
Three grouting technologies for foundation reinforcement and their applications
The stability and bearing capacity of the foundation are crucial factors in construction projects, especially when constructing on soft soil foundations, the application of foundation reinforcement technology is particularly critical. Grouting technology, as an effective means of foundation reinforcement, improves soil properties and improves the bearing capacity and stability of the foundation by injecting specific slurry into the foundation. This article will introduce three common grouting technologies in detail: static pressure grouting, high-pressure jet grouting and composite grouting, and explore their principles, application fields and advantages.
1. Static pressure grouting: split grouting method for foundation reinforcement
Static pressure grouting, also known as split grouting, is mainly used in house construction projects on soft soil foundations. Its principle is to use pressure to inject cement slurry or cement mortar with a larger specific gravity into the foundation. Under the action of pressure, the slurry splits and extends along the minimum principal stress surface or weak stress distribution area in the foundation stress field to form an irregular condensate, squeeze and compact the surrounding soil, reduce soil voids, and increase compression modulus. The slurry condensate plays a skeleton role in the soil, significantly improving the bearing capacity of the foundation while reducing the possibility of settlement and deformation.
2. High-pressure jet grouting method: a pioneer in reinforcement in multiple fields
The high-pressure jet grouting method has been developed since the late 1960s and has been widely used in my country's construction industry, especially in the reinforcement of soft foundations of highways, the reinforcement of mine tunnels and the anti-leakage projects of water conservancy projects. With the acceleration of high-rise building and subway construction, the anti-leakage work of urban deep foundation pits is also increasingly using high-pressure jet grouting technology. This method forms a reinforcement body by high-pressure jetting slurry to enhance the stability of the foundation and is suitable for a variety of geological conditions.
3. Composite grouting method: an innovative technology for pile foundation reinforcement
The composite grouting method is a new reinforcement technology that combines the advantages of high-pressure rotary jet grouting and static pressure grouting, and is mainly used for pile foundation reinforcement. First, the high-pressure rotary jet grouting method is used to form the pile column, and then the static pressure grouting method is used to enhance the rotary jet effect, so that the reinforcement slurry gradually spreads, avoids the solidification and shrinkage of the slurry, and eliminates the grouting blind area. The composite grouting method has a wide range of applications. It can not only reinforce clay, sand and gravel layers, analytical sand layers and silt, but also effectively deal with karst soil caves, showing its strong adaptability under complex geological conditions.
