infrastructure construction, concrete spraying machine plays an indispensable role as a key equipment. It not only improves construction efficiency, but also greatly improves the working environment and ensures the health of workers. Concrete sprayers are mainly divided into two categories: concrete dry sprayers and concrete wet sprayers. This article will focus on exploring the advantages of concrete wet spraying machines in construction and their positive impact on engineering quality.
The perfect combination of high efficiency and low rebound
The concrete wet spraying machine is known for its excellent construction efficiency and low rebound. Compared to traditional dry spraying techniques, the rebound rate of wet spraying machines can be significantly reduced to below 10%, which means that more concrete can accurately adhere to the target surface, reducing material waste and accelerating construction progress. This efficiency improvement is of great significance for large-scale projects such as mining tunnels, railway and highway tunnels, water conservancy culverts, underground engineering, high-rise building excavations, military engineering, etc. It can significantly shorten the construction period and reduce project costs.
Guardian of environmental friendliness and worker health
By using wet spraying technology, the dust concentration generated by the concrete spraying machine during the construction process is significantly reduced, effectively improving the working environment and reducing potential hazards to workers' health. In wet spraying operations, the water cement ratio is easy to accurately control, ensuring the atomization degree of concrete and improving the quality and uniformity of sprayed concrete. This technological innovation not only protects the respiratory system of workers and avoids potential health problems caused by long-term inhalation of dust, but also provides a more comfortable and safe working environment for construction workers.
The widespread application of concrete wet spraying machines not only reflects the progress of modern construction technology, but also embodies environmental protection and worker health care. With the continuous development of technology, the performance of concrete wet spraying machines will be further improved, and their applications in the fields of construction and engineering will become more widespread. In the future, we can expect concrete wet spraying machines to play a greater role in improving construction efficiency, ensuring project quality, protecting the environment, and safeguarding workers' health.
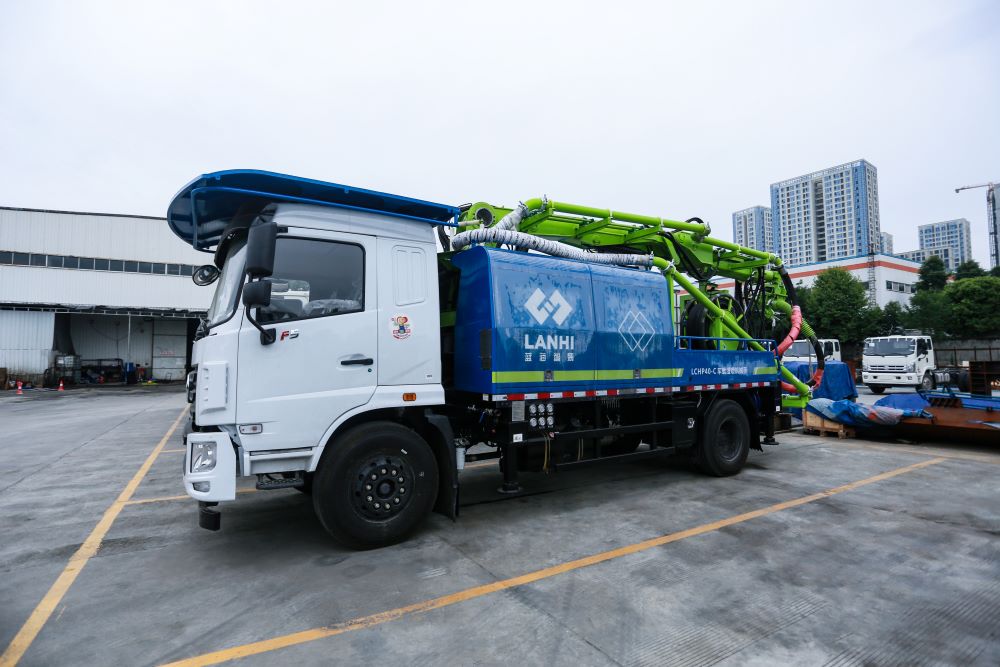
The emergence of concrete wet spraying trolley has ushered in a new era for tunnel support construction technology
In modern infrastructure construction, tunnel engineering is an important link connecting cities and regions. With the continuous advancement of technology, construction equipment is also constantly innovating, and the concrete wet spraying trolley is one of the outstanding ones. It is gradually becoming a strong force in the field of tunnel construction with its excellent performance and advantages.
Efficient construction, stable quality
The concrete wet spraying trolley integrates advanced spraying technology and automation control system, which can achieve continuous and stable concrete spraying, greatly improving construction efficiency. Compared with traditional small wet sprayers, it is not only flexible and fast in operation, but also more convenient to operate. It can quickly adapt to different construction environments and needs, significantly shorten the construction period, and ensure project progress.
Construction safety and environmental friendliness
Safety is always the primary consideration during the construction process. The design of the concrete wet spraying trolley fully considers the safety of operators, reduces manual intervention through automated control, and lowers operational risks. At the same time, the dust and noise generated during the construction process are relatively low, providing a safer and more comfortable working environment for operators and reflecting a friendly attitude towards the environment.