As an important means of foundation reinforcement, the development and application of grouting technology has greatly promoted the technological progress of the construction industry. Static pressure grouting method, high-pressure jet grouting method and composite grouting method have their own characteristics and are suitable for different types of foundation reinforcement projects, providing strong technical support for improving foundation bearing capacity and ensuring the safety of construction projects. With the continuous innovation of technology, grouting technology will play a more important role in the field of foundation reinforcement in the future.
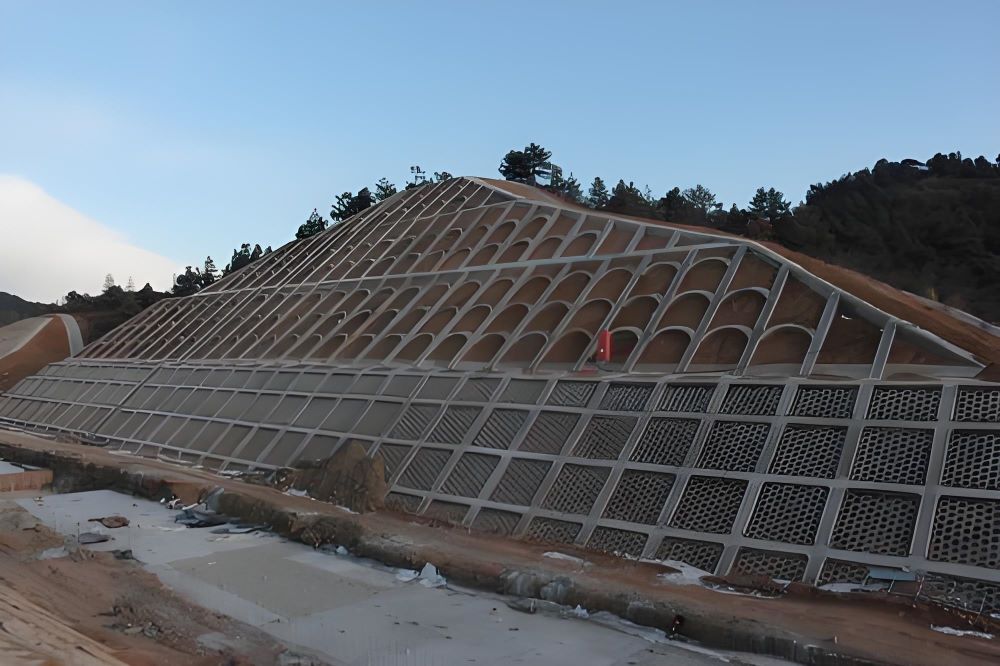
Common types, functions and construction methods of slope support
Slope support engineering is a technology widely used in civil engineering, geological disaster prevention, mining, railway and highway construction, etc. It aims to stabilize slopes through various engineering measures, prevent geological disasters such as landslides and collapses, protect people's lives and property, and ensure the normal operation of engineering facilities.
I. Common types of slope support
1. Soil nail wall support: by setting soil nails in the soil slope, it works together with the soil to improve the stability of the slope.
2. Anchor support: using anchors to transfer tension to stable strata to maintain the stability of the slope.
3. Gravity retaining wall: relying on its own gravity to resist soil pressure.
4. Pile-board retaining wall: composed of piles and boards, used to support higher slopes.
II. Main methods of slope support
1. Anchoring technology: by drilling holes in the slope, implanting anchors or anchor cables, and tightly combining them with the slope rock or soil, the stability of the slope is improved.
2. Retaining wall: Build a retaining wall at the bottom or middle of the slope to resist the lateral pressure of the soil and prevent the soil from sliding.
3. Gabion stone cage: Use metal mesh boxes to fill stones to form a slope protection structure, which is suitable for waterside or eroded slopes.
4. Vegetation slope protection: By planting plants such as turf and shrubs, the plant roots are used to reinforce the soil and reduce soil erosion. It is suitable for slopes with smaller slopes.
5. Sprayed concrete: Spray concrete on the surface of the slope to form a protective layer, which is suitable for the protection of rock slopes.
6. Drainage system: Set up drainage ditches, drainage holes, etc. to remove water from the slope in time and reduce the adverse effects of water on the stability of the slope.
III. The main functions of slope support
1. Prevent slope collapse and protect the safety of surrounding buildings and personnel.
2. Maintain the stability of the slope to ensure the normal progress of the project.
3. Reduce soil erosion and protect the environment.
Slope support is a complex project that requires comprehensive consideration of geological conditions, engineering requirements, environmental protection and other factors. Reasonable selection of support methods, careful design of construction plans, and strengthening of post-monitoring and maintenance are the keys to ensuring the success of slope support projects. With the development of science and technology, slope support technology is also constantly innovating, providing more effective solutions for engineering safety and environmental protection.
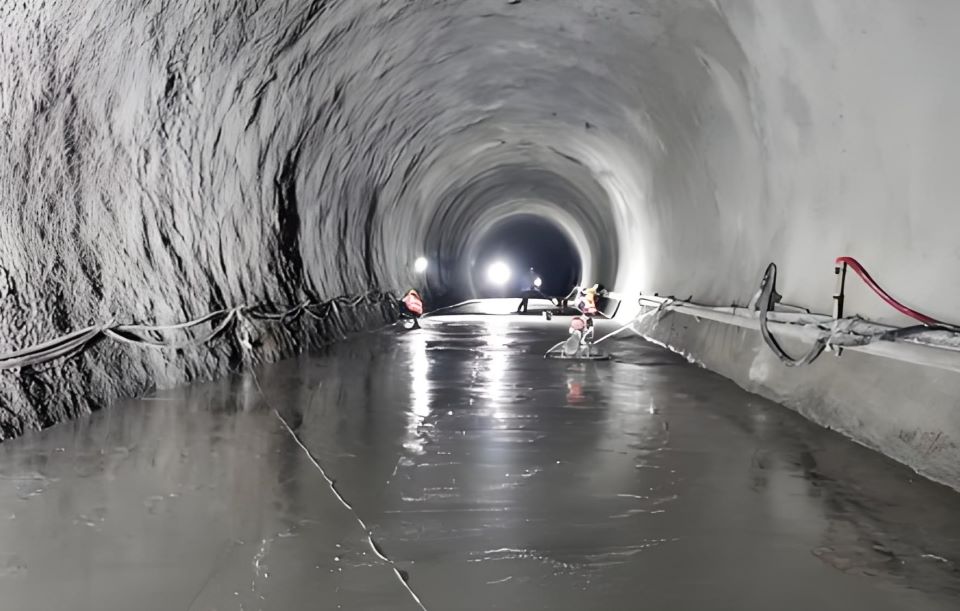
What are some obvious signs of insufficient concrete strength?
What are some obvious signs of insufficient concrete strength? Here are some obvious signs of insufficient concrete strength:
1. Cracks: Insufficient concrete strength may cause cracks in the structure. These cracks may appear on the surface of the concrete or penetrate the entire structure. The presence of cracks may indicate that the tensile strength of the concrete is insufficient, or that the compressive strength of the concrete is not sufficient to withstand the loads applied to it.
2. Spalling and wear: Insufficient concrete strength may cause spalling and wear on the surface of the concrete, especially in areas subject to high friction or abrasive forces. This may indicate that the concrete is not sufficiently resistant to wear or impact.
3. Deformation: Insufficient concrete strength may cause deformation of the structure, such as bending, twisting, or settling. This may indicate that the flexural strength or compressive strength of the concrete is not sufficient to withstand the loads applied to it.
4. Water seepage: Insufficient concrete strength may cause the compactness of the concrete to decrease, resulting in water seepage. This may indicate that the concrete is not sufficiently impermeable.
5. Powdering or sanding on the concrete surface: Insufficient concrete strength may cause powdering or sanding on the concrete surface, which may indicate that the concrete has insufficient weathering resistance or durability.
6. Reduced bearing capacity of concrete structure: Insufficient concrete strength may cause the bearing capacity of concrete structure to be reduced, unable to bear the designed load, thus affecting the safety and stability of the structure.
7. Reduced durability of concrete structure: Insufficient concrete strength may cause the durability of concrete structure to be reduced, unable to resist environmental erosion, such as freeze-thaw cycles, chemical corrosion, etc., thus affecting the service life of the structure.
When the above signs are found, concrete strength testing should be carried out immediately to confirm whether the concrete strength meets the design requirements. If the concrete strength is indeed insufficient, measures should be taken immediately to repair or reinforce it to prevent further damage. Before repair or reinforcement, necessary evaluation and analysis should be carried out to determine the necessity and feasibility of repair or reinforcement. Repair or reinforcement should be carried out by experienced professionals in a safe environment to ensure the repair or reinforcement effect and construction safety.

Are there any technologies that can improve mine safety?
New technologies to improve mine safety are constantly emerging, mainly including the following aspects:
1. Advanced monitoring technology: Using Internet of Things (IoT) technology, environmental conditions in the mine, such as temperature, humidity, gas concentration, etc., as well as the operating status of equipment can be monitored in real time. These data are collected by sensors and transmitted to the ground control center to achieve real-time monitoring of the mine environment and equipment status.
2. Automation and robotics: Automated manipulators and unmanned vehicles (UGVs) are being introduced into mining operations to perform dangerous or repetitive tasks, such as post-blasting cleanup, ore loading and transportation. These technologies reduce the time that personnel are directly exposed to dangerous environments, thereby improving overall safety.
3. Virtual reality (VR) and augmented reality (AR): VR and AR technologies are used to train and simulate mine operation scenarios, allowing workers to learn operating skills and emergency response in a simulated environment. In addition, AR can provide real-time information on site to help workers identify potential risks and correct operating methods.