Improve concrete quality and reduce labor intensity
The concrete wet spraying trolley adopts wet spraying technology, which can effectively improve the compactness and strength of concrete, and ensure the quality of tunnel lining. In addition, automated operations greatly reduce the labor intensity of operators, making the construction process more humane, improving work efficiency, while also reducing labor costs and enhancing economic benefits.
The emergence of concrete wet spraying trolley marks a new era in tunnel construction technology. It not only solves the problems of traditional concrete spraying machines, but also brings revolutionary changes to the construction field with higher construction efficiency, more stable construction quality, safer construction environment, and lower labor intensity. In the future, with the further development of technology, concrete wet spraying trucks are expected to demonstrate their unique charm in more fields and become a key force in promoting efficient, safe, and environmentally friendly infrastructure construction.
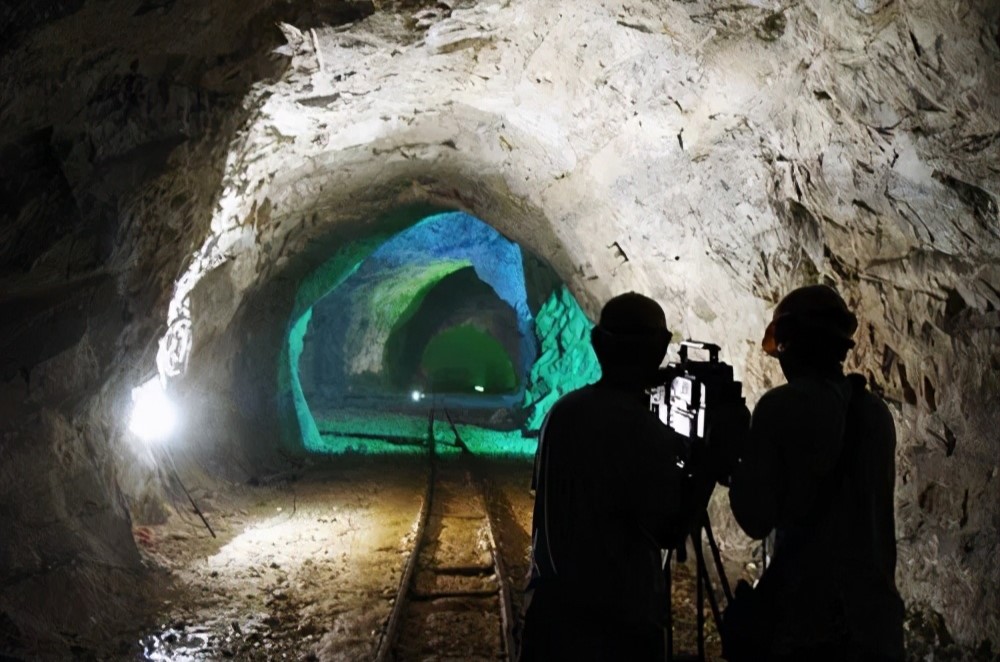
What does' non coal mine mountain 'refer to? What are the non coal mines
Non coal mines, as the name suggests, refer to various types of mines other than coal mines, which mainly extract resources including metallic minerals, non-metallic minerals, building materials, and other industrial raw materials. There are various types of non coal mines scattered around the world, providing abundant mineral resources for human society and supporting the development of multiple industries such as industry, construction, electronics, and chemical engineering.
Metal mines
Metal mines mainly mine various types of metal ores, such as:
·Copper mine: Copper is an important industrial metal used in the manufacture of wires, cables, pipelines, and more.
·Aluminum ore: Bauxite is the main source of aluminum, which is widely used due to its lightweight and corrosion resistance.
·Iron ore: Iron ore is the main raw material for steel production, and steel is the basic material for modern industry.
·Gold Mine: Gold is a precious metal used not only in jewelry, but also as an important industrial material and investment tool.
·Silver mine: Silver is also a precious metal used in fields such as electronics, photography, and medicine.
·Lead zinc ore: Lead and zinc are often associated and widely used in batteries, anti-corrosion coatings, alloy manufacturing, etc.
·Tin ore: Tin is used to manufacture solder, alloys, packaging materials, etc.
Non metallic mines
Non metallic mines mainly mine non-metallic ores, including:
·Graphite ore: Graphite is an important raw material for manufacturing pencil leads, electrodes, and refractory materials.
·Quartz ore: Quartz is the main raw material for manufacturing glass, electronic devices, and precision instruments.
·Limestone mine: Limestone is the main raw material for cement production and is also used in industries such as construction and chemical engineering.
·Gypsum mine: Gypsum is used to manufacture gypsum boards, sculptures, building decoration materials, etc.
·Salt mine: Salt is not only a food seasoning, but also an important raw material for industries such as chemical, pharmaceutical, and agriculture.
·Phosphate ore: Phosphate ore is the main raw material for manufacturing fertilizers, food additives, matches, etc.
Building materials mine
Building materials mines mainly extract ores used in the construction industry, such as:
·Granite mine: Granite has a hard texture and is used for construction, carving, road paving, etc.
·Marble mine: Marble has a delicate texture and rich colors, often used for architectural decoration and carving.
·Sandstone ore: Sandstone is the main raw material for concrete and road construction.
The development of non coal mines has a significant impact on the economy, but it also brings environmental and safety challenges. Therefore, reasonable planning, environmentally friendly mining, and safe production are the key to its sustainable development.