4. Biometric technology: Biometric technologies such as fingerprint recognition, iris scanning and facial recognition are being used for identity authentication at mine entrances, ensuring that only authorized personnel can enter specific areas, thereby improving safety management.
5. Wireless communication technology: The introduction of 5G networks provides mines with high-speed and stable wireless communication, making real-time data transmission and remote control possible. This is essential for emergency response and quick decision-making.
6. Smart wearable devices: Wearable devices such as smart helmets, safety belts and shoes integrate sensors and communication modules to monitor workers' health and location while providing necessary navigation and alarm functions.
7. Drone technology: Drones are used for reconnaissance and monitoring of mine areas. They can enter areas that are difficult or impossible for humans to reach, provide high-resolution terrain and structural images, and help identify potential safety hazards.
8. Disaster warning system: Disaster warning systems based on artificial intelligence (AI) and machine learning algorithms can analyze historical data and real-time monitoring data, predict the risks of natural disasters such as gas explosions and water disasters, and issue warnings in advance so that preventive measures can be taken.
9. Intelligent ventilation system: The intelligent ventilation system uses sensors and automatic control technology to dynamically adjust air flow according to the actual needs of the mine, ensuring a suitable working environment while reducing energy consumption.
10. Safety training and education technology: VR and AR technology are used for safety training, so that employees can learn the correct methods to deal with various emergencies in a simulated environment, improve their safety awareness and emergency response capabilities.
The application of these new technologies is gradually changing the traditional mine safety production model, and effectively improving the safety production level of mines by improving monitoring accuracy, automation and emergency response capabilities. With the continuous advancement and maturity of technology, mine safety production will be more intelligent, efficient and sustainable in the future.
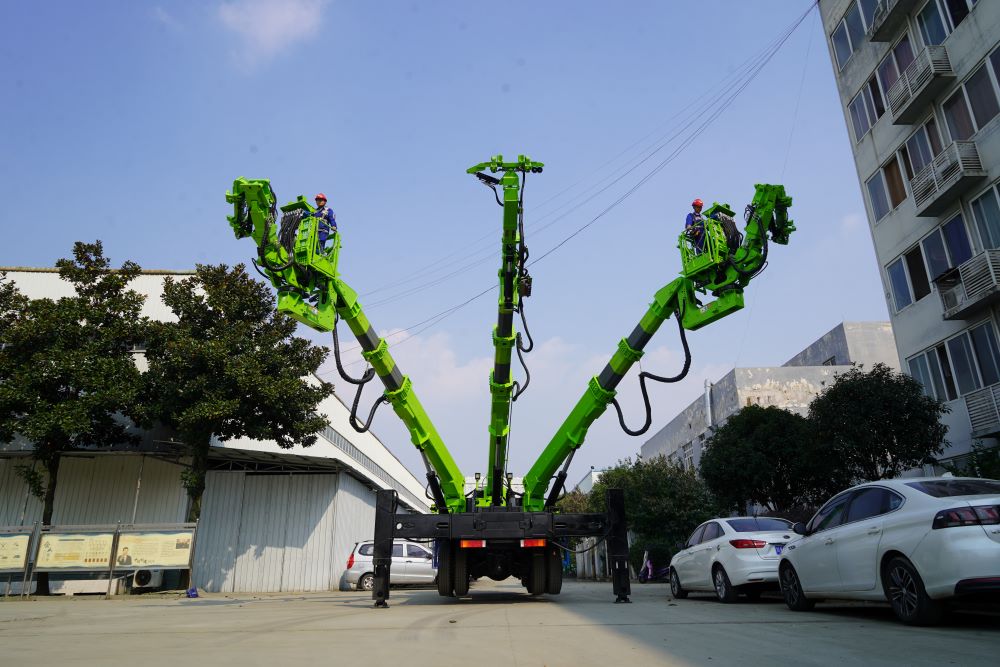
How to choose a suitable tunnel three-arm arch installation trolley?
How to choose a suitable tunnel three-arm arch installation trolley? The following key factors need to be considered when choosing a suitable tunnel three-arm arch installation trolley:
1. Tunnel size and shape: First, the specifications of the required trolley need to be determined based on the diameter, length and shape of the tunnel. Tunnels of different sizes may require different types of trolleys.
2. Arch type and size: The trolley must be able to adapt to the type and size of the arch used, including parameters such as the span, thickness and weight of the arch.
3. Construction environment: Consider the geological conditions, ventilation conditions and whether there are harsh environmental factors such as high temperature and humidity at the construction site, and choose a trolley that can adapt to these conditions.
4. Construction technical requirements: According to the technical standards and quality requirements of tunnel construction, select a trolley that meets the corresponding technical specifications to ensure the construction quality.
5. Economy: Under the premise of meeting the construction needs, comprehensively consider the purchase cost, operation and maintenance costs and expected economic benefits of the trolley, and choose a product with high cost performance.
6. Manufacturer reputation: Choose well-known brands and manufacturers with a good after-sales service record to ensure the quality of the trolley and subsequent technical support.
7. Safety performance: The trolley should have necessary safety protection measures, such as anti-fall and anti-collision devices, to ensure the safety of construction workers.
8. Convenience of operation: The trolley's operating system should be simple and easy to use, which can reduce the training requirements for operators and improve work efficiency.
9. Scalability: Consider possible changes in construction needs in the future and choose a trolley that can be upgraded or modified to adapt to future work needs.

How should a concrete spraying machine be operated during construction on rainy days?
Using a concrete spraying machine for construction on rainy days or in high humidity environments will face many challenges, such as moisture protection of equipment, performance adjustment of concrete mixtures, and construction safety. The following are the operating measures that should be taken during construction on rainy days:
1. Equipment moisture protection and maintenance
·Electrical component protection: Use waterproof covers or waterproof cloths to cover the electrical components of the spraying machine to prevent direct contact with rainwater and avoid short circuits or electrical failures.
·Mechanical component lubrication: Ensure that all mechanical components are fully lubricated to prevent rust and wear caused by rainwater.
·Regular inspection: Before and after construction on rainy days, the equipment should be carefully inspected to ensure that all components are in good condition, paying special attention to the electrical system and transmission system.
2. Concrete mixture adjustment
·Adjust the water-cement ratio: The air humidity is high on rainy days, and the hydration process of concrete may be affected. Properly adjust the water-cement ratio to compensate for the additional moisture and maintain the fluidity and strength of the concrete.
·Protect the mixture: When transporting and storing concrete mixture, use waterproof cloth to cover it to prevent rainwater from seeping in and affecting the quality of concrete.
3. Preparation of construction environment
·Drainage measures: Ensure that the construction site has a good drainage system to avoid rainwater accumulation and affect the adhesion and stability of shotcrete.
·Shielding measures: Set up shielding in the spraying area, use waterproof cloth or temporary scaffolding to protect the area under construction from direct impact of rainwater.
4. Safety measures
·Personnel safety: Ensure that all operators wear waterproof work clothes and safety equipment, such as waterproof gloves, safety shoes, etc., to prevent slipping and electric shock.
·Equipment stability: Check the placement of the spraying machine to ensure that the ground is solid to avoid the ground becoming soft due to rainwater soaking, which affects the stability of the equipment.
·Emergency plan: Develop an emergency plan for construction on rainy days, including rapid evacuation of equipment and safe evacuation of personnel, to cope with sudden severe weather.
5. Construction quality monitoring
Continuous monitoring: During construction in rainy days, the spraying quality and hardening process of concrete are continuously monitored, and construction parameters are adjusted when necessary to ensure that the quality of the project is not affected.
Construction using a concrete spraying machine on rainy days requires more detailed preparation and careful operation to ensure equipment safety, construction quality and personnel safety. By taking the above measures, efficient construction progress and quality control can be maintained under adverse weather conditions.
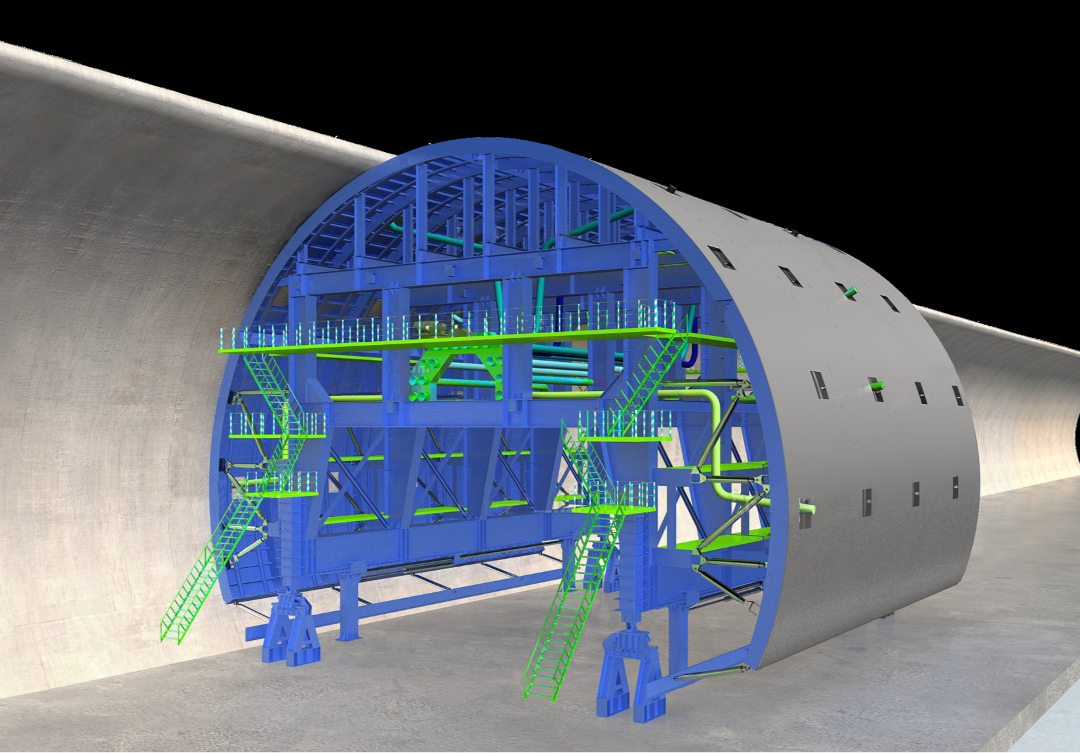
Construction process of secondary lining trolley
As an important equipment in tunnel construction, the secondary lining trolley is mainly used for concrete pouring of tunnel secondary lining. Its working principle combines mechanical automation and concrete pouring technology to achieve efficient and precise construction of tunnel lining. Below, we will discuss the construction process of the secondary lining trolley in detail.
The construction process of the secondary lining trolley is as follows:
1. Trolley positioning: Move the trolley to the position where lining is required, and adjust the trolley to the correct height and horizontal position through devices such as jacks.
2. Template positioning: Adjust the template of the trolley to the position and shape required by the design through devices such as hydraulic systems or screws to ensure that the template fits tightly with the tunnel wall.
3. Concrete pouring: Pour concrete in the template, and the concrete can be transported into the template by pumping or other means. During the pouring process, attention should be paid to the uniformity and density of the concrete to avoid quality problems such as voids or honeycombs.
4. Vibration and curing: After the concrete is poured, a vibrator is needed to vibrate the concrete to ensure the compactness of the concrete. At the same time, the concrete needs to be cured to ensure the strength and durability of the concrete.
5. Demolding and moving: After the concrete reaches a certain strength, the formwork of the trolley needs to be removed, and then the trolley is moved to the next location where lining is required for the next lining construction.
The secondary lining trolley realizes the automated construction of the secondary lining of the tunnel through its precise structural design and control system, greatly improving the construction efficiency and engineering quality.
The secondary lining trolley is mainly composed of a traveling mechanism, a template system, a concrete pouring system, a hydraulic system, an electrical control system, etc. Among them, the traveling mechanism is used for the movement of the trolley in the tunnel; the template system is responsible for forming the mold for concrete pouring; the concrete pouring system is used for the transportation and pouring of concrete; the hydraulic system and the electrical control system are used to control the operation of the trolley and the opening and closing of the template.

Characteristics, functions and importance of secondary lining trolley in tunnel construction
In modern tunnel engineering, secondary lining trolley plays an indispensable role. It not only improves construction efficiency, but also ensures the safety and quality of the project. This article will explore in depth the characteristics, functions and importance of secondary lining trolley in tunnel construction.
Forming and support: a solid foundation for building tunnels
One of the main functions of the secondary lining trolley is to provide a template for the secondary lining concrete to ensure that the shape and size of the lining structure strictly follow the design requirements. This process is crucial to the overall structural safety of the tunnel. In addition, the trolley bears huge pressure and weight during the concrete pouring process, which effectively prevents the deformation of the concrete and ensures the safety and stability of the construction process.
Flexible movement and adaptability to changing construction environments
Another significant advantage of the secondary lining trolley is its mobility. It can move easily inside the tunnel and quickly adapt to the construction needs of different sections without frequent disassembly and assembly, which greatly saves time and labor costs. This flexibility enables the trolley to operate efficiently under complex and changing geological conditions, improving the flexibility and adaptability of the entire construction process.
Mechanized construction accelerates the progress of the project
With the advancement of technology, the mechanization degree of the secondary lining trolley is constantly improving, and the introduction of the automatic control system makes the construction process more accurate and efficient. The use of the trolley not only reduces the dependence on manual labor and reduces labor intensity, but also significantly accelerates the construction progress of the secondary lining, which is of great significance for shortening the tunnel construction period and controlling the project cost.
Considerations of design and application
The design and use of the secondary lining trolley need to comprehensively consider factors such as the size, shape and geological conditions of the tunnel. The designer must accurately calculate the load-bearing capacity of the trolley, the size and shape of the template, and the maneuverability to adapt to different construction environments. Through careful planning and reasonable layout, the stability and reliability of the trolley during construction are ensured, so as to achieve the dual goals of improving construction efficiency and ensuring project quality.
As a key technical equipment in tunnel construction, the secondary lining trolley has the characteristics of molding, support, movement and mechanized construction, which provides a strong guarantee for the efficient and safe construction of modern tunnel projects. With the continuous advancement of science and technology, the design and application of the secondary lining trolley will also become more intelligent and refined, opening up a broader development space for future tunnel construction.

Concrete construction technology in tunnel construction: from primary support to secondary lining
In tunnel construction, concrete construction technology is the key to ensure the stability and safety of tunnel structure. Concrete construction of tunnels usually adopts the method of excavation and lining at the same time. This process involves multiple steps, from initial support to secondary lining, and each step is crucial. This article will introduce this construction process in detail to help readers understand the whole process of tunnel concrete construction more deeply.
Initial support: shotcrete and steel mesh fixing
After tunnel excavation, the first task is to carry out initial support to prevent the collapse of the tunnel wall. This process usually uses shotcrete as a temporary support. Shotcrete can harden quickly and provide immediate support for the tunnel wall. Subsequently, the construction workers will set up the steel mesh and use anchor rods to fix it to the tunnel wall to further enhance the stability of the initial support.
Secondary lining: Collaborative operation of steel bar trolley and casting trolley
After the initial support is stable, the tunnel enters the secondary lining stage. The secondary lining is part of the permanent structure of the tunnel and is crucial to the long-term stability and safety of the tunnel. This stage of construction requires the use of special trolleys, including trolleys for setting up and welding steel bars and casting trolleys.
1. Setting up and welding the steel bar trolley: First, use the steel bar trolley to set up the steel bar frame inside the tunnel. The steel bar frame must be built accurately to ensure the structural strength and durability of the concrete lining.
2. Casting trolley: After the steel bar frame is built, the casting trolley enters the operation for pouring concrete. In the concrete formwork, a casting port of about 50 mm by 50 mm will be reserved to ensure that the concrete can be evenly distributed, avoid the generation of bubbles and voids, and thus improve the density and strength of the concrete.
Tunnel concrete construction is a complex and precise process. From initial support to secondary lining, each step must be strictly controlled to ensure the safety and durability of the tunnel structure. By using shotcrete, steel mesh fixing, and the coordinated operation of the steel bar trolley and the casting trolley, tunnel builders can effectively respond to the challenges of geological conditions and build high-quality tunnel projects.
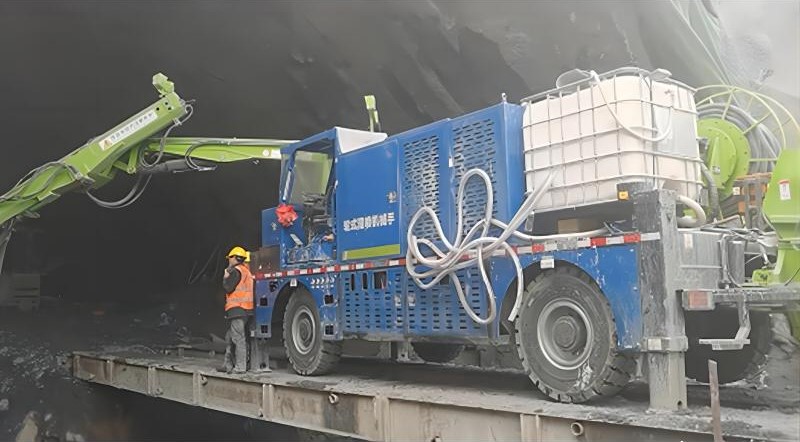
Advantages, characteristics, and application fields of tunnel wet spraying robotic arm
Tunnel wet spraying manipulator is an indispensable and important equipment in modern tunnel engineering, widely used in shotcrete support construction in railway and highway tunnels, water conservancy and hydropower culverts, underground mines and other fields. Compared with traditional dry spraying equipment, wet spraying robots have significant advantages in construction quality, efficiency, and safety.
Improve construction quality and efficiency
The wet spraying robot uses wet spraying concrete, which can cover the tunnel wall more evenly than dry spraying equipment, greatly improving the construction quality. The wet spraying method of concrete has better adhesion and flowability during the spraying process, which can ensure the compactness and uniformity of the concrete layer, effectively reducing the occurrence of voids and cracks. In addition, the wet spraying robot has a high degree of automation and simple operation, which can significantly improve construction efficiency and shorten the project cycle.
Reduce rebound rate
During the spraying process of dry spraying equipment, concrete is prone to rebound, resulting in material waste. The rebound rate of wet spraying robotic arms is relatively low, allowing concrete to better adhere to the construction surface, significantly reducing material waste and lowering construction costs. This not only saves resources, but also enhances the environmental friendliness of construction.
reduce labor intensity
The use of wet spraying robotic arms greatly reduces the labor intensity of workers. Traditional dry spraying construction requires workers to operate in close proximity for a long time, which not only consumes a lot of physical energy but also faces high risks. The automation operation of the wet spraying robotic arm reduces the direct involvement of workers, who only need to monitor and adjust within a safe distance, greatly reducing physical labor and construction difficulty.
Improving the health status of workers
The construction environment of tunnels usually has a lot of dust, and dry spraying equipment can generate a large amount of dust, which poses a serious threat to the health of workers. The wet spraying robotic arm effectively reduces the generation of dust, lowers the risk of workers inhaling harmful dust, and significantly improves the air quality at the construction site. This not only ensures the health of workers, but also meets the requirements of modern environmental protection construction.
Tunnel wet spraying robotic arm plays an important role in tunnel construction due to its superior performance. By improving construction quality and efficiency, reducing rebound rate, reducing labor intensity, and improving the health status of workers, wet spraying robots not only enhance the safety and economy of construction, but also promote the development of tunnel engineering towards a more environmentally friendly and efficient direction. As the core equipment for tunnel construction, wet spraying robotic arm is undoubtedly an important innovation in modern engineering construction.